Midrex Research & Development Technical Center – Expanding a Tradition of Innovation & Improvement
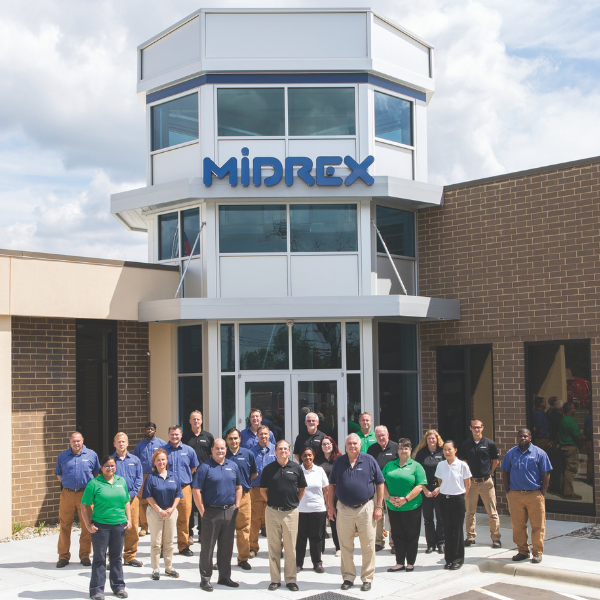
EDITOR’S NOTE:
In the 2Q 2015 issue of Direct From Midrex, we presented the various ways in which Midrex Global Solutions supports MIDREX® Direct Reduction Plants (“Lending a Helping Hand: MIDREX GLOBAL SOLUTIONS”). In this issue, we will look at the driving force behind 45 years of innovative technology and technical excellence – The Midrex Research & Development Technology Center.
Research and development (R&D) is an essential investment for a technology company such as Midrex. R&D keeps the pipeline filled with improvements to existing processes and equipment and is the catalyst for innovation that leads to new technological solutions. R&D takes an incredible amount of time, effort and resources. Midrex and its parent company, Kobe Steel Ltd. (KSL), recognize this and have consistently made R&D a priority throughout the company’s history by dedicating the proper resources to this purpose.
R&D, itself, can take several roles depending on the type and the objective (Figure 1). In academic and institutional circles, it is a means of obtaining new knowledge that may or may not have a practical use. Industrial R&D also seeks to obtain knowledge but that knowledge must be applicable to a company’s business and result in improvements to existing products and the introduction of new products that anticipate a need in the marketplace.
For Midrex, R&D is deeply engrained in company culture. It began almost 50 years ago with a handpicked group of engineers and scientists that made up the first Midrex Technical Center. Drawing on their varied technical expertise in thermal processing, gas reforming and industrial furnace design, they came up with an innovative way to produce a highly metalized iron product directly from iron ore without melting it. Their innovative idea became the MIDREX® Direct Reduction Process. Their legacy is the world’s most productive, reliable and commercially successful direct reduction technology.
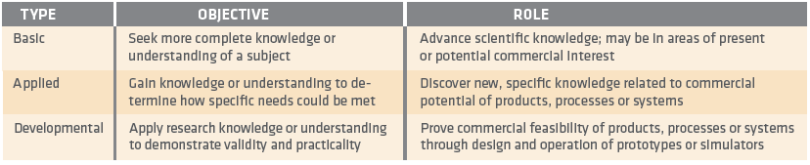
FIGURE 1.
Objectives & Roles of R&D
The original Midrex Technical Center served as the technology learning center from its early Surface Combustion days. Today, the Midrex R&D Technology Center is continuing that tradition. The Technology Center has three primary roles: to be the catalyst for innovation within Midrex, to support the business operations of Midrex and KSL, and to serve as experts in direct reduction technology. People, process and facilities/ equipment are key to fulfilling these roles.
INNOVATION & IMPROVEMENT
Midrex has built its business on a “renewable technology” concept, a self-sustaining cycle that blends science, engineering and real world experience to constantly renew and improve innovative ideas. The R&D Technology Center is the linchpin in the MIDREX® Technology Cycle.
