The Versatile OBM (Ore-Based Metallic): Part 2 – How to get what you paid for: A guide to maintaining the value of DRI
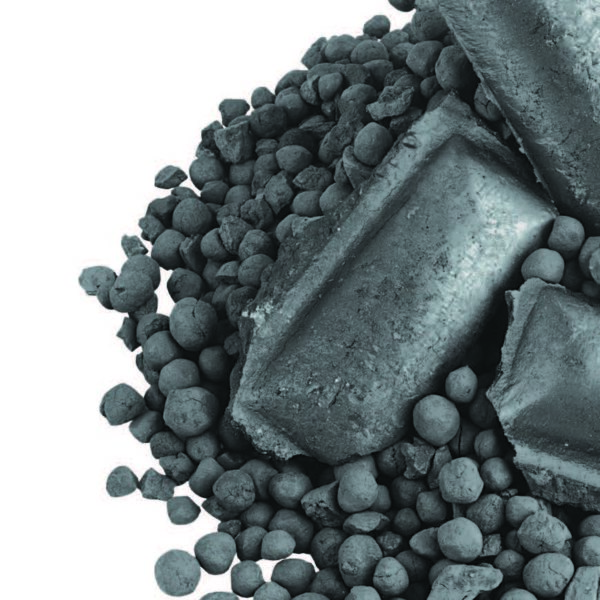
EDITOR’S NOTE:
This is the second in a series of articles designed to remove some of the confusion about direct reduced iron [DRI] for the novice and perhaps even expand what the seasoned veteran understands. Part 1 of this series [“The Versatile OBM (Ore-Based Metallic): Part 1 – Everything you ever wanted to know about Direct Reduced Iron … but were afraid to ask!“] began with the basics: what is direct reduction and what is direct reduced iron [DRI]. In Part 2 we will discuss what happens after the DRI is produced, the factors affecting DRI quality and how to maintain the quality [and thus the value] of DRI during handling, storing, transporting and ocean shipping.
INTRODUCTION – THE VALUE OF DRI
Direct Reduced Iron (DRI) is first and foremost a metallic iron raw material for making steel. Simply stated, it is a means for achieving the goals and objectives of the steelmaker using it.
DRI has evolved into various forms over the last 50 years (Figure 1). The first DRI plants produced only a cold metallic product (CDRI). As demand for DRI increased, a product with excellent handling and shipping characteristics was needed for the merchant market, which resulted in development of hot briquetted iron (HBI). Over time EAF steelmakers with captive DRI plants (i.e., plants adjacent to or nearby the meltshop) wanted a way to take advantage of the heat contained in DRI immediately following reduction, leading to the introduction of hot DRI (HDRI).
All three DRI product forms are versatile ore-based metallics (OBMs) and have distinctive characteristics that benefit steelmakers. The most effective and efficient use of DRI products will depend on the financial and operational objectives of the user. Much like operation of a meltshop, the use and preference of metallic materials will vary with the complexity of the steelmaking practice and the market in which the steel producer competes. As a result, there is no one way to use DRI nor a single product form that fits all applications. With that said, the value of DRI is best gauged by what is most important to each steelmaker using the product and how well it meets these expectations; thus the product specification can vary with each user.*
Once produced, the product quality (and hence value to the steelmaker) can be directly impacted by what happens to the product prior to it being melted. DRI products, like other forms of iron, have the potential to degrade over time especially if not properly handled, stored or transported. Steelmakers largely have control over maintaining this quality if they take the right measures. This article will examine these measures required to maintain that value.
*It also must be noted that all direct reduction processes remove only the oxygen from iron oxide, thus the DRI is only as good as the iron ore from which it is made. Therefore, additional items such as acid gangue content will affect product value. Since discussing the “right ore specification” is a separate issue, this article will only focus on what users and buyers of DRI products can do after the product is made in order to best maintain the value of the DRI.
