Story
The green revolution in steelmaking: how Midrex is leading the way
February 3, 2025
Steelmakers are facing unprecedented challenges: meeting growing global demand for high-quality steel while addressing mounting pressure to reduce CO₂ emissions and combat more severe climate change.
This dual force – driven by regulation and consumer demand – is reshaping the industry. Regulations enforcing emissions reductions and growing consumer demand for sustainable materials create a powerful ‘push and pull’ effect on steelmakers. Governments are setting stricter national emissions reduction targets under the Paris Agreement, while industries such as automotive are seeking low-emission steel to meet their sustainability goals.
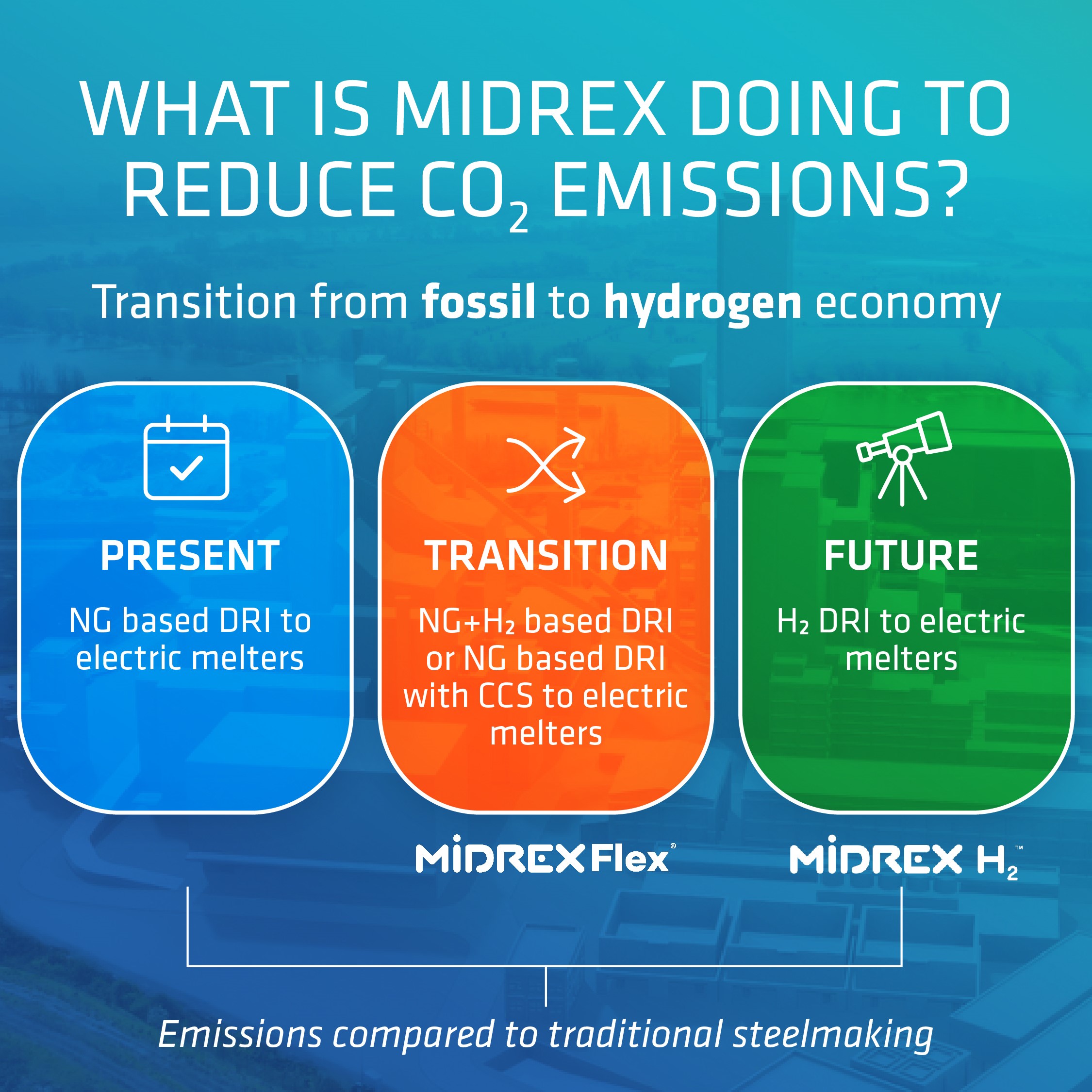
Global plantmaker and technology company Midrex provides innovative solutions that enable steelmakers to adapt to these demands while future-proofing their operations. Midrex’s technology converts iron ore into metallic iron known as Direct Reduced Iron (DRI) by using high-temperature reducing gases to strip oxygen from the iron oxide. DRI is a high-quality feedstock primarily used in Electric Arc Furnaces (EAFs) to produce steel but can also be utilized in Blast Furnaces (BFs) in specific applications.
