Hot Briquetted Iron (HBI), Steel’s Most Versatile Metallic: Part 1 – Starting with the Basics
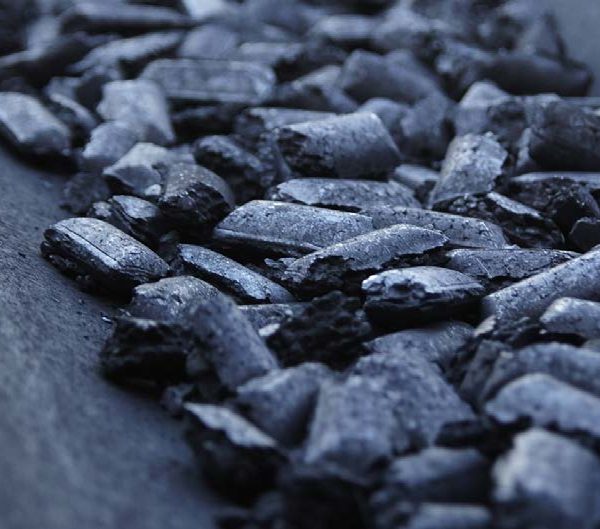
EDITOR’S NOTE:
The 4th quarter 1982 issue of Direct From Midrex first mentioned a new direct reduced iron (DRI) product from Midrex called hot briquetted iron (HBI). Midrex was not the first to produce a hot briquetted form of DRI (Fior de Venezuela had produced and shipped a product in the late 1970s), but we did help establish HBI as the steel industry’s most flexible iron source.
Here we are almost 36 years later, and what was old is new again. Two of the most recent DRI plants to start up in the past few years are HBI facilities and at least one more is on its way. Thus we thought this was the perfect time to revisit HBI with a series of articles to explain the basics of the product and how its technical and commercial development has responded to the changing landscape of the global steel industry. Part one, of course, starts at the beginning…
What is Hot Briquetted Iron (HBI)?
Hot Briquetted Iron (HBI) is a compacted form of DRI that is manufactured with well-defined, consistent chemical and physical characteristics. HBI is manufactured to be shipped over great distances and melted in a variety of iron and steel processes. It is available throughout the year unlike scrap, which tends to have a collection season. The chemical composition of HBI is certified by the producer, and ISO quality standards are strictly followed.
Physical characteristics are typically credited with why HBI was created. Its greater mass allows rapid penetration of the furnace slag layer. HBI is 100 times more resistant to reoxidation than conventional DRI and will pick up 75% less water. HBI also generates fewer fines, which provides greater value to users and reduces safety concerns during handling and shipping. Its size and shape are compatible with standard materials handling equipment, and HBI can be batch charged or continuously fed to a melting furnace.
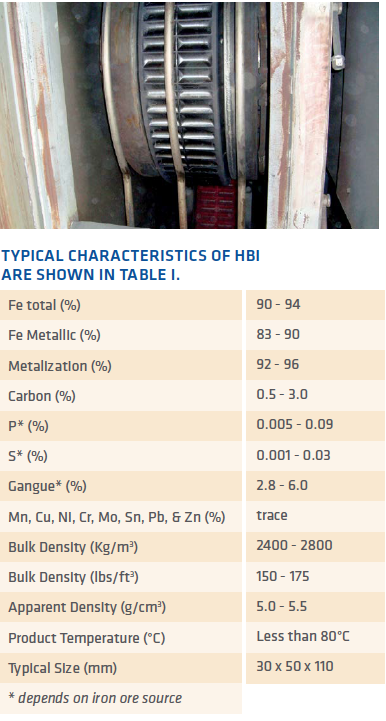
TABLE I. Typical characteristics of HBI
ADVANTAGES OF Hot Briquetted Iron (HBI)
HBI is a modern charge material for use in combination with scrap or as an alternative to scrap in steelmaking furnaces or as an addition to blast furnaces in ironmaking applications. Because it is made directly from iron oxides without melting, HBI contains none of the impurities in smelted iron resulting from coke, limestone and scrap inclusions. Depending on the chemistry of the iron oxide used in its production, HBI is low in residual metal elements (copper, nickel, chrome, molybdenum and tin), as well as sulfur and phosphorus.
