Impact of HBI Use in Integrated Steel Plants: Environmental Impact and OPEX Comparison
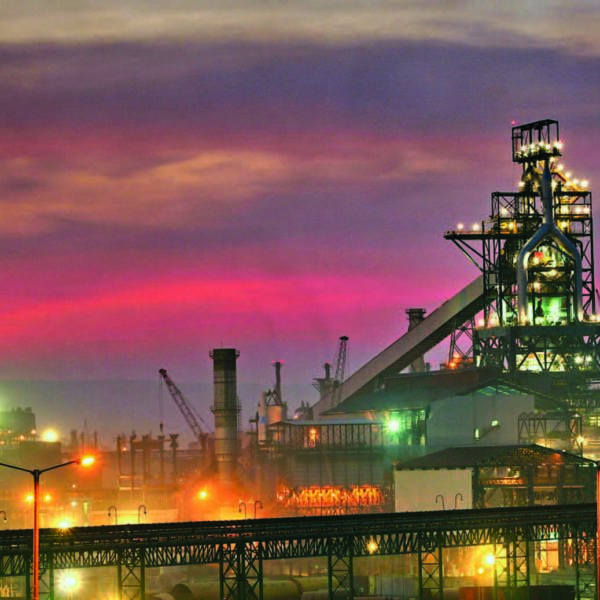
EDITOR’S NOTE:
As economic and environmental pressures continue to increase for the traditional BF/BOF route of steel production, many steelmakers are faced with the challenge of lowering emissions while simultaneously maintaining production. Sustainability is ultimately the key issue for every steelmaker going into the future, but how to achieve this goal in light of new challenges is the question at hand.
Shale gas exploration has led to low cost natural gas in North America and other areas of the world, creating interest in new direct reduced iron (DRI) facilities and DRI product including hot briquetted iron (HBI), which were once viewed by integrated steelmakers as an electric arc furnace (EAF)-specific charge material, may actually present a long term, scalable solution that is achievable for steelmakers going forward. HBI usage as charge material especially in the blast furnace (BF) is now seen as a powerful way to help displace CO2 emissions and increase hot metal production of the facility. This is no longer a hypothetical scenario, as the first DRI Plant built to specifically supply HBI to BFs is operating near Corpus Christi, Texas, USA.
INTRODUCTION
A major challenge for all industries worldwide is how to comply with more stringent environmental emissions standards. This will be essential for sustainability. The general consensus is that emissions restrictions will get tighter for all industries globally and this will severely affect the ability of many integrated steelmakers going forward. Carbon dioxide (CO2) has become the symbol for the plight of society against industry over the greenhouse gas (GHG) effect. Although not the most powerful GHG, CO2 is the most abundant one and the one that is capturing the most attention.
Total production of CO2 by human activities is around 35 billion tons per year. Iron and steelmaking accounts for almost 7% of mankind’s entire carbon footprint [1]. Ironmaking alone constitutes 80-85% of iron and steel’s total CO2 output. Integrated mills are the largest contributor of CO2 by both volume and percentage, with coke-fueled blast furnaces currently producing well over 90% of the world’s iron.
Based on the world steel industry’s coal consumption, it is estimated that blast furnace ironmaking (including the processing step to make coke from metallurgical coal) generates approximately 1.8 tons of CO2 for every ton of iron produced. As no proven carbon capture system exists for blast furnaces, the best way for integrated steelmakers to reduce CO2 emissions is simply by not creating the emissions in the first place.
Shuttering a certain percentage of BF capacity will no doubt be necessary in the next few decades, but economics will prevent simply replacing blast furnace-basic oxygen furnace works with direct reduction-electric arc furnace mills. Some DR/EAF capacity is and will continue to replace older, inefficient BF/BOF capacity, but it is not a feasible solution for the industry as a whole.
A practical way to keep blast furnaces operating is needed. The solution could still involve the benefits of direct reduction ironmaking but from an operational standpoint rather than as an outright replacement of BF capacity.
This article will explore possible combinations and integrations of iron and steelmaking routes within an integrated steel mill by using direct reduced iron (DRI) in its physically enhanced form, hot briquetted iron (HBI), and show the environmental benefits, as well as the related OPEX implications. Various plant configurations will be schematically presented with quantified examples and the main process gas and energy balances.
USE OF HBI/DRI IN INTEGRATED STEEL PLANTS
For most of its history, DRI has been essentially one product form. However, after decades of development and use, DRI is now better defined as three specific products with different uses within the iron and steel industry, as depicted in Figure 1. These are: Cold DRI pellet and lump (CDRI), which is cooled before handling and used mostly in the EAF and BOF; Hot DRI (HDRI), pellet and lump specifically developed for the EAF, is discharged from the shaft furnace without cooling and charged into a melter; and Hot Briquetted Iron (HBI), which is DRI discharged from the shaft furnace at ≥ 650° C and compacted to a density ≥ 5gm/cc, is suitable for all applications including Blast Furnace (BF). Figure 2 shows the chemical and physical characteristics of HBI.
