Process Gas Heater – Proven Technology for Process Flexibility
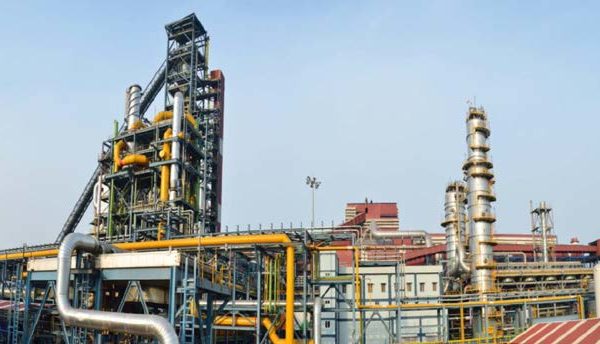
INTRODUCTION
Natural gas has fueled the growth of direct reduction of iron technology from its infancy in the mid-20th century to its role today as a source of vital feed materials for high quality steel production. This clean-burning energy source has been identified as a means to help facilitate the integration of the steel industry into the future global hydrogen economy. However, the availability and price of natural gas has posed challenges to its use for direct reduced iron (DRI) production and still does in some regions of the world. As a result, methods for producing a synthesis gas suitable for DRI production from coal gasification, coke oven gas treatment, and excess process gas have been introduced. Likewise, technology for the use of hydrogen as the reductant source for DRI production has been developed.
The MIDREX® Direct Reduction Process was conceived from the idea of reforming natural gas to produce a high-quality synthesis gas to reduce iron oxide pellets. The originators of the MIDREX Process applied their commercially proven combustion and heat transfer knowledge to create the proprietary design of a near-stoichiometric gas reformer and a gravity-flow, shaft-type reduction furnace. The current generation of Midrex engineers has adapted the world’s most efficient gas reformer to design a Process Gas Heater (PGH) for use with a broad range of alternate fuels including hydrogen in the MIDREX Process.
BASIC PROCESS REQUIREMENTS
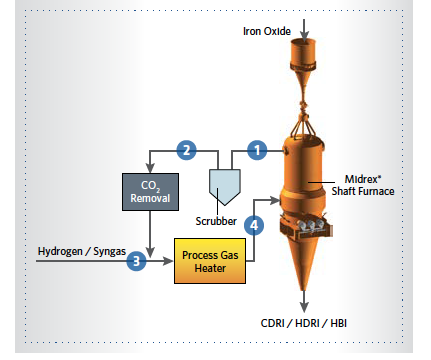
FIGURE 1. MIDREX Process alternate fuels diagram showing gas flow streams
The block flow diagram of the MIDREX Process when using alternate fuels instead of natural gas is shown in Figure 1.
The main process gas loop has several unit operations to clean, heat, and adjust the gas chemistry to the required properties suitable for the reduction of iron ore, which are summarized in TABLE I.
TEMPERATURE
The temperature of Stream 3 primarily depends on the type of the CO2 removal that is applied and the chemistry of the make-up of the fuel (syngas or hydrogen). However, from the point-of-view of the PGH, the inlet gas temperature range of 35°C to 55°C does not have a significant impact on the required heat duty because the outlet gas stream needs to be heated to a much higher temperature. For direct reduction, the minimum required temperature is 760°C; however, the state-of-the-art is to operate at much higher temperatures. In most plants, it is desirable to heat the gas to the maximum possible temperature, which is primarily limited by the softening temperature of the DRI. In modern plants, it is reasonable to expect the outlet gas from the heater to be approximately 950°C.
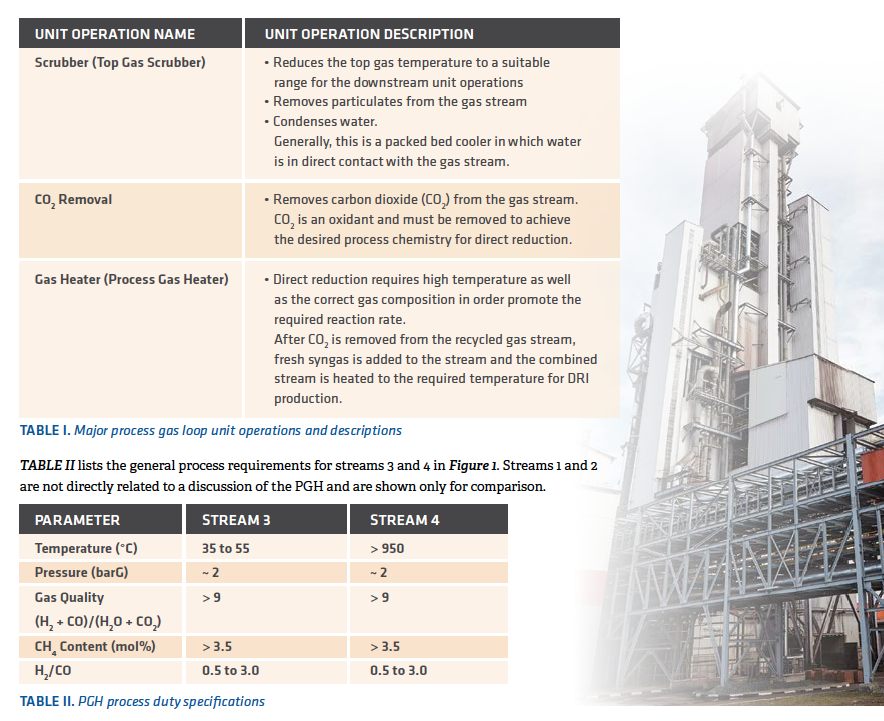
PRESSURE
The operating pressure of the PGH is set by the requirements of the reduction furnace, which generally is around 2 barG but can vary depending on the specific site conditions. The pressure is an important parameter in designing the mechanical components of the PGH, but generally the heater does not set the limitation or requirement for the operating pressure.
