Parent, Partner and Pacesetter: Kobe Steel’s Role in the Direct Reduction Industry
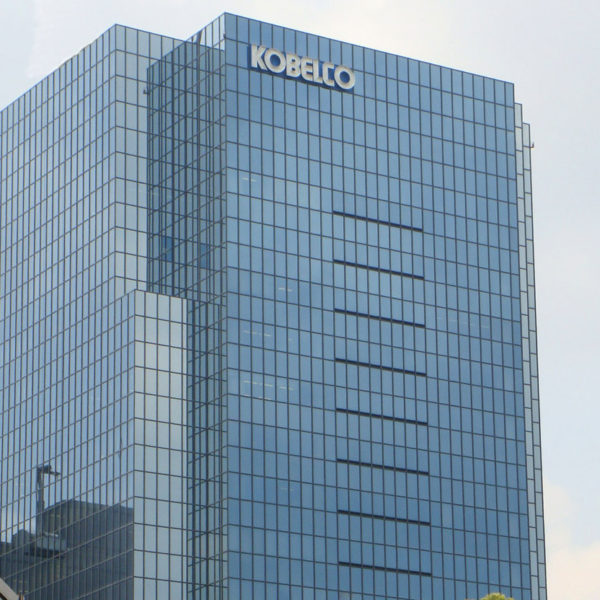
EDITOR’S NOTE:
Kobe Steel, Ltd. (KSL) is the owner of Midrex Technologies, Inc., and the Licensor of MIDREX® Direct Reduction Technology. In the past 40 years, it has supplied 14 MIDREX NG™ (natural gas-based) Plants in 10 projects located throughout the world. These plants, all of which were completed and put into production on time, represent KSL’s skill, expertise and commitment to the direct reduction ironmaking industry. This article looks at KSL’s earliest involvement in the direct reduction industry and how it has distinguished itself as an innovator and a driving force in the supply of MIDREX® Direct Reduction Plants for the past 40 years.
Kobe Steel Ltd. (KSL) KSL is one of Japan’s leading steelmakers and is comprised of numerous consolidated and equity-valued companies in Japan, Asia, Europe, and the Americas.
Since its founding in 1905, Kobe Steel, Ltd. (KSL) has pursued “monozukuri” — a Japanese approach to quality manufacturing — across a broad range of fields, supplying outstanding products and technologies that contribute to the advancement of industry and the promotion of a prosperous society. KSL is engaged in extremely diverse corporate activities including iron and steel, welding, aluminum and copper products, machinery, engineering, construction machinery, cranes and etc.
When Midrex was purchased on August 25, 1983, it became the first outright acquisition of a foreign company by KSL and positioned KSL as the world leader and innovator in direct reduction ironmaking technology.
Today, the Iron Unit Division, belonging to KSL’s Engineering Business Unit, administers the Midrex corporate relationship and participates as a MIDREX® Construction Licensee. The Iron Unit Division was established to implement EPC (engineering, procurement, and construction) projects such as steel making plants, industrial plants and chemical plants throughout the world. As a result, the Iron Unit Division is able to form strong project task forces staffed by highly experienced personnel to execute a variety of EPC projects.
Throughout the succeeding years, Midrex and KSL have cooperated closely in all aspects of the business to expand the technological boundaries of ironmaking and set the quality and performance standards of the direct reduction industry.
A KNACK FOR FIRST-OF-A-KIND PROJECTS
KSL has supplied 14 MIDREX NG™ (natural gas-based) Plants in 10 projects located throughout the world. Some of KSL’s major projects are shown in TABLE I.
