Top 10 Midrex Social Posts of 2022
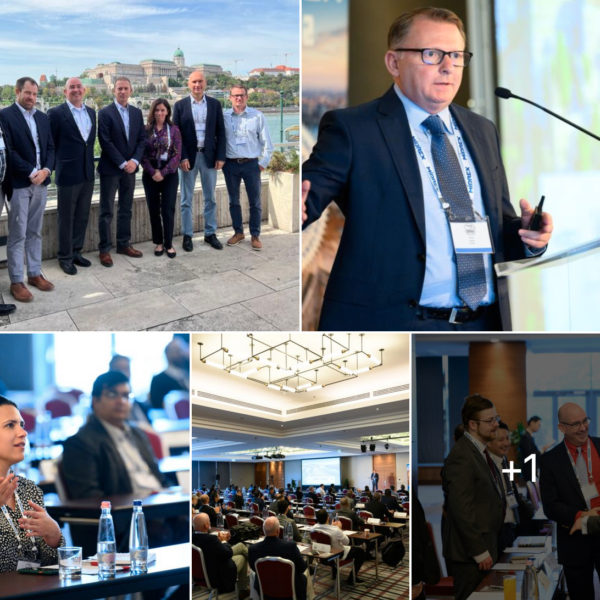
During 2022, posts related to our family of MIDREX Plants brought the highest engagement rate, according to data.
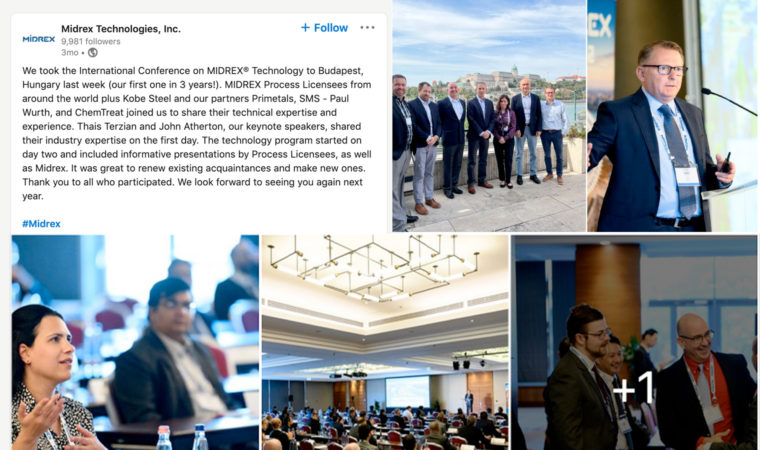
#1 - International Conference on MIDREX® Technology
We took the International Conference on MIDREX® Technology to Budapest, Hungary last week (our first one in 3 years!). MIDREX Process Licensees from around the world plus Kobe Steel and our partners Primetals, SMS-Paul Wurth, and ChemTreat joined us to share their technical expertise and experience. Thais Terzian and John Atherton, our keynote speakers, shared their industry expertise on the first day. The technology program started on day two and included informative presentations by Process Licensees, as well as Midrex. It was great to renew existing acquaintances and make new ones. Thank you to all who participated. We look forward to seeing you again next year.
#2 - ArcelorMittal spotlight
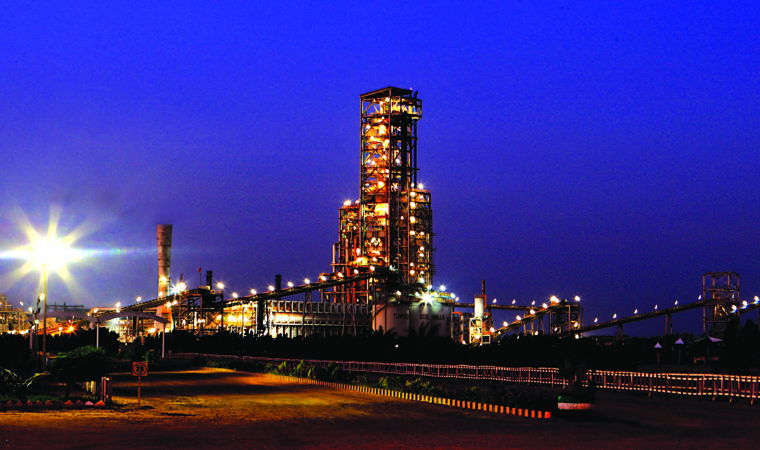
ArcelorMittal owns and operates 15 MIDREX® Modules (a plant can include one or more module) in seven countries having a combined rated capacity of 11.52 million tons/year*. AM has experience with all forms of DRI products: cold DRI (CDRI), hot DRI (HDRI), and hot briquetted iron (HBI), and AM Group plants have produced a cumulative total of 262.61 million tons of DRI.
