Direct Reduction in the Digital Age – Introducing MidrexConnect™
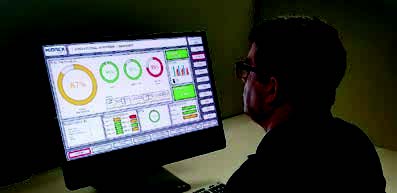
The Greek philosopher Heraclitus of Ephesus (c. 500 BC) said, “Change is the only constant in life,” which has been popularized as, “The only thing constant is change.” However, it doesn’t really matter whether we see change as an always-to-be-expected condition or as something that is occurring continuously; it’s how we respond to change that makes the difference.
Industrialization is an example of change, when agricultural societies turned to producing manufactured goods and services on a wide scale. The first so-called Industrial Revolution began in the mid-1700s, with the transition from hand production methods to machines. In the late 1800s, machines advanced to become more efficient and gave rise to the second Industrial Revolution, known as the Technological Revolution. Despite significant advances in the design and capabilities of machines, it took 20-30 years for the processes that make use of these machines to change and usher in the third Industrial Revolution, characterized by computerized automation.
Today, a fusion of technologies is blending computerized automation with digital data exchange to create the “smart factory,” which promises to take manufacturing to new levels of performance and efficiency. This is being called Industry 4.0 – the fourth Industrial Revolution.
INDUSTRY 4.0 SOLUTIONS
Industry 4.0 draws from the advancements of processes, methods, and strategies across multiple industries and integrates them into collaborative information platforms, providing access to information for many different consumers to use. These consumers can be human or machine, as both now can learn from the information being gathered. In parallel it leverages the recent leaps made in computing technologies, cloud infrastructure, enhanced internet connectivity, and virtualization, to build cyber-physical representations of our physical world. Overlay of these two areas; information platforms and virtualized physical worlds is yielding a revolution called Digital Transformation, which in short is the harnessing of these technologies to find and implement new competitive advantages that were once unthinkable to customers.
Industry 4.0 strategies look different across various industries. The oil & gas industry uses condition-based monitoring to determine asset health, predictive maintenance to automatically create workorders and generate purchase orders for replacement parts, and remote assistance to solve real-time problems. In the airline industry, condition monitoring and situational awareness are used to notify airline pilots when a system is outside of normal range and to help them make faster decisions, while predictive maintenance allows better management of asset downtime, and remote analysis & assistance is available via satellite. The utility industry uses predictive maintenance to access the impact of required maintenance and plan accordingly and situational awareness tools to filter “noise” and focus on critical metrics.
However, common across all industries is the need for a collaborative information sharing platform (Figure 1).
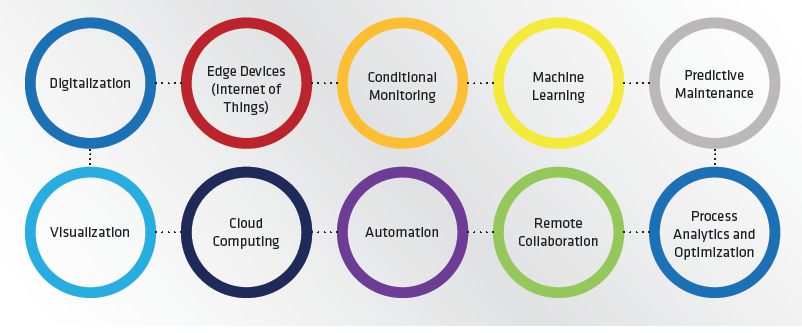
FIGURE 1.
Information components of a collaborative information sharing platform
INTRODUCING MidrexConnect™
Midrex has developed MidrexConnect™, a collaborative services platform to centralize the viewing and analysis of asset and operational data essential for plant operators to achieve their goals, whatever they may be – productivity, availability, quality, or longevity. MidrexConnect™ can access plant data in real time from the Midrex home office by Web-based viewing of process variables that impact plant performance and can interact with all areas of the production process. This enables Midrex to provide plant operators the information they need to make fast, informed decisions.
The MidrexConnect™ platform integrates three key information hubs: Asset Management (AM), Operational Management (OM), and Maintenance and Materials Management (MM), as shown in Figure 2. Each hub includes data and information from Midrex, MIDREX® Plants, industry partners, and vendors. Clients can choose what type and how much data to make available to other parties.
