Technical Excellence with a Human Touch: Engineering, the Midrex Way
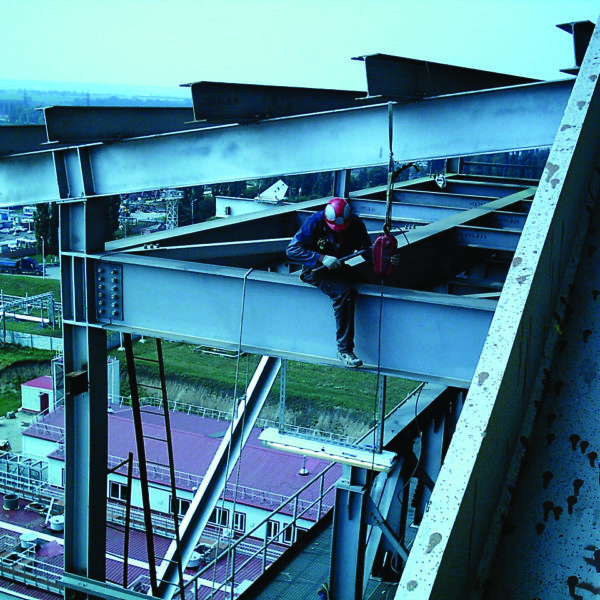
Midrex engineers are as accustomed to being at a plant site as they are to being in the office behind a computer.
From the start-up and commissioning of the first plant in 1969, Midrex engineers have run calculations, devised control loops and designed specialized equipment and then gone to the field to put them into action.
Midrex attracts a special breed of engineers – people who question how things are done, but are eager to learn; people who are adventurous, but responsible; and people who strive for individual achievement while contributing to the success of the team.
Within Midrex Engineering there is a culture of personal “ownership” of the technology and a camaraderie borne of a common purpose: to maintain the technical excellence the industry has come to expect of MIDREX® Direct Reduction Technology.
WHAT MAKES MIDREX UNIQUE?
Most companies known for industry-leading products and services have thousands of employees and own sprawling office campuses. Midrex, on the other hand, prides itself in being large enough to properly get the job done – designing, engineering and servicing the most reliable direct reduction plants in the world – but small enough to give each project the personal touch.
Midrex is first a technology company. Most similar type and size companies are content to license their technology and have a passive role in how it is used. Midrex is different because it also is an engineering and technical services company, which allows Midrex to take an active role in every project.
The involvement of Midrex from basic design through the supply of aftermarket services and materials assures customers that their MIDREX® Direct Reduction Plants will have long and productive lives. For example, some plants, such as Arcelor Mittal Hamburg (formerly Hamburger Stahlwerke, GmbH), ArcelorMittal Montreal 1 (formerly Sidbec-Dosco I) and Tenaris Siderca (formerly Dalmine Siderca) are into or entering their fourth decade of reliable operation.
CONTINUING THE MIDREX TRADITION
Although computers have replaced drawing boards and email has supplanted the fax machine, the development of engineers within Midrex remains true to tradition. The leads in three of the groups within the Engineering Department are good examples of how Midrex insures its technology remains in touch with the realities of plant operations and performance while striving for the next innovation and improvement.
Geoff Wallwork Chief of Process Engineering for Midrex
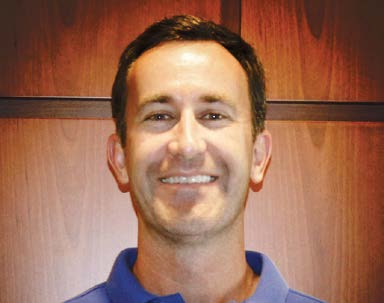
Geoff Wallwork
Let’s start with Geoff Wallwork, Chief of Process Engineering for Midrex. Wallwork developed an early appreciation for the theory of the MIDREX® Direct Reduction Process through interaction with senior Midrex process engineers and a propensity for computer modeling. His deep understanding of process fundamentals and control loops has been honed in the office and the field, where Wallwork has been involved in numerous task forces assigned to troubleshoot and optimize plant systems.
Wallwork has participated in the start-up or optimization of every type of direct reduction plant that Midrex designs, from shaft furnace-based plants utilizing natural gas or syngas from coal to rotary hearth furnace-based plants. His chemical engineering background, office training, and field experience with real-life operation of MIDREX® Plants has served him well in recognizing process and safety aspects associated with the plant design, construction and improvement.
“How often do you get to come up with an idea, see it take shape, and be part of putting it into action?” asked Wallwork. “That, and the opportunity to travel to interesting places that most people don’t know exist are for me what makes Midrex a special place to work.”