The chemistry of HBI depends largely on the chemistry of the iron oxide feedstock. Carbon level can be adjusted by the operating parameters of the direct reduction process. The result is a high iron content, low residual charge material for iron and steel production. The compacted form also allows for longer term storage without risk of severe re-oxidation.
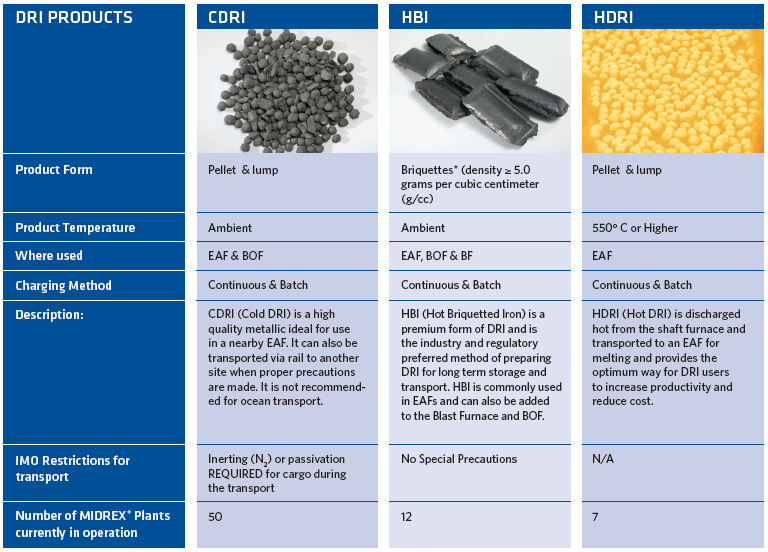
FIGURE 1.
Forms of direct reduced iron (DRI) *The MIDREX® Process requires less oxide coatings than competing DR technologies, which allows for easier briquetting of DRI and stronger physical HBI characteristics
USE OF HBI IN THE BLAST FURNACE (BF)
The addition of metallic iron in the blast furnace (BF) is not a new idea. Even using DRI as the metallic charge has been discussed and written about for decades. However, with economic and environmental pressure mounting on integrated steelmakers, the rhetoric is now turning into action. BF operators are realizing that the flexibility afforded them by using HBI, the physically-enhanced form of DRI, can translate into increased productivity, greater operational control and reduced emissions, all of which contribute to the sustainability of their plants.
The size and shape of HBI is comparable to standard blast furnace burden materials and can be charged using the existing blast furnace stock house and charging systems. Therefore, it is easier to charge than scrap, and HBI will not cause the sticking or hanging problems sometimes encountered with scrap. Also, scrap must be carefully selected to ensure that the hot metal is not contaminated with unwanted elements, such as copper and other residual metals and that it is suitably sized for blast furnace charging.
Since the iron in HBI is already metallic when charged to the BF, hot metal production is greatly increased (8% for each 10% of metallization of the BF burden) and coke savings are similarly impressive (7% for each 10% of metallization of the BF burden), as shown in Figure 3. In addition, CO2 emissions are reduced due to lower coke consumption.
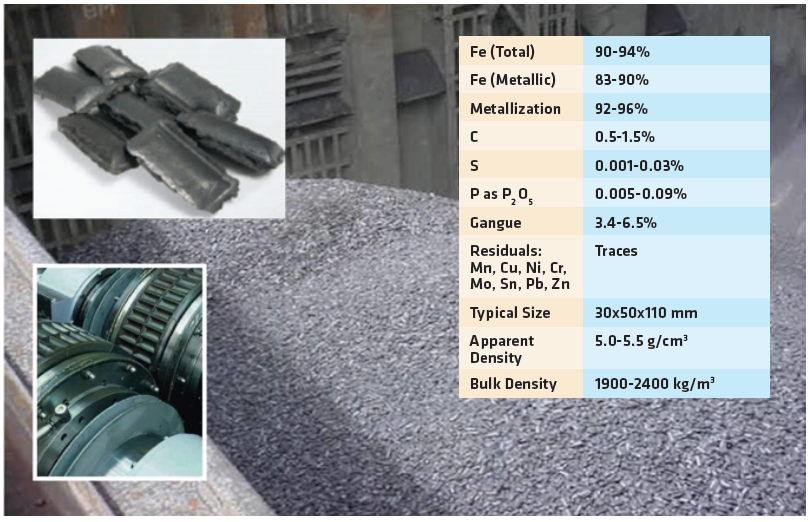
FIGURE 2.
