Algerian-Qatari Steel (AQS): At First Glance
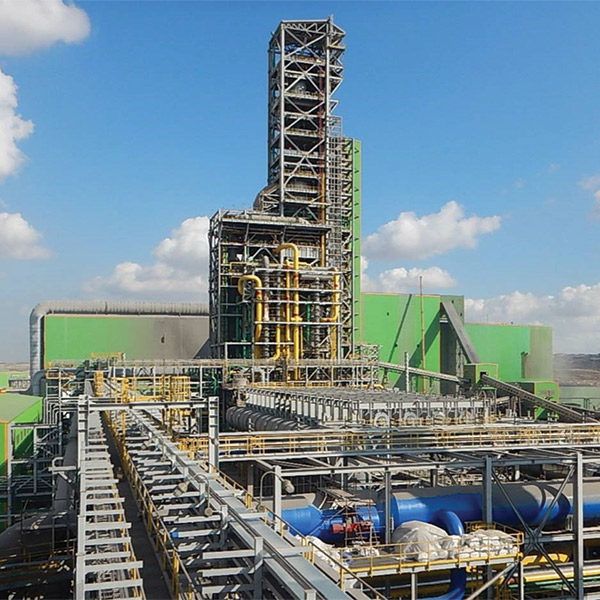
Introduction
Algeria, by its geographical location, is a gateway to Mediterranean Europe and the MENA (Middle East & North Africa) Region. Algeria enjoys natural benefits that include climatic diversity, mineral resources, and agricultural land, as well as specialized and skilled labor, which together provide investment opportunities in various sectors such as mining, medicine, tourism, industry, and agriculture.
Today, Algeria is home to the Arab Iron and Steel Union (AISU) and the location of the two largest capacity direct reduction (DR) plants in the world, both based on MIDREX® technology: Algerian Qatari Steel (AQS) in Bellara Industrial Zone (El-Milia) near Jijel in the east and Tosyali Algeria at Bethioua (Oran) in the west. Both companies are embarking on expansion projects that will include the installation of an additional direct reduction plant equipped for on-demand production of hot DRI (HDRI) and cold DRI (CDRI) plus an insulated conveyor system to transport HDRI to the EAF steel shop.
This article will take a closer look at what makes Algeria ideal for DRI-EAF steel production, the origin of AQS, the results of the first full year of DRI-based steel production, and future plans of AQS.
THE RISING STAR IN DRI PRODUCTION
The following main reasons make Algeria attractive for iron and steel investments:
- Political stability boosts the confidence of foreign investors
- Availability and pricing of natural gas and electricity, which are among the lowest in the world
- Strong governmental policies favoring the industrial sector
- Reserving natural gas for national industry development
- Strong bilateral trade agreements and incentives
Moreover, after the Gara Djebilet iron ore deposit in Tindouf Province development, Algeria will be one of the lowest-cost DRI producers in the world (iron oxide pellets typically make up 80-90 % of DRI OPEX).
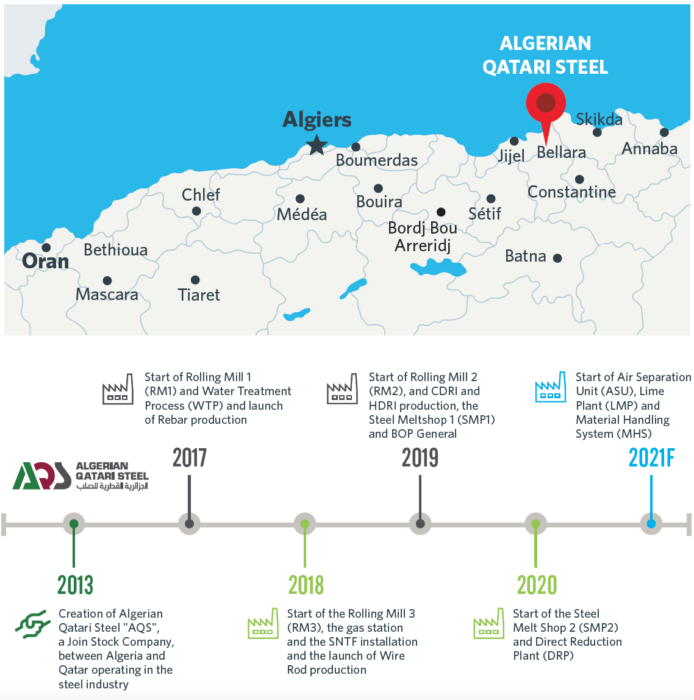
Timeline
AQS production units launching schedule
ALGERIAN-QATARI STEEL (AQS)
AQS was established in December 2013 as a joint venture between Qatar Steel International (49%), SIDER Investment Group (46%), and the Algerian National Investment Fund (5%). The relations between Algeria and Qatar are longstanding and growing, highlighted by decades of cooperation and synergy in economy and trade, industry, energy, mining, agriculture, and social and political initiatives.