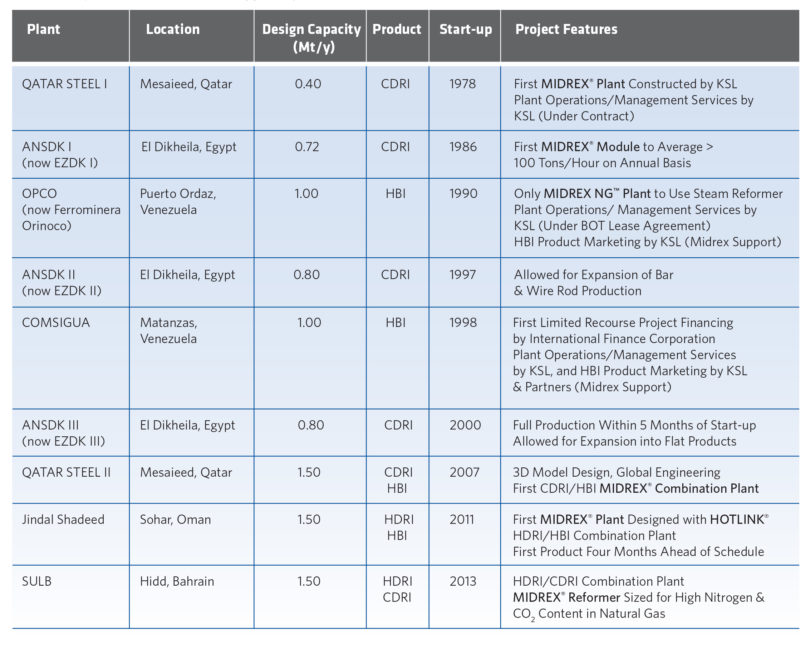
TABLE I.
Major MIDREX NG™ Plants Supplied by KSL as MIDREX® Construction Licensee
In most of these projects, KSL’s role was much more than plant builder. KSL took on the responsibilities of operating the production facilities and managing the business operations of the QATAR STEEL I, Ferrominera Orinoco (FMO) and Complejo Siderúrgico de Guayana (COMSIGUA) projects. In the case of QATAR STEEL I, the know-how necessary for successful plant operation and effective corporate management was imparted to the client during the term of the operations & management services contract. Today QATAR STEEL is wholly owned, operated and managed by Industries Qatar, a national company.
The FMO project was supplied by KSL as build, operate and transfer (BOT). This concept took full advantage of almost 20 years of building and operating MIDREX® Plants, which facilitated securing project financing. COMSIGUA was the first award by limited recourse project financing in Venezuela.
KSL has been the MIDREX® Construction Licensee for a number of first-of-a-kind MIDREX NG™ Plants including the only one to make use of a steam reformer to supply a portion of the fuel and reducing gas (OPCO), the first commercial application of the MIDREX HOTLINK® plant design (Jindal Shadeed) and plants capable of simultaneous hot and cold discharge of DRI products (QATAR STEEL II and SULB). Each of these projects was executed on time despite significant challenges along the way.
KOBE STEEL LTD., AS MIDREX® CONSTRUCTION LICENSEE
Qatar Steel Company (Module I)
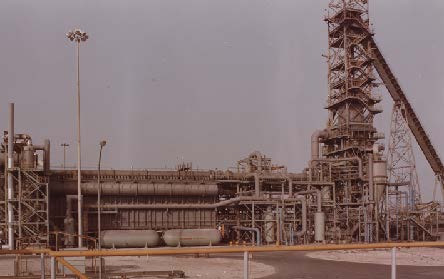
KSL’s relationship with Midrex began almost 10 years prior to KSL becoming the owner of the MIDREX® Direct Reduction Process and Midrex Corporation, as the company was then known. In 1974, Kobe Steel Ltd. (KSL) and a Japanese trading house entered into a joint venture with the Government of the State of Qatar to create Qatar Steel Company (QATAR STEEL) as the centerpiece of a national steel industry. A feasibility study found that the direct reduction/electric arc furnace (DR/EAF) process route was best suited for QATAR STEEL’s requirements. A subsequent study recommended the MIDREX® Direct Reduction Process because it was natural gas-based, adaptable to extreme climatic conditions in Qatar and had an excellent performance record. QATAR STEEL would become the first integrated steelmaking facility to be built in the GCC (Gulf Cooperation Council) region.