Chemical and physical characteristics of HBI
HBI has been used as part of the regular, routine operation of a commercial blast furnace in North America for over 25 years, as well as in other blast furnaces around the world. It has been shown that charging 30% HBI yields approximately a 24% increase in production of hot metal. HBI is the preferred form of DRI for use in the BF because CDRI does not have the mechanical properties needed to resist the over burden pressure in a large modern blast furnace and tends to react with the off-gas in the top of the furnace. The high density of HBI makes it much less reactive. HBI also has proven to be a useful alternative to scrap in the BOF.
Blast furnace burden enrichment using HBI can be economically attractive under various conditions. Five of the most likely are:
- Hot metal availability is insufficient to meet orders for finished product and additional downstream capacity is available.
- An imbalance exists between scheduled shipped steel tonnage and the number of blast furnaces; therefore, the plant operates two or three blast furnaces when the hot metal output of one- and-a-half or two-and-a-half furnaces is really required.
- One blast furnace is offline for repair or rebuild and the remaining blast furnace or furnaces must maximize hot metal output to make up the deficit.
- At some locations, it also could be possible to shutter aging coke batteries and related equipment, such as for coal processing and handling and coke oven gas processing.
- The costs of operating an older, smaller furnace can be eliminated by increasing the capacity of a newer, larger one.
In each of these cases, the use of HBI to enhance hot metal production is frequently more attractive than other alternatives, such as purchasing premium scrap or slabs for the metallic charge or being unable to produce the amount of steel when the market demands it.
EXPERIENCE USING HBI AT AK STEEL
Since the 1980s, AK Steel has added HBI to the charge mix of the blast furnace in Middletown, OH. For several years, AK Steel typically charged 30% of the burden as metal, primarily HBI from Venezuela, together with some steel scrap. Furnace productivity averaged over four tons per day per cubic meter of working volume, among the best in the world. Also, total fuel consumption was remarkably lowered to about 440 kg per metric ton of hot metal.
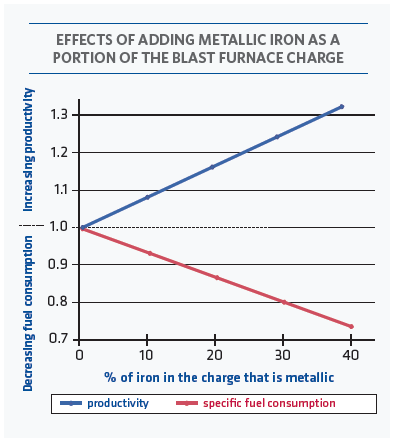
FIGURE 3.
Effects of adding metallic iron to the BF charge
The benefit this provided AK Steel was primarily an increase in productivity. With the blast furnace as the limiting operation of the entire steel works at Middletown, additional tonnage from the blast furnace meant more tons of salable product.
Prior to using HBI to increase the productivity of the Middletown blast furnace, AK Steel operated another blast furnace about 30 miles away in Hamilton, Ohio, which was used to supplement hot metal output of the Middletown furnace. This was necessary to keep the steel shop running at the desired rate. Once the Middletown furnace raised its production rate by charging HBI, the Hamilton furnace could be closed. Tom Graham, then president of AK Steel, stated at the World Steel Dynamics 1994 Steel Survival Strategies conference that the closure of the Hamilton blast furnace saved AK $60 million dollars per year in fixed costs. Those were 1994 dollars; today the equivalent figure would be over $100 million.
SOURCING HBI FOR BF USE
If we accept that the most effective, currently available means of lowering the amount of CO2 generated by the steel industry is to use HBI produced by a natural gas-based direct reduction plant in the blast furnace, the important question is how does a plant source HBI?
HBI can be sourced two ways by an integrated steel mill:
1) buy HBI from a dedicated merchant HBI plant or from a DRI plant with the capability to produce HBI; 2) build a natural gas-based DRI plant with HBI capabilities either onsite or near operations or off-shore where there are sufficient supplies of reasonably priced natural gas. In the case of on-site installation of new DRI plant, possible synergies by the utilization of steelmaking gasses can be also exploited, as described hereafter.
For most BF producers, merchant HBI plants are the most obvious sources of supply. Merchant HBI allows those who do not wish to own and operate their own plant to purchase material in the open market. To date, blast furnace operators have chosen to obtain HBI in this manner. HBI plants dedicated to merchant supply exist in Venezuela, Libya, Russia and Malaysia. Except for Russian HBI supply, in recent years political and financial issues have limited the activities of several of these HBI suppliers.
