MIDREX H2: Ultimate Low CO2 Ironmaking and its place in the new Hydrogen Economy
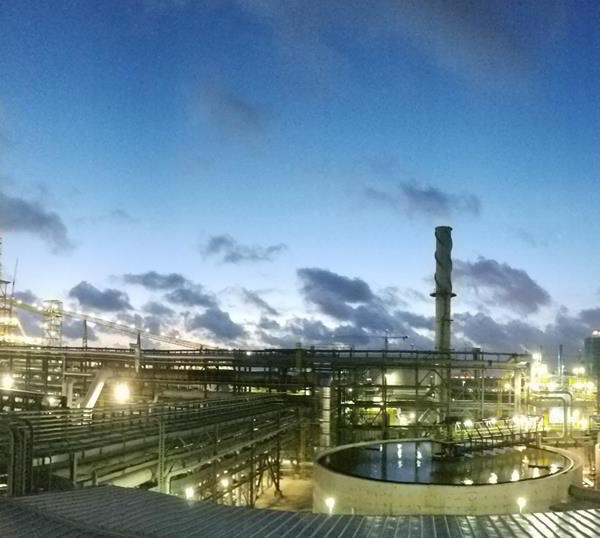
EDITOR'S NOTE: This article is based “Future of Direct Reduction in Europe – Medium and Long-Term Perspectives,” co-authored by Primetals and Midrex and presented at the ESTAD Conference in June 2017.
INTRODUCTION – THE VALUE OF DRI
Over the past few decades there has been increasing interest and work to explore and mitigate CO2 emissions in the iron and steel industry. The natural gas-based MIDREX® Direct Reduction Process paired with an electric arc furnace (EAF) has the lowest CO2 emissions of any commercially proven steelmaking route; yet, there is even more room for lower emissions through use of hydrogen as a fuel and chemical reactant. The best possibility for drastically reducing the steel industry’s CO2 footprint is the use of pure hydrogen as the energy source and reductant for direct reduced iron (DRI) production in a MIDREX® Shaft Furnace. This concept, known as MIDREX H2™, holds great promise to be developed and realized in either new or existing DRI Plants. A major obstacle to implementing hydrogen direct reduction ironmaking in the difficulty of producing pure hydrogen without a large CO2 footprint. Still, this idea may be closer than many realize as the idea of the “Hydrogen Economy” evolves. This article will look at the new Hydrogen Economy and how it will influence next-generation iron and steelmaking, specifically by examining the MIDREX H2™ concept of using the proven MIDREX® Process with an H2 energy source.
MOVING FROM A HYDROCARBON ECONOMY TO A HYDROGEN ECONOMY
Most energy today comes from one of three hydrocarbon sources: petroleum, coal or natural gas. This is called the Hydrocarbon Economy when talking about energy and its relationship to global markets. The Hydrogen Economy is a proposed system of delivering energy using hydrogen. It has been put forth as a way to solve some of the negative effects of using hydrocarbon fuels, which release carbon to the atmosphere as carbon dioxide, carbon monoxide, unburnt hydrocarbons, and so on.
Proponents of a world-scale Hydrogen Economy argue that hydrogen can be an environmentally cleaner source of energy to end-users without the release of pollutants, such as particulate matter or carbon dioxide at the point of end use. However, there are many issues to overcome for hydrogen to become a major economic factor. For instance, hydrogen has a high energy density by weight, but a low energy density by volume when not compressed or liquefied, thus the high cost of a hydrogen fuel cell has been a major obstacle in its development. Other related issues, such as storage, distribution infrastructure and hydrogen purity and concerns for safety will have to be overcome for the Hydrogen Economy to take off.
Also, there is the classic “chicken and egg” syndrome. Potential producers are eagerly awaiting consumers to come forward so they can demonstrate the use of hydrogen at scale, while consumers appear ready once sufficient amounts of hydrogen can be produced at a competitive cost. Full realization of the Hydrogen Economy will require the cooperation of industry, academia, government and the consumer.
Getting to Know Hydrogen
There are two major uses for hydrogen today. About half is used to produce ammonia (NH3) for use in fertilizer. The other half is used to convert heavy petroleum sources into lighter fractions suitable for use as fuels, which is known as hydrocracking. Because this can effectively enhance poorer source materials, such as tar sands and oil shale, hydrocracking is seen as a growth area.