In 1975, a three-party agreement was signed by Midrex Corporation, Mitsui and Company Ltd. and Kobe Steel Ltd., which established KSL as a technical partner in the MIDREX® Construction License of Mitsui for the QATAR STEEL project.
The MIDREX® Direct Reduction Plant started operations in August 1978, less than 17 months after the start of construction. The plant reached its rated hourly production within the first 24 hours of start-up. Average metallization during the performance guarantee test was 94 percent, plant availability was 98 percent and gas consumption was 20 percent better than the guarantee.
In addition to the contracts for turnkey supply of the MIDREX® Plant, EAF melt shop, continuous caster and rolling mill, KSL was awarded an eight-year plant operations & management services contract, which commenced at the commissioning and start-up of the production units. The management services contract later was extend for an additional three years.
Included in the plant operations & management services contract were:
• Supervision of plant commissioning
• Organizational planning and recruiting
• Administration of marketing, purchasing, accounting and daily business operations
• Plant operations (entire works)
• Annual budgeting
Qatar Steel I Project Challenges
Local conditions in Qatar presented a number of challenges to which KSL responded with the following solutions:
- Equipment had to be capable of withstanding extremely high temperatures, seasonal high humidity, sandstorms and salt pollution
- A closed circuit cooling system using a heat exchanger system instead of a cooling tower system was chosen to minimize the consumption of industrial water. There can be considerable loss of water in a cooling tower system from evaporation and by splashing.
- A desulfurization system was installed to treat the high amount (2,000 ppm) of hydrogen sulfide (H2S) in the crude natural gas supplied to the MIDREX® Plant
- Flicker compensating equipment was installed for operation of the EAF melt shop. The large amount of electricity consumed by the EAF melt shop could cause a major disruption of the electric power supply network in Qatar.
- A centralized maintenance system was established for repairing and maintaining installed systems and equipment, as there were few subcontractors available for such work in Qatar.
- Production equipment was designed to interface easily with automated operation and control systems in order to simplify plant procedures for newly trained operating personnel.
Alexandria National Iron and Steel Company (ANSDK I, II and III)
In second quarter of 1984, KSL signed an equipment and services supply contract with ANDSK for a 716,000 tons/year MIDREX® Plant, the first of three to be supplied by KSL in El Dikheila, Egypt. Today the plants are owned by Ezz Steel and known as EZDK I, II and III.
ANSDK I was supplied by KSL in cooperation with Lurgi GmbH, also a MIDREX® Construction Licensee at the time. The two subsequent plants were supplied by KSL in cooperation with Midrex, and each is rated at 800,000 tons/year.
When ANSDK I began production in 1986, it was the largest single module CDRI plant in the world. Going into its performance guarantee test, ANSDK I was operating at 90 tons/ hour, well in excess of its rated hourly capacity.
Within the first week of operation in November 1996, ANSDK II was operating above its rated daily capacity, and the plant was operating 12 percent above rated monthly capacity in less than a year after start-up.
ANSDK III reached full production after its first five months of operation. During this period, the plant consistently produced DRI with metallization in excess of 94 percent. KSL was awarded a separate contract in 1998 to expand the mineral jetty to facilitate materials handling from the iron ore yard at the jetty to ANSDK III.

Alexandria National Iron and Steel Company (ANSDK I, II and III)
Complejo Siderúrgico de Guayana (COMSIGUA)
A KSL-led consortium signed an agreement with CVG in June 1996 to supply the largest dedicated merchant HBI plant (1 million tons/year). COMSIGUA was the first use of limited recourse project financing in Venezuela.
Groundbreaking occurred in November 1996, and the first HBI was produced in August 1998. The COMSIGUA plant passed its performance guarantee test in October 1998, operating at 112 percent of hourly production rate during the test period, and the first HBI shipment took place the same month.