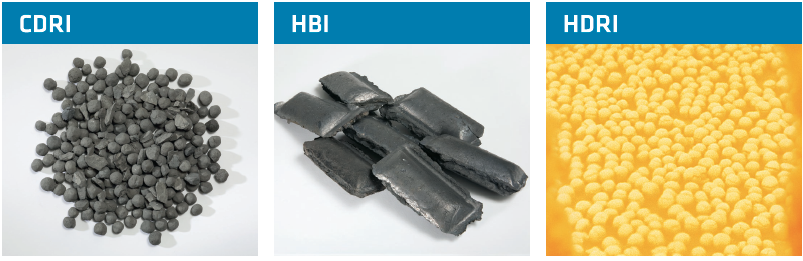
FIGURE 1.
Three Types of DRI Products
FACTORS AFFECTING DRI PRODUCT VALUE
It is a question probably not asked enough: “Is the product the same quality when it reaches the melting furnaces as when it was produced or purchased?”
DRI products provide value to steelmaking operations by delivering a highly metallized, low residual iron source to the melt shop. The extent of this value depends on maximizing the iron units (yield) by minimizing fines and maintaining product metallization after production.
Each DRI product, no matter how it is made, requires special considerations to maintain its value. Therefore, the yield and the degree of metallization (the percentage of total iron in the metallic form) are key factors in determining DRI value. In addition, there are safety concerns that if not addressed could negatively impact a user’s bottom line. These are factors that apply to all three DRI products; however, the ways to address these issues vary to a degree for each particular DRI product.
Fines Generation
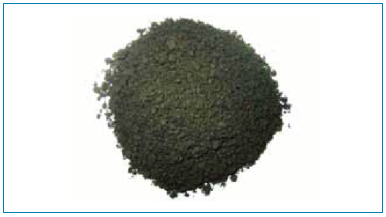
FIGURE 2. Example of DRI fines
Let’s start with fines (Figure 2). This factor should be obvious, as generating fines impacts product yield and productivity downstream. Materials handling equipment selection and system design have a huge impact on how much fines will be generated during handling, as will be discussed later in this article.
For steelmaking purposes, it is important that care is taken to prevent DRI from fragmenting into chips (+3 to -6 mm) or degrading into fines (-3 mm) during handling, transporting and storing to and within the steel mill. Fines generation and spillage can range from 3% to 7% and higher if not treated with care. These losses mean fewer iron units reach the meltshop, which can have significant financial impact on the steel mill’s bottom line.
Metallization
In all DRI products, a small amount of iron oxide (FeO) remains. Metallization is a quantification of the portion of the iron that is metallic. Why is it important? Achieving high metallization is the purpose of direct reduction as it creates metallic iron that is easier and less energy intensive to melt; therefore, higher metallization means value by creating more savings.
When it is stated that DRI has a certain degree of metallization, it means the percentage of metallic iron divided by total amount of iron in the DRI. Total iron is defined as the sum of metallic iron and iron contained as oxide. Metallization is normally expressed as a percentage:
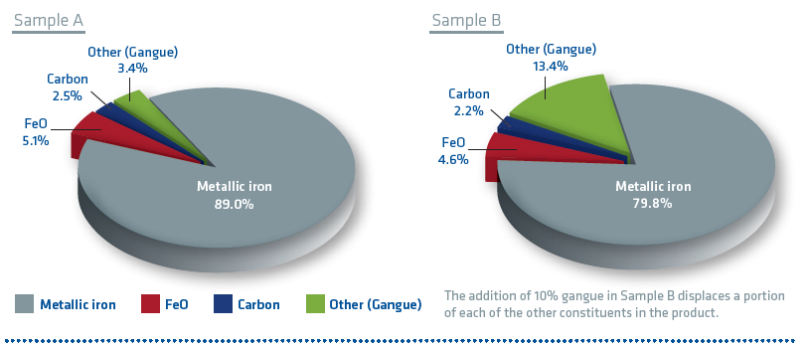
FIGURE 3.
Two examples of DRI at 95% metallization
The extent to which reduction has been completed is represented by the percentage of metallization. Simply speaking, DRI with 95% metallization (or met) means that 95% of the iron is metallic and thus, the remaining 5% exists as FeO. Depending on operating practice of the meltshop, it may be possible to recover 20-80% of the iron present in DRI as FeO.