Soon after Kobe Steel acquired Midrex in 1983, a procedure was established to regularly review MIDREX® Direct Reduction Technology in order to identify opportunities for innovation and improvement. The Technology Improvement Program (TIP) is guided by a joint KSL-Midrex steering committee, which considers performance data from existing plants and emerging market trends then assigns specific engineering and R&D tasks. A New Technology Notice (NTN) is prepared, which gives the background of the project, new design features, advantages and disadvantages, risk assessment and cost estimate.
The two essential ingredients for producing direct reduced iron (DRI) are iron ore and reducing gas. Midrex R&D labs have tested more than 7,000 iron-bearing materials since the early days in Toledo, Ohio. The state-of-the-art minerals processing lab in the current Technology Center allows Midrex to test and analyze various iron ores, as well as alternative iron-bearing and non-ferrous materials and to provide laboratory and start-up support for MIDREX® Process Licensees and potential clients. Some of the testing protocols developed over the years by Midrex have become ISO standards.
The Technology Center has been instrumental in expanding the direct reduction industry by developing alternative sources of reducing gas for the MIDREX® Process including coal gasification, coke oven gas (COG) and process synthesis gas. Pilot and demonstration-scale facilities used in commercializing and improving the natural gas-based MIDREX® Process, the coal-based FASTMET® Process and the COG-based Thermal Reactor System™ (TRS®) have been constructed and operated at the Technology Center. Data obtained from the pilot unit at the Technology Center was used to build the FASTMET® Demonstration Plant at KSL’s Kakogawa Works in Japan.
MIDREX® TECHNOLOGY CYCLE
FACILITIES AND EQUIPMENT
The R&D facility has been modified, expanded and upgraded several times since Midrex Corporation was established in Charlotte, NC, over 40 years ago, and its name has been changed to reflect its evolving role in the Midrex business model. Today it is known as the Midrex Research & Development Technology Center and is the focal point for R&D activities of Midrex and KSL including various metallic reduction technologies, advanced gas reforming methods and equipment, as well as ferrous and non-ferrous materials testing.
The Technology Center is located on six acres in Pineville, North Carolina, USA, just south of the Midrex Corporate Offices in Charlotte. Facilities include a 15,000 square foot office/laboratory building, and 21,500 square feet of bench and pilot-scale buildings with pelletizing, briquetting, and reduction capabilities. In addition, the facility houses a 9,000 square foot warehouse. All of this allows Midrex to simulate all direct reduction-related activities – from raw materials preparation to DRI melting.
The Technology Center has two fully automated and instrumented pilot facilities to simulate commercial operating conditions of MIDREX® Direct Reduction Technology. The two multi-purpose facilities are moving packed beds with recirculating gas systems capable of producing 0.25-1.0 ton of DRI per hour.
A demonstration-scale plant for the Thermal Reactor System™ (TRS®), a coke oven gas option for producing DRI in a MIDREX® Shaft Furnace jointly developed by Praxair and Midrex, has been constructed adjacent to the office/laboratory building.
A major area of expertise is bench-scale and laboratory-scale work, which includes raw materials and catalyst testing and evaluation, DRI reduction and strength testing, heat processing of ferrous and non-ferrous materials, coal reactivity and evaluation of pelletizing and briquetting techniques. Larger scale raw materials and catalyst tests under actual operating conditions can be arranged and supervised in the field by Technology Center personnel.
VISION AND PURPOSE
The reputation of Midrex is embodied in how its people develop, adapt and apply technology to solve problems and meet challenges. Having a good idea is not enough. It’s what is done with an idea that makes it memorable, sustainable and successful.
Throughout its history, Midrex has attracted highly motivated, creative people for its R&D function; people with talents ranging from mathematical modeling, metallurgy and chemistry to a variety of engineering disciplines. They have provided the vision and purpose to transform ideas into equipment, systems and processes that have become synonymous with performance, reliability and technical excellence.
Within Midrex there is a long-standing tradition of involving as many employees as possible in the R&D activities of the company. A Midrex engineer will be involved in some type of R&D work at least once during his or her career. Likewise, Technology Center scientists and technicians will spend time outside of the laboratory at MIDREX® Plant sites, mining facilities and proprietary equipment suppliers.
