Midrex Water Treatment Management for Increasing Plant Availability & Productivity
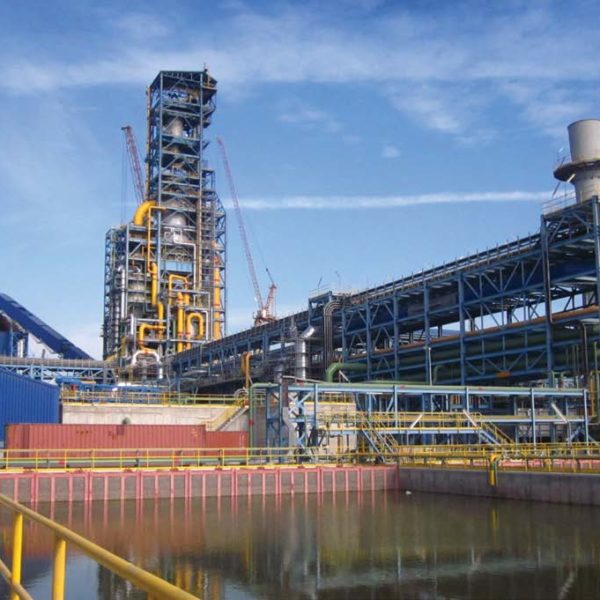
The emergence of DRI production technology over the last 50 years has revolutionized the steel industry by providing a more environmentally-compatible method of iron production. DRI provides electric arc furnace (EAF) operators the means to compete at the highest steel quality levels and blast furnace operators the ability to optimize their hot metal production and reduce emissions.
From humble beginnings in Portland, Oregon, USA, in 1969, where the two modules that comprised the first MIDREX® Plant were each rated at 150,000 tons per year (t/y), Midrex has been at the forefront of the direct reduction industry both technically and commercially. Today, the world’s largest single module DRI plant is in operation near Oran, Algeria, at the Tosyali Algeria steelworks. This MIDREX Plant is rated at 2.5 million t/y and is capable of producing hot and cold DRI (HDRI and CDRI, respectively) to meet the requirements of the steel plant’s EAF melt shop. When HDRI is sent to the melt shop, the EAF electrical and electrode consumption will be lower and tap-to-tap times will be reduced, as compared to using a 100% scrap mix. A similar MIDREX Plant soon will be commissioned at Algerian Qatari Steel in Jijel, Algeria.
In 2018, as in every previous year since 1987, plants based on MIDREX Technology produced more than 60% of the world’s DRI supply, and the cumulative total of DRI production since 1969 eclipsed 1 billion tons. MIDREX Plants consistently have the industry’s highest average number of annual operating hours and best average plant availability percentage.
Midrex Technologies, in collaboration with its construction partners and process licensees, has made significant strides in advancing DRI process technology and overall plant reliability. Major engineering initiatives have improved equipment performance and reliability, resulting in plants operating at near- optimal rates. Plants are able to run longer campaigns between maintenance shutdowns and major repairs. Today, plants typically operate 8-14 months between major shutdowns.
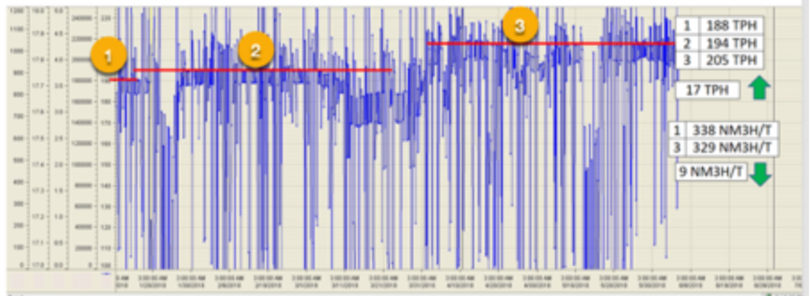
FIGURE 1.