GAS QUALITY, CH4 CONTENT, AND H2/CO RATIO
The gas quality, methane (CH4) content, and H2/CO ratio are determined primarily by the composition of the make-up fuel (syngas or hydrogen) and also the type of the CO2 removal technology that is applied. In any case, the commercial application requires the gas quality to be greater than 9. The gas quality requirement effectively sets a limitation on the amount of H2O and CO2 that can be present in the process gas.
TABLE II shows a CH4 content of > 3.5 mol%. However, this is only the desired value and is dependent on the type and chemistry of the make-up fuel. For example, the operating range for CH4 in a MxCōl® Plant in commercial operation has been as low as 0.5% and as high as 8%.
TABLE II also shows a range for the H2/CO ratio. This value is established primarily by the type and composition of the make-up fuel to the process. In a MxCōl Plant, the commercial operating range is from 0.5 to 3.0.
HEAT DUTY REQUIREMENTS
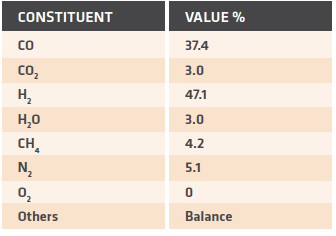
TABLE III. Composition of reference process gas
The primary process requirement for the PGH is to heat the gas from approximately 50°C to around 950°C. If we consider a gas with the composition shown in TABLE III, we can calculate the required heat duty.
The heat duty is a sole function of the enthalpy change due to increasing the gas temperature from 45°C to 950°C. For a reference plant producing 1.0 million tons per year of DRI, the total duty is in the range of 60 to 70 Gcal/h. This large heat duty requirement dictates that the PGH must be a significant unit operation when operating the MIDREX Process with alternate fuels.
DETAILED DESIGN CONSIDERATIONS
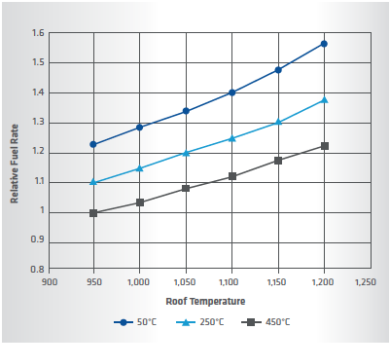
FIGURE 2. Relative fuel rate for various heater conditions
Energy Efficiency
The required large heat duty also implies that the PGH can have a significant impact on the entire plant’s OPEX. For instance, the fuel required for the burners would become too expensive to support the economical production of DRI if the efficiency is low. The key parameter that affects heater efficiency is the flue gas temperature leaving the heater box. Figure 2 illustrates a typical calculation.
In Figure 2, the relative fuel rate is shown on the y-axis. The calculation is based on a fixed gas composition and flow that needs to be heated from a fixed inlet temperature to a fixed outlet temperature. The variable axis is the roof temperature of the heater, which also is the assumed exit temperature of the flue gas, and various combustion air preheat temperatures are shown as series.
Figure 2 shows that as the roof temperature is increased, the amount of fuel needed to achieve the same heat duty to the process stream increases. This is natural because if the combustion products leave the furnace at higher temperature, the combustion gas has less available energy to contribute to the process gas. As a consequence, more fuel (combustion products) is required for the same process heat duty. The trade-off in the design becomes a question of minimizing the roof temperature to reduce the fuel consumption versus having a high enough roof temperature to satisfy the final required process gas temperature and maintain sufficient heat transfer to produce an economical design.
Figure 2 also shows the impact of preheating the combustion air. If the combustion air is not preheated, as seen in the 50°C case, the relative fuel rate is increased compared to the cases where air preheat is considered. Therefore, it is necessary to have some type of preheat to achieve reasonably low fuel rates. The exact heat recovery configuration is vendor-specific.