Please note that metallization is not the total percentage of everything contained in the DRI, just that of the iron-bearing portion (Figure 3). DRI also contains silica and other minerals. In fact, DRI could conceivably have a met of 95% and contain 10% of other minerals.
Metallization is impacted by its reactivity, which is directly influenced by how the DRI is stored and the product form of the DRI (CDRI, HDRI or HBI). In addition, metallization loss varies depending on the particle size of the material. Fines and chips, which have a much higher surface-area-to-volume ratio, are prone to more substantial corrosion and metallization loss, as will be discussed in the next section.
REACTIVITY OF IRON
Any discussion of the value of DRI and what happens during handling, storing, transporting and shipping must include the reactivity of iron. The natural tendency of all iron is to rust; i.e., to combine with oxygen in air (oxidize) and in water (corrode) to form iron oxides.
The tendency of iron to rust is intensified in the case of DRI. After all, DRI is the result of oxygen being chemically removed from iron oxide. A DRI pellet has a sponge-like structure consisting of a network of interconnected pores, which gives it an internal surface area thousands of times greater than a solid iron pellet. This large surface area encourages reactivity with oxygen and water, resulting in oxidation and corrosion. (Note: We should point out that this is theoretical with HDRI, as the temperature of the product would cause a steam explosion if it were to be in contact with water.)
The tendency of DRI to oxidize or corrode is called reactivity. All types of DRI are reactive regardless of the production process or product form. Prolonged exposure of DRI to water reduces product metallization due to rusting (the product of corrosion). Given sufficient time, oxygen and water, any iron mass eventually will be entirely converted to rust.
Rusting also generates heat and in bulk scenarios, this heat can cause DRI to ignite if the heat becomes trapped inside a product pile. This in turn could create a potential safety issue, costing additional money. In addition, a fire will no doubt affect both metallization and product yield; however, there is no need to panic as this phenomenon is completely controllable if properly handled. Excessive fines within a DRI pile also can pose a safety hazard, especially if the fines become wet and are buried in the pile.
Oxidation and Corrosion
In order to better appreciate the challenges of handling, storing, transporting and shipping DRI products, it is helpful to understand the two most important reactivity reactions – oxidation and corrosion.
Oxidation
Oxidation occurs when hot DRI reacts with oxygen in the air to form either magnetite (Fe3O4) or hematite (Fe2O3), according to the following reactions:
Oxidation is an exothermic (i.e., heat liberating) reaction and will continue as long as DRI remains hot and sufficient oxygen is present. However, the oxidation reactions form a thin protective layer that modifies the DRI surface structure and substantially affects its porosity, which reduces DRI reactivity.
Research and plant experience have shown that freshly produced DRI reacts quickly with air when first discharged but the reaction decreases rapidly within minutes and continues to slowly decrease as the DRI cools. This reaction is known as natural aging and results in a modest loss of metallization (typically a fraction of one percent). Insufficient heat is generated during natural aging to cause an acceleration of the reaction.
HDRI is already above the ignition temperature (>200° C/390° F). Therefore, if it is allowed to be in contact with air, it will burn.
Corrosion
Corrosion occurs when CDRI or HBI is wetted and reacts with oxygen in the air to form rust (as previously mentioned, in the case of HDRI, exposure to water would cause a steam explosion due to its elevated temperature).
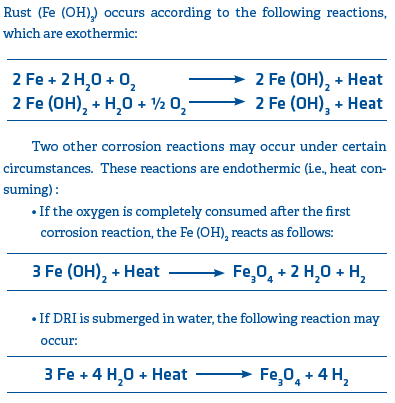
Corrosion is limited to the wetted surface of the DRI and will continue as long as water is present; however, evaporation occurs at 100° C/212° F, so corrosion reactions tend to be temperature-limited. Corrosion is accelerated by contact with salt water because corrosion is an electrochemical reaction. As noted in the equations, hydrogen is also generated when DRI reacts with water.