This August, three direct reduction plants owned by Arcelor Mittal companies reached significant milestones: ArcelorMittal Canada 2 in Contrecoeur, Quebec, Canada will complete its 45th year of operation. The plant has produced 28.24 million tons of CDRI since its initial start-up in 1977.
ArcelorMittal/Nippon Steel India III in Hazira, Gujarat, India will complete its 30th year of operation. The third of six modules belonging to AM/NS India has accounted for 14.06 million tons of HDRI and hot HBI.
Arcelor Mittal Lazaro Cardenas in Lazaro Cardenas, Michoacan, Mexico will complete its 25th year of operation. The plant has provided the adjacent melt shop with 36.06 million tons of CDRI.
#3 - Tosyalı Algérie Sets DRI Production Record in 2021, Contracts 2nd DRI Plant
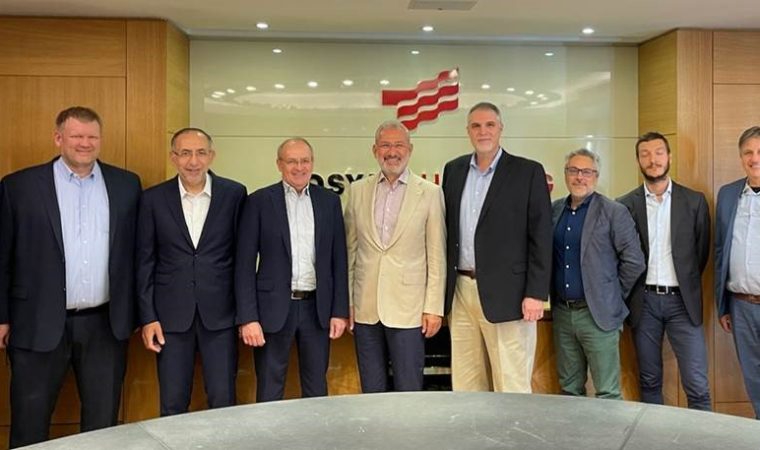
Tosyali Algerie A.Ş. established a new world record in 2021 for annual direct reduced iron (DRI) production by a single module plant, producing more than 2.28 million tons. The former record was set in 2020 by Tosyali in only its second year of operation.
“Our fundamental priority is operational sustainability and full compliance with environmental, social and governance principles,” Dr. Suhat Korkmaz, CEO of Tosyalı Holding, said.
In July 2021, Tosyali Holding awarded Midrex and its partner Paul Wurth a contract to build a second DRI plant at the Tosyali Algerie steelworks in Bethioua (Oran), Algeria. The new DRI plant will produce 2.5 million tons of cold DRI (CDRI) and hot DRI (HDRI), similar to the original plant, with the capability of all MIDREX Plants to operate with even more hydrogen in the future.
“We’re very pleased to be working with Tosyali on a second DRI plant.” Midrex Technologies President and CEO Stephen C. Montague said. “Direct reduction is the best technology to reduce the CO2 footprint of the steel industry, and this plant is designed to utilize even more hydrogen as it becomes available in the future.”