AQS operates a 2 million metric tons per year (Mt/y) steel mill in the industrial zone of Bellara, in El-Milia, an administrative district of Jijel, located 400 km from the Algerian capital, Algiers. The steel complex occupies a total area of 216 hectares (> 553 acres) and includes these main production units:
- MIDREX Direct Reduction Plant – production capacity of 2.5 Mt/y HDRI and CDRI
- Two 120-ton EAFs – total production capacity of 2.2 Mt/y
- Three rolling mills – total production capacity of 2 Mt/y of reinforcing bars and wire rod
Supporting these production units are an industrial gas plant, lime production unit, station for receiving & transporting raw materials, water treatment plant, and electrical substation.
The AQS project was launched in March 2015, and the first rolling mill (for reinforcing bars) and the water treatment plant began operation in 2017. The complex continued to take shape in 2018, with startup of a second rolling mill (for wire rods) and the industrial gas plant and SNTF (The National Rail Transportation Company) installation between the plant and Djen Djen international Port. In 2019, the third rolling mill and the first EAF were put into service. The second EAF and the MIDREX Plant were started up in end of 2020, followed in 2021 by the air separation plant, lime plant, and the materials handling system.
AQS MIDREX COMBINATION (CDRI-HDRI) PLANT
Midrex Technologies, Inc. and Paul Wurth were contracted in 2016 to supply a 2.5 million tons/year direct reduction plant (DRP) capable of producing both CDRI and HDRI.
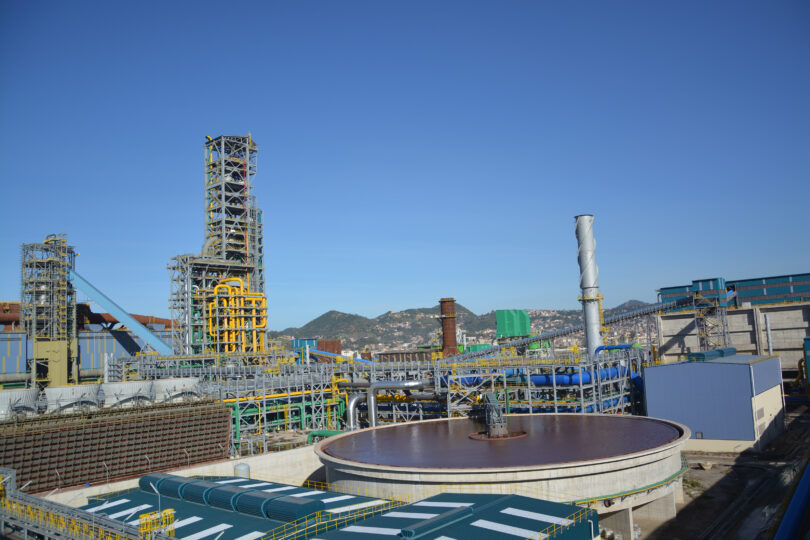
Main Features:
- World’s largest combination HDRI/CDRI plant
- 7.65 meters diameter MIDREX MEGAMOD® furnace
- 8 rows x 18 bays MIDREX Reformer
- 312.5 t/h HDRI transported by insulated metallic conveyor at 650° C
- Switch to 100% CDRI when HDRI is not required
First product was produced by the DRP in February 2021, HDRI was charged to the EAF in March 2021, and hourly design capacity (312 t/h) was achieved in September 2021. AQS was operating at 9% over design capacity by March 2022.
During 2022, 74% of total production (1.7 million tons) was HDRI, which had a remarkable positive impact on DRI costs, as will be discussed in the following section. DRI production (CDRI and HDRI) in 2022 was based on melt shop demand.
HDRI TRANSPORTING & FEEDING SYSTEM
The AQS DRP is equipped with an enclosed and insulated metallic conveyor capable of feeding HDRI at up to 312.5 tons per hour according to melt shop demand. The HDRI reaches the EAF at 650° C, and direct charging to the EAF ensures there are no fugitive dust emissions.
The transporting & feeding system is designed so HDRI and CDRI can be mixed at the discretion of the melt shop or HDRI can be diverted to a product cooler and stored as CDRI according to melt shop requirements. During 100% HDRI production, some “trickle discharge” is maintained to avoid static DRI at the product cooler.
