MIDREX® Combination Plant – Designed for Changing Market Conditions
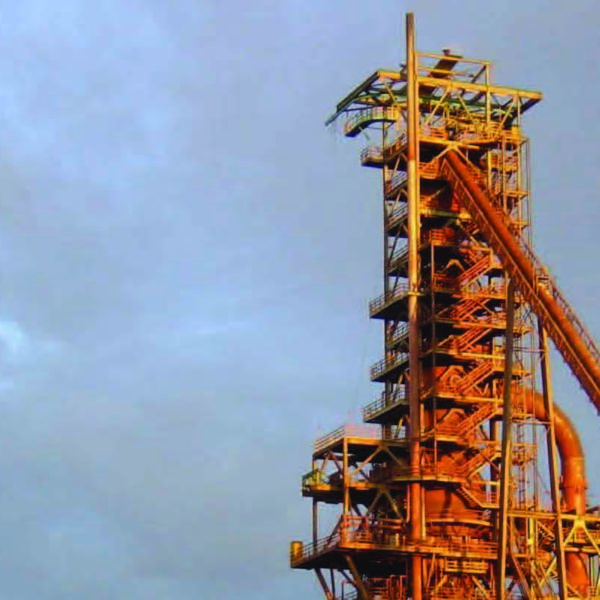
Opportunity is often the mother of invention. The decision in the early 1980s to amend the Sabah Gas Industries (SGI) plant supply contract to produce hot briquetted iron (HBI) is a good example.
Leading up to the SGI project (Editor’s note: plant now owned and operated by Antara Steel Mills, a Lion Group company), Midrex had the idea of designing a reduction furnace to discharge hot DRI (HDRI). Several development programs were conducted in parallel by Midrex and its licensees. The result was a marriage of the proven MIDREX® Shaft Furnace design with technical innovations that allowed for uniform discharge of HDRI and assured consistent gas and product flow characteristics.
The MIDREX® Hot Discharge Furnace has proven to be a keystone technological development. This innovative design has since gone on to be at the heart of a direct reduction plant that gives operators the ability to respond quickly and effectively to changing market conditions – the MIDREX® Combination Plant.
WHAT IS A MIDREX® COMBINATION PLANT?
As the name implies, a MIDREX® Combination Plant is capable of simultaneously discharging hot DRI (HDRI) and cold DRI (CDRI). HDRI then can be transported in insulated vessels or enclosed conveyors to a nearby electric arc furnace (EAF), discharged directly into a close-coupled EAF, or compacted into HBI and sold as a merchant product. CDRI can be reclaimed from storage silos or covered piles and either batch charged or continuously charged along with scrap into a nearby EAF.
As part of an integrated DR/EAF steel mill, the MIDREX® Combination Plant can continue to produce and discharge DRI during periods when the EAF is down for maintenance or in response to changing market conditions. Conversely, the EAF can utilize stored CDRI or HBI to maintain production while the MIDREX® Plant is undergoing routine maintenance.
A merchant HBI plant equipped with an external product cooler can continue to produce CDRI when the plant’s briquetting machines are shut down for maintenance. A typical DRI plant that makes CDRI or HDRI is rated at 8000 hours per year and an HBI Plant is rated at 7800 hour of year because of additional preventive maintenance required. A combo plant allows a traditional HBI plant to produce additional product during this maintenance downtime.
Simply stated, a Combination Plant is a MIDREX® Direct Reduction Plant, either natural-gas based (MIDREX® NG configuration) or coal-based (MXCOL® configuration), equipped with a hot discharge furnace and an external product cooler. HDRI is discharged into either the product cooler, which is designed similar to the cooling zone in a CDRI furnace, or into a bottom seal leg/product discharge chamber (PDC) system. The most important innovations embodied in a MIDREX® Combination Plant are the way in which the furnace is barometrically sealed while discharging HDRI and how uniform material flow is maintained. Two proprietary equipment designs play key roles: the bottom seal leg and the PDC, which have been integral components of the MIDREX® Hot Discharge Furnace since its introduction in the HBI plant for SGI.
