Ultra-Low CO2 Ironmaking: Transitioning to the Hydrogen Economy
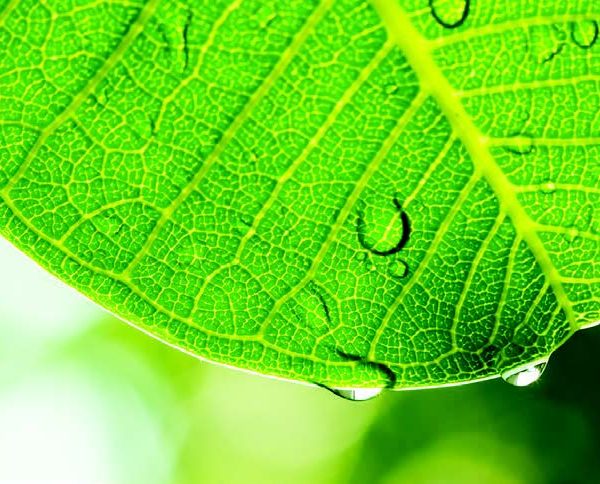
INTRODUCTION
Mitigating carbon dioxide (CO2) emissions in the iron and steel industry will become even more critical in Western Europe as the cost of CO2 emissions increases over time. While the MIDREX® Process using natural gas, paired with an electric arc furnace (EAF) has the lowest CO2 emissions of any steelmaking route using iron ore, there is room to further decrease emissions using hydrogen as a fuel and chemical reactant in the direct reduction process. The best possibility for significantly reducing the CO2 footprint now and in the future is to use green hydrogen to produce DRI/HBI, which then can be used as feed-stock for steelmaking. This concept is known as MIDREX H2™.
Unfortunately, hydrogen is not currently available at sufficient scale and low enough cost for rapid adoption. This article discusses the status of the transition from a Carbon Economy to a Hydrogen Economy, its challenges, and various ongoing activities. As green hydrogen becomes available and cost effective, the MIDREX Process can be converted to MIDREX H2 in stages allowing steelmakers to take advantage of CO2 reduction immediately and further reduce emissions in the future without major capital expenditure.
MOVING TOWARD A HYDROGEN ECONOMY
The Hydrogen Economy is a proposed system of delivering energy using hydrogen. It has been put forth to solve some of the negative effects of using hydrocarbon fuels, which release carbon to the atmosphere as CO2, CO, unburnt hydrocarbons, etc. Proponents of a world-scale Hydrogen Economy argue that hydrogen can be an environmentally cleaner source of energy to end-users without the release of pollutants, such as particulate matter or carbon dioxide at the point of end use. The only emission from using hydrogen as fuel or in fuel cells is water.
The Paris Agreement opened for signature on Earth Day 2016 and entered into force on 4 November 2016. The goal of this agreement is to increase the global response to the “threat of climate change by keeping a global temperature rise this century well below 2 degrees Celsius above pre-industrial levels” [1]. CO2 reduction from the industrial sector is widely recognized as a key to achieving these targets. The steel industry, especially traditional ironmaking, is among the largest contributors of greenhouse gases emissions – in the range of 7-9% of total emissions – because of its significant reliance on coal.
About 75% of the world’s iron is made using blast furnaces (BF), which is refined in a basic oxygen furnace (BOF). The BF uses coke (refined coal) as the energy source and as the reductant to make iron with ~4.5% carbon, which is burned in the BOF to produce energy. As a result, BF/BOF emissions can be 1.6-2.0 kg CO2/kg steel depending on the technologies used. The MIDREX NG™ Process paired with an EAF has the lowest CO2 emissions of any commercially proven steelmaking route using virgin iron ore at 1.1 – 1.2 kg CO2/kg steel. By adding a CO2 removal system, the MIDREX Process can lower CO2 emissions even further to around 1/3 of the emissions from the BF/BOF route.
Yet, there is even more room for lower emissions through use of hydrogen as a fuel and chemical reactant in the MIDREX Process. The ultimate method for drastically reducing the steel industry’s CO2 footprint is the use of green hydrogen (produced from renewable energy) for DRI production in a MIDREX Shaft Furnace. This concept, known as MIDREX H2, holds great promise in either new or existing MIDREX Plants. A major obstacle to implementing hydrogen direct reduction ironmaking is the difficulty of producing enough hydrogen at a low enough cost without a large CO2 footprint, as it is done currently in steam-methane reformers. Still, this idea may be closer than many realize as the idea of the Hydrogen Economy gains traction and support.