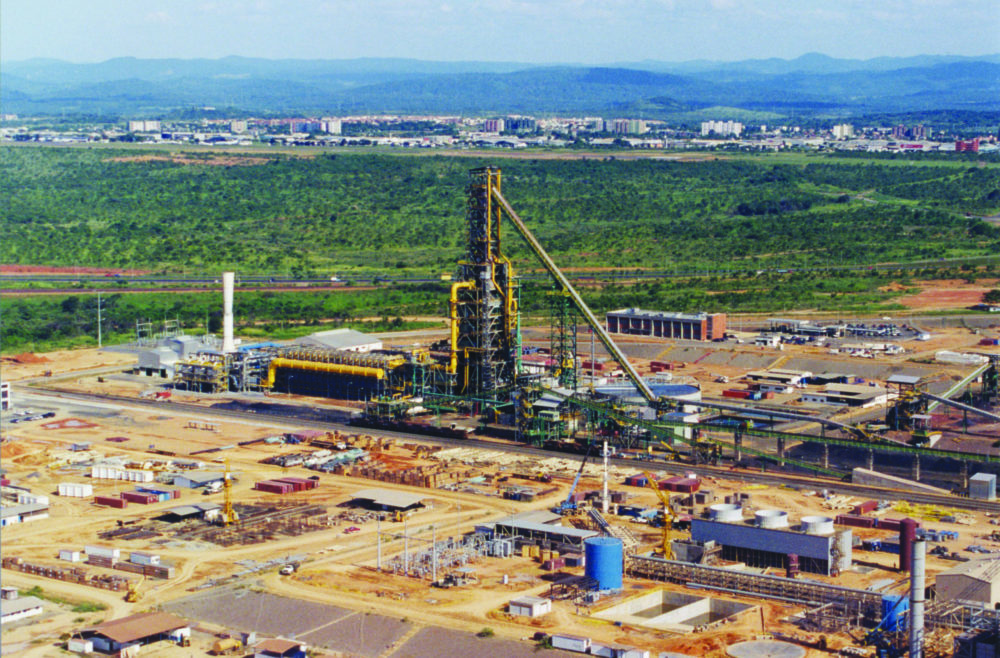
Comsigua
Qatar Steel Company (Module II)
In February 2005, QATAR STEEL contracted KSL to supply a 1.5 million tons/year MIDREX® Combination Plant, the world’s first DR facility designed and constructed to simultaneously produce multiple DRI products. QATAR STEEL II is capable of producing CDRI for use in the new QATAR STEEL EAF melt shop or HBI for merchant sale or storage for future local use.
QATAR STEEL II was started up producing CDRI in July 2007 and added HBI in September 2007. Almost the entire production from QATAR STEEL II in 2014 was CDRI, with metallization averaging 94.6 percent for the year. In its seventh full year of operation, QATAR STEEL II set a new annual production record for the fourth consecutive year. It was operated 19 percent over rated annual capacity and set a new monthly production record of 230 t/h.