CDRI is very porous and has a structure reminiscent of the iron oxide pellet from which it was made. As a result it tends to pick up water (as much as 15% of its weight) when exposed to intense wetting. HBI, due to its dense, compacted structure, is much more resistant to water pick up, which typically does not exceed 3% (Figure 4).
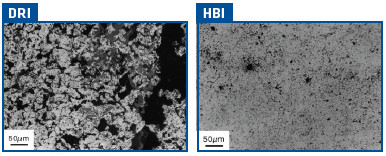
FIGURE 4.
Internal structure comparison of DRI and HBI
In order to assess the extent of corrosion that can be expected to occur when storing HBI, a long-term experiment was carried out by BHP Billiton. A 65-ton HBI pile was set up next to the ocean in a salt-laden atmosphere.
The photos in Figure 5 show the pile when it was first formed, 6 weeks later and 6 months later.
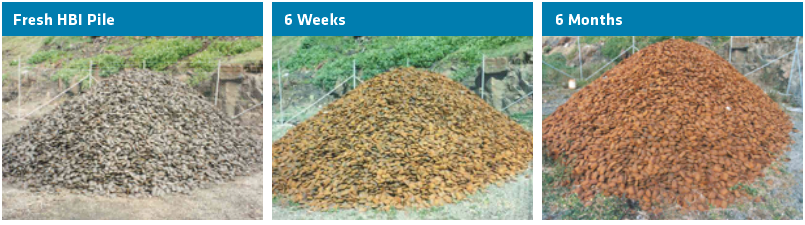
FIGURE 5.
HBI corrosion test pile (courtesy of BHP Billiton)
It was found that the majority of metallization loss occurred in a surface layer approximately 0.2 m thick and a transition layer approximately 0.5 m thick with a relatively unaffected core. The test also showed that briquette density influenced the metallization loss of HBI (see Figure 6); i.e., the higher the density, the lower the metallization loss. This is understandable since the higher density briquettes have less surface area available for reaction with the atmosphere.
In addition, the metallization loss varies depending on the fraction size of the sample. Fines and chips, which have a much higher surface-area-to-volume ratio, are prone to more substantial corrosion, as shown in Figure 7.
A similar test was conducted by Sabah Gas Industries, the predecessor of Antara Steel Mills, on Labuan Island off the north cost of Borneo. A 660-ton pile of HBI was outfitted with thermocouples at six different locations on and in the pile and monitored for six months. At the end of the test period, it was determined that the metallization level decreased by only 0.8% per month despite exposure to tropical weather conditions and a salt-laden atmosphere (see TABLE I, next page).
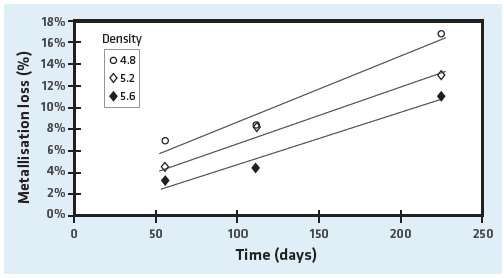
FIGURE 6.
Metallization loss over time of various HBI densities (courtesy of BHP Billiton Technology)
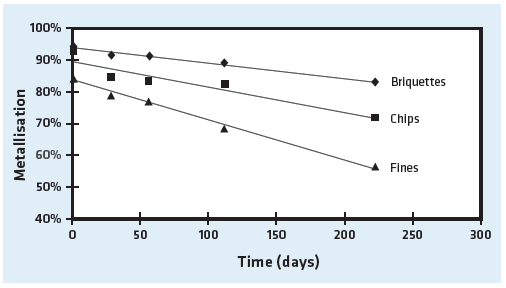
FIGURE 7.
Metallization loss over time of HBI, chips and fines (courtesy of BHP Billiton Technology)
DRI Reactivity Stages
Experience has shown that the DRI reactivity mechanism consists of the following stages and is the same for CDRI and HBI:
- Oxidation – DRI will slowly oxidize in storage in the same way as scrap. The resulting rust will reduce metallization over time.