This is evident in the experience and perspective of members of the Technology Center management and staff.
VINCENT F. CHEVRIER, PH.D.
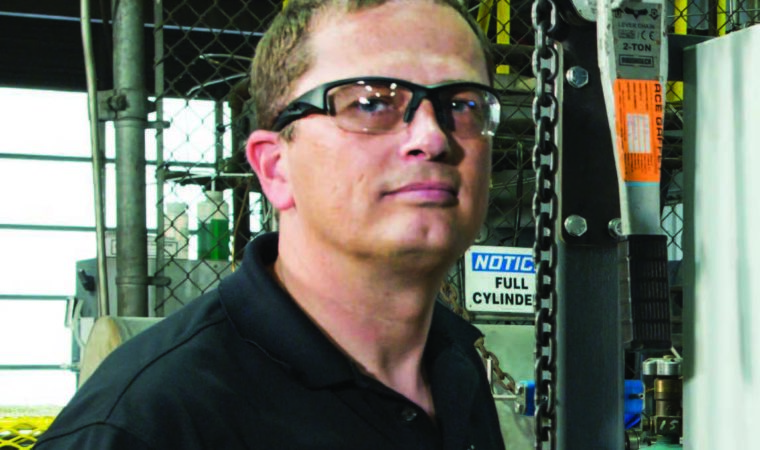
Materials Science and Engineering; Director – Research and Technology Development
Dr. Chevrier brings to the Midrex R&D function 13 years of melt shop experience with Usinor/Arcelor
(now ArcelorMittal S.A.), J&L Specialty Steel and Keywell, LLC. His first-hand experience with melt shop raw materials management, the use of alternative iron units in EAF charge blends and metal recycling provides Chevrier a unique perspective.
Chevrier takes seriously the Technology Center’s role in developing the technical expertise of Midrex. “It takes 3-5 years to develop a Midrex engineer,” according to Chevrier. “Young engineers on assignment at the R&D Technology Center gain a deeper understanding of the, “how’s and why’s”, of MIDREX® Technology by working shoulder-to-shoulder with permanent staff experts,” Chevrier said.
“R&D is in the DNA of Midrex,” Chevrier observed. “We (the Technology Center) are the catalyst for innovation and improvement, which involves the entire company.”
JAYSON RIPKE, PH.D., QP

Metallurgical and Materials Engineering Manager – Technology Center Operations
Dr. Ripke has more than 15 years of commercial and technical experience with all aspects of processing ferrous and non-ferrous materials. His first involvement with MIDREX® Technology was as a graduate engineering researcher in 1997, when he successful made pig iron nuggets in the laboratory based on the Kobe Steel ITmk3® process technology.
Ripke possesses a unique understanding of how R&D programs are structured, funded and implemented from his previous managerial and executive roles at Cliffs Natural Resources and Cardero Iron Ore Company, Ltd. “The hands-on experience of setting up multimillion dollar R&D facilities was instrumental in bringing in the renovation and expansion of the Midrex Research & Development Technology Center on budget and on schedule,” Ripke said. “Knowing what goes into creating and managing a successful R&D project contributed greatly to planning, engineering and building the state-of-the-art facility we have today.”
URVASHI SRIVASTAVA, PH.D.
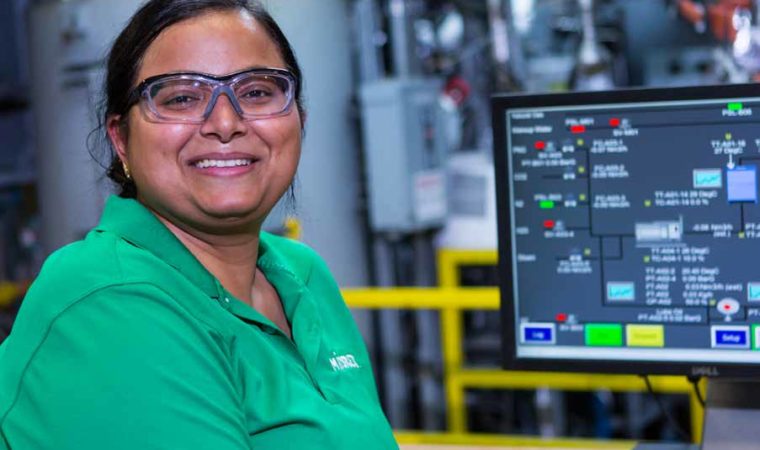
Chemical Engineering Metallurgist – Mineral Processing
Dr. Srivastava has been involved in analyzing and processing iron-bearing materials for almost 10 years. Her work has included the reduction of iron oxides with various types of sustainable and renewable reducing agents, strategies for processing low-grade iron ores and the agglomeration of fine iron ore concentrates.