In 2016, 96% of global hydrogen production was from fossil fuels: 48% from natural gas, 30% from oil and 18% from coal; water electrolysis accounted for 4%. Linking the centralized production of hydrogen to a fleet of light-duty fuel cell vehicles would require the siting and construction of a costly distribution infrastructure. Further, the technological challenge of providing safe, energy-dense storage of hydrogen on board the vehicle must be overcome to provide sufficient range between fill-ups. Therefore, of the four methods for obtaining hydrogen, partial combustion of natural gas in a natural gas combined cycle (NGCC) power plant appears to offer the most efficient chemical pathway and the greatest off-take of usable heat energy.
Most hydrogen is produced in a steam methane reformer (SMR) using natural gas as the feedstock. This is similar technology to a MIDREX® Reformer. The reformer produces a gas containing H2 and CO, then the CO is removed. While large-scale hydrogen production utilizing steam re-formers is a reality today, it does not provide a solution for greatly reducing CO2 emissions because it is made from natural gas; therefore, an SMR has significant CO2 emissions.
Another technology for H2 production is electrolysis, which uses electricity to split water into hydrogen and oxygen. This is done today, but there are two problems for its use in the Hydrogen Economy: 1) in most countries, electricity is generated primarily with fossil fuels so there remains a large CO2 footprint, and 2) the cost of hydrogen is too high for many applications at prevailing electricity prices (about twice the cost of hydrogen from steam reforming). There are 1.0 MW electrolyzers available today, but the total world installed capacity is only about 50 MW.
In 2016, the US Department of Energy (DOE) identified “H2@Scale” as an underemphasized major opportunity, which they term a “Big Idea.” DOE is focusing on it in a combined effort with 14 of their 17 national labs. Rather than generating H2 by electrolysis using electricity produced during times of peak demand, DOE envisions the use of lower cost off-peak power, storing the H2 produced, then transporting it to users when required. Figure 1 shows its vision of the economics. Using $0.01/kWh electricity, the cost of hydrogen is about the same as from a steam reformer (see second bar from left in Figure 1). Further R&D advances could result in an even lower cost for electrolytic hydrogen. The volumes that could be produced at this cost leads us to the very real possibility of using H2 for the purpose of iron and steelmaking.
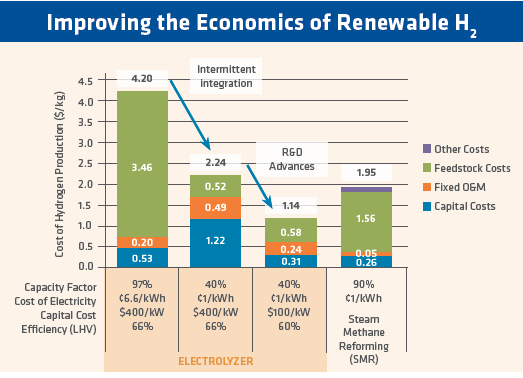
FIGURE 1.
Improving the Economics of Renewable H2; Department of Energy H2 @ Scale FCTO Webinar - July 28, 2016
Using Hydrogen for Ironmaking
There is tremendous interest and work underway worldwide to reduce CO2 emissions. A very promising solution is use of hydrogen as a fuel and chemical reactant rather than fossil fuels.
The steel industry accounts for as much as 5% of total world greenhouse gas emissions because of its significant use of coal. About 75% of the world’s steel is made using blast furnace (BF) iron processed in a basic oxygen furnace (BOF). The BF uses coke (refined coal) as the energy source and reductant. This process route generates about two tons of CO2 for every ton of steel produced.
The natural gas-based MIDREX® Direct Reduction (DR) Process, paired with an electric arc furnace (EAF), has the lowest CO2 emissions of any commercially proven steelmaking route. This occurs because natural gas contains much more hydrogen than does coal. The process gas of a typical MIDREX® Plant contains about 55% hydrogen and 36% carbon monoxide (CO), whereas BF gas is nearly all CO. As a result, the MIDREX/EAF combination produces about half the CO2 emissions per ton of steel as a BF/BOF. By adding CO2 scrubbers, Midrex can lower CO2 emissions even more by removing CO2 in the flue gas. If the CO2 can be used and/or sequestered, emissions are reduced by half again versus the BF/BOF.
