Results of Lab Trials of MIDREX ACT™
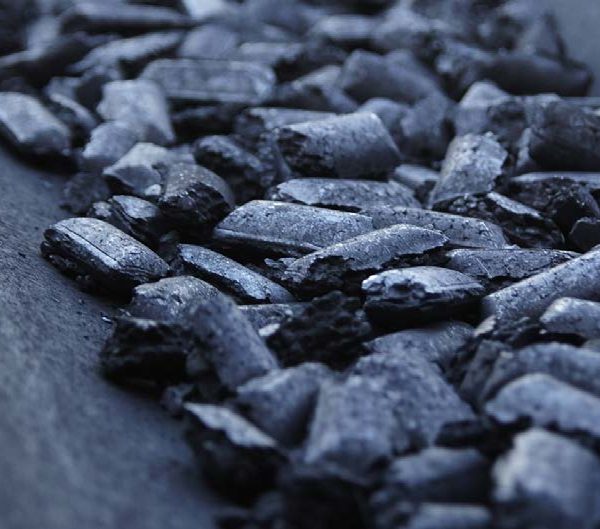
Modern electric arc furnaces (EAF) make better use of chemical energy; therefore, EAF steelmakers have greatly increased the use of carbon and oxygen as energy sources to reduce electricity consumption and increase productivity.
Ore-based metallics, such as pig iron and direct reduced iron (DRI), are frequently added to the EAF scrap charge for their pure iron units. However, many EAF steelmakers have espoused the practical benefits of higher carbon levels in DRI in recent years, making it more like pig iron in chemical composition.
By nature, the more carbon added to DRI products, the less iron the product will contain. There is no universal optimum carbon level established for DRI products, as the physical and chemical requirements are different for cold DRI (CDRI), hot DRI (HDRI), and hot briquetted iron (HBI) and are further influenced by the amount included in the metallic charge and the steel grade being produced. No application is the same, and product usage can vary greatly over time within a company, and even within a melt shop.
HBI currently is produced in the 1-2% carbon range because increasing carbon levels beyond that range would lower the briquetting temperature, which in turn would adversely impact product quality. In 2017, Midrex introduced the patented Adjustable Carbon Technology (ACT), which allows the plant operator to add carbon in DRI without sacrificing temperature and to independently control carburization and temperature over a wide range of operating conditions. This technology is available for both existing and new MIDREX® Plants and can be a unique differentiator for merchant HBI plants, as product quality can be tailored to the specific needs of the customers while maintaining the physical strength of the HBI which enables very high yield during transportation, handling, and melting.
THE NEED FOR VARIABLE CARBON IN DRI PRODUCTS
Although the primary appeal of DRI products in EAF steelmaking is for their virgin metallic iron units, the percentage of carbon within the DRI also can play a key role for the steelmaker (Figure 1). The percentages of carbon in DRI and the advantages of that carbon are situationally based on various steelmaking conditions (Figure 2). In the EAF, carbon is used: (1) to reach the required melt chemistry specification of the steel desired or for further refining; (2) to reduce any remaining FeO in the scrap or DRI; and (3), as an additional energy source to help melting.