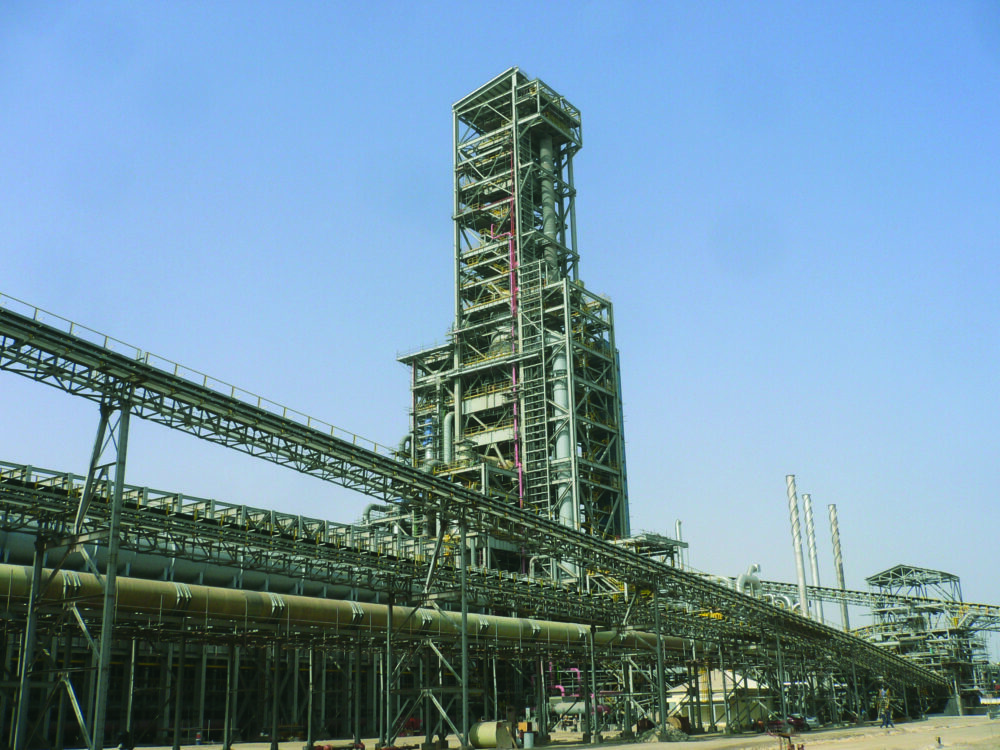
QATAR STEEL
Jindal Shadeed Iron & Steel LLC (Jindal Shadeed)
The first MIDREX® Plant designed for HOTLINK®, direct gravity feed of HDRI to a close-coupled EAF melt shop, was constructed by KSL in Sohar, Oman. Jindal Steel and Power Ltd. (JSPL) acquired the project from Shadeed Iron and Steel Company LLC during construction and renamed it Jindal Shadeed Iron and Steel LLC (Jindal Steel).
By having the 1.5 million tons/year MIDREX® Plant equipped to produce HBI as well as HDRI for direct feeding via HOTLINK®, JSPL was able to make good use of the facility while the EAF melt shop was still under construction. Jindal Shadeed first produced HBI in December 2010, less than four months after its acquisition and four months ahead of schedule. In 2014, the plant transferred HDRI to a nearby steel melt shop in insulated hot transport vessels, as well as operating its HOTLINK® system to directly feed the adjacent Jindal Shadeed melt shop.
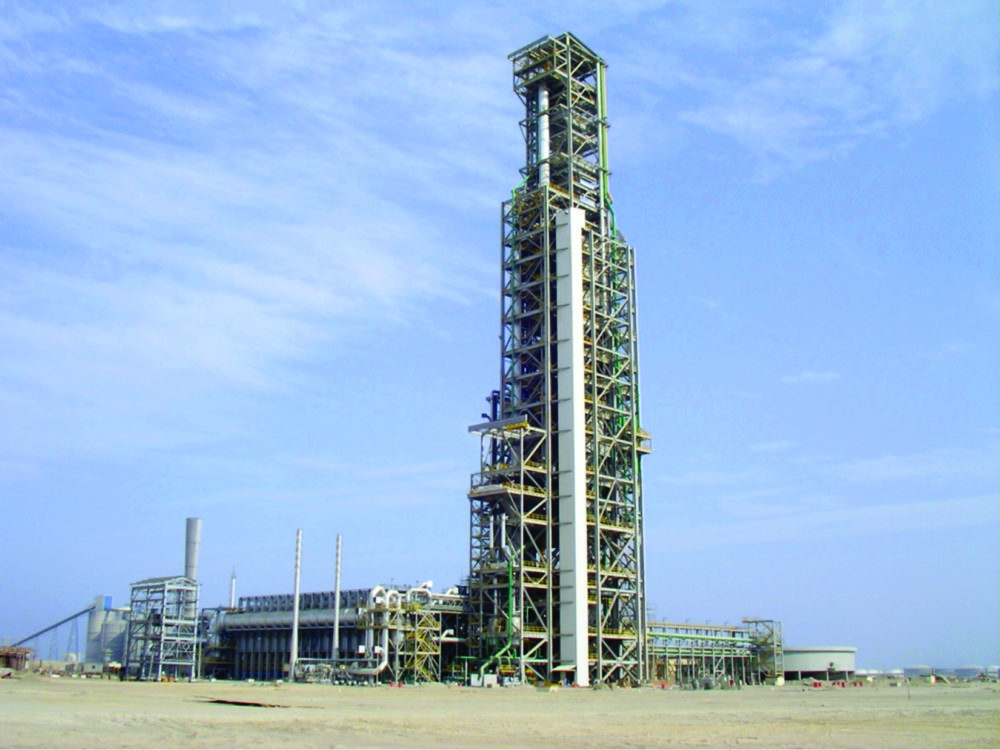
Jindal Shadeed
Bahrain United Steel Company (SULB)
KSL signed a contract in March 2010 for turnkey supply of a 1.5 million tons/year MIDREX® Combination Plant as part of SULB’s integrated steelworks to be located adjacent to a six million tons/year iron ore pelletizing plant also constructed by KSL for Gulf Industrial Investment Co. (E.C.).