THE USE OF HBI CAN BENEFIT THE STEELMAKER IN EITHER OF TWO WAYS:
- It allows the production of high quality steel products that could not be made consistently due to high residual elements levels inherent in most obsolete scrap.
- It allows the use of less costly, lower grades of scrap to make basic grades of steel products.
HBI is used primarily in the electric arc furnace (EAF) for its diluent effect; i.e., to lower the overall level of metallic residuals and sulfur. In addition, HBI shares these operational advantages with other forms of DRI:
- Blends with other metallics for best total charge economics
- Can be continuously fed to maximizes power-on time and increase bath weight
- Promotes foamy slag and reduces EAF nitrogen level
- Shields refractory to reduce damage
- Equally effective in AC or DC furnaces, long or short arc operation
- Compatible with injected fuels and oxygen
- Predictable mass and heat balances
These unique characteristics of HBI provide other benefits:
- High density (5.0 g/cm3) allows for rapid penetration of the furnace slag layer
- Increased thermal and electrical conductivity for faster melting
- Less fines generation during handling, shipping and storage
- Easy to handle, store and transfer in all types of weather and with standard materials handling equipment
- Safer and less costly for ocean transport
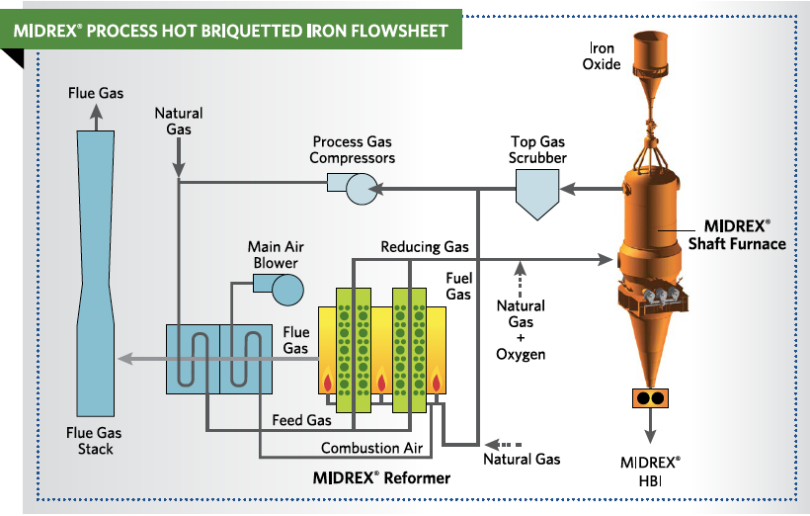
FIGURE 1.
MIDREX™ hot briquetted iron flowsheet
MIDREX ADDS HOT BRIQUETTING
When Midrex announced its intention to include hot briquetting, the MIDREX® Direct Reduction Process was in its fifth generation of operational design. Building on a basic flowsheet that was well proven in over 15 years of operation at the time, Midrex, in cooperation with its Construction Licensees, designed and optimized a hot discharge/hot briquetting system that required only minor process changes and incorporated commercially available equipment.
As shown in Figure 1, the most significant process modification was the elimination of the cooling gas circuit. The cooling zone in a cold discharge plant is used only for adjusting carbon content and cooling the DRI (in pellet/lump form) prior to it being discharged.
Recently Midrex introduced ACT™ [Adjustable Carbon Technology], which can be included in new plants and retrofitted into existing plants to increase carbon content up to 4.0%* while maintaining the physical integrity of the HBI. (See the article in 3Q2017 DFM or download the ACT brochure from www.midrex.com.)