Example of RPS data
TECHNOLOGY AND SERVICES
Midrex has developed an Integrated Plant Solution (IPS) for water treatment management, specifically aimed at enhancing plant availability and productivity. It combines several programs that together address the following industry imperatives:
- Create additional production opportunities
- Reduce maintenance & operating costs
- Protect critical equipment & components
- Deliver quality production
IPS ties the operational decision-making with water treatment and maintenance, providing a holistic approach to solutions. A critical component of this integrated solution is Remote Professional Services (RPS). RPS allows Midrex operations experts to remotely view the plant DCS in a read-only environment. Operational data is observed from the Charlotte control room and analyzed using the extensive technical expertise of Midrex, supported by proprietary software to troubleshoot specific problems and enhance the production process. Based on the findings, Midrex will recommend solutions and operational adjustments to a plant’s operations team. These suggestions, backed by actual plant data and sound technical reasoning, can be further discussed and implemented by the plant with Midrex assistance, if deemed appropriate. Utilizing this second “layer” of experience has proven to have significant, real time advantages to the plant’s production and operating parameters. It also has the advantage of utilizing all of the Midrex in-house disciplines including proprietary software. Figure 1 follows the production and natural gas enhancement at one client over a 6-month time period. During this period, plant operators and management worked with Midrex’s RPS team to make incremental changes, which resulted in significant enhancements.
THE ANATOMY OF A WATER SYSTEM-RELATED SHUTDOWN
With all the advancement in DRI process technology through the years, one area that has changed little is the treatment of the water circuits. However, enhanced water treatment can have a significant impact on increasing production availability, reducing operating costs, and protecting critical component assets. So, it comes as no surprise that one of the primary tasks during a shutdown is to remediate problems associated with the water system. In 2018, Midrex performed a survey and found that nearly 30% of “annual” outages were attributable to remediation of water-related problems, such as scale removal, sludge removal, packing removal, cleaning and replacement, and numerous other related issues (Figure 2). The amount of time and man-power required to fix these problems are “hidden” costs to an operating plant. They are budgeted and incurred regularly, so few questions are raised about fixing the problems, as they are considered a “cost of operation.” Midrex’s strategic partner, Chemtreat, initiated a study with the gas stripper at the voestalpine Texas HBI plant to determine if improvements to clarifier performance could be achieved against industry norms. The plant originally had the gas sripper installed for safety reasons (to remove CO) but the functionality of the equipment is uniquely suited for enhancing water treatment since CO2 is also removed.
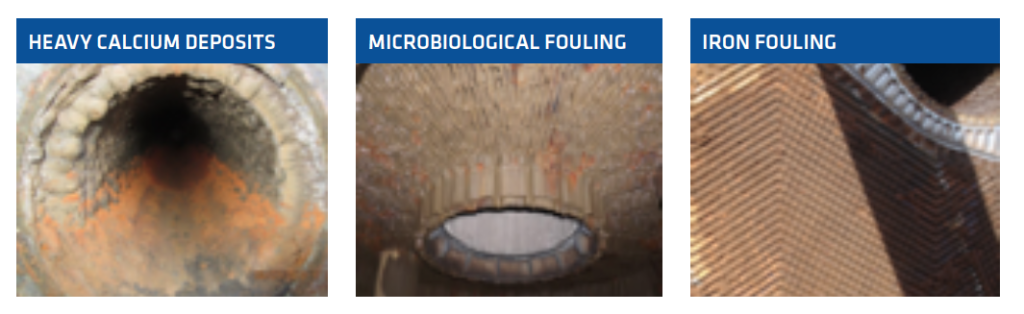
FIGURE 2. Typical problems found in DRI plant water system
To understand the importance of CO2 in the water, the Pour-baix Diagram is included as Figure 3. Essentially there are both soluble iron (Fe2) and insoluble iron (Fe3) species in any given process recirculating in the water (PCW) circuit. Depending on conditions, a significant amount of iron could be in the soluble state. These conditions are defined by the Pourbaix Diagram.
The diagram shows the relationship between oxidation- reduction potential and pH. In a PCW circuit that does not have a CO2 stripper, the pH of the water circuit is generally < 8, which favors a higher level of soluble iron (Fe2) recirculating and being carried over the weir. With a CO2 stripper present prior to the clarifier, the pH of the recirculating water is elevated and a significant level of soluble iron – perhaps greater than 50% – becomes insoluble and therefore, precipitates out within the clarifier.
This phenomenon has a dramatic effect on clarifier performance because more iron is capable of removal – where it is designed to be removed – within the clarifier. Without the CO2 stripper, soluble iron leaves the clarifier and as the CO2 naturally evolves, the iron converts to insoluble iron throughout the return water circuit, generating deposition. Specifically, the advantages of this design change include:
- Improved iron removal at the clarifier, and potential additional iron credits at the pelletizing or fines collection plant
- Reduced fouling in the hot and cold wells of the cooling tower
- Reduced tower fill fouling
- Reduced pipework fouling and packing fouling going to and into the top gas scrubber
- Reduced localized corrosion in the return loop due to reduced carbonic acid (HCO3) formation
- Reduced erosional effects of excessive iron oxide abrasion as the water recirculates
- Reduced potential for iron induced micro-bio corrosion
- Improved blowdown water clarity and improved environmental compliance
Additionally, the removal of CO2 reduces the potential for calcium carbonate scaling because the calcium hydroxide (lime coating source) reaction with CO2 will not occur, as shown below:
CaO(s) + H2O(l) ->Ca(OH)2(s)
Ca(OH)2(s) + CO2(g) -> CaCO3(s) + H

FIGURE 3.