Brian Voelker Chief - Proprietary Equipment
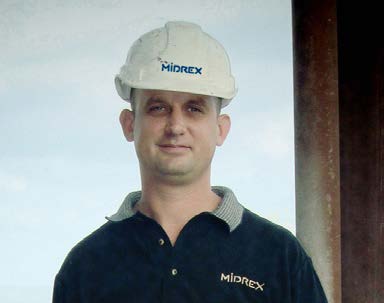
Brian Voelker
Brian Voelker is Midrex’s Chief of Proprietary Equipment. Voelker joined Midrex with a degree in mechanical engineering and experience designing equipment and systems for pre-heating, conveying and melting scrap steel. Early in his Midrex career, Voelker participated in the start-up and commissioning of the MIDREX® Hot Briquetted Iron (HBI) Plant for COMSIGUA in Venezuela. His hands-on experience with a MIDREX® Hot Discharge Reduction Furnace coupled plus his involvement with methods for handling and charging heated scrap have produced patents for charging hot DRI (HDRI) to a melter and a system for combination discharge of cold DRI (CDRI) and HDRI from a reduction furnace.
Voelker also has been instrumental in the design and optimization of rotary hearth furnace (RHF) technology at Midrex. Again, true to Midrex tradition, he followed his equipment designs for the RHF-based FASTMET® Process and ITMk3® Process from computer to pilot plant in Japan to commercial plant in Minnesota.
The makeup of his group reflects the nature of Midrex Engineering. “I have people with 39 years to less than three years of experience,” Voelker remarks. Their interaction and mutual respect are what keep us sharp and productive.”
Chris Hayes Chief - Mechanical Engineering
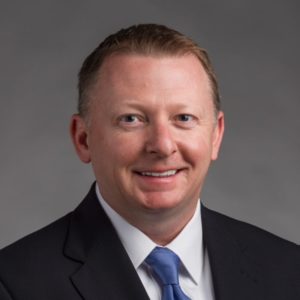
Chris Hayes
Rounding out the profiles is Chris Hayes, Chief of Mechanical Engineering for Midrex. Hayes has firsthand appreciation of the seemingly unlimited potential of MIDREX® Direct Reduction Technology. He spent most of his first 10 years with Midrex designing and optimizing in the field equipment and systems to boost the performance of existing MIDREX® Plants. With a mechanical engineering degree and knowledge of civil engineering, Hayes has served as project engineer, project manager or mechanical lead on 13 greenfield and brownfield Midrex projects in 12 countries.
Hayes has built strong relationships with key vendors to facilitate a seamless transition of plant needs into practical solutions. His experience in new plant design and commissioning & start-up teams, as well as in a broad range of engineering assignments for Global Solutions, the field and technical services arm of Midrex, has prepared Hayes to transform situations into opportunities for the mutual benefit of Midrex and its Process Licensees.
“Working shoulder-to-shoulder builds respect and confidence. This holds true whether in the office or in the field,” Hayes observed. “It’s what we do with the earned respect and confidence that produces value.”
ENGINEERING, THE MIDREX WAY
Midrex Engineering has a long tradition of attracting talented technical people and totally immersing them in the process of creating innovative technologies and using them to design, start-up and commission the direct reduction industry’s most successful plants.
A Midrex engineer is surrounded from the start by seasoned professionals, both within Midrex and from among its Construction Partners and Process Licensees. It’s the resulting interaction and mentoring that instills a sense of belonging and the perception of ownership of the technology.
Go to the site of a MIDREX® Plant currently under construction or in start-up & commissioning and most likely you will meet a future Midrex executive or maybe even a president. Then stop by the Midrex offices because on any given day, you will find several generations of Midrex engineers working side-by-side. That’s “the Midrex way”.
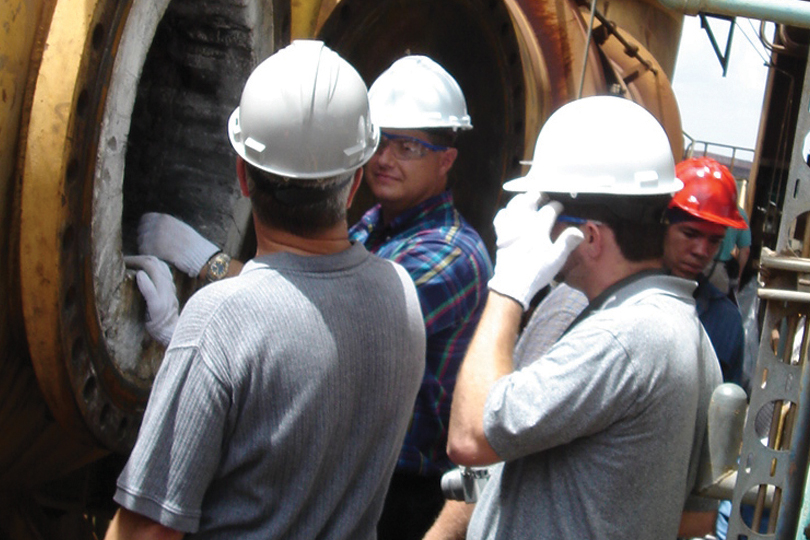