DRI can enable steelmakers to reduce their CO₂ emissions by varying degrees, depending on the type of energy and feedstock gases they use.
A natural gas-based MIDREX Direct Reduction Process paired with an electric arc furnace (EAF) has the lowest CO₂ emissions of any current commercially proven steelmaking process. However, there is scope to reduce emissions further by using hydrogen (H₂) as a fuel and chemical reactant.
Midrex offers two types of technology that enable the production of high-quality DRI while cutting CO₂ emissions compared with traditional forms of steelmaking.
MIDREX Flex
The use of green hydrogen – hydrogen made using clean, renewable energy – is the ideal way to decarbonize the steelmaking industry. However, the availability of hydrogen and its high cost make it unsuitable for all steelmaking plants today.
Until hydrogen is abundant and cheap, the industry needs flexible plants that can produce steelmaking feedstocks using various fuels and reducing gases. And since energy availability changes as markets evolve, it can be an advantage for steel companies to have flexibility built into their production facilities.
MIDREX Flex does just that. It future-proofs the steelmaking process. The technology allows steelmakers to adapt to the hydrogen economy at their own pace. Natural gas can be used immediately in a MIDREX Flex plant. As sufficient quantities of hydrogen become available at competitive prices, the plant can easily be modified to operate with higher percentages of hydrogen, including a 100% replacement of natural gas.
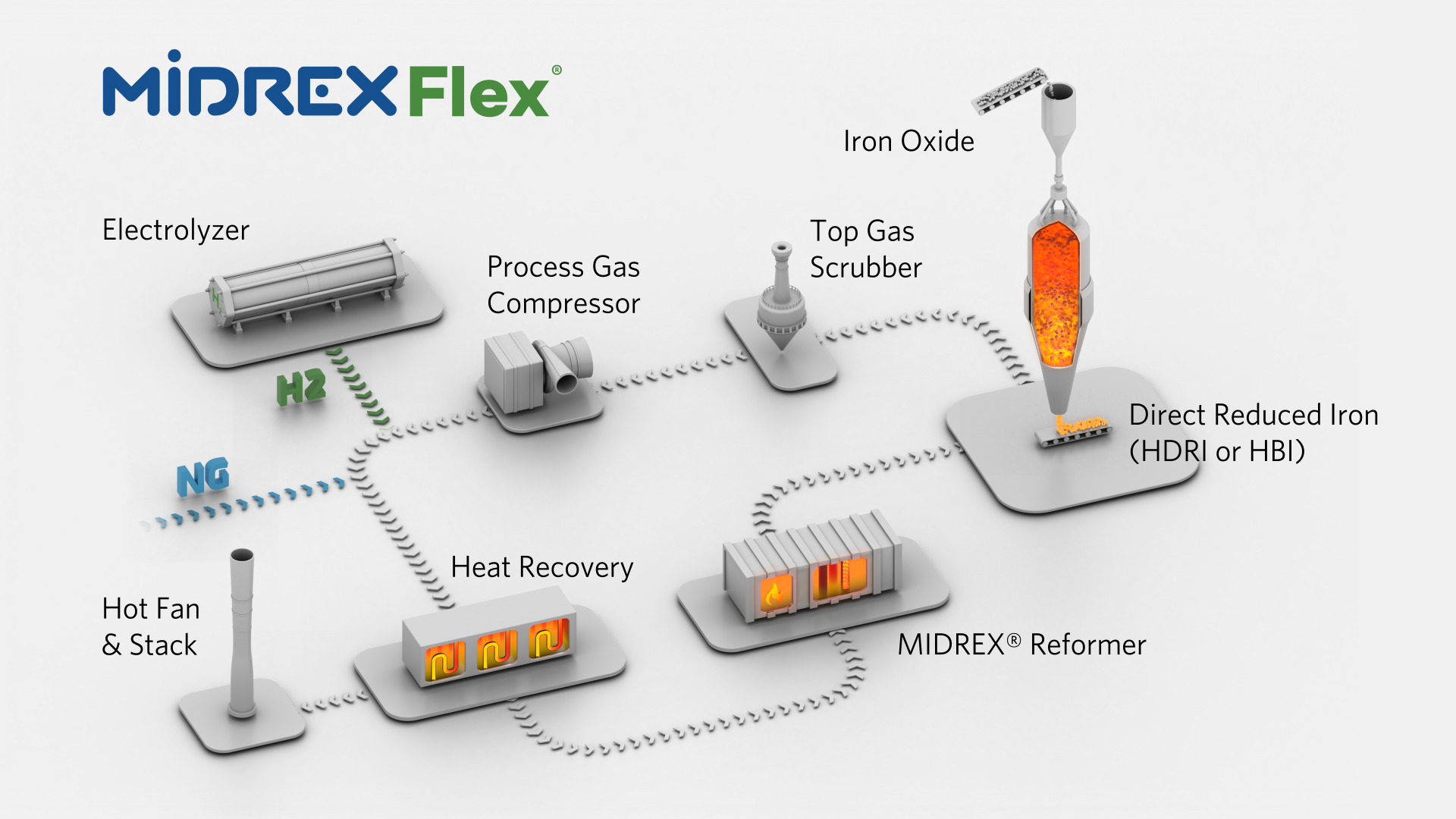
MIDREX H2
The best way to reduce CO₂ emissions from steelmaking is using pure hydrogen as an energy source and reductant for DRI production in a shaft furnace. This is the basis of MIDREX H2 technology.
Hydrogen can replace hydrocarbons such as coal, oil, and natural gas, thereby reducing emissions of CO₂ and other pollutants, such as particulate matter, at the point of combustion. However, hydrogen can be made through various routes, all of which affect the proportion of CO₂ emissions released.
In the MIDREX H₂ process, pure hydrogen is preheated using an electric heater before entering the shaft furnace. This eliminates the need for a traditional reformer and ensures that the reduction reaction occurs efficiently while maintaining near-zero CO₂ emissions. By leveraging green hydrogen, MIDREX H₂ offers steelmakers the ability to drastically cut emissions and produce DRI with unparalleled sustainability.