KEYS TO HOW A MIDREX® COMBINATION PLANT WORKS
The MIDREX® Reduction Furnace operates at a relatively low pressure (≤ 1 barg), which simplifies the design of the charging and discharging systems. Two dynamic seals accomplish the same task that would require as many as 50 mechanical valves and five lock hoppers if the furnace were designed to operate at a pressure of 5-6 barg. This takes on added importance when designing a hot discharge furnace to simultaneously discharge HDRI and CDRI on a continuous basis.
The lower pressure operation of the MIDREX® Reduction Furnace combined with the bottom seal leg/PDC system make it possible for a MIDREX® Combination Plant to achieve true simultaneous discharge of CDRI and HDRI while maintaining consistent chemistry throughout the material bed and uniform material flow in the furnace.
Bottom Seal Leg
The lower cone of the reduction furnace feeds into a bottom seal leg, which functions as a dynamic seal for the furnace discharge just as the upper seal leg does for furnace charging. The dynamic seal concept allows the down-flowing material to provide the majority of the seal while using seal gas to fill in any voids between the materials and establish an inert purge.
The function of the bottom seal leg is to contain the pressurized process gases within the reduction furnace and thus maintain the integrity of the closed loop of process gases at the lower end of the furnace. By sealing the reduction furnace, process gases are prevented from escaping from the furnace while air or oxygen is prevented from entering the furnace, thus preventing oxidation of the metallized material.
Because of the lower pressure drop associated with this restriction and the dynamic seal concept, the quantity of seal gas required is relatively small, while the movement of the metallized material is maintained as a smooth continuum, unobstructed by mechanical closures or sealing mechanisms. The bottom seal leg terminates at the wiper bar inside the Product Discharge Chamber (PDC).
Product Discharge Chamber (PDC)
The PDC includes all equipment from the point where product is discharged from the bottom seal leg to the point where metallized product is delivered to briquetting machines or to a hot transport vessel, hot transport conveyor, or in the case of HOTLINK®, directly into an EAF. This portion of the discharge system is responsible for discharging product from the furnace, screening and sizing the product, and feeding it to the designated destination. (Note: The product cooler has its own cold seal leg into which it discharges. There is no seal leg between the furnace discharge and the product cooler.)
The PDC consists of a wiper bar, screen sizers, and tramp doors. The wiper bar is a variable speed, positive displacement feeder that moves the metallized product into the screen sizers. Any material exceeding 50mm X 50mm is directed by the screen sizers to each side of the PDC, where it is discharged through tramp doors into containers.
JSP Angul
Qatar Steel 2
Hadeed Module E
LION DRI
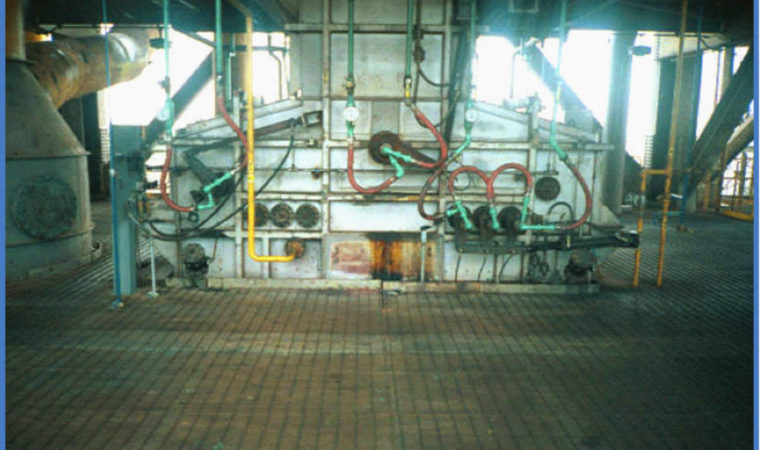
The PDC is designed to:
1) Discharge HDRI from the reduction furnace at
a consistent rate
2) Maintain constant feed to briquetting machines or to an EAF meltshop
3) Screen out any large pieces that could damage down stream equipment or cause the screw feeder to jam
4) Break up any soft material clusters
5) Capture and remove tramp material from the furnace discharge
6) Provide an outlet for seal gas from the bottom seal leg
7) Provide product surge into feed leg(s) when the feed leg(s) slide gate is opened
COLD, HOT OR SOME OF BOTH
The operator of a Combination Plant has available a variety of product options: CDRI, HDRI, HBI, or simultaneous production of CDRI/HDRI, CDRI/HBI, or HDRI/HBI.