TUBE MATERIAL SELECTION
The process conditions and duty also play a large part in the heater tube configuration and material selection. The first concern that needs to be addressed is the maximum allowable tube wall temperature for the heater tubes. Generally, the heater tube wall temperature is highest where the process gas is the hottest. The tube wall temperature can be calculated by balancing the radiation heat transfer from the combustion box with the conductive and convective heat transfer characteristic of the heater tubes. The equations and solution methods are commonly available in heat transfer technical references and are not presented here. If we apply the typical example from this article where the roof temperature is 1150°C, the gas temperature is 950°C and the tube is made from a high-nickel alloy, then we find that the equations balance with a tube wall temperature of approximately 1050°C (roughly the arithmetic average of the process gas temperature and roof temperature). These tube wall temperatures are very high compared to the allowable temperature for even special, high temperature alloys that are typically used in these applications. Therefore, tube material must be selected to have enough temperature to withstand the process conditions. The next point of concern related to material selection is gas chemistry. TABLE II has shown that the direct reduction reaction requires a high gas quality and additionally that the H2/CO ratio depends on the type and composition of the make-up syngas or hydrogen to the plant. When the H2/CO ratio is coupled with the gas quality constraint, the CO concentration can vary widely depending on the application. TABLE IV illustrates this point.
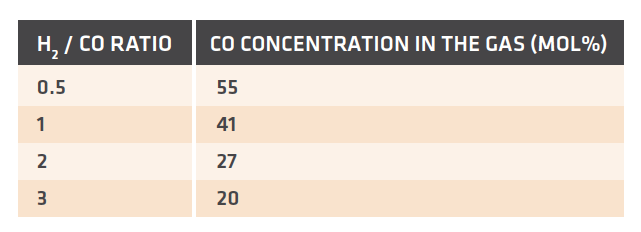
TABLE IV. CO mole % for a gas with quality of 10 and various H2 / CO ratios
TABLE IV shows the effect that the H2/CO ratio has on the gas composition within the range of ratios that has been applied commercially for MxCōl Plants. The key point of concern is that the typical process gas is a carbon-saturated stream and therefore can deposit carbon in certain temperature ranges. The two most important carbon depositing reactions are hydrocarbon cracking and Boudouard carbon deposition. The general forms of the reactions are:
Equation (1) is the hydrocarbon cracking reaction, which is endothermic and is promoted at higher temperatures. Equation (2) is the Boudouard carbon reaction, which is exothermic and is promoted at lower temperatures. In terms of tube selection, the Boudouard carbon reaction normally is more critical since it typically occurs in the range of 550°C to 650°C. The deposited carbon, if not controlled, could easily promote metal dusting of the metallic tubes causing rapid degradation of the tubes and ultimately accelerated tube failures.
It can be seen in Equation (2) that increased CO concentrations and reduced CO2 will favor the deposition of carbon from an equilibrium point of view. In TABLE IV, the CO2 concentration already is quite low due to the requirement of having a reducing gas quality > 9. Thus, the effect of the H2/CO ratio is apparent in that at very low H2/CO ratios, the CO concentration can be greater than 50%. When compared to high H2/CO ratios of 2 or 3, where the CO concentration is about 20%, the lower H2/CO ratio gases have a significantly higher tendency to form Boudouard carbon. This is especially likely in the inlet of the heater tubes where the gas must be heated to through the critical Boudouard reaction zone.
There are various strategies for handling the material selection and carbon deposition issues, and the specific strategy is up to the individual heater vendor.
FUEL TYPE
In general, there are several fuel options that can be used in the PGH. The most common fuels are Top Gas Fuel, which is generated within the MIDREX® Plant, and syngas or hydrogen, which is normally identical to the make-up process fuel. TABLE V shows typical heating values for common fuels and hydrogen.
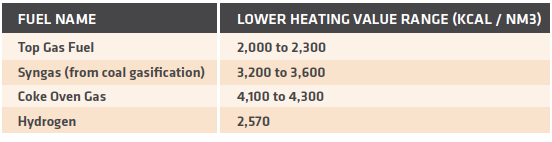
TABLE V.
Typical heating values for MIDREX Process alternate fuels
Top Gas Fuel is normally the preferred fuel, as it is generated within the MIDREX Plant. Top Gas Fuel can be used directly within the PGH without additional compression or cleaning steps. The disadvantage is that Top Gas Fuel is not available during start-up conditions. Also, if there is an interruption in plant operation, the Top Gas Fuel quantity and quality will be affected. This means that the PGH must be designed to meet the heat-up duty and plant interruption cases with fuels other than Top Gas Fuel. Considering the difference in heating values listed in TABLE V, the specific design of the burners and combustion systems is not always straight forward.