- Steaming – DRI will absorb water when heavily wetted due to capillary action, or wicking. The exposed surfaces of a DRI pile will release water vapor (steam) due to the heat generated by the corrosion reaction. Piles will continue to steam until the water is evaporated and the material cools to ambient temperature.
- Hydrogen Generation – hydrogen gas can evolve when water is present during oxidation and corrosion, which poses a risk of explosion and is detrimental to breathing in enclosed spaces.
- Auto Ignition – DRI is not pyrophoric (a material that ignites spontaneously in air at or below 55° C/130° F) but neither is it an inert material. Therefore, DRI piles can reach the ignition point (>200° C/390° F) as a result of excessive fines or hot product in the pile, the presence of excessive water or as a result of prolonged oxidation or corrosion. The auto ignition tendency should be monitored closely because hydrogen can be generated, especially in the presence of saltwater, and without any flame present.
Various techniques have been developed to address the reactivity of DRI products (Figure 8):
- Natural aging – an oxide patina develops in first few hours after discharge when DRI is exposed to air. Naturally aged DRI is resistant to dry oxidation up to 50-60° C.
- Air passivation – fresh DRI is exposed to a gaseous environment containing a controlled amount of oxygen for 48-72 hours. The effect is similar to natural aging.
- Coatings – various materials have been tested and used to coat DRI, such as sodium silicate in solution and even wax. Proponents of coatings claim that dust is suppressed in addition to inhibiting DRI oxidation and corrosion.
- Hot briquetting – compaction of DRI while it is hot, which increases the density of the DRI thus reducing the specific surface area and porosity, thereby decreasing its reactivity. Proponents of hot briquetting claim that dust and fines generation are reduced in addition to making DRI more resistant to oxidation and corrosion.
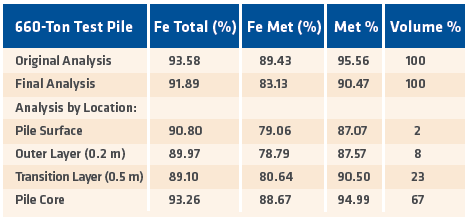
TABLE I.
SGI 6-month weatherability test results
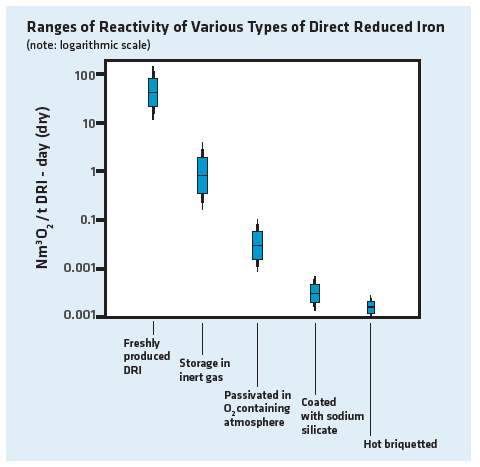
FIGURE 8.
Ranges of reactivity of various DRI products
HANDLING DRI PRODUCTS
To preserve product quality, care must be taken to varying degrees with each product. As a general rule, users should try to minimize any unnecessary handling of the product. A material handling system should be designed for the minimum number of transfer points required to move material from point A to point B and with the shortest drops. The easiest way to minimize the number of transfer points is to take material along the straightest path possible. However, care should be taken not to compromise metering and feed control in an attempt to eliminate all transfer points. Spillage from overloaded belts may lose more material than breakage through the extra transfer point of a feeder.
A typical DRI handling system associated with a captive DRI plant may include the operations listed in Figure 9.
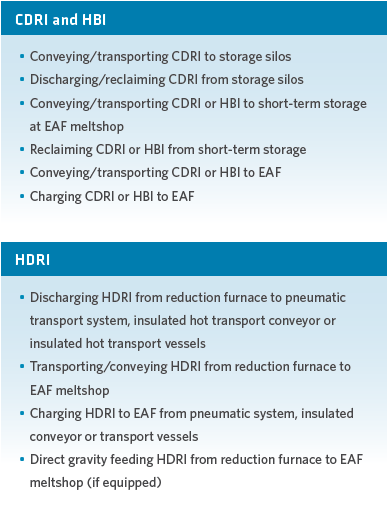
FIGURE 9.
