The Basic of DRI Plant Safety
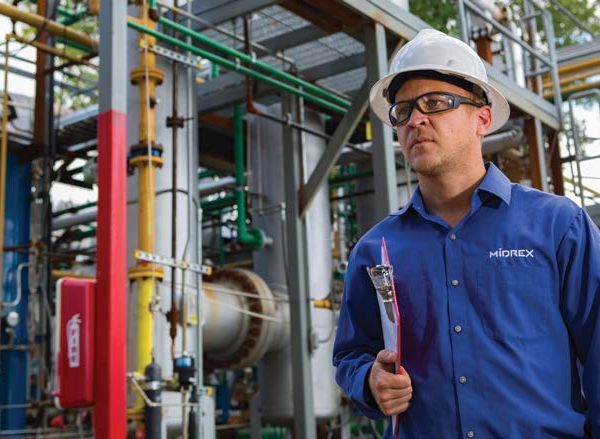
INTRODUCTION
From the earliest days, personal safety of plant personnel and protection of plant equipment have been of paramount importance in the design and operation of MIDREX® Direct Reduction Plants. After all, a MIDREX Plant is a chemical plant that processes iron oxide using combustible, explosive, and toxic gases at high temperatures.
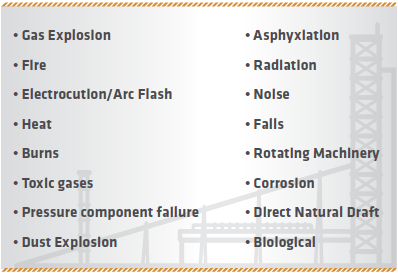
FIGURE 1. Potential hazards within a MIDREX Plant
The original purpose in our plant design was to provide the safest working environment possible. MIDREX Plants are good examples of this safety-by-design concept and have enjoyed an excellent safety record since the first start-up in 1969.
Midrex engineers are ever-mindful of the basic design guidelines that have proven time and again to provide the highest level of personal safety for plant operators while producing the most tons of DRI: keep it simple, provide safety interlocks, develop procedures for safe operation and train plant personnel to recognize hazards (Figure 1) and follow safety procedures.
When discussing plant design safety, three areas/operations within a MIDREX Plant deserve particular attention: gas handling, materials handling, and storage.
GAS HANDLING
MIDREX Plants handle the following types of gases: natural gas, process gases, inert gas, and flue gas. For combustion to occur, the concentration in air of combustible gases must be within their flammable limits and a minimum percentage of oxygen must be present to generate sufficient heat. The flammable limits of the gases used in the MIDREX Direct Reduction Process and the oxygen percentages necessary for combustion are shown below.

Ignition will occur when the auto-ignition temperature of a gas-air mixture is within its flammable limits and the oxygen level is more than the limit for the gas. The auto-ignition temperatures of the fuel gases used in the MIDREX Process are hydrogen, 570° C; carbon monoxide, 610° C; and methane, 630° C. Therefore, it is essential that no unburned flammable gas-air mixture is allowed to accumulate in the furnace, which could cause an explosion later. Purging the furnace to below 5% oxygen is a safe practice; however, a plant operator always should know the composition of the other 95% of gases present before proceeding.
The MIDREX Reformer is designed to ensure:
- the reformer is purged with air
- the auxiliary burners have the proper gas-air mixture for ignition to heat the reformer box
- the main burners are ignited after the reformer box temperature exceeds 980° C (220° C above conventional furnace combustion practice)
Midrex engineers design the process gas recirculating system to be kept under pressure to avoid introducing any source of oxygen into the system. Therefore, the system should be purged with nitrogen prior to depressurizing it to atmospheric pressure.
Gas monitoring equipment plays a key role in protecting employees from harmful gases or environments while working in a MIDREX Plant. Whether it is during start-up, commissioning, shut downs, or other maintenance activities, these personal pieces of equipment can and will save lives. All employees who wear a personal gas monitoring device must be trained in proper operations of gas monitoring equipment prior to entering a plant site.
