Quality & Performance Assurance: Reformer Management & Catalyst Optimization
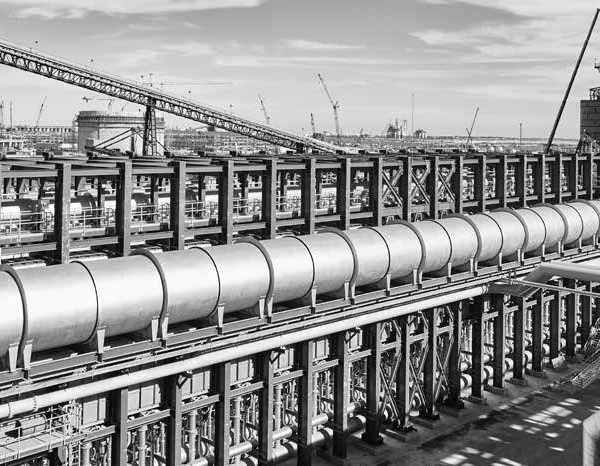
INTRODUCTION
Except for our homes, the motor vehicles we drive usually are our largest and most important purchases. Therefore, we want to keep them in good working condition so they operate reliably and at peak performance for as long as we own them.
We have options for servicing our vehicles, as well as for replacing parts and equipment. We can go to where we purchased them for service and to buy replacement parts or we can shop for a mechanic and parts that fit. When making these decisions we look for value – what it will cost weighted against performance expectations, supplier reputation, and peace of mind. Seldom are value decisions made on price alone.
Multiply the price of an automobile by 10,000 and that is approximately the investment involved in a direct reduction plant. So, is it worth taking a long-term risk for a short-term gain when choosing a services provider and buying replacement parts and materials?
INNOVATIVE TECHNOLOGY TRANSFER
Contrary to the typical practice of US companies in the 1970s, Midrex sought to enter offshore markets through cooperative technology transfer agreements rather than direct investment and control of production plants. As a result, the customer service function has evolved alongside the global expansion of the MIDREX® Process. As the number of plants increased over the years, Midrex tailored its customer service function to maintain regular communication, close cooperation, and an open dialogue with plant operators. Today, two groups are designated to support MIDREX® Plants: Technical Services and Global Solutions.
The Technical Services staff consists of experienced professionals, most of whom have worked in MIDREX® Plants and understand first-hand how plants are operated and maintained. They are uniquely qualified to interact with plant management and staff to diagnose and troubleshoot problem areas and make recommendations that can improve productivity, reliability, product quality, and safety.
When more in-depth assistance is needed, Global Solutions has dedicated program managers who work closely with the plants to develop sustainable solutions. They are equipped with a platform of advanced digital tools (see the article, “DIRECT REDUCTION IN THE DIGITAL AGE Introducing MidrexConnect™” in this issue of Direct From Midrex) and the body of knowledge and experience that has been developed over 50 years of designing and servicing MIDREX Plants.
THE REAL DEAL
Two examples of how Midrex uses digital technology and a keen sense of purpose to benefit clients involve the MIDREX® Reformer. The reformer is the engine room of a MIDREX Plant, where the reducing gases that power the reduction reactions in the MIDREX® Shaft Furnace are produced. The MIDREX Reformer is a refractory-lined, gas-tight, welded steel box, which is kept at slightly negative pressure to prevent gas leakage. The reformer contains hundreds of catalyst-filled alloy tubes, which are anchored at the roof of the reformer and allowed to expand downward. The bottom of the tubes is covered by a flexible expansion seal to prevent air intrusion into the combustion chamber of the reformer. The reformer box is anchored in the center and is allowed to expand freely lengthwise in either direction on a series of lubricated bearing plates.