Figure 1 shows the product discharge arrangements that allow AQS to produce HDRI and CDRI from the same shaft furnace.
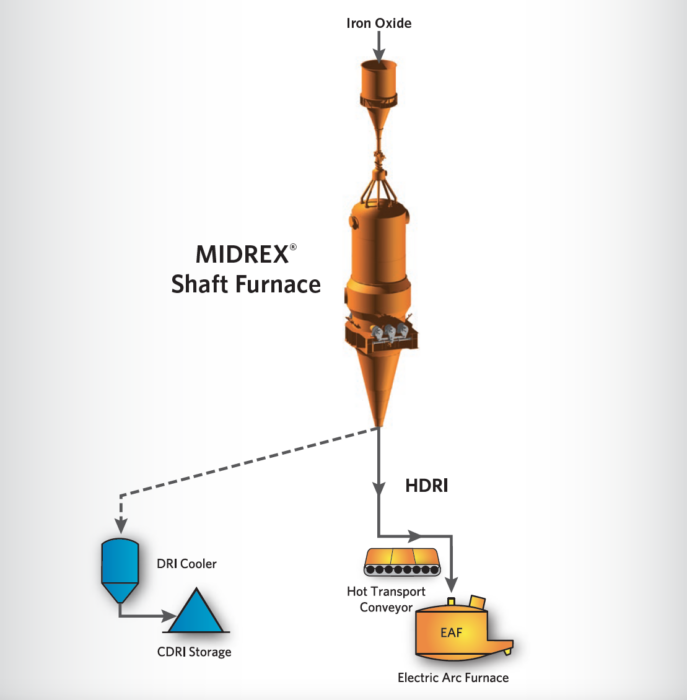
FIGURE 1
Reduction furnace product discharge options
GAINS ACHIEVED BY HDRI FEEDING SYSTEM – DRP
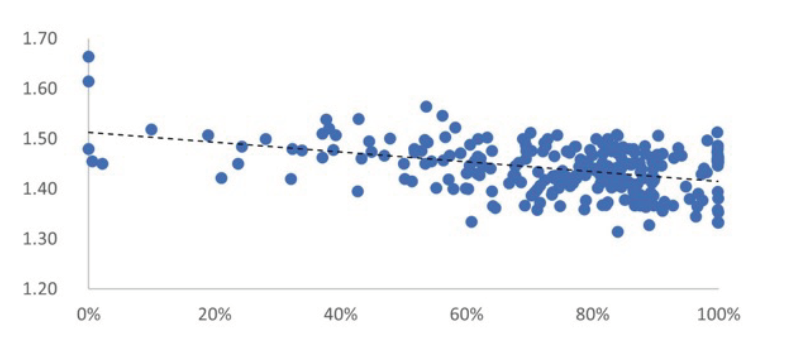
FIGURE 2. Daily average MRMR (iron oxide/product) with different HDRI ratios
During Y-2022, AQS DRP increased plant yield by reducing the major raw material ratio (MRMR) due to the following, as shown in Figure 2:
- No fines/dust carryover to the cooling gas system
- No losses from CDRI handling (product fines charged to EAF along with HDRI)
During the same period, natural gas consumption was reduced due to stoppage of cooling gas recycle (no in situ natural gas), as shown in Figure 3.
Daily average electricity consumption by the DRP was reduced because the cooling gas compressor and the CDRI handling conveyor and product screen were not needed (due to 100% HDRI charging), as shown in Figure 4.
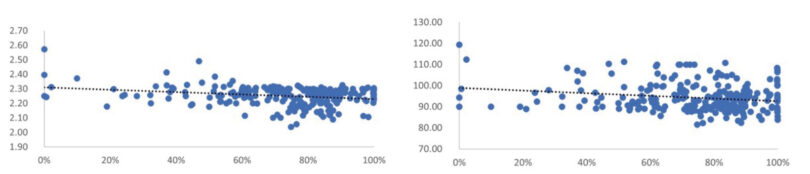
FIGURE 3.(left) Daily average NG consumption Gcal/TDRI with different HDRI ratios; FIGURE 4.(right) Daily average electricity consumption Kw/ton DRI with different HDRI ratios
Ultimately, product quality was improved including a remarkable gain in carbon content compared to CDRI, as shown in Figure 5a and Figure 5b.