Despite the benefits of natural gas-based DR/EAF steelmaking, there is interest in an even lower emissions process route to dramatically reduce the steel industry’s CO2 footprint. Major initiatives underway worldwide to use hydrogen to make iron are described in the Appendix to this article. This is not a new concept. Cleveland-Cliffs, Lurgi and LTV Steel built a 400,000 ton/year Circored direct reduction plant in Trinidad that used hydrogen from a steam reformer as its reductant and energy source. The plant was started up in 1999, but the fluidized bed reactor had numerous problems and it produced only about 150,000 tons by the time it was shut down in 2001.
The ultimate low CO2 ironmaking solution would be to produce pure hydrogen using a low carbon energy source such as solar, wind, hydro, or nuclear, and use the hydrogen in a shaft furnace to make DRI. Midrex is now developing MIDREX H2™ to do just that.
An Iron Reduction Primer
Before going into the details of ironmaking with hydrogen, let’s review some basics. Pyrometallurgical (high temperature) ironmaking uses CO and H2 to accomplish reduction, which is the removal of oxygen from ore (opposite of oxidation). There are many reactions occurring in a direct reduction reactor or a blast furnace, but the primary ones are shown in Figure 2. Iron is represented by Fe and methane (primary component of natural gas) is represented by CH4.
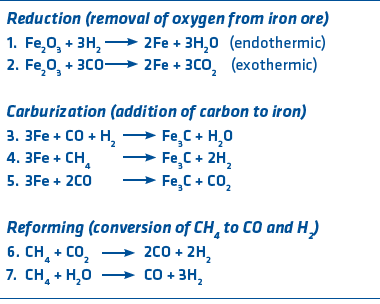
FIGURE 2.
Ironmaking Reactions
In a blast furnace, almost all reduction is done using CO (reaction 2), which is generated from coke. In direct reduction, reduction is accomplished with CO and H2. In the case of the standard MIDREX® Process using natural gas, 60% (ratio of H2 to CO) of that is done with hydrogen. Since reduction occurs in a BF at about 1300°C and in a DR furnace at about 900°C, temperature control is a very important consideration. Reaction 1 is endothermic (requires heat) while reaction 2 is exothermic (gives off heat). The MIDREX® Process, using the typical gas content of 55 percent H2 and 36 percent CO is easy to control because the temperature in the furnace stays relatively constant.
The carburization reactions occur automatically in the BF because of all the carbon present; in a direct reduction process, they occur if the reducing gas contains CH4 and CO. The re-forming reactions occur when methane is present either in a BF or a DR furnace. Many BFs now inject methane (natural gas) into the furnace to reduce coke consumption.
Hydrogen Use in MIDREX® Plants
As noted in the paper, “Future of Direct Reduction in Europe – Medium and Long-Term Perspectives,” co-authored by Midrex and Primetals and presented at the ESTAD Conference in June 2017, hydrogen can be used in two ways in a DR plant. Some H2 can be introduced in a natural gas-based plant as a substitute for part of the natural gas or the DR plant can be based on 100% H2. In the case of H2 addition to a MIDREX® Plant, one-third of the required natural gas can be substituted. For example, 60,000 Nm³/h of H2 can be substituted for approximately 20,000 Nm³/h of natural gas in a 2.0 Mtpy plant, which represents approximately 30% of the total natural gas consumption. The flowsheet for this approach is shown in Figure 3. This can be done with an existing or new plant.
MIDREX H2 refers to the use of 100% hydrogen as the feed gas. Midrex has vast experience using hydrogen to make iron in a shaft furnace. Since 1969, MIDREX® Plants have produced more than 955 million tons of DRI made with over 50% hydrogen. MIDREX® Plants utilize three different ratios of H2 and CO. Most use natural gas and a standard MIDREX® Reformer that produces a reducing gas with 55% H2 and 36% CO (H2/CO of 1.5). The FMO MIDREX® Plant in Venezuela uses a steam reformer, and H2/CO has varied from 3.3 to 3.8. There are six MIDREX® Modules that utilize gas made from coal, and these have hydrogen to CO ratios from 0.37 to 0.56. Thus, the MIDREX® Process has successfully produced DRI at H2/CO ratios from 0.37 to 3.8.