The reliable and low cost dynamic seal gas system used in all MIDREX® Plants was also modified to accommodate the hot discharge of DRI for briquetting. The seal gas system is a closed loop gas circuit which dedusts, compresses and reheats the seal gas. It allows optimum control of product temperature and furnace atmosphere.
After the iron oxide is reduced, the hot DRI (HDRI) is continuously discharged at 650°C or higher into a product discharge chamber (PDC), which purges any combustible gases from the HDRI bed and smooths out any production surges. The purge gas is externally heated to keep the HDRI at the proper briquetting temperature.
*Note: At carbon levels over 3.0%, it may not be possible to meet the apparent density of 5.0 (g/cm3 ) for IMO code DRI(A).
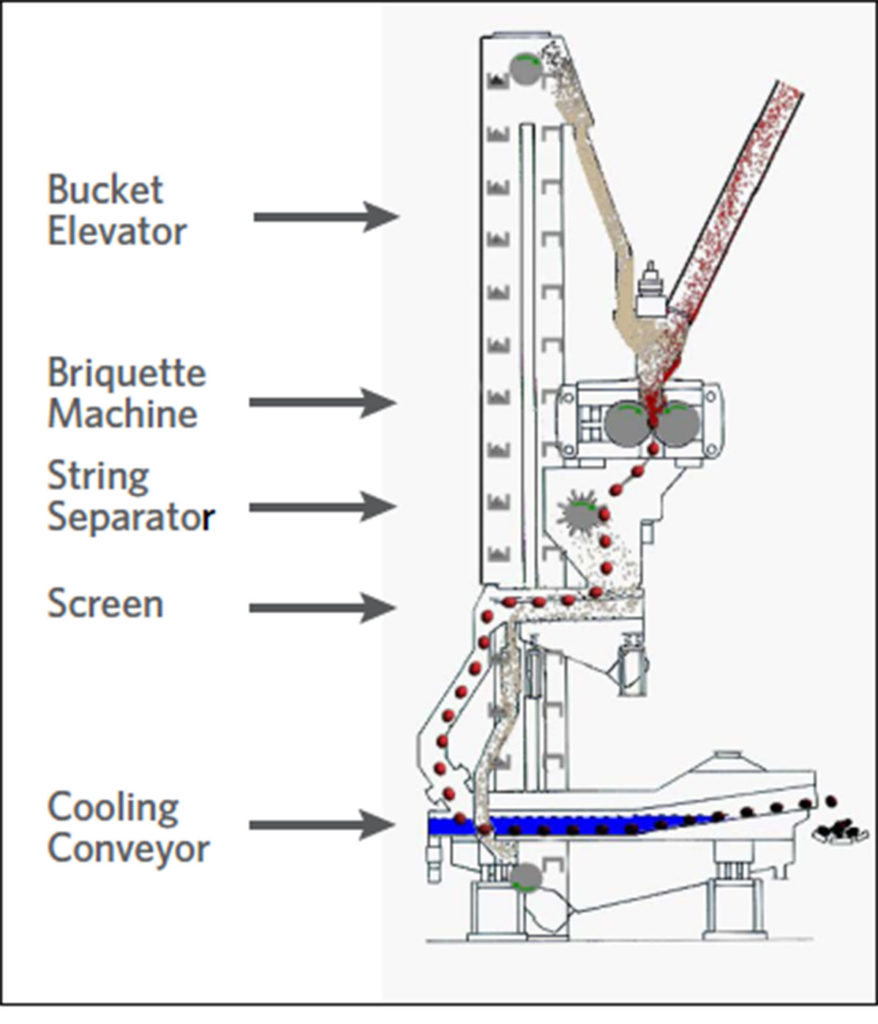
FIGURE 2. MIDREX™ hot briquetted iron system
The PDC equally distributes the HDRI among feed pipes to each of the briquetting machines, where a screw feeder introduces the material into pocketed briquetting rolls, which compress and compact it into a continuous strand of pillow-shaped briquettes. The strands are fed through a device that mechanically separates the briquettes, after which they are cooled to reducing oxidation and typically stored in outdoor piles to await further use or transportation.