Read the official press release:#4 - DRIC-2 completes 15 years of operation
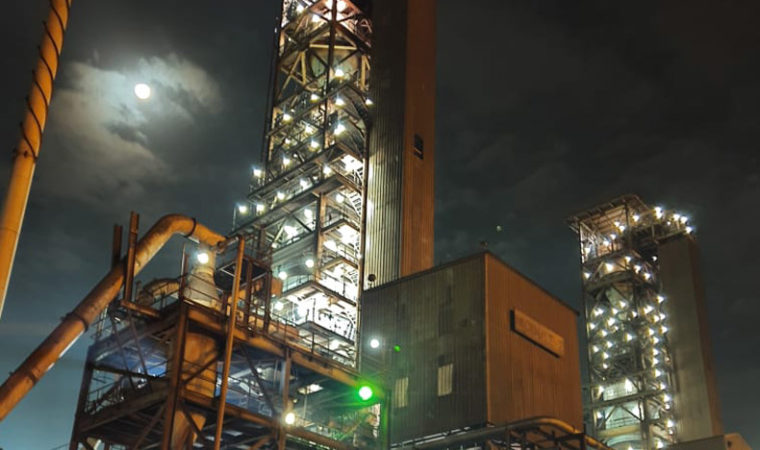
Direct Reduction Iron Company Ltd. operates the two most-traveled MIDREX® Direct Reduction Modules, having been first installed in Hunterston, Scotland, for British Steel Corporation, then relocated to Mobile, Alabama, USA, to supply DRI to BSC subsidiary Tuscaloosa Steel, before becoming established as key production facilities of Al Ittefaq Steel Company’s Arab Steel works in Damman, Saudi Arabia. The DRIC-2 module was started up in May 2007 and together with DRIC-1 (started up December 2007) have an annual production capacity of 1.0 million metric tons of cold DRI (CDRI).
After setting its all-time production record in 2019 (534,643 tons), DRIC-2 continued to exceed its annual rated capacity in 2020, produced almost 525,000 tons of CDRI, with plant availability of 99.6%. The two DRIC modules have produced more than 10 million tons of CDRI since start-up in 2007.
DRIC is a subsidiary of Arab Steel Company, which is part of Al Ittefaq Steel Company (ISPC).
#DirectReducedIron #midrex #steel
Al Ittefaq Steel Co. (ISPC) website#5 - H2 Green Steel announcement

Midrex is proud to announce our agreement with H2 Green Steel to supply the world’s first commercial 100% hydrogen direct reduced iron (DRI) plant. The 2.1 million tons per year MIDREX H2™ Plant will be located in Boden, northern Sweden.
This first-of-a-kind DRI plant will be provided by a consortium of Midrex and Paul Wurth and sets the standard for green steel. By replacing coal with green hydrogen powered by renewable electricity, water and heat become the primary emissions.
“This unique project is a ‘lighthouse’ to our industry and sets the standard for green steel. There is simply nothing like it – 100 percent hydrogen from day one to produce over 2 Mt/y of DRI with up to 95% reduction in CO2 emissions,” says Stephen C. Montague, President and CEO of Midrex Technologies, Inc. “This is where Midrex wants to be – at the leading edge of technology.”
Read the full press release#6 - MIDREX® Process Meets the Challenges
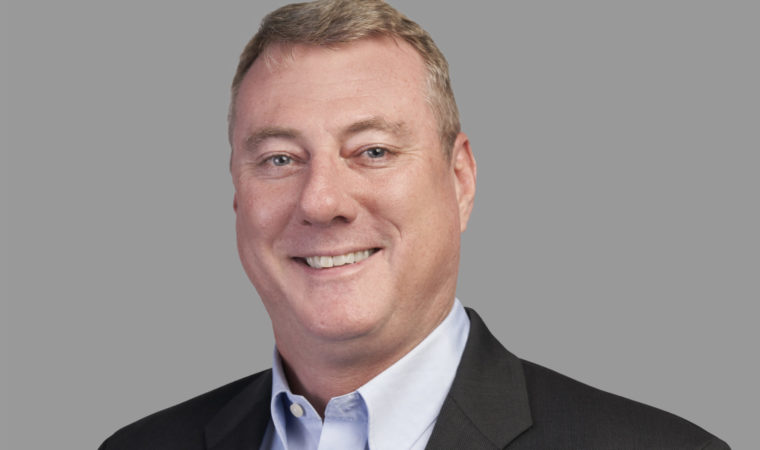
When John Teeters, Director of Engineering at Midrex, first started at Midrex in 1996, the 6.65-meter shaft furnace was a relatively new and crucial step for us. His team talked about a “MEGAMOD” plant design, as if it were a stretch for our capabilities. Apart from the COMSIGUA HBI plant in Venezuela, all of the latest contracted plants were designed to produce DRI only.