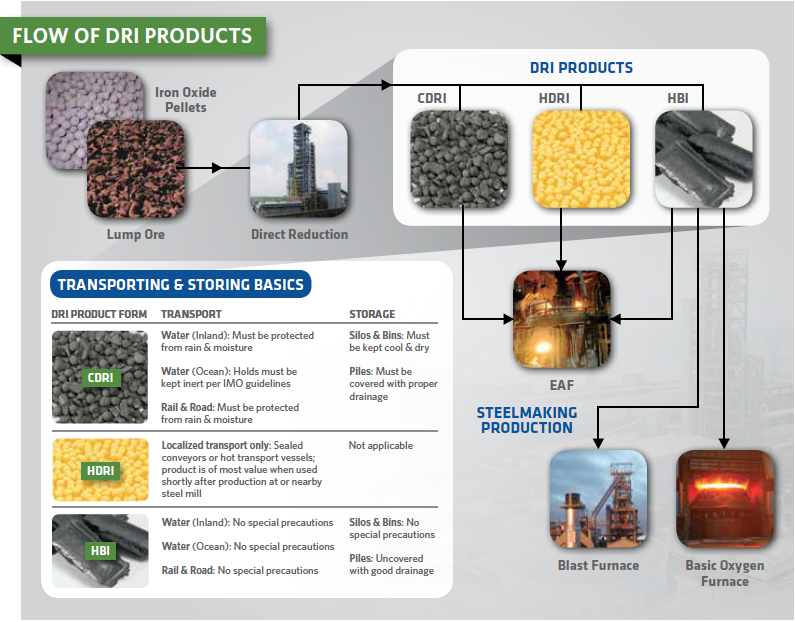
FIGURE 1.
Flow of DRI products in steelmaking
Carbon in DRI is first used to reduce any FeO to metallic iron (each 100 kg of FeO requires 16.7 kg of carbon). Therefore, DRI at 96% metallization will need less than 1.0% carbon for this purpose, while 93% met DRI will require about 1.5% carbon. Any remaining carbon is available for oxidation and can be burned to provide additional heat energy, supplementing the heat from the electric arc. Carbon can be added through injection into the EAF or charged as contained carbon in the DRI itself.
Carbon contained in the DRI can be very valuable to the steelmaker if it can be adequately utilized (Figure 2). The idea is to use the additional carbon to help melt the steel quicker to reduce tap-to-tap time and increase productivity. This is the primary reason that many EAF producers who mix scrap and DRI/HBI desire carbon levels above 3%. However, it must be noted that excessive carbon in the DRI will be in the bath until it is blown down with oxygen.
Thus, even though additional carbon can be viewed as an extra form of energy, it is possible to have too much carbon. This is defined as carbon that does not add any value to the production or further decrease the tap-to-tap time of a steel heat. Any carbon above specification of the steel after the iron is melted needs to be removed. The extra time consumed in decarburizing causes a decrease in productivity of the EAF.
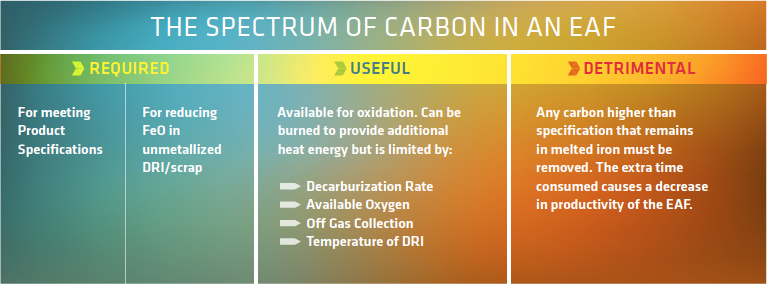
FIGURE 2.
The spectrum of carbon in DRI products
EFFECT OF VARIABLE CARBON ON PHYSICAL PROPERTIES OF HBI
Commercial HBI plants of any process have not produced HBI above 3% carbon in large quantities due to degradation of the HBI. Carburization by methane is endothermic, leading to lower briquetting temperature, which is very detrimental to the briquette quality. Temperature and carbon control are decoupled with MIDREX ACT, giving HBI producers the ability to adjust carbon while maintaining a high briquetting temperature. So, in addition to the known benefits of HBI in terms of yield and reactivity during transportation, HBI of various carbon levels can be produced with desirable physical properties of strength and density.
While the overall effect of carbon and temperature on HBI properties has been experienced by plant operators for years, there is very limited data available. Only one pilot-scale study has been published by Tenova HYL/Köppern(1), but it was very limited in scope. To our knowledge, there has never been a complete study on the effect of carbon and temperature independently on HBI properties.