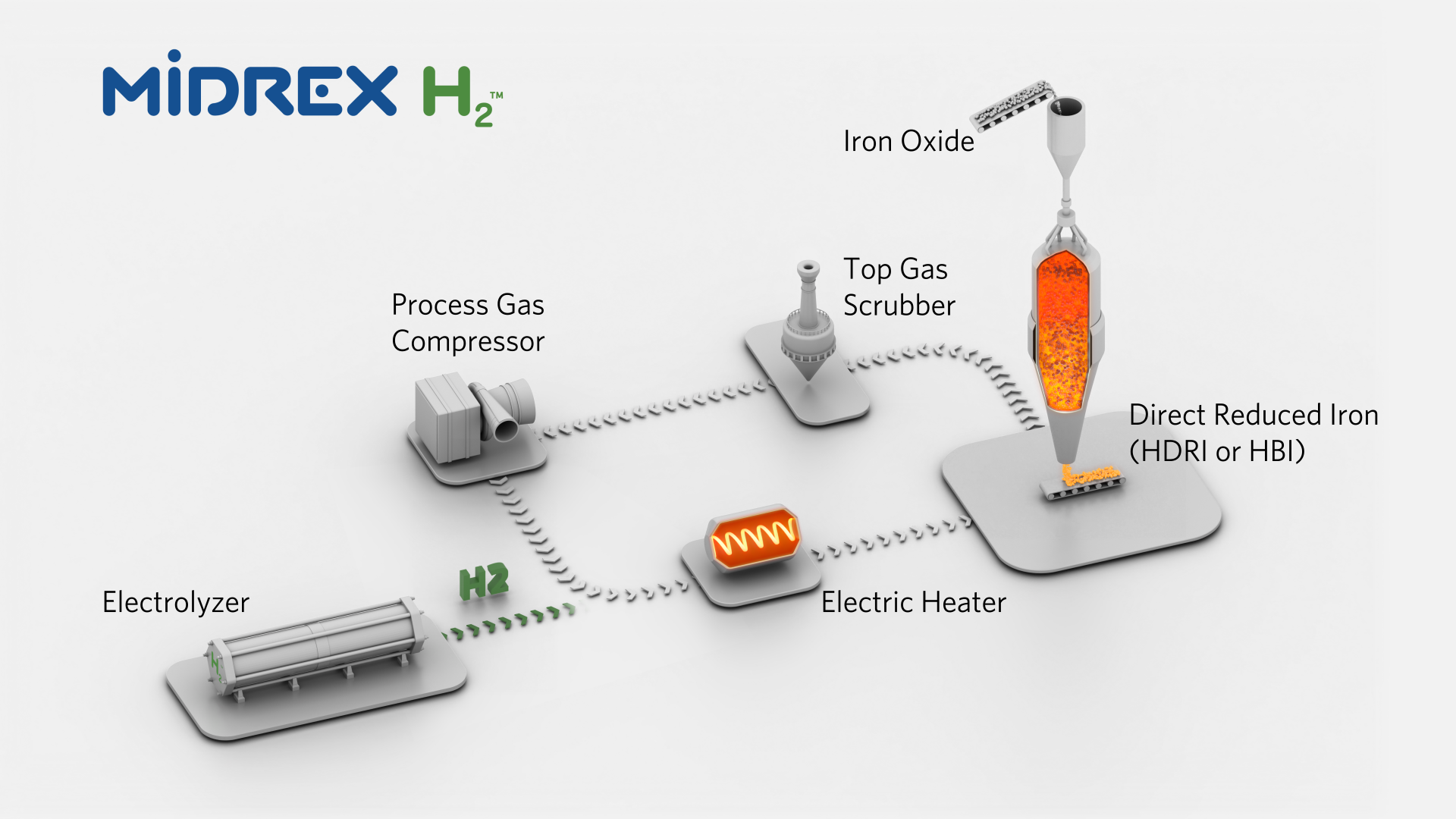
A leading position in DRI
Midrex is a leader in the global development of DRI for steelmaking. MIDREX Plants produce approximately 80% of the world’s low-CO₂ DRI.
To recap, Midrex technology offers steelmakers a proven pathway to decarbonization with these advantages:
- Quality: Produces high-quality DRI for steel production
- Reliability: Proven operational success in plants worldwide
- Flexibility: Can adapt to various energy sources, from natural gas to hydrogen, enabling a smooth transition to low-emissions steelmaking
- Efficiency: Maximises resource use by reusing energy and reducing waste
- Sustainability: It cuts CO₂ emissions to around one-third of those produced in a traditional blast furnace/basic oxygen furnace (BF/BOF) steelmaking route
With these significant advantages, Midrex offers steelmakers a proven route through the increasingly stringent environmental regulatory landscape. It allows companies to adapt to the varying availability of energy types and feedstock gases such as natural gas and hydrogen. Midrex technology will enable steelmakers to evolve at their own pace while preparing their business for a sustainable future.
Sources:
MIDREX Flex – Midrex Technologies, Inc.
Ultra-Low CO2 Ironmaking: Transitioning to the Hydrogen Economy – Midrex Technologies, Inc.