OPERATING CONDITION CONSIDERATIONS
In addition to the normal operating conditions, the PGH also must be able to handle other special or transient conditions. A few of the conditions and their special concerns are noted in TABLE VI.
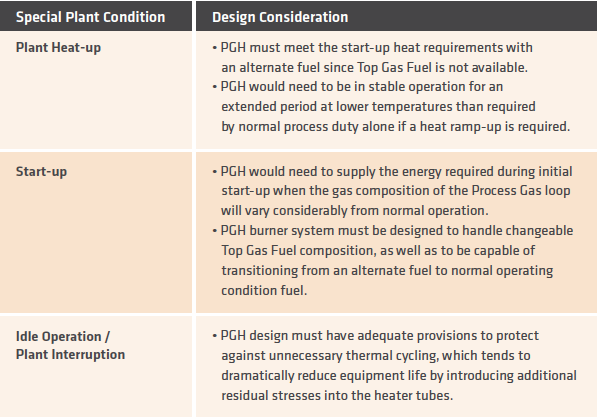
TABLE VI.
PGH design consideration for special or transient conditions
CONCLUSIONS
The Process Gas Heater is a critical unit in the operation of the MIDREX Process with fuels other than natural gas. Although several commercial designs are available that are suitable to the duty and temperature requirements, there are additional operational conditions that must be considered to achieve the required process conditions, expected operation costs, and long heater life. The Midrex PGH design is derived from the design of the MIDREX Reformer, which has proven to be the most reliable and efficient means of transforming natural gas into a high-quality reducing gas for producing DRI in use today in commercial MxCōl Plants. When the supply of hydrogen becomes available in sufficient quantities to fuel DRI plants, Midrex will be ready with a process configuration powered by a PGH that provides added flexibility to the world’s most preferred process for the direct reduction of iron.
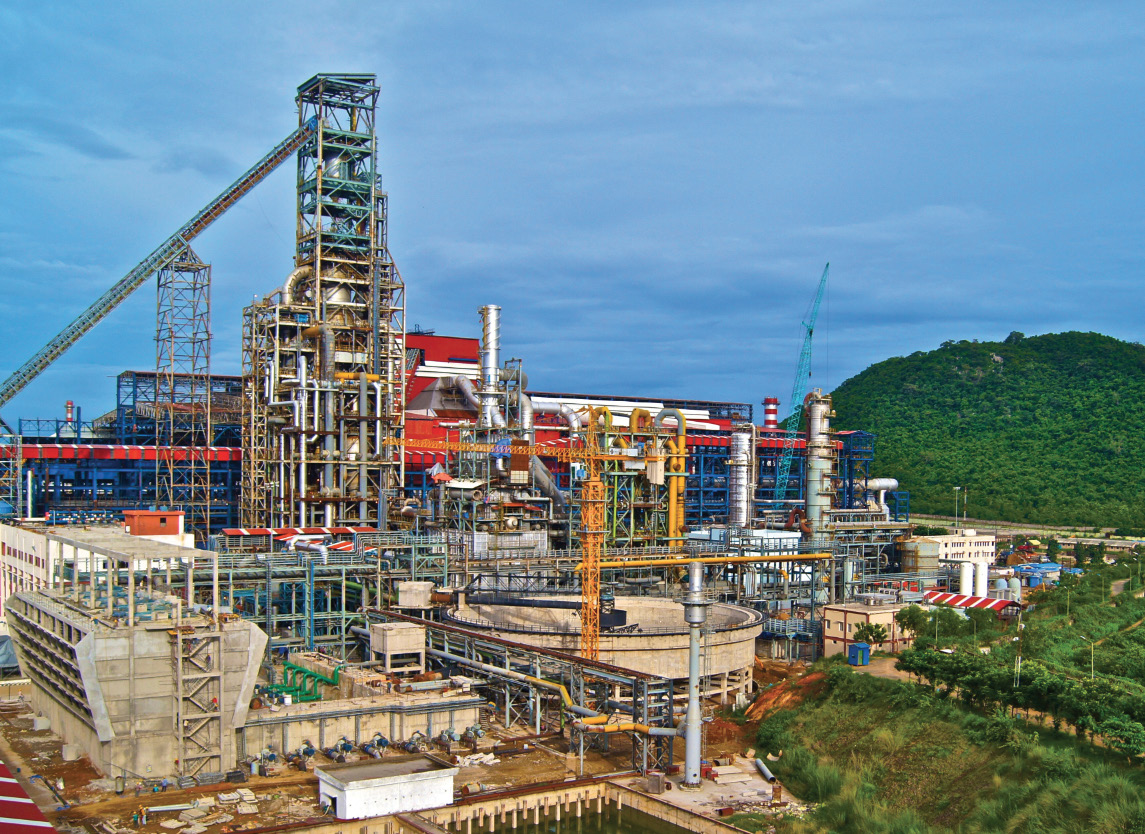