Asphyxiation can occur when gaseous contaminants, called asphyxiates, displace the oxygen in breathable air. Chemical asphyxiation occurs when a contaminant, such as carbon monoxide, reacts with hemoglobin to prevent the blood from transporting oxygen. In low concentrations, asphyxiates do not present an immediate threat but in higher concentrations, they can displace the oxygen in the blood and result in loss of consciousness or eventual suffocation.
Gas leaks, whether from the process system or natural gas piping, must be detected and identified immediately. Large changes in gas pressure, temperature, flow, or analysis can indicate leaks in the gas system. Any gas leak that presents the chance for explosion must be repaired immediately. The determining factor in these cases should be safety – not economics.
Gas leaks can be detected by carbon monoxide (CO) monitors located at various points throughout the plant or by portable personal CO monitors. When a leak is detected, a local alarm is activated to warn personnel in the area, and a remote alarm notifies those in the control room. If the plant only utilizes portable CO monitors, it is the responsibility of the worker to advise the control room and others of the danger. If the plant does not utilize fixed monitors, all employees must be equipped with a portable CO monitor system.
MATERIALS HANDLING
The natural tendency of all iron is to rust; i.e., to combine with oxygen in air (oxidize) and in water (corrode) to form iron oxides. This is intensified in the case of DRI. After all, DRI is the result of oxygen being chemically removed from iron oxide.
The tendency of DRI to oxidize or corrode is called reactivity. All types of DRI are reactive regardless of the production process or product form. Prolonged exposure of DRI to water reduces product metallization due to rusting (the product of corrosion). Any iron mass eventually will be entirely converted to rust given sufficient time, oxygen, and water.
Rusting also generates heat and in bulk scenarios, this heat can cause DRI to ignite if the heat becomes trapped inside a product pile. Excessive fines within a DRI pile also can pose a safety hazard, especially if the fines become wet and are buried in the pile.
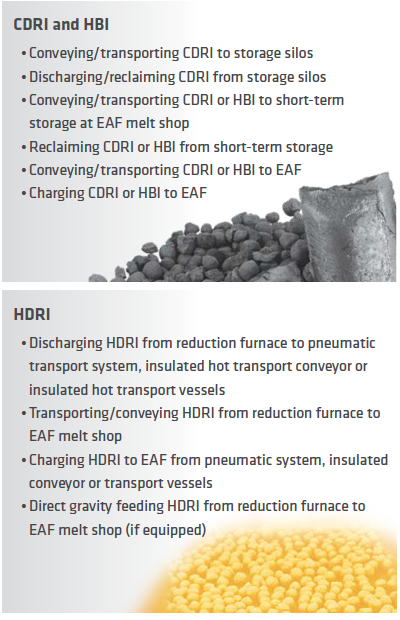
FIGURE 2. Characteristics of DRI handling systems
To preserve product quality, care must be taken to varying degrees with each product. As a general rule, users should try to minimize any unnecessary handling of the product. A material handling system should be designed for the minimum number of transfer points required to move material from point A to point B and with the shortest drops. The easiest way to minimize the number of transfer points is to take material along the straightest path possible. However, care should be taken not to compromise metering and feed control in an attempt to eliminate all transfer points. Spillage from overloaded belts may lose more material than breakage through the extra transfer point of a feeder.
A typical DRI handling system associated with a captive DRI plant may include the operations shown in Figure 2.
A frequently quoted estimate for cold DRI (CDRI) breakage due to handling is 0.25% loss per 2-meter drop. This number can be much larger for weaker material, longer drops, or poorly designed transitions. Fines and chips generated during handling will oxidize much faster than whole DRI products. A conservative number is 15% loss for -6.35 mm fraction material after exposed (outdoor) storage for a month.
Hot DRI (HDRI) can be transferred from the DRI plant to the melt-shop by hot transport vessels, hot transport conveyors or pneumatic transport, depending on the distance between the DRI plant and the melt shop, or by direct gravity feeding in the case of a close-coupled reduction furnace and EAF. Hot transport vessel systems employ ladle-type insulated vessels that are transported on flat-bed trucks and can be (next page) maintained at temperature if the melt shop is delayed in accepting the HDRI. Pneumatic transport systems use gas to blow DRI at high velocity through pipes to carry it to the EAF or to a product cooler. The high velocity and resultant turbulence can cause significant breakage and erosion of the HDRI, especially at bends in the pneumatic line. This method can result in fines generation of as much as 8-10%. Hot conveyor systems using enclosed conveyor buckets are less jarring and greatly reduce HDRI fines generation.