Although DRI plants equipped with briquetters have the capability of producing HBI, their first priority is to supply HDRI to their own steel operations. Therefore, BF operators would be subject to the uncertainty of the spot market.
To have greater control of HBI supply without having to rely on merchant sources would require building a dedicated facility, as many EAF steelmakers have historically done. In regions where natural gas is not readily available or sufficiently allocated for HBI production, off shore sourcing may be a practical option.
One steel company has already chosen this route. voestalpine of Austria is operating a 2 million metric tons per year MIDREX® HBI plant near Corpus Christi, Texas, USA. The company is capitalizing on the low natural gas prices in North America to supply its BFs in Linz and Donawitz, Austria. Current plans are for about half of the plant’s output to be supplied to voestalpine’s steel plants, with the remaining HBI to be sold to parties interested in supply over the long-term.
When Wolfgang Eder, CEO and Chairman of the Management Board of the voestalpine Group, announced the decision to invest in the HBI plant in Texas, he pointed out that the use of a natural gas-based direct reduction process will significantly improve the overall carbon footprint of voestalpine and serve as an important step in achieving the Group’s ambitious internal energy efficiency and climate protection objectives.
Europe is the first to pursue the off-shore HBI sourcing solution, but it will not be the last. BF producers in India and China, who are faced with limited or high cost natural gas, much like in Europe, have an even greater incentive to search for ways to decrease smog derived from the burning of coal.
STUDY OF POSSIBLE INTEGRATION STRATEGIES OF DRI PLANTS WITHIN AN INTEGRATED STEEL PLANT
The following chapters depict the various scenarios resulting from the application of natural gas-based and syngas-based MIDREX® technology within an integrated plant, exploiting the possible combinations given by the process gas available and the different process routes to produce liquid steel. An overview of the expected OPEX implications, environmental benefits and resulting plant configuration will be provided.
Iron and Steelmaking Calculation Strategy
The steelmaking industry is composed of several process routes and by a wide spectrum of existing plant set-up and configurations. However, it was decided to compare different scenarios by fixing the final production target for all the scenarios to a capacity of 4 Mtpy and keeping open all balance parameters.
Considering the large ranges of final steel products available in the market and the related different plant configurations, it was decided to compare all the different scenarios with hot rolled coil as final product.
System Boundaries
To properly compare several process routes, as well as their possible combination/interaction, a key point is boundary definition. In fact, steelmaking presents a wide variety of processes with a complex raw materials, gasses and energy balance. Selected system boundaries are shown in Figure 4.
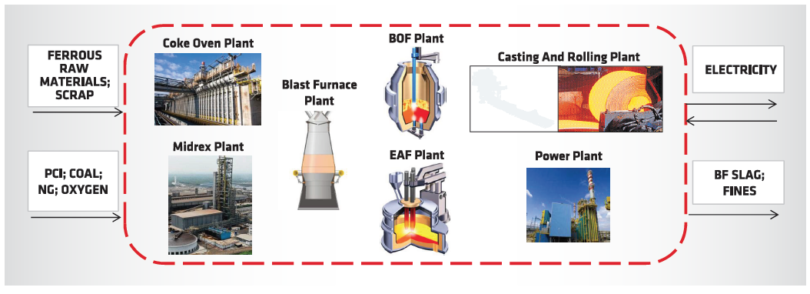
FIGURE 4.
System boundaries for calculation
A few key points and considerations were assumed:
- Power plant was included in the system boundaries to take care of the surplus of process gasses generated in the plant and not directly consumed.
- Agglomeration steps, such as sintering and pelletizing were not included in the system boundaries in order to treat at par the BF route (which normally includes the sintering within the integrated plant) and the DR route (which is based on purchase of pellets from pellet plants normally located near the mines externally of the plant). This choice is representative of a reasonable share of blast furnaces operating with high pellet burden, which is typical of many North American ones and a few operating in the EU.
Steelmaking Gasses
The main gasses involved in the steelmaking process and their typical lower heating value (LHV) considered in the gas and energy balances are given in TABLE I. Their typical distribution across the system boundaries is shown in Figure 5.