ISSUES TO OVERCOME
Besides nuclear power, most energy today comes from one of three hydrocarbon sources: petroleum, coal, and natural gas. Renewable energy, such as wind, solar or hydro power have steadily increased market share, but their penetration is often limited by geography and the ability of the grid to accommodate the fluctuating generation (also known as the ‘duck curve’) associated with them. Electrical power is also expensive to store and distribute due to high yield losses in the transmission lines. In the case of hydrogen, there are specific issues to overcome for it to become a major economic factor. For instance, hydrogen has a high energy density by weight, but a low energy density by volume when not compressed or liquefied. Thus, the prohibitive cost of a hydrogen fuel cell has been a major obstacle in its development. Other related issues, such as storage, distribution infrastructure and sufficient hydrogen purity, and concerns for safety will have to be overcome for the Hydrogen Economy to take off.
Also, there is the perceived “chicken and egg” syndrome, where potential producers are eagerly awaiting consumers to come forward so they can generate hydrogen at scale (and lower cost from economy of scale), while consumers claim they will be ready once sufficient amounts of hydrogen can be produced at a competitive cost. Cooperation between industry, academia, government, and the end consumers is needed to address these challenges. Many countries already have such initiatives in place and are collaborating to expedite full realization of the Hydrogen Economy.
CURRENT HYDROGEN USAGE AND GENERATION
There are two major uses for hydrogen today. About half is used to produce ammonia (NH3) for use in fertilizer. The other half is used to convert heavy petroleum sources into lighter fractions suitable for use as fuels, which is known as hydrocracking. Hydrocracking can effectively enhance poorer source materials, such as tar sands and oil shale. In 2016, 96% of the global hydrogen production was from fossil fuels; 48% from natural gas, 30% from oil, and 18% from coal. Most of this ‘blue’ hydrogen is generated and consumed on the same site; it is not traded or transported. The vast majority of this hydrogen is produced in a steam methane reformer (SMR) using natural gas as the feed-stock. The reformer produces a gas containing H2 and CO, then the CO is removed.
While large-scale hydrogen production utilizing steam reformers is a reality today, it does not provide a solution for greatly reducing CO2 emissions because it is made from natural gas and still has significant CO2 emissions. Capture from SMR is feasible, but the CO2 needs to be sequestered, as generation of CO2 far exceeds consumption. Gas-based direct reduction of iron ore falls into that category, whether from the MIDREX Process or from HYL/Energiron. Both technologies generate H2 on-site via a reformer and the hydrogen is used for direct reduction in the adjacent shaft furnace.
“GREEN” HYDROGEN
Another technology for H2 production is electrolysis, which uses electricity to split water into hydrogen and oxygen. Water electrolysis accounts for 4% of the global hydrogen production. Since the hydrogen molecules come from water and not hydrocarbons, it may be considered “green.” However, there are two problems for its use in the Hydrogen Economy: 1) in most countries, electricity is generated primarily with fossil fuels so there remains a large overall CO2 footprint, and 2) the cost of hydrogen is too high for many applications at prevailing electricity prices (about twice the cost of hydrogen from steam reforming).
In 2016, the US Department of Energy (DOE) introduced the H2@Scale initiative to “advance affordable hydrogen production, transport, storage, and utilization to increase revenue opportunities in multiple energy sectors.” [2] The DOE consortium includes universities, national labs, and industry and focuses on R&D projects and providing funding opportunities. The overall approach is not solely to produce hydrogen from renewable energy sources, such as solar and wind, but rather to use hydrogen as a response to fluctuating power generation vs. demand and to increase utilization of all sources of power including coal, natural gas, nuclear, and renewables. For example, hydrogen can be produced and stored during times of excess power generation (e.g. when the sun is shining or the wind is blowing), then converted back to power for times of high power demand. Hydrogen can also be transported to industrial users, such as a steel producer. This scheme is more realistic than generating hydrogen solely from renewable energy sources.
There are many growth areas for green hydrogen and transportation is leading the way. Use of hydrogen in commercial vehicles, such as buses, drayage trucks or forklifts is rapidly increasing. Hydrogen-fueled cars are being demonstrated in select locations like California. However, linking the centralized production of hydrogen to a fleet of light-duty fuel cell vehicles would require the construction of a costly distribution infrastructure for further expansion. Further, the technological challenge of providing safe, energy-dense storage of hydrogen both at distribution stations and on board the vehicle must be overcome to provide sufficient range between fill-ups.