GENERAL GUIDELINES FOR DEALING WITH GAS LEAKS
- Always use properly calibrated gas monitoring equipment before entering a hazardous atmosphere.
- Priority must be given to warn plant personnel of any gas leak. The area surrounding a gas leak should be roped off and identified as a safety hazard.
- Any area where gas could accumulate in explosive proportions, such as under the reformer, should be repaired immediately. Personnel should be evacuated, and the area should be ventilated if at all possible.
- Leaks in the seal gas piping should be treated with caution and repaired as required to maintain safety and proper operation of the seal gas system. Remember, seal gas in an enclosed area can cause asphyxiation. If a leak develops where proper ventilation cannot be ensured, the leak must be repaired immediately.
- Gas leaks in the feed gas, reformed gas, and bustle gas piping, as well as leaks from the furnace can burn without being seen. During daylight hours, leaks often can be located by a “hissing” sound. In the case of hydrogen, only very faint heat waves can be seen. Exercise extreme caution when trying to pinpoint the location of a leak. Never use your hand to feel for a leak.
- Any equipment or machinery that could be a source of ignition should be removed from an area where a gas leak occurs.
- Gas leaks within the analyzer building can cause a toxic buildup of combustibles. MIDREX Plants include a ventilation fan, which continuously forces fresh air into the analyzer building. It is imperative the ventilation system operates at all times and is kept in good working condition.
- Gas leaks from the cooling zone of the shaft furnace or product cooler may contain carbonyls. As with other gas leaks, the area surrounding the gas leak should be roped off and identified as a safety hazard.
STORAGE
CDRI can be stored safely in open, well drained piles if it will not be moved until it is used in the melt shop. Rain only can penetrate the stack to a certain depth, typically less than a meter. Although the resulting corrosion will reduce the metallization, as described earlier in this article, the stack should not overheat unless additional material covers the wet area. This will insulate the wet iron and prevent the dissipation of the associated heat, which can cause the pile to overheat and lead to ignition.
HDRI is not intended for long-term storage but can retain much of its heat when needed to wait for a charging cycle or to be transported to a different nearby melting furnace. This is a temporary option when using hot transport vessels and not really an option with using pneumatic or conveyor bucket systems.
Hot briquetted iron (HBI) is normally stored outdoors in exposed piles built on a firm, well drained surface. Bulk piles of HBI tend to dissipate heat rapidly due to good thermal conductivity characteristics and a shape and form that create voids in the pile. HBI, like scrap also can rust. Rusting has been observed to reduce its metallization by less than 1% per month even in salt-laden, humid air and frequent, heavy rainfall conditions.
The following precautions should be followed when storing DRI products outdoors:
- Build pile on a firm base, such as concrete, and ensure proper drainage to prevent the intrusion of water under the pile. The base should provide protection from moisture in the ground. A sealant layout of tar, bitumen or some other material impervious to water should be laid down before the concrete is poured.
- Keep DRI away from corrosive chemicals, such as salt
- Avoid excessive fines content in the pile.
- In the case of CDRI cover the pile to keep DRI dry and to prevent air stacking in the pile.
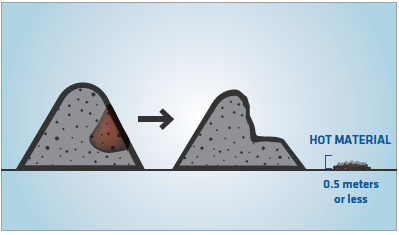
FIGURE 3. Method for controlling hot material in a storage pile
A DRI pile will warm up to about 60°C/140° F as steaming occurs but will cool down again to ambient temperature when the water is evaporated. Normally it is not necessary to take additional action if the pile is steaming as long as the temperature does not exceed 100°C/212° F.