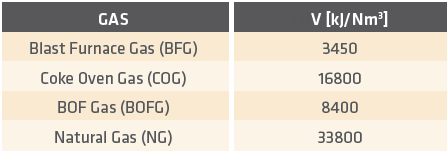
TABLE I. Typical steelmaking gasses and their LHV
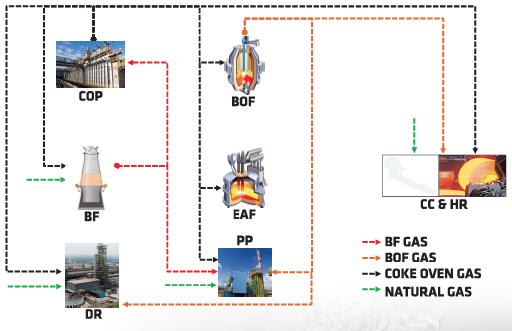
FIGURE 5. Main gaseous flows within system boundaries
The gas balance is done for each scenario, assuming the relevant specific consumption of each plant. The total gas consumption is then calculated, considering resulting plants capacity for the given scenario. The surplus gasses, not directly consumed by the process, are then used in the power plant (with an assumed efficiency of 34%) to produce electrical energy, which is consumed within the plant or sold externally. In several scenarios, an internal energy deficit arose in the plant; therefore, thermal and process balance was maintained by purchasing natural gas where required.
Raw Material and Gas Prices
Main raw materials, media and utilities prices considered in this paper are presented in TABLE II. The figures were taken from main statistical databases or assumed in line with main market trends considering an EU scenario related to late 2015/early 2016 period.
CO2 Calculation
Direct (Scope I) CO2 emission per ton of hot rolled coil of each scenario was determined by calculating the balance between the amount of each material/media input, entering into system boundaries, and the material/media output produced by multiplying such amounts by the specific emission factor of each material/media. Carbon content in the final steel product was not considered.
Indirect emissions (Scope II) related to the electrical energy imported to the plant were considered.
CO2 specific emission factors considered are reported in TABLE III.
Overall CO2 emissions per ton of hot rolled coil were then calculated by adding Scope I and Scope II, as well as the credits for electrical energy exported out of system boundaries (Scope III) and the credits related to the export of BF slag (Scope III). It should be noted that in several cases neither credit for BF slag nor for export of electrical energy produced by the steelmaking plants is included in the calculation. This could substantially change the end results considering that emission savings in the cement industry accountable to BF slag use are substantial, as seen in TABLE III.
Emissions relevant to the production, extraction and transportation (Scope III) of incoming raw materials and media outside of system boundaries were not considered.

TABLE II.
Material, media, and utility prices considered (Exchange rate EUR/USD 1,11)
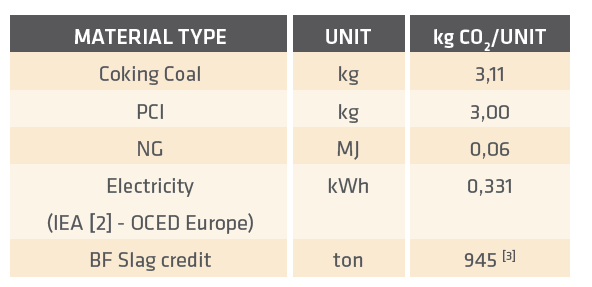
TABLE III. Specific CO2 emission factors considered
Selection of Scenarios
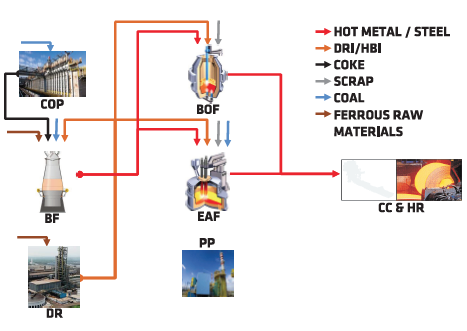
FIGURE 6. Main materials flows within system boundaries
Scenarios definition considered the possible flows of the main materials within system boundaries, as shown in Figure 6, and the corresponding effect on each sub-plant unit.
The intermixing of the typical flows of the BF-BOF route and the ones typical of the DRI-EAF route possible within the system boundaries, such as HBI feeding of the BF or the BOF or HM feeding of an EAF can be seen in Figure 6.
The following scenarios were selected:
a) Scenario 1: Base Case
The typical BF-BOF route was used as the base case. Benchmarking blast furnace operation (having a coke rate of 303kg/tHM and a PCI rate of 200 kg/tHM) and BOF parameters (with scrap input of 200kg/tHM) was selected.
b) Scenario 2: HBI to BF
Keeping the BF-BOF route to produce steel, a MIDREX® Plant was added to the system feeding HBI to the blast furnace. The effect of HBI feeding to the blast furnace burden is well known since industrial trials have been executed since 1966 [4] and have continued up to the present days, as in AK Steel [5]. Main effect of the increased metallization content of blast furnace burden is a reduction of coke rate coupled with an increase of furnace productivity (7-8% per each 10% of burden metallization content [6]).
A maximum blast furnace input of 300kgHBI/tHM was selected considering the effect of BF thermal equilibrium shifting of the HBI, resulting in low top gas temperature.