The MIDREX® Hot Briquetting System is shown in Figure 2.
THE DECISION FOR HOT BRIQUETTED IRON (HBI)
In 1980, steel industries based on the electric arc furnace (EAF) were developing in ASEAN (Association of South East Asian Nations) and the MENA (Middle East North Africa) Region. EAF steel mills could be sized to a specific market and were less capital-intensive than traditional integrated mills. However, EAF-based mills melted scrap and the amount of scrap that could be generated in these emerging economies was extremely limited.
DRI was gaining attention as an effective alternative and supplement to scrap in the EAF. Global production of DRI in 1980 was little more than seven million metric tons, almost all of which was being consumed by steel mills adjacent to the DR plants. In the same period, Asian countries alone were importing approximately eight million tons of scrap, mostly from the US and Europe.
A merchant DRI plant fit perfectly into the development plan of Malaysia’s Sabah Gas Industries (SGI), which was created in 1981 to manage the use of natural gas associated with the Erb West and Samarang offshore oil fields off the north coast of Borneo. With gas expected to be available to Labuan Island near Kota Kinabalu by 1984, a turnkey contract was awarded to voestalpine AG (VA), a Construction Licensee of Midrex, on May 19, 1981, to construct a merchant DRI plant. Site work began in November 1981, and start-up was scheduled for early 1984. However, in October 1982, The Inter-Governmental Maritime Consultative Organization (IMCO, today known as IMO – International Maritime Organization) developed and adopted a code for shipping DRI due to its propensity to heat up and evolve hydrogen gas when exposed to water, especially saltwater. The new IMCO BC (Bulk Cargoes) Code* made the provision that ships’ holds containing DRI should be maintained under inert atmosphere conditions unless the DRI was manufactured or treated in a manner approved by the competent authority to provide protection against corrosion and oxidation by water and air.
Therefore, SGI needed a method to make its DRI more resistant to oxidation and safer to ship, especially because the plant would be located in a tropical region where significant rainfall occurred 4-6 months of the year (average annual rainfall on Labuan is 4000 mm/160 inches). After comparative studies of several passivation techniques and hot briquetting by an outside consultant, SGI made a decision for hot briquetting and the plant supply contract was amended in August 1982. Mechanical construction of the plant was completed in January 1984. Plant commissioning began in June 1984, and the plant produced highly metallized HBI during the first week of August 1984, with the first shipment of 5,000 tons taking place in December 1984.
*Following multiple incidents involving DRI cargoes which were deemed to have been “manufactured or treated in a manner approved by the competent authority to provide protection against corrosion and oxidation by water and air,” the subsequent International Solid Bulk Cargoes (IMSBC) Code issued by IMO stipulated that only HBI or “hot-moulded briquettes, DRI (A)”, as it is known in the Code, is not subject to inerting for ocean transport.)
LEGACY OF THE LABUAN PLANT
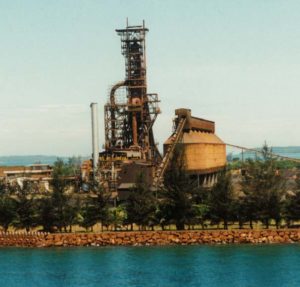
Labuan Plant
Producing value-added products from associated natural gas was one of the goals of SGI. Equally important was educating and training people from the local population to develop a sustainable industrial infrastructure that would stimulate economic and social growth. Similar thought processes have given rise to the majority of the direct reduction projects throughout the world.
Likewise, the optimization phase of the SGI plant produced improvements and innovations that have been assimilated into the body of MIDREX® Technology, such as furnace modeling tests that led to improved product flow and discharge. SGI plant operators also demonstrated that the life of briquette machine segments could be as much as 100,000 tons when initial estimates were for only 60,000 tons.