According to the theories of powder metallurgy and compaction of metal powders, the overall strength of the resulting compact is proportional to the amount of plastic deformation during compaction. During plastic deformation, highly metallic particles interlock and form metallic bonds or “cold-weld”. The amount of plastic deformation is a function of the overall ductility and compaction parameters of the material, such as pressure and temperature. An increase in compaction pressure and compaction temperature increases the amount of plastic deformation, therefore, increasing the overall mechanical properties. Conversely, an increase in the amount of carbon present in the iron as iron carbide (Fe3C) will decrease the material’s ductility and lower the amount of plastic deformation and the mechanical properties of the compaction. Losses in compaction strength of iron due to carbon addition can be offset by an increase in compaction pressure and temperature.
TESTING METHODOLOGY AND ASSESSMENT OF HBI QUALITY
The development of MIDREX ACT involved various tests to better understand how the technology would impact DRI product quality, especially the density of HBI, and to minimize scale-up risks. Our approach was to conduct several bench-scale tests that were cheaper and easier to perform, then increase to pilot-scale, and ultimately move to commercial-scale. For our study, we started with hot compaction tests, then moved to our hot briquetting pilot plant, and finally confirmed trends in industrial plant trials.
Drawing from the vast experience and plant data of Midrex, all tests performed in the lab used commercial pellets and conditions like in existing MIDREX HBI plants for benchmarking purposes. It is important to note that these tests were meant to be comparative, not absolute. Results from hot compaction cannot be extrapolated to an operating HBI plant because there are too many variables that cannot be replicated on a small scale. We were looking for trends and confirmation that those trends could be scaled up.
Density is a very important characteristic for merchant HBI and affects how it is shipped around the world over international waters. The International Maritime Bulk Cargoes Code (IMSBC), published by International Maritime Organization (IMO), defines HBI as, “Direct Reduced Iron (A), produced by reducing iron oxide lumps, pellets, or fines and compressing at a temperature of at least 650°C to achieve an apparent density of 5.0g/cm3.” It should be noted that domestic HBI shipments by rail or truck are not subject to the density requirements of the IMSBC.
Compacts and briquettes produced for the trials were analyzed at the Midrex Research and Technology Development Center. HBI apparent density was measured according to ISO 15968:2000, and HBI tumbling index according to ISO 15967, although Midrex uses 6.7mm screen rather than 6.3mm and hot compactions are tumbled in a 0.5m tumble drum for 100 and 300 revolutions.
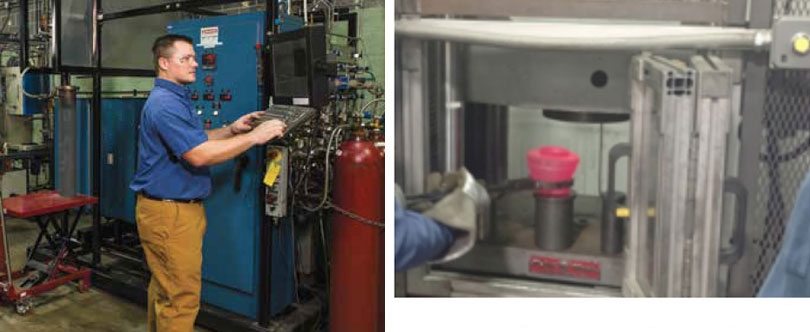
FIGURE 3.
Reduction furnace and hot compaction test apparatus
HOT COMPACTION TESTS
Hot compaction tests (also called piston-tests) are designed to simulate the hot briquetting process by placing approximately 180g of HDRI into a die that is pressed hydraulically. While the productivity is very low, this method gives us the ability to control many variables for parametric studies and does not require large DRI samples.