In case of a pile of DRI overheating to temperatures in excess of 100°C/212° F, the overheated material should be removed from the pile and spread out on dry ground in a layer of about 0.5 meters using a track-equipped bulldozer or front-end loader, as shown in Figure 3. Another method is to bury the pile under sand or other suitable material to cut off the oxygen supply.
Storage bins and silos are used to protect DRI products when there is a time delay between arrival and when the product can be used or shipped. Badly designed silos can create operational problems and a decrease of product quality. The design of silos should be determined on the basis of the material flow properties of the bulk solid(s) to be stored. The expenses for testing and silo design are small compared to the costs of lost production, quality problems, and retrofits that may be needed because of irregular flow patterns.
The precautions shown in Figure 4 are recommended when storing DRI products.
All employees should be trained in the methods and procedures for proper storage and handling of DRI prior to starting their assignment. They should have access to Safety Data Sheets (SDS), which will provide them with important information on DRI storage, handling, and other safety pre-cautions. All SDSs must comply with the Globally Harmonized System, which was adopted in 2013. All SDS records are kept and maintained for each MIDREX Plant.
OTHER SAFETY CONSIDERATIONS
Midrex also incorporates in its plant designs various fire and explosion protection features, such as:
- Non-combustible and low-combustible construction materials
- Site selection in an open, well-ventilated area
- Separation of plant sections to prevent “domino effect”
- Paved and/or concrete surfaces in fire risk areas
- Two (minimum) escape routes from every point in the plant
- Fire alarms which activate visual and audible signals
in the control room - Automatic shutdown in case of pressure drop (gas valves go to fail-safe positions and purge gas is supplied immediately
- Carbon monoxide monitors and alarms
- Critical areas are well marked and signed
(Important Note: Water should not be sprayed on an overheated DRI pile under normal conditions. However, in case of a runaway fire, the pile should be inundated with a strong water stream. Firefighters should be prepared for violent steaming and hydrogen flashing resulting from such action.
PRECAUTIONS FOR STORING DRI PRODUCTS
- Any DRI at a temperature in excess of 65° C should not be sent to a storage bin or silo. It should be separated from all other material and piled no more than one meter high.
- Bins and silos should be purged with an inert gas from the bottom.
- Top slide gates should be closed except when DRI is being delivered.
- Bottom slide gates should be closed except when DRI is being discharged..
- Inert gas should be introduced into the top of the bin or silo during extended storage periods to ensure a slight positive pressure while the top and bottom slide gates are closed.
- Periodic gas analyses should be performed to ensure that oxygen level is below 3% and hydrogen is not being generated.
- Temperature within the bin or silo should be monitored. If high temperature (65-75° C) is observed, the bin or silo should be sealed and purged from the top until it cools. If the temperature rises to above 90° C, the DRI should be removed from the bin or silo.
FIGURE 4. Recommended precautions for storage bins and silos
CONCLUSION
Workplace safety is a crucial part of any successful, well managed business and keeping people safe should be first priority. DRI plants and products can be potentially dangerous under certain conditions if the proper precautions are not taken. There are no cost savings worth the risks of shortcutting safety procedures when producing, handling, and storing DRI products. Loss of life, injuries, or destruction of property are costly on many levels. Direct cost to the company for a major accident include at a minimum: worker compensation claims, indemnity payments, and legal fees. Direct costs for a disabling on the job injury or death can quickly exceed seven figures.
The indirect costs are much more expensive over the long-term. The indirect costs of a lost time accident (LTA) will generally exceed the direct costs by a ratio of 4 to 1 or higher and compound into the millions of dollars in total cost over time. With the true costs of major injury accidents in mind, clearly the best way forward to stay with best industry practices and safety standards to help ensure safest possible conditions.
Midrex Technologies Inc. strives to be the worldwide leader in DRI production and we work just as hard to have the safest DRI plants in the world. Midrex provides each plant a detailed safety manual, and our employees go through rigorous safety training. We investigate all incidents, large or small, to identify causes and pinpoint potential hazards so corrective actions can be taken to ensure that every MIDREX Plant is as safe a working environment as possible.