Pourbaix diagram
RESULTS-BASED SOLUTION
With the introduction of this equipment, separate “clean water” and “dirty water” systems, and the strategic placement of chemical injection points, Midrex and Chemtreat significantly altered water treatment strategies to prove how much better the system could function. During the initial campaign, total suspended solids (Figure 4) were much lower than any plant for which Midrex has data. Treatment products and dosages were altered to determine the best result.
Other key indicators (water flows and operational pressures) to key components, such as top gas scrubber, reform gas cooler, and temperatures remained stable indicating that typical fouling was not occurring.
After nearly two years of uninterrupted operation, the plant decided to have a shutdown and inspect the component and the water system. The results were exceptional. Packing and nozzles in the top gas scrubber (“dirty water” system) was free from deposition. The seal gas cooler and reformed gas cooler, supported by the “clean water” circuit, also were free of build-up (Figure 5).
Findings after 22 months of continuous operation were the best results ever recorded for a water system, according to Midrex experience. Plant personnel and Midrex engineers agreed that the system could have run another 1-2 years without experiencing water quality issues. Midrex has used these findings in discussing how to best optimize future and existing plants to realize:
- Maximum plant availability, thereby extending tph production
- Reduced maintenance costs
- Asset protection
- Quality optimization
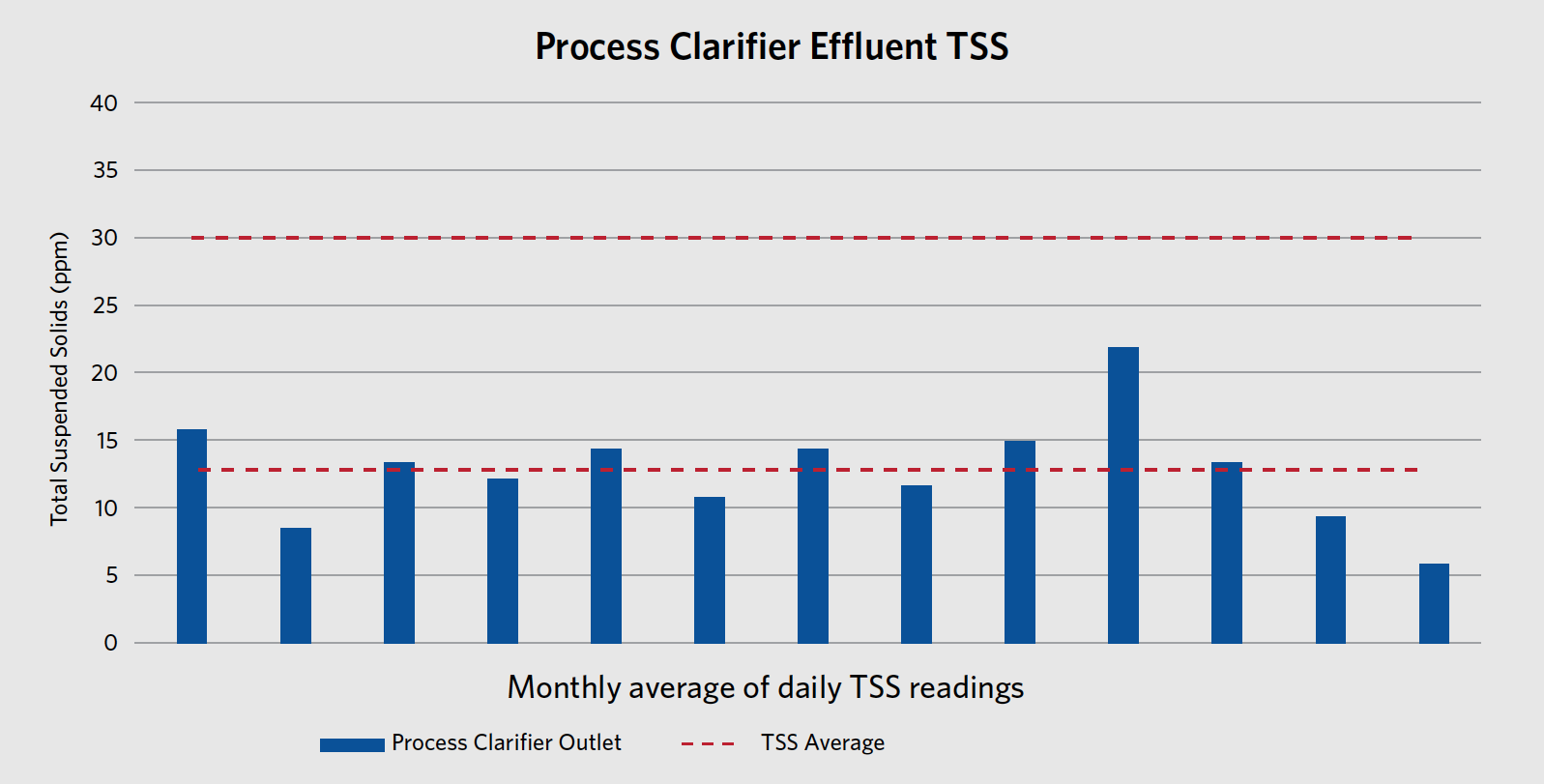
FIGURE 4.
12-month TSS average
SUMMARY
The Integrated Plant Solution (IPS) for water treatment management combines the following:
- Best-in-class water treatment strategies – selecting the right chemicals, dosed at the right location and at the right levels to achieve the needed results for the plant.