We have access to DRI produced in MIDREX Plants or we can produce our own DRI in small, medium, or large batches (Figure 3). With these furnaces, we can replicate DRI produced in operating plants, make DRI with untested iron ore, and make DRI outside of typical production ranges as needed for testing. All furnaces have full control of reduction/carburization time, temperature, and gas composition so we can optimize the desired metallization (%met), carbon (%C), and cementite (%Fe3C). The limitations are that these furnaces are externally heated (i.e. not adiabatic), batch processes and the bed does not move, as in a MIDREX® Shaft Furnace. For the hot compaction tests, we used the medium furnace that produces batches of 1,500g of DRI.
TEST PROCEDURE
The hot compaction equipment design and test procedures were developed in collaboration with Köppern Equipment, Inc. The DRI samples and dies were pre-heated according to our Figure 3. Reduction furnace and hot compaction test apparatus established procedure, which also defines heating rates and soak times.
The pre-heated die is placed under the piston press and the hot DRI vessel is placed on top of the die. Hot DRI is then discharged into the die by opening a slide gate on the bottom of the preheat vessel. For safety reasons, the steel door must be locked. Compression is triggered by two buttons on opposite sides of the door. Pressing force and pressing time are controlled by the PLC. Despite all the controls in place, proper execution and timing by the technician is critical to obtain quality data. For each data point, a total of 6 compacts are made: three samples are used for compression testing and for chemical analysis while the remaining three are used for tumble drum testing.
Validation tests were performed to verify repeatability and reproducibility. Based on Midrex experience with commercial HBI, we used oxide pellets from two different plants and made DRI in the lab according to our procedures. One supply of oxide is notoriously difficult to briquette commercially, while the other is much easier. Under the test protocol developed, we saw a difference between strong and weak compacts as shown in Figure 4.
A complete parametric study was performed and documented by Andrew Ruthenbeck of the Midrex Research & Development Technology Center(2) to quantify that effect over a larger scale than what can be achieved in commercial HBI production. However, in this article, only the key findings are presented.
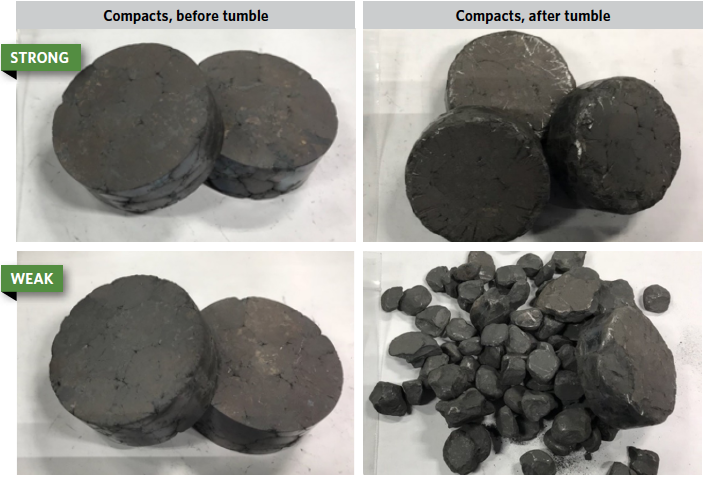
FIGURE 4.
Compacts before and after tumble
EFFECT OF TEMPERATURE
From many years of plant operation, it is well known that the DRI temperature during the briquetting process is the dominant factor in HBI quality. The next series of tests was designed to quantify that effect over a larger scale than what can be achieved in commercial HBI production. Temperature also affects factors like segment life, but this cannot be studied at laboratory scale.
The temperature in Figure 5 is the pre-soak temperature of the DRI prior to compaction. Some temperature loss is expected during the handling of the DRI prior to the compaction, but it cannot be measured accurately. Regardless, Figure 5 shows that the DRI temperature has a strong effect on both density and strength.