As an already optimized and highly efficient BF operation was envisaged, fuel rate reduction due to HBI charging was only possible by lowering the PCI rate.
To reduce the OPEX and maximize the synergies of a MIDREX® Plant within the integrated route, the DRI plant was fueled by NG and by COG. The share of 2GJ/tDRI by COG was selected, as higher energy share would result in a different MIDREX® Plant configuration (MXCOL®), which was analysed in a different scenario.
The benefit of productivity increase with HBI charging to BF is not considered in the study, as it would be reflected in a CAPEX reduction rather than in the operating costs considering that overall production is fixed.
c) Scenario 3: HBI to BOF
Keeping the BF-BOF route to produce steel, a MIDREX® Plant was added to the system feeding HBI to the BOF to replace in part purchased scrap. The maximum replacement of 95kg/tLS of HBI was considered, as higher rates have proven to create a slopping problem [7]. MIDREX® Plant set-up was considered, as described in Scenario 2 above.
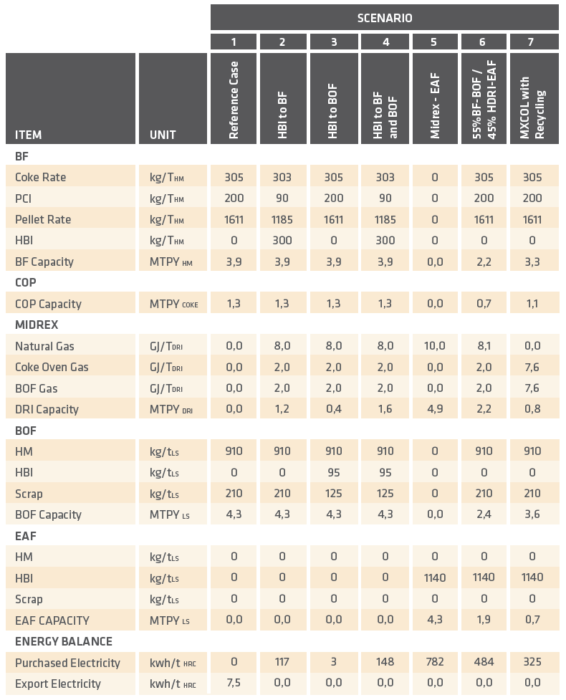
TABLE IV.
Results
d) Scenario 4: HBI to BF and BOF
The maximum utilization of HBI within the BF-BOF route was considered. MIDREX® Plant set-up was considered, as described in Scenario 2.
e) Scenario 5: MIDREX – EAF
The typical DR-EAF route was analysed. The most common MIDREX® NG (natural gas) flowsheet was considered. In order to optimize the OPEX and CO2 emission, 100% hot DRI (HDRI) directly charged into the EAF was selected, reducing the EAF electrical consumption to 385kwh/tLS [8].
f) Scenario 6: Parallel Route with BF-BOF and MIDREX-EAF
A combined route to produce steel adopting a combination of BF-BOF and MIDREX-EAF was considered.
In order to maximize the COG availability within the system rolling mill, reheating furnaces fueled by a mixture of BFG and available BOFG and fully BFG fueled BF hot stove plant were considered.
In order reduce the dependency on natural gas (and therefore also reducing the CO2 emissions and OPEX), the share of the DRI/EAF route was selected so that a full exploitation of the COG produced in the BF-BOF route to saturate the 2GJ/tDRI of the MIDREX® Plant was achieved.
g) Scenario 7: Full Exploitation of Steelmaking Gasses to Produce HBI
To avoid dependence on natural gas to produce DRI, Midrex developed the MXCOL® flowsheet, fueled up to 100% by COG as feedstock [9]. Accordingly, the parallel installation of a BF-BOF and a MXCOL-EAF was considered. The share of MXCOL/EAF capacity was selected to completely exploit all the available COG and BOFG available within system boundaries.
Results
The material, energy and gas balance were developed for each scenario. Main results of each scenario, capacity of each plant, as well as energy import/export are reported in TABLE IV. OPEX and CO2 emission of the various scenarios are indicated in Figure 7, based on prices shown in TABLE II.
The following clarifications should be noted:
- The DRI plant was coupled with the partial or full use of the steelmaking gasses, with the aim of reducing both CO2 emissions and OPEX of the system. Therefore, the system energy balance was driven toward an increased import of external electrical energy. In this sense, the plant is increasingly dependent on the reliability of the surrounding electrical infrastructure and to the price and CO2 specific emission of the electrical energy. Considering the increasing share of electrical energy produced by renewable resources within the EU, it is expected that specific CO2 emission related to electrical generation will further decrease in the future years. This will result in a further reduction of overall CO2 emissions, as most of the scenarios are based on strong electrical imports. The gap of such cases compared to the reference scenario, which is electrically independent, will therefore increase.