Characteristics of various DRI handling systems
A frequently quoted estimate for CDRI breakage due to handling is 0.25% loss per 2-meter drop. This number can be much larger for weaker material, longer drops or poorly designed transitions. Fines and chips generated during handling will oxidize much faster than whole DRI products. A conservative number is 15% loss for -6.35 mm fraction material after exposed (outdoor) storage for a month.
HDRI can be transferred from the DRI plant to the meltshop by hot transport vessels, hot transport conveyors or pneumatic transport, depending on the distance between the DRI plant and the meltshop or by direct gravity feeding in the case of a close-coupled reduction furnace and EAF. Hot transport vessel systems employ ladle-type insulated vessels that are transported on flatbed trucks and can be maintained at temperature if the meltshop is delayed in accepting the HDRI. Pneumatic transport systems use gas to blow DRI at high velocity through pipes to carry it to the EAF or to a product cooler. The high velocity and resultant turbulence can cause significant breakage and erosion of the HDRI, especially at bends in the pneumatic line. This method can result in fines generation of as much as 8-10%. Hot conveyor systems using enclosed conveyor buckets are less jarring and greatly reduce HDRI fines generation.
STORING DRI PRODUCTS
DRI products are somewhat like fresh fruit. Although they don’t have an expiration date they are best consumed when “fresh.” As with fruit, this may not always be possible, so the products may need to be placed in storage to preserve their quality, and value.
HDRI is not intended for long-term storage but can retain much of its heat when needed to wait for a charging cycle or to be transported to a different nearby melting furnace. This is a temporary option when using hot transport vessels and not really an option with using pneumatic or conveyor bucket systems.
Outdoor Storage
HBI is normally stored outdoors in exposed piles built on a firm, well drained surface. Bulk piles of HBI tend to dissipate heat rapidly due to its good thermal conductivity characteristics and its shape and form that create voids in the pile. HBI, like scrap can also rust. Rusting has been observed to reduce its metallization by less than one percent per month even in salt-laden, humid air and frequent, heavy rainfall conditions (see TABLE I, page 13).
CDRI can be stored safely in open, well drained piles if it will not be moved until it is used in the meltshop. Rain can only penetrate the stack to a certain depth, typically less than a meter. Although the resulting corrosion will reduce the metallization, as described earlier in this article, the stack should not overheat unless additional material covers the wet area. This will insulate the wet iron and prevent the dissipation of the associated heat, which can cause the pile to overheat and can lead to ignition.
The following precautions should be followed when storing DRI products outdoors:
- Build pile on a firm base, such as concrete, and insure proper drainage to prevent the intrusion of water under the pile. The base should provide protection from moisture in the ground. A sealant layout of tar, bitumen or some other material impervious to water should be laid down before the concrete is poured.
- Avoid excessive fines content in the pile.
- In the case of cold DRI (CDRI), cover the pile to keep DRI dry and to prevent air stacking in the pile.
- Separate any DRI that has been wetted or has a temperature in excess of 65°C/149° F and follow the same precaution as for bins and silos.
A DRI pile will warm up to about 60°C/140° F as steaming occurs (see “DRI Reactivity Stages” earlier in the article) but will cool down again to ambient temperature when the water is evaporated. Normally it is not necessary to take additional action if the pile is steaming as long as the temperature does not exceed 100°C/212° F.
In case of a pile of DRI overheating to temperatures in excess of 100°C/212° F, the material should be removed from the pile and spread out on dry ground in a layer of about 0.5 meters using a track-equipped bulldozer or front end loader, as shown in Figure 10. Another method is to bury the pile under sand or other suitable material to cut off the oxygen supply.