Commissioning of the MIDREX® Plant was performed with no significant start-up issues, and the performance guarantee test was passed on the first attempt in only three days. SULB began commercial operation in February 2013, producing only CDRI while awaiting completion and commissioning of the melt shop and rolling mill. HDRI production began in August 2013. CDRI and HDRI metallization and carbon have exceeded the guaranteed values during actual simultaneous operation.
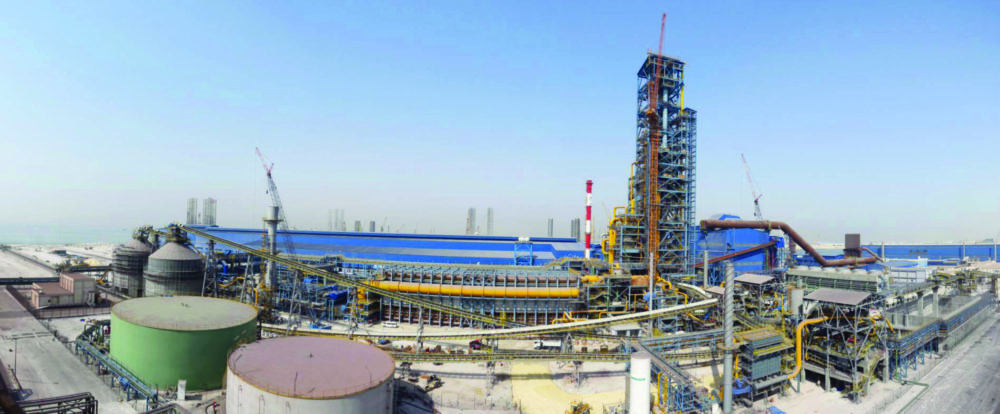
Bahrain United Steel Company (SULB)
KEYS TO KSL PROJECT EXECUTION SUCCESS
The total cycle time of building a MIDREX NG™ or MXCOL® Direct Reduction Plant from excavation to production is a major consideration in the financial sustainability of the project. KSL has developed and closely follows a set of guidelines for executing the engineering, erection, commissioning and start-up of these MIDREX® Plants that has produced a perfect on schedule record.
1.Understanding the technology reduces unknowns and “what ifs”
KSL maintains close communication with Midrex in all phases of the technology, from R&D to project execution. KSL project task force team members have a thorough understanding of the principles of the MIDREX® Process. Iron Unit Division managers and specialists participate in a broad range of categories, such as engineering, procurement, construction, operation, maintenance, QA/QC and logistics. A Risk Management Meeting is conducted during the planning phase of a project in order to minimize the chance of unknown risks. Follow up meetings are held periodically, as well as Monthly Progress Review Meetings.