Industrial use of hydrogen, such as for producing iron, offers the advantage of a fixed location and large demand. Hydrogen can be generated on-site or supplied over-the-fence with significant lower infrastructure cost per volume of gas. Steel mills also have the ability to integrate hydrogen generation with other utilities available on site, such as steam and other gases.
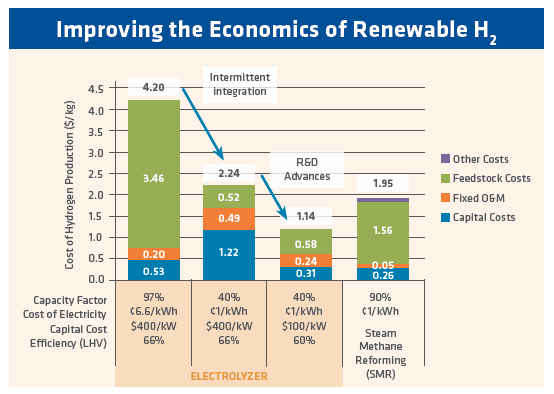
FIGURE 1. Improving the Economics of Renewable H2 (Department of Energy H2 @ Scale FCTO Webinar – July 28, 2016)
Between the challenges of transportation, storage, and use of hydrogen, at-scale hydrogen generation is of prime interest for industrial users. There are several technologies at various levels of technical readiness to produce hydrogen from water. The most mature is the alkaline electrolyzer. However, proton exchange membrane (PEM) is in the commercialization stage and solid oxide electrolysis cell (SOEC) is in demonstration stage. The cost of hydrogen from these technologies currently is not competitive to SMR, by at least a factor of 2x. Figure 1 shows the vision of the economics: using $0.01/kWh electricity, the cost of hydrogen is about the same as from a steam reformer (see second bar from left in Figure 1). Further manufacturing and R&D advances could result in an even lower capital cost for electrolytic hydrogen.
Undoubtedly, increased production will reduce the capital cost of these electrolyzers. The total world installed capacity is growing rapidly: in 2017, DOE estimated the global electrolyzers sales to be 100MW. There are electrolyzers commercially available today in the range of 1MW, but large capacity electrolyzers are becoming reality – for example voestalpine is commissioning a 6MW PEM in Austria, and AirLiquide announced in February 2019 the construction of a 20MW PEM in Canada. In 2018, Nel (Oslo, Norway) contracted 1GW of capacity between Nikola Motor company and the largest alkaline electrolyzer plant (360MW) in Norway. The current technologies generate ~200Nm3/h of H2 per MW, although the figures vary based on the technology, so the volumes that can now be produced lead us to the very real possibility of using H2 for iron and steelmaking. While increasing plant size will decrease production cost, scaling up the electrolyzer does not lead to significant economies of scale like most industrial equipment. Scaling up is accomplished by multiplying cells and stacks, not by increasing their volume. Reduction in capital costs must come from efficiencies in manufacturing and raw material selection. On the other hand, this linear scale up involves significantly less technical risks. The other aspect of cost reduction is the cost of electricity, which is the majority of the operational cost associated with electrolysis, regardless of technology. Figure 1 shows that 1¢/kWh is needed to achieve competitiveness to SMR. The cost of electricity varies greatly between countries and even within regions, but it is generally not available at this price over long periods. It is however conceivable that – at times when supplies far exceed demand – cheap electricity can be supplied intermittently and used to produce hydrogen. This topic is outside the scope of this article, but national agencies like the DOE are looking at the overall balance of technologies (renewable, fossil, and nuclear) to provide both grid resilience (e.g. no blackouts) and electricity at competitive costs.
IRONMAKING USING HYDROGEN
Using hydrogen to make iron is not a new concept. Over the last 50 years, direct reduction technologies like the MIDREX Process and ENERGIRON use a majority of hydrogen in the reducing gas (balance is mostly CO), and already offer a significant reduction in CO2 emissions. Other technologies have been tried and others are underway, driven in part by the desire to reduce emissions (raw materials and cost reductions are also important). For example, Cleveland-Cliffs, Lurgi, and LTV Steel built a 400,000 tons/year Circored direct reduction plant in Trinidad that used hydrogen from a steam reformer as its reductant and energy source. The plant was started up in 1999, but the fluidized bed reactor had numerous problems and it produced only about 150,000 tons by the time it was shut down in 2001. More recently, the Flash Ironmaking technology – developed by the University of Utah with support from AISI and DOE – is looking at building a demonstration plant.