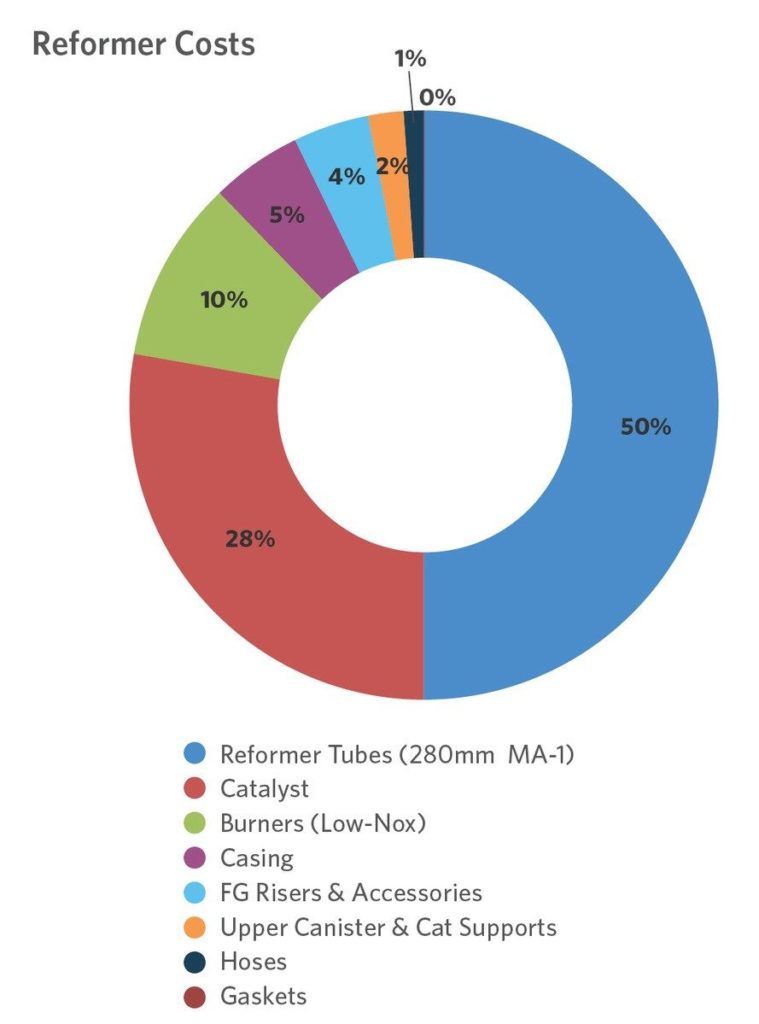
FIGURE 1. Cost Breakdown of a MIDREX Reformer
Together, tubes and catalyst comprise about 78% of the cost of a MIDREX Reformer (Figure 1) and are usually replaced every 8-10 years. Only Midrex has the first-hand design knowledge and process expertise to look beyond the materials to how they affect overall plant performance. As the developer of the MIDREX® Process, Midrex has the knowledge, expertise, and vision to manage the health of the entire plant. Remote Professional Services (RPS), powered by the MidrexConnect digital platform, can detect issues before they become problems and provide the basis for solutions that prolong the useful life of the tubes and catalyst, as well improve overall plant performance.
REFORMER MANAGEMENT
RPS, which digitally transforms data into actions, is at the core of Midrex reformer management solutions. As its name implies, RPS allows Midrex engineers in the Charlotte home office to look at all areas of a MIDREX Plant in real-time for process variables or equipment settings that impact reformer performance or equipment and materials longevity. With RPS, data is collected digitally for analysis and evaluation, which leads to recommendations for adjustments or other optimization actions, the effects of which are remotely observed, and the data continues the cycle (Figure 2).
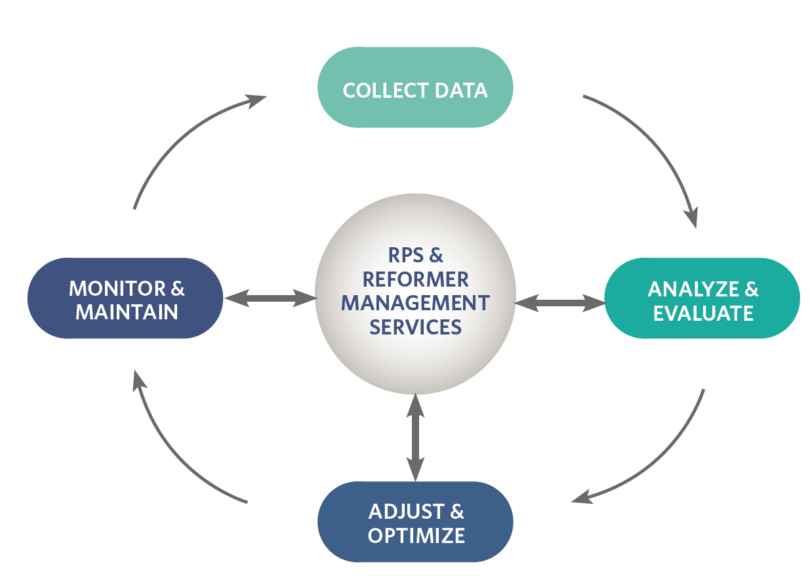
FIGURE 2.
Reformer Management Solution Cycle
RPS reviews data on tube and catalyst conditions in real-time and creates a profile of the reformer’s operating history that can be viewed on-demand. The data includes reformer tube roof and floor thermocouple temperatures and thermal reversals, H2/CO ratios, gas quality (ratio of reductants to oxidants), and hydrocarbon levels. The data collected is used during the analysis phase to check for thermal imbalance of the reformer at various operating conditions and to avoid carbon buildup on the catalyst.