Srivastava is currently the lead in a program to develop a new catalyst for the MIDREX® Reformer. She developed the iron ore pelletizing procedure and testing methods used by Midrex and set up the new minerals processing laboratory. “In order for the metallic iron market to continue growing, we must constantly broaden the range of raw materials that can effectively be processed into direct reduced iron and other highly metallized materials,” Srivastava said. “This not only involves methods and techniques for agglomeration and beneficiation but also how these materials affect the reactivity of catalyst for the MIDREX® Reformer and other operational aspects of the MIDREX® Process.”
DANIEL ZUFFEREY
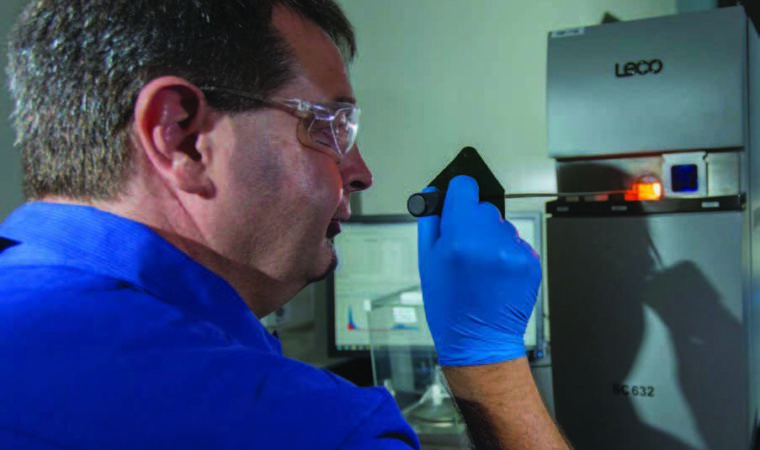
Chemical Engineering Metallurgist – Mineral Processing
Zufferey has been involved in setting up chemistry laboratories at MIDREX® Plants throughout the world and establishing laboratory operating, quality control and safety procedures. During 15 years at Midrex, in addition to his laboratory work, Zufferey has participated in teams with Midrex engineers on plant start-ups and has worked with key customers to monitor the quality of raw materials and to review laboratory data for accuracy.
Zufferey assists in the management of Technology Center operations in four main areas: customer support, project-related testing and analysis, quality control and facility capabilities development.
“Most of what occurs in a MIDREX® Plant involves chemistry,” Zufferey observed. “Being able to use my education, training and experience to help Midrex customers better understand, test and analyze the materials they use and the products they make is very gratifying.”
A TECHNOLOGY LEGACY
Before Midrex was a company, there was a Midrex Technical Center. R&D has been the centerpiece of the Midrex business model from its inception because technology must be constantly re-engineered and reinvented to remain relevant.
The Midrex R&D function has played a significant role in all of the major innovations and improvements of MIDREX® Technology (see “Major Midrex Technology Developments” on page 10). Just like the original MIDREX® Process pioneers, the management and staff of the Technology Center use their experience and expertise to transform ideas and concepts into marketable realities and helping transfer them from the laboratory to the plant site.
Midrex and KSL continue to invest in the equipment, facilities and personnel that have made the Midrex Research and Development Technology Center the preeminent R&D facility in the direct reduction industry. The Technology Center is dedicated to advancing the knowledge and understanding of the techniques, methods, materials and equipment that comprise the world’s most reliable, productive and safe direct reduction technology. In addition, the Technology Center is looking beyond direct reduction for new ways to utilize MIDREX® Technology … in the spirit of innovation.