On the commercial side, SGI made a lasting impression in how it approached the market. The practice of offering trial shipments with on-site application assistance introduced by SGI was highly successful and has been adopted by merchant HBI plants since then. Today, most HDRI plants are designed with the option for briquetting machines to provide an additional income stream with merchant HBI.
Plants capable of producing more than 25 million tons of HBI have been installed or is under construction worldwide; 18 using MIDREX® technology, 3 HYL/ENERGIRON® and one each FINMET®, CIRCORED® and FIOR® (TABLE II).
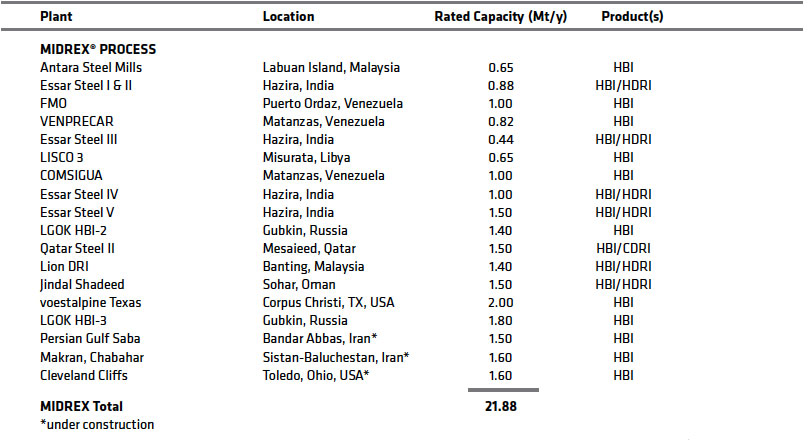
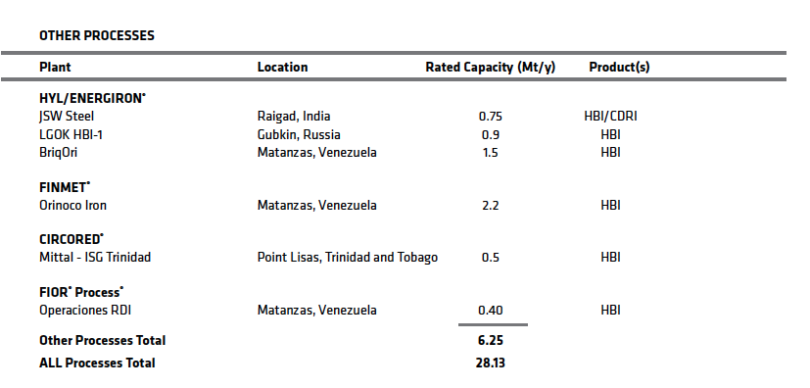
TABLE II.
Direct reduction plants capable of HBI production
The latest MIDREX® HBI plant was announced in 2017 by Cleveland-Cliffs Inc. The 1.6 million t/y plant, to be located in Toledo, Ohio, USA, will the source of highquality HBI for the EAF steel market in the Great Lakes region when it is started up in 2020.
CONCLUSION
The decision by Midrex to add hot briquetting as a feature of its direct reduction process technology was made initially for operational and marketing reasons. The product’s enhanced physical characteristics proved to be a solution to handling, shipping and storing issues associated with conventional cold DRI Briquetting HDRI also was found to improve in-plant losses and to expand the potential market for DRI products beyond electric arc furnaces to include blast furnaces.
Today, HBI’s popularity as an ore-based metallic is steadily increasing as more capacity comes online. It has become a key element in the environmental strategies of a few traditional integrated steelworks, as well as a valuable secondary product for EAF steelmakers that have their own captive hot discharge direct reduction plant.
All in all, HBI continues to prove that it is steel’s most versatile metallic.