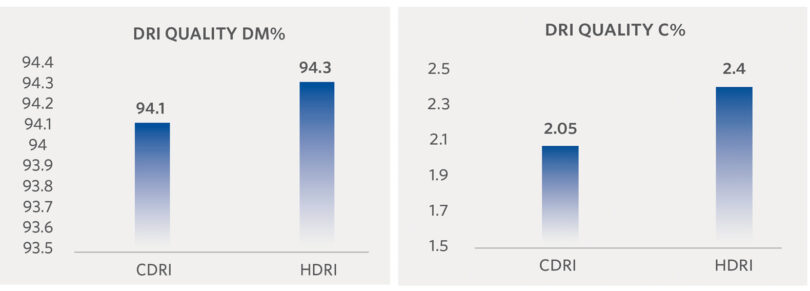
FIGURE 5a.(left) DRI % metallization HDRI vs CDRI; FIGURE 5b.(right) DRI % carbon HDRI vs CDRI
GAINS ACHIEVED BY HDRI FEEDING SYSTEM – MELT SHOP
The AQS melt shop recorded significant operational gains attributed to the HDRI feeding system, as shown in Table I:
- Lower specific electricity consumption, increased productivity due to shorter tap-to-tap times
- Less electrode and refractory consumption due to shorter overall melting cycle
The savings in electricity, natural gas, and raw material by the DRP and the Melt Shop were approximately 15 USD/ TMS, and the additional 360,000 tons of liquid steel when using 100% HDRI vs 100% CDRI .
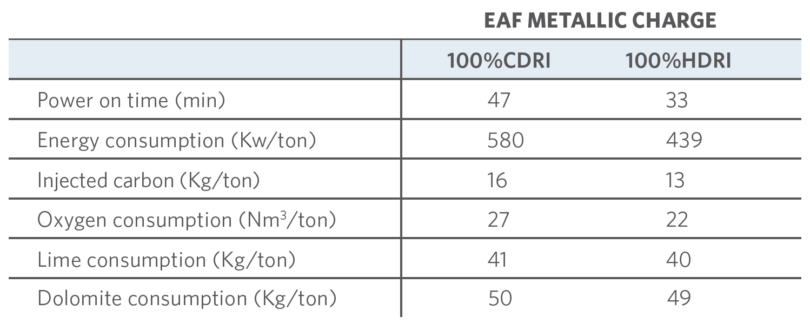
TABLE I.
Comparison of operating with 100% HDRI vs 100% CDRI
GUIDELINES FROM LESSONS LEARNED
Because the DRP operates continuously and the EAFs have a batch operating pattern, close coordination between the DRP and melt shop teams is essential to achieve the maximum benefits from feeding HDRI. A smooth switch between HDRI and CDRI discharge patterns to meet melt shop demands and maintain productivity rates. Also, long periods of inactivity in CDRI discharge allows the cooling gas scrubber packing to become fouled from scaling.
AQS has adopted the following guidelines from their operating experience:
1. When the melt shop can take entire HDRI production, CDRI is stopped and “trickle discharge” is directed to the product cooler to avoid a static bed inside the cooler, as follows:
2. When the cooling gas compressor is stopped for an extended period, scale inhibitor and biocide doses to the cooling gas scrubber must be adjusted.
AQS EXPANSION PLANS
On November 1, 2022, the Emir of Qatar, Amir Sheikh Tamim bin Hamad Al-Thani, and the president of the People’s Democratic Republic of Algeria, Abdelmadjid Tebboune, attended the official inauguration of the AQS steel plant. The intention to expand the steel complex to 4 Mt/y of steel and 5 Mt/y of DRI was announced during the ceremony.
AQS has started the expansion process by launching a tender for selecting an external consulting firm to prepare the feasibility study for extending the existing steel complex in the Bellara Industrial Zone (Phase II) and to determine whether AQS will launch any new steel products as part of the expansion project.
The expansion project is expected to be completed by the end of 2025 or early 2026.
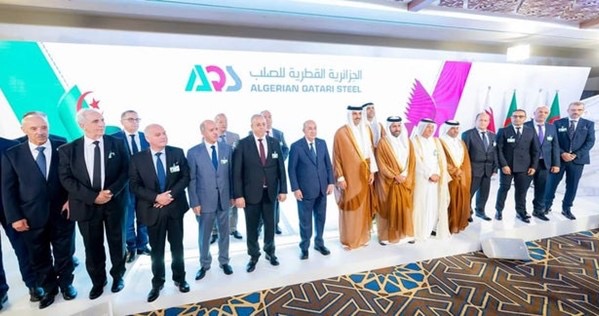
Shown in the photo are the Emir of Qatar, Amir Sheikh Tamim bin Hamad Al-Thani, the president of the People’s Democratic Republic of Algeria, Abdelmadjid Tebboune, as well as the AQS Board of Directors.