Based on initial modeling and laboratory experiments, it is possible to use almost pure hydrogen to make DRI in a MIDREX® Shaft Furnace. The flowsheet is shown in Figure 4. It is similar to the standard MIDREX® Process except that the H2 input gas is generated external to the process. Thus, there is no reformer and a gas heater is employed to heat the gas to the required temperature. In practice, the reducing gas H2 content is about 90 %, with the balance CO, CO2, H2O and CH4. These constituents result from addition of natural gas for temperature control and carbon addition, as described in the following section.
Because H2 is converted to H2O and condensed in the top gas scrubber, no CO2 removal system is necessary. Hydrogen consumption is approximately 550 Nm³/t DRI. Additionally, up to 250 Nm³/t DRI of H2 or other environmental friendly heat sources such as waste heat, electricity, and/or natural gas is required as fuel for the reduction gas heater. With this process, CO2 emissions could be reduced up to 80% vs. the BF/BOF steelmaking route.
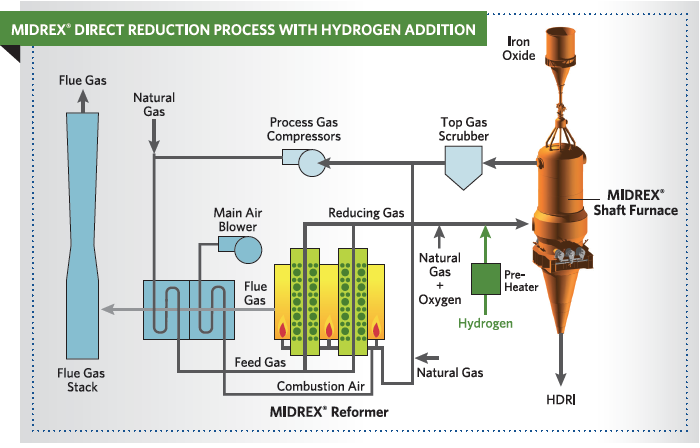
FIGURE 3.
MIDREX Process with Hydrogen Addition
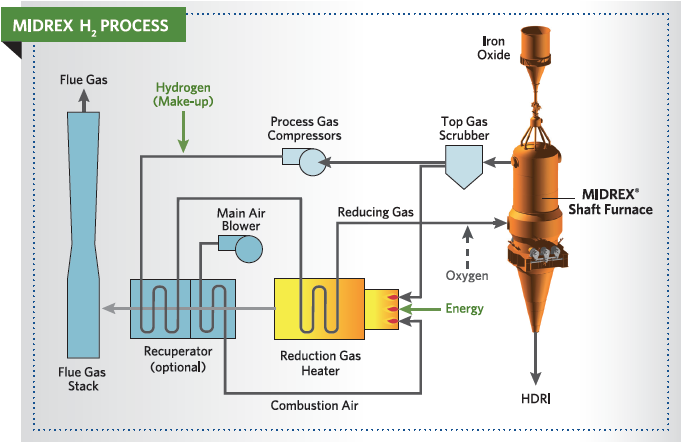
FIGURE 4.
MIDREX H2™ Process
There are a number of considerations for the MIDREX H2™ Process, first of which is temperature. With so much hydrogen, the DRI cools off as the reducing gas enters the shaft furnace because of ironmaking reaction 1 (see Figure 2). Thus, it is necessary to add natural gas to maintain the desired reduction temperature. According to Midrex modeling, the addition of natural gas at a rate of 50 Nm3/t DRI should accomplish this.
The second issue is DRI carbon content. The vast majority of DRI is used in EAFs. EAF steelmaking practice today generally employs carbon added either in metallic charge materials such as DRI, HBI and pig iron or as pure carbon. Burning this carbon with injected oxygen creates significant heat which reduces electricity consumption and enables faster melting. Since pig iron is made from BF hot metal that is saturated with carbon, it contains 4-4.5 percent carbon. DRI can have 1-4.5 percent carbon depending on the process, reducing gas used and the way the DR plant is operated. Most EAF steelmakers prefer to use DRI with 1.5-3 percent carbon, but the optimum carbon level varies based on metallic charge mix and the steel grade produced.
With high amounts of hydrogen in the reducing gas, it will be necessary to add hydrocarbons at some place in the process to achieve the desired carbon level. DRI carburizing options include addition of hydrocarbon to the cooling zone or in the furnace lower cone. Addition of 50 Nm3/t of natural gas for temperature control results in DRI carbon of about 1.4 percent. The next evolution in steelmaking will be to melt iron without using carbon, but this will be very energy intensive since the melting point of steel increases as carbon content decreases.