- Engineered solutions – to provide the CO2 stripper and other associated equipment and separate water systems, if required.
- Remote Professional Services (RPS) powered by MidrexConnect™ – focused on plant optimization. This utilizes various Midrex proprietary software and experience to optimize plant operation and troubleshoot issues. This is achieved by viewing real-time, read-only screens of the plant DCS in the Midrex headquarters control room. The operators can identify where process variables and water issues can impact the entire plant. Findings are communicated to the plant operations team.
- Technical field support – Midrex embeds service employees at the local plant to ensure results are achieved.
Since the development of the IPS program, Midrex engineers have been working with an earlier generation module to design, built, construct, and deploy a new CO2 stripper to help optimize the plant. Chemical dosing equipment was upgraded and chemical feed was optimized. Treatment strategies were aligned to ensure Midrex/Client objectives are met post commissioning. The timeline for implementation was August- September 2019. Additionally, the RPS team will soon implement this service to enhance support.
Midrex’s expectation is that collectively IPS will enable the DRI manufacturer to extend campaign life and optimize productivity shutdown-to-shutdown. IPS will ensure that the desired production parameters are better controlled, so day-to-day operations are not impeded by water or process-related issues. As a team, Midrex and a plant’s operations personnel, can work together to significantly improve existing plant operation using the strengths of Midrex’s engineering, IT resources, and water services team in a comprehensive program.
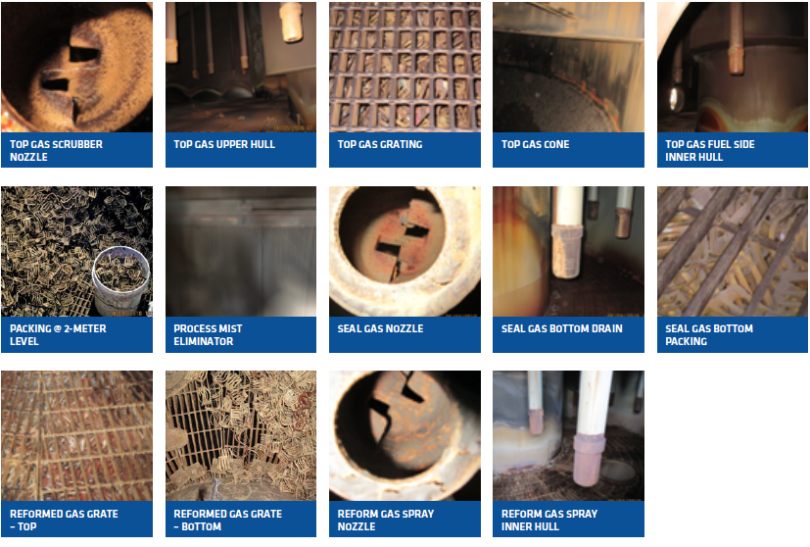
FIGURE 5.
After 22 months of continuous operation