Perhaps more of an evolution than a breakthrough technology, the MIDREX Process already uses large amounts of hydrogen to produce DRI. The process can be adapted to accommodate more hydrogen as it becomes economical to do so. The process uses CO and H2 to accomplish reduction, which is the removal of oxygen from ore (opposite of oxidation).
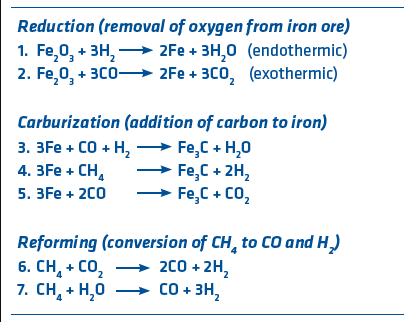
FIGURE 2. Ironmaking Reactions
There are many reactions occurring in the direct reduction reactors, but the primary ones are shown in Figure 2. Iron is represented by Fe and methane (primary component of natural gas) is represented by CH4. In the case of the standard MIDREX NG Process, the typical gas content is 55% H2 and 36% CO. Since reduction occurs at about 900°C, temperature control is a very important consideration. Reaction 1 is endothermic (requires heat) while reaction 2 is exothermic (gives off heat). Reforming reactions are highly endothermic and mostly done in the reformer, although some in-situ reforming takes place in the shaft furnace. Careful consideration and design of the process temperatures makes the MIDREX Process easy to control. Since 1969, MIDREX Plants have produced more than 1 billion tons of DRI made with over 50% hydrogen.
Direct reduction with higher levels of hydrogen has been proven in a MIDREX Shaft Furnace. The FMO MIDREX Plant in Venezuela uses a steam reformer, and the H2/CO ratio has varied from 3.3 to 3.8. There are six MIDREX Modules that utilize gas made from coal, and these have hydrogen-to-CO ratios from 0.37 to 0.56. Thus, the MIDREX Process has successfully produced DRI at H2/CO ratios from 0.37 to 3.8.
On a smaller scale, Midrex has vast experience with hydrogen reduction. In the late-1970s to mid-1980s, Midrex operated a pilot plant at its R&D Technology Center. The pilot plant was built to test and demonstrate the Electrothermal Direct Reduction Process (EDR). While the purpose of this pilot plant was not to test hydrogen reduction, several campaigns utilized a very high hydrogen content – as high as 4.2 H2/CO in 1986.
More recently, all tests designed to evaluate carburization kinetics, which are the basis for the MIDREX Adjustable Carbon Technology (ACT™), were performed under pure hydrogen in the experimental furnace at the Midrex R&D Technology Center [3].
In 2017, Midrex introduced two concepts: MIDREX H2 (100% hydrogen as the feed gas) and a MIDREX NG flowsheet with H2 substituted for part of the natural gas [4]. Together with the MIDREX NG flowsheet, they provide a staged transition to the Hydrogen Economy.
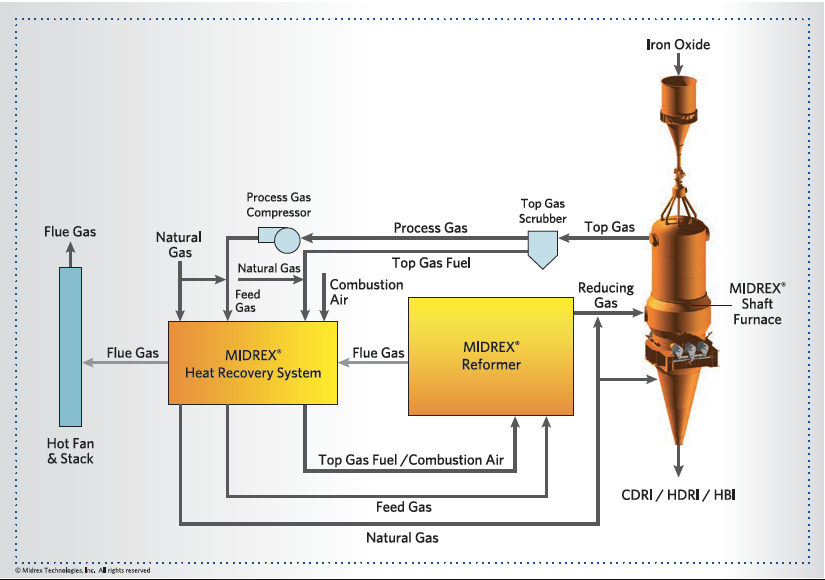
FIGURE 3.