CONCLUSION
Today, the best possibility for drastically reducing the steel industry’s CO2 footprint is the use of pure hydrogen as the energy source and reductant for iron ore. There are many efforts underway worldwide to achieve this goal. The use of hydrogen in a MIDREX® Shaft Furnace, known as the MIDREX H2™, holds great promise to be developed and realized in either new or existing DRI Plants. The main obstacle to implementing hydgrogen direct reduction ironmaking is in the difficulty of producing pure hydrogen without a large CO2 footprint. Despite this hurdle, governments and industry are looking at ways to make a Hydrogen Economy a reality in the near future and with it a cleaner way to make iron and steel.
APPENDIX:
HYDROGEN IRONMAKING RESEARCH PROGRAMS
USA
American Iron & Steel Institute (AISI) – CO2 Breakthrough Program
AISI has been working with leading universities and the Department of Energy on projects aimed at developing revolutionary new ways of making steel while emitting little or no CO2 through research called the CO2 Breakthrough Program. Two potential “breakthrough technologies” are currently being tested. The first is Molten Oxide Electrolysis, a program conducted at the Massachusetts Institute of Technology (MIT) that seeks to produce iron by molten oxide electrolysis, which generates near-zero CO2 emissions. The second program involves “Flash Smelting” technology, which is adapted from mining processes and includes advances in furnace technology utilizing hydrogen. This work is being done at the University of Utah.
US Department of Energy
H2@Scale is a concept that describes the potential of wide-scale renewable hydrogen production to dramatically reduce U.S. greenhouse gas emissions. The DOE will facilitate the development of the Hydrogen Economy by supporting research and engaging stakeholders such as utilities and regulators, industrial gas suppliers, major oil companies, metals and ammonia producers and the investment community. Research areas include low and high temperature H2 production, storage and distribution and end use.
EUROPE
Salzgitter
Salzgitter has formed a project named “GrInHy“ (Green Industrial Hydrogen) via reversible high-temperature electrolysis together with various international partners including Salzgitter Mannesmann Forschung. The project’s core will be a high-performance high-temperature electrolyser (HTE) at the Salzgitter Flachstahl strip mill. The unit will be able to convert steam into hydrogen, as well as oxygen by means of electrolysis and produce power by means of fuel cells. Its start of operation is planned for summer 2017. The hydrogen produced by the HTE could partially substitute for carbon as a reduction agent in the blast furnace or be used in annealing processes.
SSAB/LKAB/Vattenfall (Sweden)
Swedish steelmaker SSAB, iron ore producer LKAB and power company Vattenfall have launched a joint initiative called Hybrit to develop carbon dioxide-free steelmaking and have received SEK 6.7 million from the Swedish Energy Agency. The project, called Hybrit (hydrogen breakthrough ironmaking technology), is performing a pre-feasibility study. If successful, this will be followed by a full feasibility study with trial operation of a pilot plant during the period 2018-24. The project calls for this to be followed by construction of a demonstration plant to undertake trials in 2025-2035.
voestalpine Stahl
voestalpine Stahl is working to gradually decarbonize steel production. The company built the world’s first direct reduction plant for largely environmental reasons. The facility, a MIDREX® Plant near Corpus Christi, Texas, is producing HBI for use in their blast furnaces in Austria. This will enable voestalpine to better manage its CO2 footprint. In addition, voestalpine is also building a pilot facility at its site in Linz, Austria, which will use electrolysis to produce hydrogen to reduce iron. Siemens is providing a proton exchange membrane electrolyzer for H2 generation, and the Austrian utility Verbund will provide hydro and solar electricity. Hydrogen generated at the test facility will be fed directly into voestalpine’s gas network for testing in various process stages of steel production. Two-thirds of the project’s funding will come from the EU, and the pilot will run for 4½ years. Voestalpine CEO Wolfgang Eder has said, “Our researchers and technicians are optimistic that hydrogen-based steel production will be feasible in the 2030s.”
ASIA
Posco
In 2009, Posco announced plans to eventually halt carbon emissions by switching to a hydrogen-based steelmaking process from 2021.