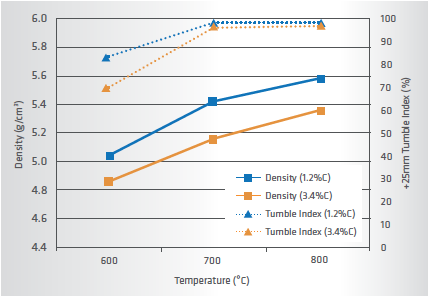
FIGURE 5.
Effect of DRI temperature on compact quality, for low and high carbon DRI (200MPa)
EFFECT OF CARBON
In this test, DRI was produced in the lab-scale reduction furnace at various levels of carbon from two commercial iron ore pellets. It was produced at a high degree of metallization to minimize carbon loss during reheat – all compacts finished above 97% metallization. Similarly, carburization was designed to achieve an elevated level of cementite to account for losses in reheating.
Figure 6 shows the expected decrease in density, as iron is being displaced by carbon, which is less dense. The curves are explained solely by mass balance and no other factor comes into play. This means we can extrapolate HBI density as a function of carbon for existing plants interested in MIDREX ACT.
Tumble index decreased with increasing carbon, as expected. However, the decrease in strength was not steep in the range of interest. If the key parameters of DRI temperature and pressing force are maintained, strong compacts can be produced at higher levels of carbon. Even above 4.5% carbon, there is sufficient plastic deformation to create the strong metallic bonds for a strong compact.
LESSONS LEARNED
Not surprisingly, this parametric study confirmed the theory, and the observed behaviors in a commercial plant- temperature and pressing force- have a strong influence on briquette quality. Under the right conditions, any DRI can be made into strong compacts or briquettes. However, this small-scale testing allowed us to isolate and quantify the relative effect of those variables individually. While the results obtained on density and tumble index are not to be extrapolated to plant performance, we can see the relative impact of these factors that are known to effect HBI quality- DRI temperature and pressing force- have a more significant impact than carbon.
The key learning from this study was the definition of a test protocol (matrix) that can estimate the briquetting performance of a given ore. The results also were benchmarked against known ores used to produce HBI in MIDREX Plants. Therefore, for a small investment, we can make a go/no go decision on whether to proceed to larger scale testing and minimize risks doing so.
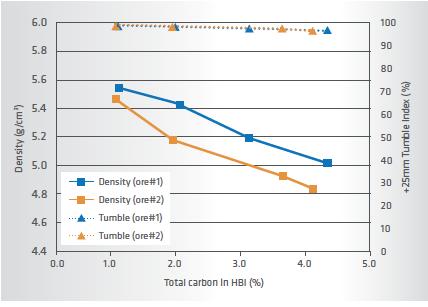
FIGURE 6.
Effect of total carbon on compact quality (700º C, 200MPa)
HOT BRIQUETTING TESTS
The hot briquetting tests were conducted following a similar approach to hot compaction. First, the DRI was made in the large reduction furnace, where reducing/carburizing gases were preheated, then passed through a fixed bed of DRI. The typical batch size was 400kg. After achieving the desired DRI quality, the retort was emptied carefully, keeping track of the location of the material in the retort. Each layer was analyzed independently (metallization, carbon and cementite). Depending on the desired DRI quality, layers were either mixed within a batch or combined with other batches (made under identical conditions) to minimize the variability of the material.
After carefully homogenizing, the DRI was loaded into a conical transfer vessel, which was then loaded in the furnace and heated under inert atmosphere. The heating profile is critical to maintaining carbon as cementite, rather than dissociating it into iron metal and graphite. The target DRI temperature for all data presented in this article was set to 750°C, which then cooled during transport to the briquetting press. Once the center bed thermocouple reached the desired temperature, the retort was lifted over the Köppern briquetting machine. Proper execution and timing was crucial so the DRI does not lose excessive temperature in the transfer. DRI temperatures at the feed screw were approximately 700°C. Both DRI and HBI temperature were measured and recorded for each test. The steady-state HBI temperature varied for each test around 680°C.

FIGURE 7.