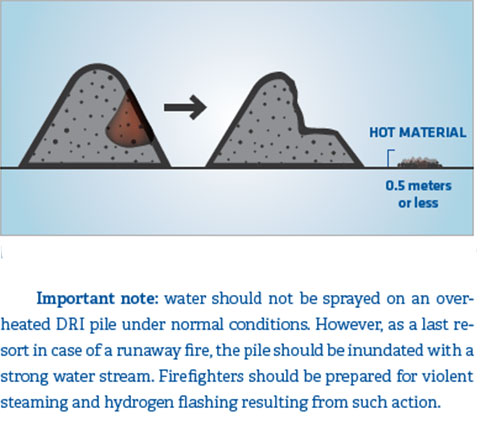
FIGURE 10.
Method for controlling hot material in a storage pile
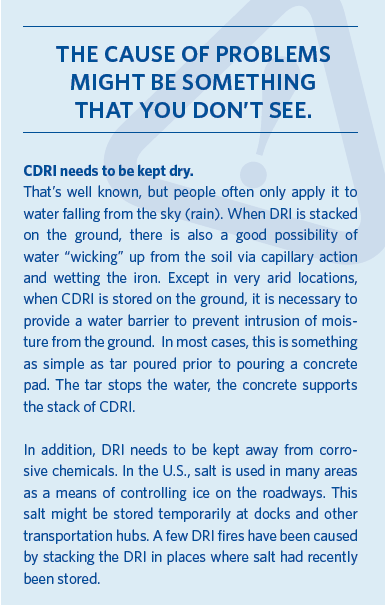
Storage Bins and Silos
Storage bins and silos are used to protect DRI products when there is a time delay between arrival and when the product can be used or shipped. Badly designed silos can create operational problems and a decrease of product quality. The design of silos should be determined always on the basis of the material flow properties of the bulk solid(s) to be stored. The expenses for testing and silo design are small compared to the costs of lost production, quality problems and retrofits that may be needed because of irregular flow patterns.
The following precautions are recommended when storing DRI products (Figure 11):
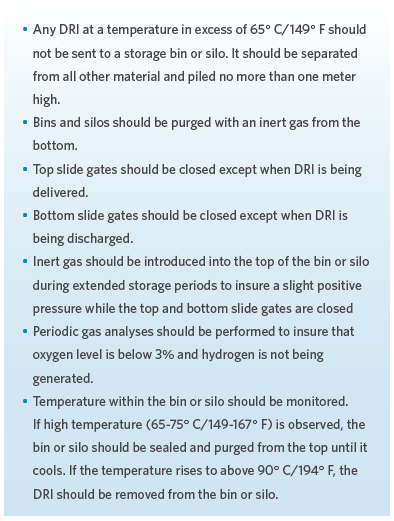
FIGURE 11.
Recommended precautions for storage bins and silos
TRANSPORTING AND SHIPPING DRI
There is a considerable body of knowledge pertaining to the physical and chemical characteristics of direct reduction products, which is derived from the collective experience of the industry since the 1970s. This knowledge provides the framework for the wording of a variety of standards and guidelines in use today. However, there is still a lack of understanding and appreciation of the proper methods and techniques for transporting and shipping these products.
Over the past 45 years, there have been a number of accidents involving direct reduction products. Many of these were the result of human carelessness or negligence when handling, storing and shipping these materials. Most of these accidents could have been avoided if the proper procedures had been followed. In other words, most hazardous situations can be avoided when the hazardous factors are fully identified, understood and controlled.
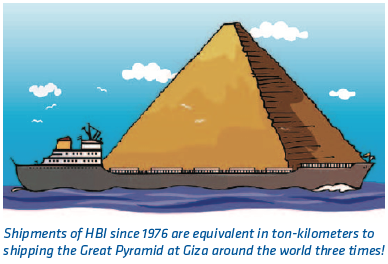
Experience with early ocean shipments of CDRI revealed the need for a product that was safer to ship and easier to handle and store. HBI was first introduced commercially by Fior de Venezuela in 1976 and became a globally traded product following start-up of the SGI plant in Malaysia 1n 1984.
Early tests of HBI showed that it is orders of magnitude more resistant to oxidation than other forms of DRI (see Figure 8 earlier in the article). In addition, the heat created by oxidation is more easily conducted through the briquettes; therefore, the heat does not collect within a bulk stack of HBI. The result of these two mechanisms (far lower oxidation rates and much better conduction of heat out of a stack) prevents the overheating and combustion of HBI.