MIDREX NG standard flowsheet
- MIDREX NG (Figure 3) is well-proven and can cut CO2 emissions by half or more immediately and without technology risks. The product of this plant (CDRI, HDRI or HBI) can be used in the EAF or BF/BOF in existing melt shops with limited or no modifications.
- MIDREX NG with hydrogen addition (Figure 4) can displace some natural gas in an existing MIDREX NG plant as green hydrogen becomes available, the MIDREX NG flowsheet can accommodate up to 30% substitution by hydrogen without modification of equipment. For example, 20,000 Nm³/h of natural gas can be substituted by approximately 60,000 Nm³/h of H2 in a 2.0 million t/y plant, which represents approximately 30% of the total natural gas consumption. For substitution up to 100%, an external steam supply, which can be supplied by a boiler or from other sources of steam at an integrated steel plant, is required to protect the reformer. The maximum hydrogen addition without modification of the flow-sheet depends on a number of factors including the desired carbon level in the DRI. This modification can be done to an existing plant or designed as an option in a new plant to provide future flexibility. The heater design would depend on energy sources available economically including a hydrogen-fired heater. The MIDREX Plant is flexible enough to allow changes in energy source over time to accommodate the likely fluctuations (daily or seasonal) in hydrogen availability when the infrastructure transitions from a Carbon to a Hydrogen Economy. The hydrogen can be generated on-site or provided over-the-fence.
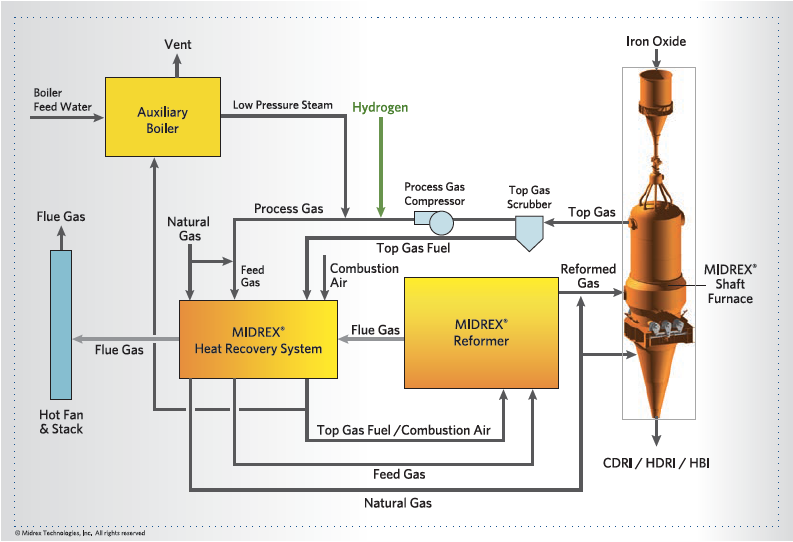
FIGURE 4.
MIDREX NG Process with hydrogen addition
MIDREX H2
-
FIGURE 5a. MIDREX H2 with hydrogen supplied over-the-fence
MIDREX H2 is similar to the standard MIDREX NG flowsheet except the hydrogen input gas is generated externally to the process (see Figures 5a) or integrated within the process (Figure 5b, next page). Thus, there is no need for the reformer; only a gas heater is needed to heat the gas to the required temperature. For an existing plant, the reformer can easily be converted to a heater since the heat duties are lower due to the absence of endothermic reforming reactions. For a new plant, the duties of each major piece of equipment will be defined specifically for hydrogen. Process modeling and laboratory experiments conducted at the Midrex R&D Technology Center have proven that almost pure hydrogen can be used to make DRI in a MIDREX Shaft Furnace, as currently designed.