Large reduction furnace and HBI coming off the Köppern press
Compared to a commercial HBI plant, our machine has smaller diameter rolls (0.75m vs. 1.0m typical) and operates at lower speed and lower pressing force. The other key limitation is that the dies are not preheated and do not achieve steady-state during the ~2-minute run. The operation setpoints were selected based on several trials using known / commercial iron ores, with the aim to produce a HBI that has similar properties (such as density) to a MIDREX HBI Plant where the ore is used. In other words, the pilot-scale briquetter is used to produce HBI realistic to an actual MIDREX HBI Plant.
The HBI was discharged into a pan. Immediately after the test, the HBI produced in near steady-state was segregated from the beginning and end-of-run material, which is of lower quality. It was spread and allowed to cool in ambient temperature. Initial trials with quenching the HBI did not indicate any significant difference in product quality.
After cooling, the HBI was tested for chemistry (metallization, carbon, and cementite) and used for physical testing. All test runs experienced a minor loss in carbon and a reversion of cementite (Fe3C) to iron and carbon, despite our best efforts to minimize this loss. This is strictly due to heating and cooling in a large fixed-bed retort.
After cooling, the HBI was tested for chemistry (metallization, carbon, and cementite) and used for physical testing. All test runs experienced a minor loss in carbon and a reversion of cementite (Fe3C) to iron and carbon, despite our best efforts to minimize this loss. This is strictly due to heating and cooling in a large fixed-bed retort. Both graphs in Figures 8 and 9 show the HBI analysis, not the analysis of the DRI that was used to make it.
Figure 8 shows the effect of carbon on the HBI density for three different commercial iron ore pellets. The density is the average of five briquettes for each test. As expected, density decreases with increasing carbon for a given iron ore.
The effect of total carbon (in HBI) on the HBI strength is plotted in Figure 9. The tumble index is measured using a 1000 mm diameter drum with 500 mm width for 200 revolutions at 25 rpm. In this graph, we elected to show the +6.7mm tumble index, as it is more representative of strength in relation to yield losses.
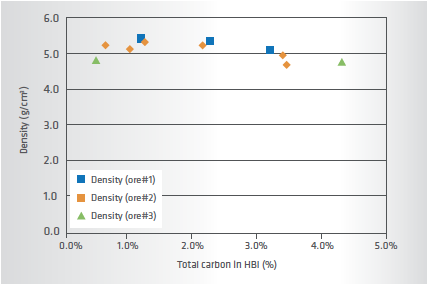
FIGURE 8.
Effect of carbon on pilot-scale HBI density for 3 different iron ores
The trend clearly indicates that increasing carbon reduces HBI strength, but this effect is limited in the carbon range of 1% to 5% (with other key briquetting parameters kept nearly constant). Strong HBI can be made even at high carbon, provided that the DRI is briquetted with sufficient temperature.
For these tests, we focused the hot briquetting tests on varying carbon/cementite, using three commercially available iron ore pellets. The trends observed are identical to the hot compaction tests: the presence of carbon does impacts the physical properties of the HBI:
- For density, the relationship is linear and according to the mass balance (where the weight of iron is displaced by carbon). While not surprising, this is a good point to prove. Density can be estimated based on the carbon content of the DRI, and there is no additional risk.
- The strength of HBI decreases with increasing carbon (at a given briquetting temperature), but maintains adequate strength over a wide range.
While we cannot extrapolate the results to a commercial plant, we expect this trend to remain. Presently, there are no HBI plants of any process that can independently control carbon and temperature so this testing cannot be replicated at the commercial scale.
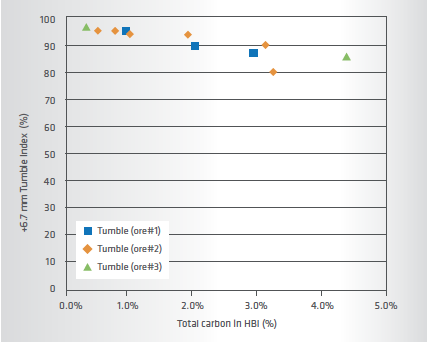
FIGURE 9.