- In all cases (except scenario 7), DRI is fully or partially produced by natural gas and therefore its price and availability play a key role in the beneficial implementation of such scenarios. The effect of natural gas price was analysed in the chapter, “Effect of Price Scenarios.”
- Depending on the relative price of captive HBI and purchased scrap, it can be economically attractive to self- produce the HBI to replace the scrap in the BOF, as in Scenario 3. However, overall CO2 emissions are increased because scrap is not associated with any CO2 emission while CO2 is emitted to produce the HBI.
- For scenarios in which BF-BOF and DRI-EAF routes are coexisting, determination of the share between the two routes should be carefully evaluated case by case. For instance, if the BF-BOF share is reduced, less steelmaking gasses will be available for use within the DRI route.
- Within the above EU price scenario, DRI production increases the operating costs. It follows that CO2 reduction can be achieved on a competitive basis only if a proper price environment will be set. [10]
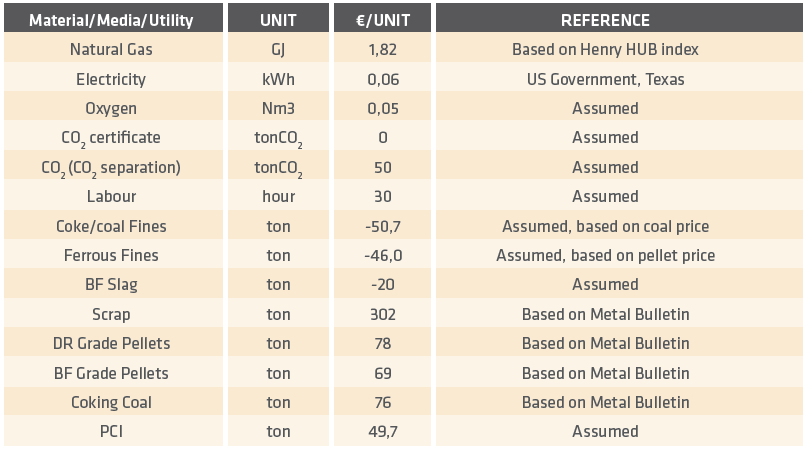
TABLE V.
Material, media, and utility prices: North America scenario (Exchange rate EUR/USD 1,11)
Effect of Price Scenarios To evaluate the effect of natural gas price, all the scenarios were recalculated considering a North American condition. In this sense, natural gas and electricity prices were changed while other raw materials prices were kept constant. No CO2 credit cost was considered and an electricity specific emission factor of 0,522 kgCO2/kwh [2] was used related to late 2015/early 2016 period. Updated prices are shown in TABLE V.
Updated OPEX and CO2 emission of the various scenarios according to the North American scenario are shown in Figure 8.
The considerable reduction of the natural gas price compared to the EU scenario resulted in a complete change of the OPEX associated with the various scenarios; in particular, a relative improvement of the OPEX of the scenarios involving HBI production. The different CO2 emissions are accountable to the higher specific CO2 emission associated with electrical production in the US.
CONCLUSION – Lowering the Carbon Footprint Is a Path to Integrated Steel’s Sustainability
As worldwide environmental regulations get more and more stringent, steelmakers will need to find ways to maximize their resources while curbing emissions. Integrated mills are the largest contributor of CO2 by both volume and percentage. Ironmaking alone accounts for 80-85% of total steel industry emissions. Simple process chemistry shows that only so much can be done to limit emission when converting FeO into Fe by the traditional coke oven-blast furnace method. Operational changes, such as using HBI in the blast furnace can shrink the carbon footprint of integrated steelmakers by decreasing the coke rate and increasing productivity.
Natural gas-based DRI production produces 1/3 the amount of CO2 as blast furnace iron production. As a result, from mine to finished steel, the DR/EAF route produces at least 50% less CO2 than the BF/BOF route. However, it is foreseeable, particularly in Europe and North America, that there will be political pressure to keep many of the large, integrated facilities online in order to keep people employed and support local and national economies. This pressure could in fact lead to the building of DRI plants, especially those that produce HBI. The building of DRI plants and increased HBI usage is a much more realistic approach than trying to replace an entire network of integrated facilities with complete DR/EAF complexes.
Long term there will be shuttering of some older, less efficient blast furnaces by increasing the productivity and reducing the emission of more efficient facilities. The use of HBI made by a natural gas-based direct reduction plant is a positive first step, followed by an effort to maximize all essential resources to their fullest. HBI is expected to see significant growth for use in blast furnaces, as exemplified by the decision of voestalpine AG to build a 2 million metric tons per year MIDREX® HBI Plant in Texas, USA, in order to supply HBI for its blast furnaces in Austria.