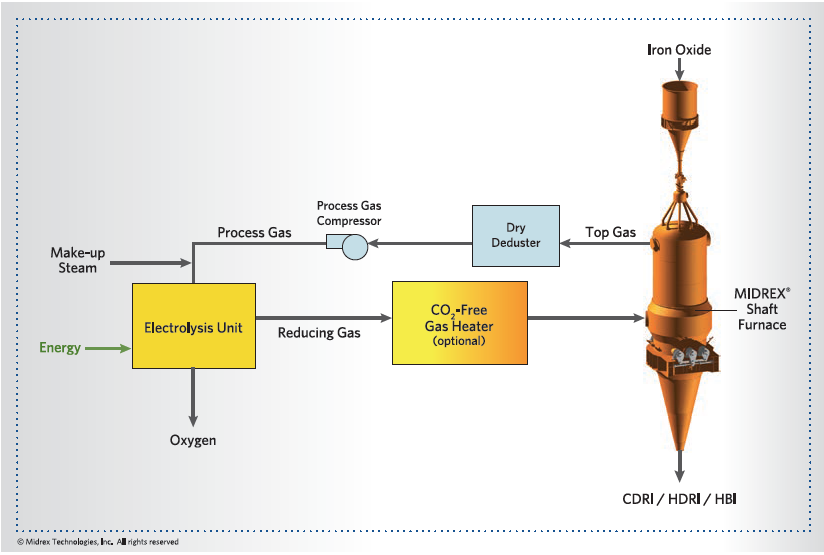
FIGURE 5b.
MIDREX H2 with integrated hydrogen generation
For this flowsheet, the hydrogen consumption is approximately 550 – 650 Nm³/t DRI. Additionally, up to 250 Nm³/t DRI of H2 or another environmentally friendly heat source, such as waste heat, electricity, and natural gas is required as fuel for the reduction gas heater. With this process, CO2 emissions could be reduced up to 80% vs. the BF/BOF steelmaking route.
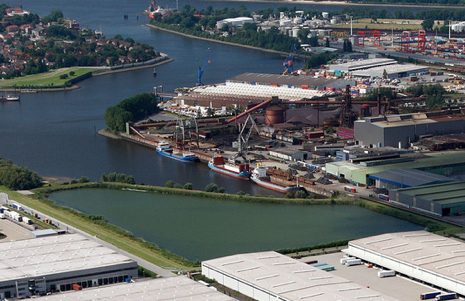
FIGURE 6. MIDREX Plant Owned and Operated by ArcelorMittal
In September 2019, ArcelorMittal announced an agreement with Midrex to design a demonstration plant at its Hamburg site to produce steel with hydrogen (Figure 6). The project will demonstrate the large-scale production and use of DRI made with 100% hydrogen as the reductant. In the coming years, the demonstration plant will produce about 100,000 tons of DRI per year, initially with “blue” hydrogen sourced from natural gas. Conversion to green hydrogen derived from renewable energy sources will likely take place once available in sufficient quantities and at an economical cost. The plant will be the world’s first direct reduction plant on an industrial scale powered by hydrogen.
ISSUES FACING HYDROGEN IRONMAKING
There are a few issues to consider for making DRI with hydrogen; the first of which is temperature. With such a large amount of hydrogen, the energy balance of the shaft furnace is affected by the absence of the exothermic carbon monoxide reduction (reaction 2 in Figure 2) to balance the endothermic reduction (reaction 1). Thus, it is necessary to add energy to the shaft furnace to carry heat in the burden. Midrex has several options available to control the shaft furnace heat balance.
The second issue is the resulting DRI carbon content; the DRI will have 0% carbon with pure hydrogen. The majority of DRI is used in EAFs, and EAF steelmaking practice generally employs carbon addition either in metallic charge materials, such as DRI, HBI and pig iron, or even pure carbon. Part of the carbon is needed to complete the metallization of the DRI, and the majority is burned with injected oxygen to create a significant amount of heat, thus reducing electricity consumption and enabling faster melting. DRI can have 1-4.5% carbon depending on the process, the type of reducing gas, and the way the DR plant is operated. Most EAF steelmakers prefer to use DRI with 1.5-3% carbon, but the optimum carbon level varies based on metallic charge mix and the steel grade produced. Under current melting practices, it will be necessary to add hydrocarbons at some place in the process to achieve the desired carbon level, including addition of hydrocarbon to the cooling zone or in the furnace lower cone. However, this added carbon will then be converted to CO2 in the EAF. The next evolution in steelmaking will be to melt iron without using carbon, but this will be very energy intensive since the melting point of steel increases as carbon content decreases. Alternatively, carbon from a renewable source (like biomass) could be used in the MIDREX Process to make the process carbon-neutral.