Midrex is developing real-time measurement of tube growth. This would make possible more accurate skin temperature measurements during operation, which result in more precise theoretical vs. actual creep calculations. “Pop-up” warnings of high thermocouple temperatures will eliminate the possibility that an imbalance might be missed, and easier-to-read system screens (Figure 3) will facilitate quicker identification of a problem area and predictive cost-saving corrective actions.
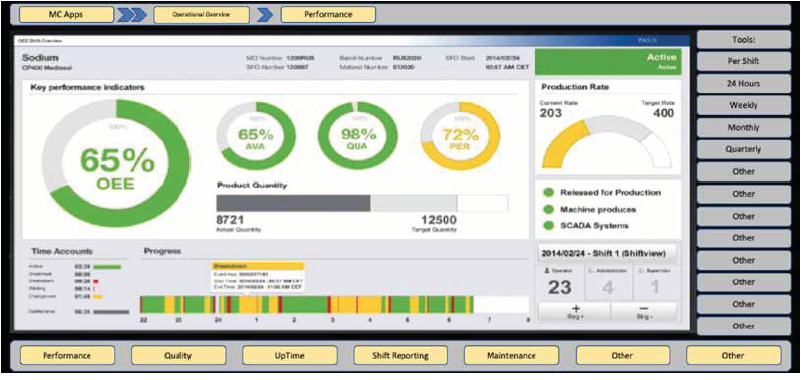
FIGURE 3.
Example of Enhanced RPS System Screen
What RPS Does:
- Observes reformer operation continuously
- Assists plant personnel in standard data collection
- Evaluates data based on Midrex design and operating philosophies using the MIDREX® SuperData program and proprietary diagnostic software
- Facilitates periodic inspections
- Issues daily, weekly or on-demand reports
How RPS Is Used:
- Confirms that scheduled maintenance adjustments were made
- Suggests when mechanical adjustments are needed, such as to support springs
- Checks that reformer is thermally balanced
- Avoids carbon buildup on catalyst
- Determines when catalyst needs to be topped or replaced
- Identifies and monitors problem tubes
- Provides basis for recommended actions and operational adjustments
The Midrex Reformer Management Program can benefit a plant in a variety of ways. Performance of reformer tubes and catalyst can be watched over their entire life cycle, which reduces the risk of unplanned shutdowns, unexpected maintenance issues, and premature tube and catalyst failure. Tubes that are suspected of having problems are readily identified, evaluated to determine the best corrective action, and monitored closely. RPS data provides easy to follow diagnostic analysis that shows if tube changes are of a technical nature or are time-related or if gas ratios or quality are affecting catalyst activity. This aids in making informed mechanical decisions and operational adjustments that can improve reformer performance and extend tube and catalyst life. Access to real time, on-demand data takes much of the guess work out of planning for purchasing equipment and materials and the allocation of plant human resources, which translates into greater plant productivity and overall cost savings.
The digital power of RPS, backed by the process design and integration expertise of Midrex, provides plant managers the peace of mind that the mechanical condition and operational performance of their reformer is being properly monitored, managed, and maintained.
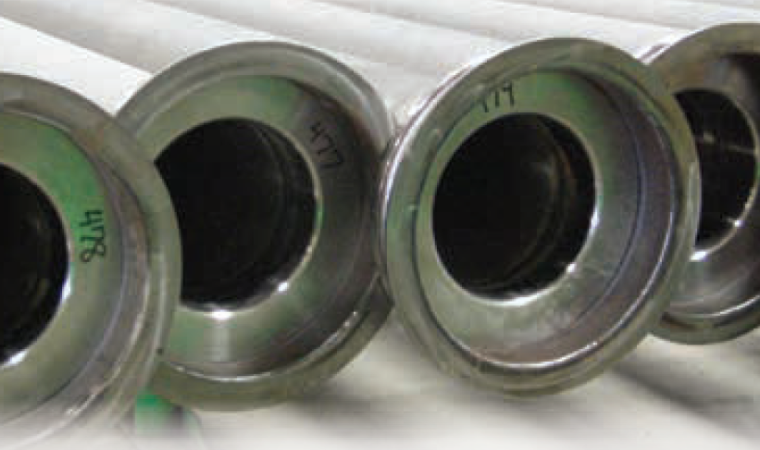
MIDREX® Reformer Tubes
MIDREX Reformer Tubes are designed and manufactured for long operating life and superior performance. Midrex offers several types of alloy tubes made from high performance metals backed by value assurance programs to assist in arranging financing and in managing reformer operation.