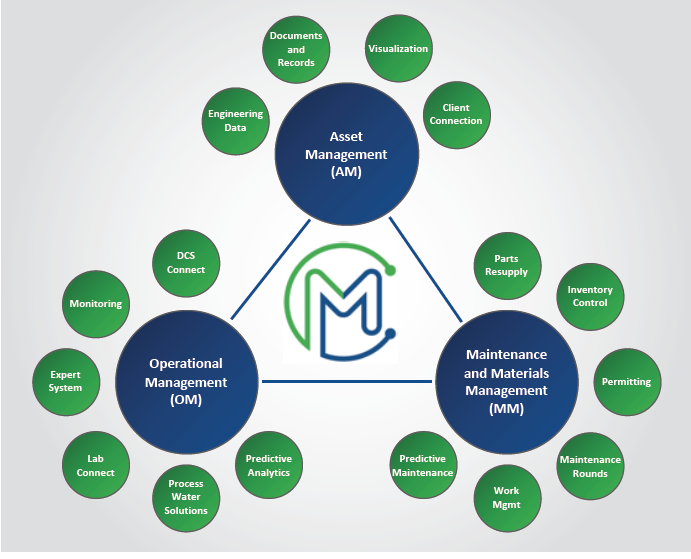
FIGURE 2.
MidrexConnect™ platform overview
Asset Management
An interactive digital portal allows plant personnel to access valuable information including engineering documents and data, training and operations manuals, maintenance records, and vendor documentation. The information is displayed in 3D, which creates an immersive plant experience and results in increased asset efficiency.
Operational Management
The operational portal provides a real-time view of the health of the plant by displaying on-demand the thousands of data points generated by the distributed control system (DCS), laboratory systems, and water quality system. The information is arranged in apps that focus on key functional areas, resulting in increased plant production and reduced downtime.
Maintenance and Materials Management
The operating plant has thousands of asset types, each with unique replacement parts and service needs. The Maintenance and Materials portal allows teams to track service history, schedule work orders, manage permitting, and verify spare part availability. This portal integrates with Condition Monitoring and Predictive Maintenance solutions to present a full understanding of the health of operating assets. Greater visibility of this data allows the maintenance team to take a proactive approach to ensuring facility uptime and focus their attention on time critical maintenance items, thus reducing maintenance time for non-critical tasks.
WHY MidrexConnect™
MidrexConnect™ is a subscription-based suite of tools that complement the skills and expertise of MIDREX® Plant operators. The tools can be configured to the specific requirements of each client, and the data of each client is isolated in per plant containers wrapped in robust security.
Midrex has assembled a dedicated team – Midrex Global Solutions (MGS) – to identify opportunities and work with the plants to create effective, sustainable solutions built upon the MidrexConnect™ platform.
MSG is focused on four key areas:
Keeping critical assets operating well
Productivity is the tons of DRI produced per hour and availability is the hours per year DRI is produced. Optimization of both is essential for plant profitability. For example, what if downtime for maintenance and remediation of water systems could be reduced by 50-75% and the effective life of reformer tubes and catalyst could be extended.
Extending the value horizon
Optimization is the primary method for keeping a plant at peak operating efficiency and plant personnel at maxi-mum effectiveness. How a plant is optimized can take many forms: minimizing process variation and human error, reducing waste, improving energy efficiency, ensuring equipment is operated properly, and upgrading the knowledge and skills of personnel. Dedicated, consistent measurement of the performance of installed equipment, systems, and staff facilitates informed decision-making.
Getting what you want when you need it
DRI is known for its low impurities content, but what about its flexibility. Adjustments can be made to vary the degree of metallization and carbon content, as well as the production rate to accommodate changes in market conditions or plant goals. Reducing the number of transfer points and the freefall distance can lessen fines generation.
Increasing awareness of lurking problems
Protecting assets and quality management go together. A plant operated and maintained by well-trained personnel will be more productive and less likely to require costly repairs. The use of guaranteed Midrex OEM parts, equipment, and materials is instrumental in keeping the plant running as designed and at the lowest cost. The use of advanced monitoring and signaling devices allows plant personnel to collect and more quickly analyze large amounts of data on which to make critical decisions that affect plant performance, product quality, safety, and environmental impact.
MAKING DATA AVAILABLE FOR ADVANCED TROUBLESHOOTING & DIAGNOSTICS
Reducing the time spent searching for data and information is critical to cost-effective plant operation and maintenance. When and how quickly plant data can be retrieved, analyzed, and acted upon can be the difference between trouble-free operation and unscheduled downtime. Remote Professional Services (RPS), powered by the MidrexConnect™ digital platform, provides plant operators a second set of eyes to identify potential upset conditions before they develop, as well as to transform problems into opportunities. RPS allows Midrex experts to review process variables and equipment settings in real time. This data is available digitally for analysis and evaluation, which leads to recommendations for preventive or corrective actions. RPS can be applied in any of the MGS areas of focus.
BUILT UPON A SOLID FOUNDATION
Midrex is committed to developing, designing, and supplying innovative technological solutions that are high-performing, flexible, and reliable. This commitment is based on a set of principles which have guided Midrex for almost 50 years:
- Innovations and improvements must be relevant to client requirements.
- Designs must be simple, reliable and in step with technology advancements.
- Technology retains its advantage and relevance through interactive information flow.
- Empowering people to take ownership of ideas and responsibility for actions produces a stronger company.
MidrexConnect™ is in lockstep with these principles, embracing the strategies of Industry 4.0 that are most relevant to the direct reduction industry and providing the tools that empower MIDREX® Plant operators.