2. Careful and accurate project planning prior to execution
Over the 40 years KSL has been involved with MIDREX® Direct Reduction Technology, an extensive database of “lessons learned” from previous projects has been assembled and serves as a powerful tool for accurate project planning. Typically, a “lessons learned” meeting is conducted as one of the wrap up activities of a project in order to strengthen the database. Feedback from clients, engineering subcontractors, project contractors and vendors, as well as from Midrex and KSL is essential for continuous improvement of project performance.
3. On-site execution and review during each project phase
Plant capacities have increased significantly in the almost 40 years between QATAR STEEL I and II and dual product combination plants have been introduced, as shown in TABLE I. These advances in direct reduction technology have resulted in significant increases in critical path activities including design engineering, civil works and equipment procurement.
To minimize the risk of critical path delays, KSL works closely with Midrex in all phases of a project. This allows for construction time schedules to be planned and site work to be initiated without waiting for 100 percent completion of design engineering. The ability for Midrex to issue partial drawings based on the KSL site activities schedule is instrumental in meeting the overall project completion date.
Likewise, bulk material procurement such as piping, fittings and valves needs the stepwise preparation of a bill of quantities by Midrex. Preparations to start fabrication and construction work should be done in exact timing with issuance of Midrex documents and drawings.
4. Continual effort to improve project execution
KSL and Midrex are committed to continuous improvement of their project execution capabilities (see Figure 1). As the figure illustrates, each factor depends on and contributes to the success of the process in a closed loop cycle. Well informed project personnel produce more accurate plans and project schedules and a better overall project experience, which increases the “lessons learned”, which are applied to good engineering practice to improve the capabilities of the project team.
5. Stressing teamwork among ourselves and with our clients
Rallying all who have a stake in the success of a project including suppliers, contractors to perform “as a team on the same boat” is a KSL goal on every MIDREX® Plant project. When the project team has a strong, mutual willingness, the plant will be completed on schedule, production will be brought online quicker and profitability is achieved much faster.
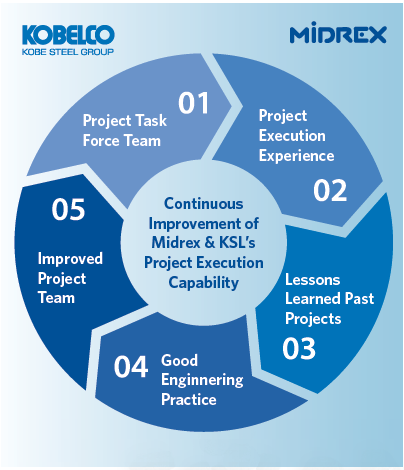
FIGURE 1.
Continuous Improvement Cycle of Project Execution Capability
CONCLUSION
KSL & MIDREX – PARTNERS FOR PROGRESS
More than 40 years ago Kobe Steel identified the importance of direct reduction technology to the future of ironmaking and recognized the potential of MIDREX® Direct Reduction Technology. KSL was already one of Japan’s most highly diversified companies when it acquired the assets of Midrex Corporation in 1983. It was KSL’s first experience owning a foreign company and how it chose to manage its acquisition has proven to be truly visionary.
Together, KSL and Midrex technical and commercial personnel have established MIDREX® Technology as the direct reduction industry standard for quality and performance. The steadfast support of KSL has enabled Midrex to weather steel industry downturns and to emerge with the strength to capitalize on the opportunities that have come with the recoveries.
The mutual commitment of KSL and Midrex to assuring that the products are available to meet the requirements of the global steel industry is evident in the close cooperation with operators of MIDREX® Plants, collaboration with proprietary vendors and related technology suppliers and the ongoing expansion of R&D capabilities – people and facilities.