We were treading carefully on our first attempts at feeding oxide to a furnace with a vertical conveyor. Midrex was installing the first of our oxide coating and oxygen injection systems, and we were just starting to talk about developing 3D models of our plants as an input for engineering. At that point, no single direct reduction module had ever produced one million tons of DRI in a year.
As part of our most recent edition of Direct from Midrex, this article shares insight from John Teeters on how today’s MIDREX® process meets the challenges.
#7 - Hadeed C Celebrates 30 Years
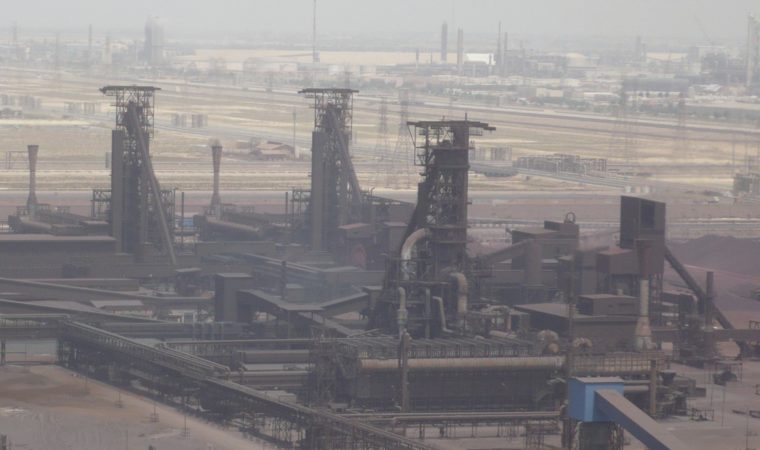
Hadeed, which means “iron” in Arabic, owns and operates four MIDREX Modules at its integrated direct reduction/electric arc furnace (DR/EAF) steelworks in Al-Jubail, Saudi Arabia, 467 km (290 mi) east of Riyadh on The Gulf. Hadeed A-C, which produce cold DRI (CDRI), were started up in 1982, 1983, and 1992, respectively. Hadeed E produces hot DRI (HDRI) and was started up in 2007. In its years of operation, Hadeed C has produced approximately 27.5 million tons of DRI, which is an annual average of more than 785,000 by a plant designed for 600,000 tons per year. Hadeed is owned by SABIC (Saudi Basic Industries Corporation).
Read more about Hadeed on the Sabic website#8 - TBT to the longest-operating MIDREX Direct Reduction Plant: ArcelorMittal Hamburg
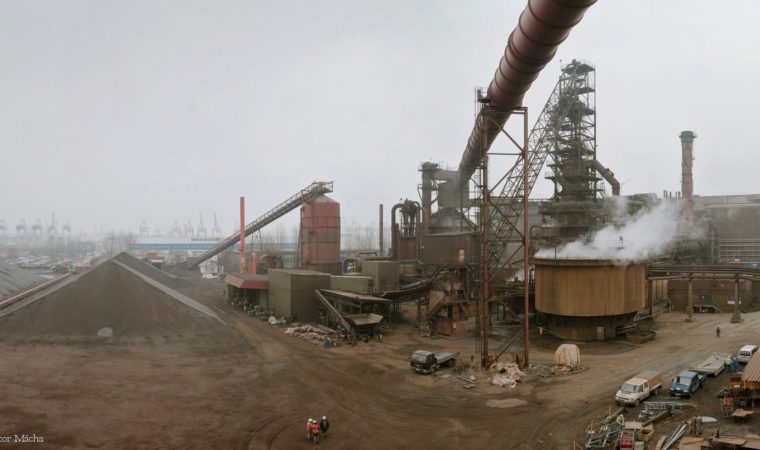
ArcelorMittal Hamburg was founded in 1969 as Hamburger Stahlwerke GmbH and is one of the largest manufacturers of quality wire rod in Germany and the only direct reduction plant in Western Europe. It is one of the world’s leading companies in the field of quality wire rod production with the mini-mill concept.
In September 2019, ArcelorMittal announced the signing of a Framework Collaboration Agreement (FCA) with Midrex to design the Hamburg demonstration plant and work on several related R&D and innovation projects. It is aimed at the first industrial scale production and use of Direct Reduced Iron (DRI) made with 100% hydrogen as the reductant.