A 3-STEP TRANSITION FOR IRON & STEEL PRODUCTION
Since the BF-BOF process is unlikely to meet the target CO2 reductions, steelmakers – especially European steelmakers – face a daunting challenge in transitioning to (near) carbon-neutral ironmaking. Blast furnaces are generally old and need expensive relines and EAFs cannot meet the target residual levels without significant amounts of ore-based metallics (like pig iron or HBI). Hydrogen is not available in quantities and cost needed to be competitive; and no one can predict when it will be.
As a possible answer, Midrex introduced two modifications of the MIDREX NG process that use some or all hydrogen as the reducing gas (see Figures 4 and 5), which will allow a 3-stage transition to the Hydrogen Economy:
Step 1: Build a MIDREX NG Plant and take immediate advantage of the reductions in CO2 emissions. The product of this plant (CDRI, HDRI or HBI) can be used in existing BOF and EAF meltshops, as well as BFs
(in the case of HBI).
Step 2: Add up to 30% hydrogen as it becomes available, but not in quantity or cost suitable for full transition to MIDREX H2. The MIDREX Plant is flexible enough to allow changes in energy source over time to accommodate the likely fluctuations in hydrogen availability when the infrastructure transitions from a carbon to a hydrogen economy.
Step 3: Modify the MIDREX NG Plant to the MIDREX H2 flowsheet and take full advantage of the available hydrogen when it becomes widely available and cost effective to do so.
This approach offers the ability to ‘buy time’ while minimizing technology risks. The MIDREX Process is a proven and reliable technology with immediate environmental benefits. The intermediate step of hydrogen addition does not require many modifications to an existing plant and can be pre-engineered on a new plant. Converting to MIDREX H2 will require modifications of some of the process equipment, as the process duties (flows, temperature, gas composition etc.) will change.
These modifications will be necessary regardless of the direct reduction technology selected.
CONCLUSION
Iron and steelmaking are a large contributor to the emission of greenhouse gases, notably CO2. The industry is facing increasing pressure to de-carbonize, but there are many challenges to overcome. Hydrogen ironmaking is a real possibility for future (near) carbon-free steelmaking, but there are significant uncertainties around the availability of hydrogen in volumes needed for ironmaking and at a competitive cost.
The best possibility for reducing the steel industry’s CO2 footprint is the use of hydrogen as an energy source and reductant for iron ore in the MIDREX Process. Today, reduction of CO2 emissions by 50% (over BF/BOF) is achievable and well proven. Although the hydrogen comes from natural gas (‘blue hydrogen’), the process is flexible to accept ‘green’ hydrogen produced from water electrolysis as it becomes available and economical, which will further reduce CO2 emissions. Ultimately, the use of hydrogen in the MIDREX Process – known as MIDREX H2 – holds great promise to be developed and realized in either new or existing DRI plants. Investments for the future can be made today with a MIDREX Plant, knowing that it is adaptable to the Hydrogen Economy.
SUMMARY
Mitigating CO2 emissions in the iron and steel industry is becoming critical worldwide, but especially in Western Europe as the cost of CO2 emissions increases over time. The MIDREX NG Process paired with an electric arc furnace (EAF) has one of the lowest CO2 emissions of any steelmaking route today and has been proven commercially. It is possible to further significantly reduce the CO2 footprint by using green hydrogen with MIDREX H2 to produce CDRI/HDRI/HBI as a feedstock for steelmaking. Unfortunately, hydrogen is not currently available at sufficient scale and low cost for rapid adoption. In the transition to a Hydrogen Economy, the MIDREX Process can be converted to MIDREX H2 in stages allowing the steelmakers to take advantages of CO2 reduction immediately, and further reduce them in the future without major capital expenditure.
References
[1] United Nations Climate Change website (https://unfccc.int/)
[2] H2@scale website (https://www.energy.gov/eere/fuelcells/h2scale)
[3] Arandas, M. et al. “New Technologies for Maximizing Operational Flexibility of MIDREX® DRI Plants: Adjusting Product Carbon in MIDREX® DRI Products”. AISTech 2017 Conference, Nashville, TN.
[4] Millner, R. et al. “Future of Direct Reduction in Europe –Medium and Long-Term Perspectives”. ESTAD conference, June 2017, Vienna, Austria