Due to the much lower reactivity and higher thermal conductivity of HBI, the International Maritime Organization (IMO) in its International Solid Bulk Cargo (IMSBC) Code is considerably less restrictive on transporting HBI, or DRI (A), as designated by IMO. Perhaps equally important is that the Protection and Indemnity (P&I) Clubs, which provide insurance underwriting for oceangoing cargoes, consider that the only proven method of safely carrying non-briquetted DRI is by maintaining the cargo holds in an inert atmosphere throughout the voyage.
From 1970-2015, approximately 1.4 billion tons of DRI have been produced, nearly 300 million of which have been transported and shipped. Prior to the introduction of HBI, CDRI was primarily transported on land by truck and rail and represents more than 52% of all DRI products transported and shipped since 1970.
However, shipping CDRI, or DRI (B), as it is known in the IMSBC Code, is a complicated, detailed and potentially hazardous process. Nu-Iron in Trinidad and Tobago has been able to safely ship by ocean more than 9.0 million tons of CDRI since 2007 by following and improving upon IMO procedures and practices.
The following guidelines should be observed for CDRI and HBI alike when shipping by sea (Figure 12):

FIGURE 12.
Guidelines for shipping CDRI and HBI by Sea
In the case of CDRI, (IMO classification DRI B), the following additional steps should be followed (Figure 13):
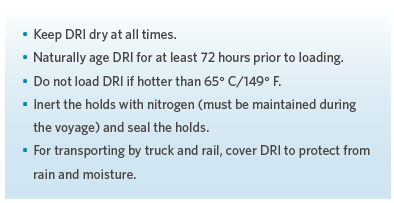
FIGURE 13.
Additional guidelines for shipping CDRI
A NOTE ON SAFETY: ADDING UP THE NUMBERS
Up to this point we have discussed issues in handling, shipping and storage that affect DRI product quality with the understanding that the loss of value means additional costs. Throughout we have noted safety precautions that although they do not improve product quality, none the less, impact financials.
It should be obvious, but workplace safety is a crucial part of any successful or prosperous business, and keeping people safe should be first priority. DRI products can be potentially dangerous under various conditions if not given the proper care. There are no cost savings worth the risks of shortcutting safety procedures when transporting and storing DRI products. Loss of life, injury, or destruction of property is costly on many levels. Direct cost to the company for a major accident include at a minimum: worker compensation claims, indemnity payments, and legal fees. Direct costs for a disabling on the job injury or death can quickly exceed seven figures.
The indirect costs are much more expensive over the long-term. The indirect costs of a lost time accident (LTA) will generally exceed the direct costs by a ratio of 4 to 1 or higher and compound into the millions of dollars in total cost over time. With the true costs of major injury accidents in mind, clearly the best way forward to stay with best industry practices and safety standards to help insure safest possible conditions.
SUMMARY
DRI is a versatile metallic iron for making steel. Its value is best determined by how it contributes to meeting the operational and productivity goals of those who use it. Each steelmaker operates a little differently; therefore, DRI must be not only highly metalized but also of consistent quality and versatile enough to satisfy the steelmaking process being used. Foremost to steelmakers is that DRI products arrive at the melting furnace in as close as possible to their physical and chemical condition as when they were made. All iron is reactive and will rust. DRI, by definition, is highly prone to react when in contact with air (oxidize) and when in contact with water (corrode). Rust robs DRI of metallization and can lead to dangerous and unsafe situations during storage and ocean shipping if proper procedures are not followed. How the materials are handled, stored, transported and shipped greatly influences the quality – and thus the value – of DRI products.
The good news is that users of DRI products have great control over maintaining the value of the DRI prior to melting by addressing various issues.
Whether you produce CDRI or HDRI to feed an adjacent or nearby meltshop, or purchase HBI or CDRI as a merchant material, it is a significant investment. By taking some well documented precautions and following procedures developed from decades of industry experiences, DRI products can be handled, stored, transported and shipped safely and steelmakers can realize the value of these versatile ore-based metallic iron sources.