Learn More
#9 - Qatar Steel 2 completes 15 years of operation
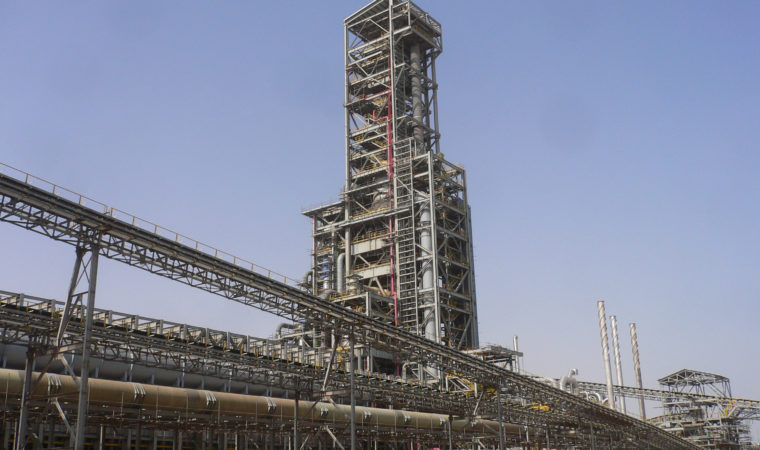
Qatar Steel 2 is a unique plant design: a combination plant (hot discharge furnace capable of dual product operation) equipped with a product cooler, which allows the production of hot briquetted iron (HBI) and cold DRI (CDRI). DR-2 has produced 19.85 million tons of DRI products since it was started up in July 2007. Together with DR-1, a 400,000 t/y MIDREX Module, which was started up in August 1978, Qatar Steel has accounted for almost 48.2 million tons of DRI and HBI.
Qatar Steel Company (QASCO) began commercial operation in 1978 as the first direct reduction-electric arc furnace (DR-EAF) steel mill in the MENA Region. The company became wholly owned by Industries Qatar (IQ) in 2003 and is now known as Qatar Steel.
Read more about Qatar Steel#10 - Getting the Most From Direct Reduced Iron – Operational Results of MIDREX® Hot Transport-Hot Charging
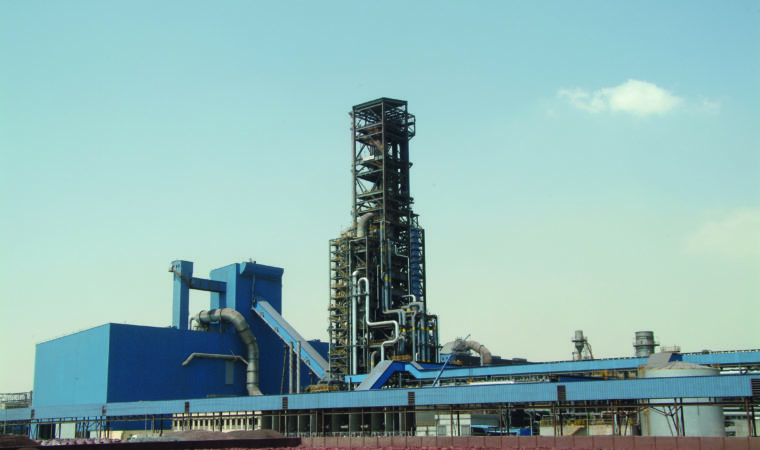
The introduction of the hot discharge furnace for producing hot briquetted iron (HBI) not only made it safer and easier to transport direct reduced iron (DRI) as a merchant product, it led to the development of methods for transporting and charging hot DRI (HDRI) into an electric arc furnace (EAF) to take advantage of the sensible heat in the HDRI. The result is increased productivity and yield, as well as reducing the need to inject carbon to balance the EAF heat, thus lowering carbon dioxide (CO2) emissions.
By using one of three hot transport systems – hot transport vessels (HTV), hot transport conveyor (HTC), and HOTLINK® – HDRI can be charged to an EAF at up to 650° C.
Read about the origin and benefits of HDRI, associated methods and criteria, and more from one of our most recent Direct from Midrex articles at the link below.
#DirectReducedIron #steelmaking #DirectfromMidrex #Midrex
Read Article