Effect of carbon on pilot-scale HBI quality for 3 different iron ores
The first implementation of MIDREX ACT is currently under construction. In June 2017, Cleveland-Cliffs, Inc. announced that Toledo, Ohio, will be the location of the company’s first MIDREX HBI production plant. The plant will have a nominal capacity to produce 1.6 million metric tons of HBI per year and will be able to supply high-quality, customized HBI to the Great Lakes region. The project broke ground for construction on April 11th, 2018, with the estimated production of HBI slated for mid-2020. Carbon in the HBI will be in the range of 1.8% to 3.0% with 95% metallization.
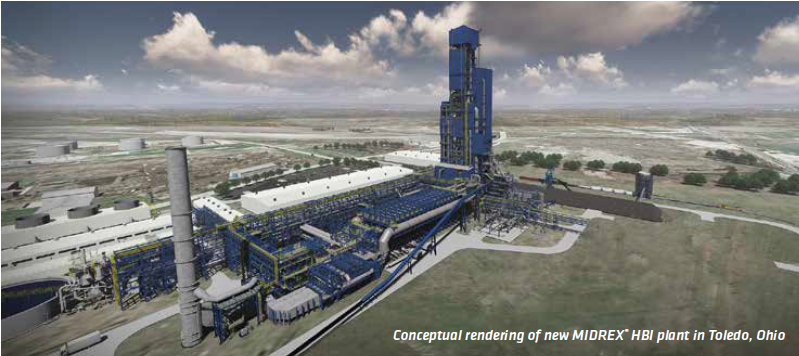
OVERALL CONCLUSIONS
For the nearly five decades that the MIDREX® Process has been in use, product carbon levels have varied based on location and use by plant. These levels have been historically in the range of 0.5% to 3% for CDRI. HDRI and HBI targets were lowered due to the endothermic carburization reactions, coupling product carbon and discharge temperature. MIDREX ACT was developed at the Midrex Research and Technology Development Center to provide a means to increase the carbon content of DRI up to 4.5% carbon without temperature loss. Temperature loss is particularly important to producers of HDRI and HBI. For example, HBI producers will benefit greatly from this innovative technology because carbon can be increased to meet specific customers requirement without affecting briquetting temperature. This is critical for making strong briquettes to achieve high yield during transportation and handling.
To minimize scale-up risks, Midrex undertook a series of tests at bench and pilot scale to quantify the impact of carbon/cementite on HBI properties, independently of temperature. The results showed that there is a measurable reduction in both density and strength of the HBI as carbon increases for a given ore. However, the HBI maintains adequate strength over a wide range of carbon (at a given briquetting temperature). Therefore, we expect that HBI produced with MIDREX ACT will maintain is transportation advantages, superior yield, and lower reactivity over DRI while providing a value-added product tailored to meet specifications of their end users (such as carbon content).
(The author wishes to recognize and thank Andrew Ruthenbeck, Mike Lamb, and the Midex Research & Development Technology Center staff for their work in conducting the tests and analyzing the data described in this article.)
References:
- High Carbon Briquettes (HCB) – The future of briquetted DRI. HYL News. December 2016.
- Ruthenbeck A., Lamb M. and Chevrier, V. Hot Briquetting Trials with variable carbon DRI. AISTech 2018. Philadelphia, PA, USA.
EDITOR’S NOTE:
For more information about MIDREX ACT, please see the article titled, “INCREASING CARBON FLEXIBILITY IN MIDREX DRI Products: Adjustable to 4.5%, Excellent Temperature Retention With ACT,” in 3Q2017 Direct From Midrex or download the brochure titled, “MIDREX ACT- Achieving Higher Carbon in MIDREX DRI Products,” from the Midrex website: www.midrex.com.