Cold DRI (CDRI)
Traditionally, DRI is cooled to about 50° C prior to discharge. CDRI is used primarily in a nearby melt shop and has excellent flow characteristics for continuous charging to the EAF.
CDRI is carburized and cooled in the product cooler by counter-flowing cooling gas. A centrally located cooling injection device serves two important purposes: 1) it distributes cooling gas uniformly throughout the burden, and 2) it prevents the material in the center of the cooler from descending at a faster rate than material along the periphery of the cooler. This is extremely important for producing CDRI at a uniform temperature and with consistent chemistry.
Hot DRI (HDRI)
During the reduction of iron oxide, the furnace burden reaches temperatures of 800-900° C. HDRI can be transported to a nearby EAF at a temperature of greater than 600° C in order to take advantage of the sensible heat. Electricity consumption can be reduced by about 20 kWh/t liquid steel for each 100° C increase in DRI charging temperature. Therefore, energy savings alone can be 120 kWh/t or more when charging HDRI.
Charging DRI at 600° C reduces tap-to-tap time, allowing a productivity increase of up to 20 percent versus charging DRI at ambient temperature. Use of HDRI can increase liquid steel production by 20 percent, resulting in $10/t savings in operating cost.
Figure 1 shows relative steel mill profitability versus profit margin per ton of steel, for a range of margins. Over this range, the increased profit by the use of HDRI is $43-70 million per year.
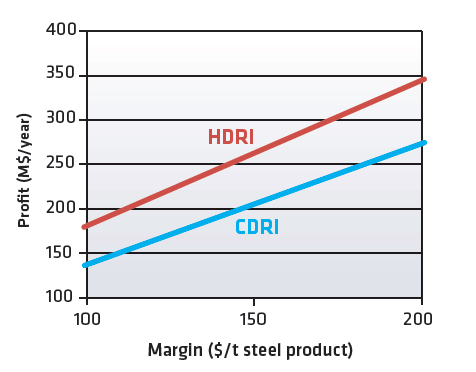
FIGURE 1. Relative Steel Mill Profitability vs. Profit Margin for CDRI and HDRI
Midrex offers three methods for transporting HDRI: hot transport vessels (HTV), hot transport conveyor (HTC) and HOTLINK®. Insulated HTVs are appropriate when the distance between the DRI plant and the melt shop is greater than 200 meters, while specially designed HTCs are effective for distances up to 200 meters and can be used to service multiple EAFs, if needed. HOTLINK® is designed to feed a close-coupled EAF by gravity flow; therefore, the distance is typically 40 meters or less. With multiple options for transporting HDRI, there is no limitation on the location of a MIDREX® Hot Discharge Plant within the overall layout of the steel mill.
Hot Briquetted Iron (HBI) H
BI is made by compressing HDRI into pillow-shaped briquettes having a typical size of 30 x 50 x 110 mm and a density ≥ 5 gm/cc. No binder is needed to make HBI. HBI is the preferred DRI product for the merchant metallics market because it is much denser than CDRI. This enables HBI to be stored and transported without special precautions and provides operational benefits in the EAF. Its enhanced physical characteristics make HBI highly effective when used in the blast furnace (BF) to increase productivity and in the basic oxygen furnace (BOF) either in the primary charge or as a trim coolant.
COMBINATION PLANTS IN ACTION
The combination plant design is the result of continually evolving MIDREX® Direct Reduction Technology. It gives plant owners the confidence that their investment is secure by providing plant operators the ability to respond quickly and easily to various operational and market changes.