It is our opinion that the true impact of direct reduction is yet to be realized by the steel industry. Low cost natural gas, a mainstay of shaft furnace direct reduction technology, is encouraging DRI production in North America and elsewhere. HBI has been used to increase hot metal output in the blast furnace since the 1980s, primarily when the meltshop was hot metal short. However, the environmental benefits of HBI use may be the best alternative for keeping some integrated steel works in operation for years to come.
Thanks to its international presence, technical know-how, expertise and the recent addition of a MIDREX license, Paul Wurth/SMS Group is open to proactively support the steelmaking industry in seeking to achieve the GHG reduction targets in the years to come.
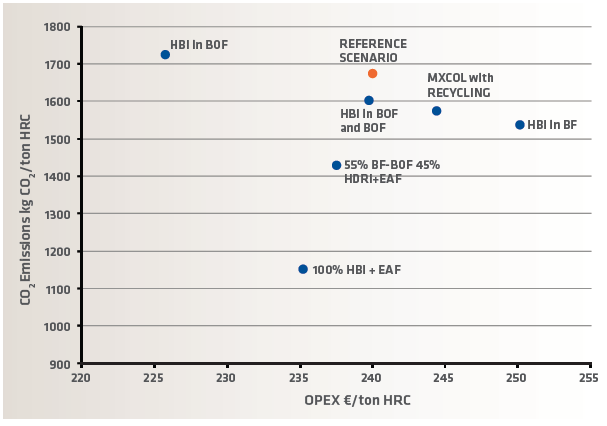
FIGURE 8.
Results: OPEX and CO2 emissions (North American scenario)
REFERENCES
[1] International Energy Agency. Tracking Industrial Energy Efficiency. 2007
[2] CO2 Emissions from Fuel Combustion (2012 Edition), IEA
[3] Steel’s contribution to a low carbon Euro 2050 – Technical and economic analysis of the sector’s CO2 abatement potential – The Boston Consulting Group.
[4] Blast Furnace operation with pre-reduced burdens. Journal of metals, February 1966
[5] F. Rorick; J. Poveromo, Recent developments in North American Ironmaking, 5th European Coke and Ironmaking Congress, 2005
[6] Schmöle P. Lüngen H. Use of pre-reduced material in the blast furnace: metallurgical, ecological and economic aspects, Stahl und Eisen, 2007, vol 4, pp47-54
[7] Pastucha K. et. Al, Steel Quality Improvement with Use of HBI Briquettes at the New Greenfield LD Steelmaking Plant AMK Alchevsk, Ukraine. AISTech 2009
[8] Abel M. Böhm C. Sterrer W. Vaillancourt D., Solutions for the increased usage of DRI in the Electric Arc Furnace, AISTech, 2014
[9] Gary Metius et al., DRI Production Using Coke Oven Gas (COG): Results of the MIDREX® Thermal Reactor SystemTM (TRS®) Testing and Future Commercial Application; AISTech 2015
[10] Perato M.; Magani S.; Astoria T.; Michishita H.; Meier L.; Application of Midrex technologies in Integrated Steel Plants; possible reduction of environmental impact and Opex; ECIC 2016, pp 686-695
ADDITIONAL REFERENCES
- Robert L. Hunter, “Massive Savings in CO2 Generation By Use of HBI,” Direct From Midrex, Midrex Technologies, Inc., Charlotte, NC, 3-4Q 2009, pp 9-11.
- Robert L. Hunter, “Massive CO2 Savings by use of HBI made with natural gas. Where are the loci?” Direct From Midrex, Midrex Technologies, Inc., Charlotte, NC, 1Q2010, pp 7-10.
- Editorial Staff, “Blast Furnace Burden Enrichment Using Direct Reduced Iron, Direct From Midrex, Midrex Technologies. Inc., Charlotte, NC, 2Q1993, pp 9-10.
- Franz L. Sammt, “Update: Blast Furnace Burden Enrichment Using Direct Reduced Iron, Direct From Midrex, Midrex Technologies, Inc., Charlotte, NC, 4Q1994, pp 9-10.
- Henry P. Gaines and Christopher M. Ravenscroft, “A scenario for integrated sustainability: Application of the TRS® for the integrated blast furnace steel industry,” 2014
- T. Buergler, J. Prammer and R. Hackl, voestalpine Stahl GmbH, Austria, and B. Kohl, voestalpine AG, Austria, “Raw materials and technologies for Iron- and Steelmaking under the aspects of the EU Low Carbon Roadmap,” 2015.