Traceability, a unique feature of Midrex supply of reformer tubes, is a prime example of how Midrex brings added value to the client relationship. Midrex maintains serial numbers and other markers that identify where and when tube assembly took place and even who performed the welding through installation of the tubes. A portion of the tubes are marked and installed in a specific manner to allow for better observation and more accurate eddy testing. This, coupled with a running log of tube performance, allows issues to be traced back to their source to facilitate timely corrective action.
CATALYST OPTIMIZATION
Midrex has a long history of developing catalyst formulations and creating loading profiles to match the operating practices and business goals of MIDREX Plants. As performance demands have increased, Midrex has responded with modern, high efficiency catalysts and the skills and expertise to maximize their value.
As shown earlier in Figure 1, catalyst makes up about 28% of the cost of a MIDREX® Reformer, and throughout the life of a MIDREX® Plant the catalyst will need to be added to or replaced several times. Catalyst manufacturers can tell a plant what the expected life of the catalyst is under “normal operating conditions,” but what if conditions are not “normal” or the catalyst profile in use is not the optimal solution.
For example, Global Solutions received a tender document from a MIDREX Plant for replacing its catalyst based on a profile developed many years earlier, when the plant configuration was different. Upon discussion with the client, it was learned that the plant has a history of changing conditions (including operating temperature, compressor capacity, natural gas quality, and heavy hydrocarbons), Midrex decided to ask about the plant’s operational goals and the current operating conditions, such as feed materials and gas quality and ratios.
Through a series of discussions during which reformer tube pressure drop and prior catalyst performance were reviewed and discussed, a joint decision was made to focus on the heavy hydrocarbons and carbon formation in the reformer tubes. Because of the change in heavy hydrocarbon, it was found that frequent carbon burnouts were needed to correct carbon deposition on the catalyst. Historically, the plant did carbon burnouts almost monthly in the first year of operation, increasing exponentially to weekly by the end of the catalyst’s life. A burnout is used to remove carbon that builds up in the tube and settles on the catalyst. Oxygen is introduced to increase the temperature inside the tube, which carries with it the risk of thermal cycling the tubes and catalyst. Reformed gas preparation is interrupted for 4-6 hours, which means lost DRI production.
Working with the plant personnel, Midrex was able to evaluate the situation in relation to overall plant operations and recommend changing the catalyst profile, which produced broad-reaching benefits. By slightly decreasing the activity of the catalyst, less carbon was deposited on the catalyst requiring fewer burnouts and increasing the time for producing reformed gas. Wear and tear on the tubes and catalyst was reduced, likely extending their effective life, and overall plant performance was optimized.
Ways Midrex Adds Value:
- Knowledge of process beyond the parts (whole is greater than sum of its parts)
- Operational knowledge (in-house and other plants)
- Custom simulations & proprietary software (MidrexConnect digital platform)
- Manage solutions (inquire, obtain, and process information & data)
- Reach mutually rewarding conclusion
Midrex approaches every replacement equipment, spare part, and material supply opportunity with the same goal: to provide the most cost-effective solution that meets the client’s goals. Plant personnel are expected to focus on their area of responsibility. Midrex is uniquely qualified as the designer of the process technology to recognize how a part, piece of equipment, or material affects the entire plant. By understanding the plant goals and partnering with clients to identify the cause and effect of issues, Midrex can bring together the right decision-makers to craft a sustainable solution.
After a solution is agreed upon and a course of action is determined, Midrex leverages its relationships with quality manufacturers and vendors worldwide to assure a competitive price and timely delivery. By functioning as a plant’s representative in dealing with equipment manufacturers and vendors, Midrex frees up plant operations and administrative personnel to focus on other tasks that require their personal attention and expertise.
BUILDING ON COOPERATION
Global Solutions embodies the spirit of innovation, opportunity, and cooperation that has been at the heart of the Midrex technology transfer philosophy since start-up of the first plant in 1969 (Figure 4). Through the years, Midrex has provided plant personnel process knowledge, training, and assistance, and the relationship of Midrex and its Process Licensees has expanded and grown.
Today, Global Solutions continues to build on that tradition by working with MIDREX Plant personnel to address issues specific to their local conditions and business models, such as optimizing operations, improving productivity and availability, maximizing product quality, and enhancing and protecting assets – human and physical. This is why Global Solutions is the only plant services provider that can guarantee that its solutions are designed and manufactured to exact Midrex specifications and backed by 50 years of unparalleled success.
The results speak for themselves – MIDREX Plants are the best performing plants in the direct reduction industry.