For example, Midrex started up a 1.5 Mt/y MIDREX® Combination Plant in 2007, for Qatar Steel Company. Qatar Steel II, as the plant is known, primarily feeds CDRI to a new EAF meltshop. The MIDREX® Plant is designed for simultaneous discharge of CDRI and HDRI, which is compacted to make HBI. In 2013, Qatar Steel II produced more than 1.6 Mt of CDRI and HBI and almost 1.8 Mt in 2014. The flexibility to quickly and efficiently change between CDRI and HBI allowed Qatar Steel to respond to changes in the market for its primary product, billets, by selling HBI to other steel mills in the Middle East and North Africa (MENA) region.
Midrex designed a 1.5 Mt/year HOTLINK® Plant (1.1 Mt HDRI, 0.4 Mt HBI) for Shadeed Iron & Steel LLC, located in Sohar, Oman, as part of an integrated DR/EAF steel mill. Four months prior to start-up of the MIDREX® Plant in 2010, Jindal Steel and Power Limited (JSPL) acquired the plant and renamed it Jindal Shadeed. The change of ownership delayed completion of the steel mill. However, because the MIDREX® Plant was capable of producing HBI as well as HDRI, Jindal Shadeed has been operated as a merchant HBI facility since start-up. In 2014, the plant produced almost 1.5 Mt of HBI and operated at 98.5 percent availability. Midrex and its Construction Licensees have supplied 13 combination plants since 1990: six producing HDRI/CDRI, five producing HDRI/HBI, and one each producing HDRI/CDRI and CDRI/HBI. This represents more than 17.5 million metric tons (Mt) of installed capacity. These plants were designed for dual product discharge. However, existing MIDREX® HBI Plants equipped with a hot discharge reduction furnace can be retrofitted for dual discharge if a steel melt shop is added at a later date (See TABLE I).
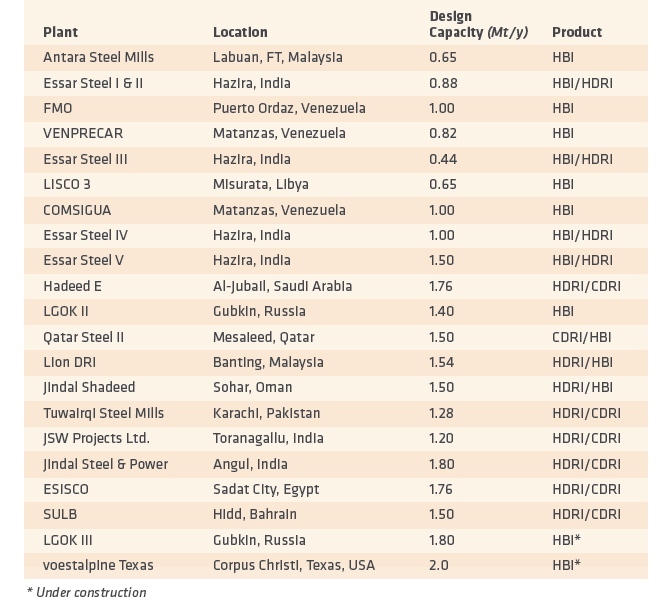
TABLE I. Plants Equipped with Hot Discharge MIDREX® Reduction Furnaces
MAKING INNOVATION COUNT
Technology is defined as the practical application of knowledge, which makes an innovative technology a new, advanced application of knowledge in a practical way. The MIDREX® Combination Plant is the embodiment of the cascading effect of innovative technology, from originally adapting an iron oxide pelletizing furnace for continuous production of DRI to modifying the resulting reduction furnace for discharging HDRI to adding the flexibility of simultaneous dual discharge of CDRI and HDRI.
The MIDREX® Combination Plant gives owners options. When part of a steel mill complex or when located in the vicinity of a steel mill, HDRI can be transported by insulated conveyor or containers and charged hot into one or several EAFs. If equipped with briquetting machines, the same plant can produce HBI to sell as an additional commercial product. An external product cooler allows for the production of CDRI when the steel mill does not require HDRI or when the hot briquetting machines are undergoing maintenance.
With change being the only sure thing in the global steel market, it makes sense to prepare for it. The MIDREX® Combination Plant not only provides owners a quick and effective response to sudden changes in market conditions but also gives them the opportunity to take advantage of those changes.