Midrex Global Solutions 2.0 – Harnessing the Power of Digitalization
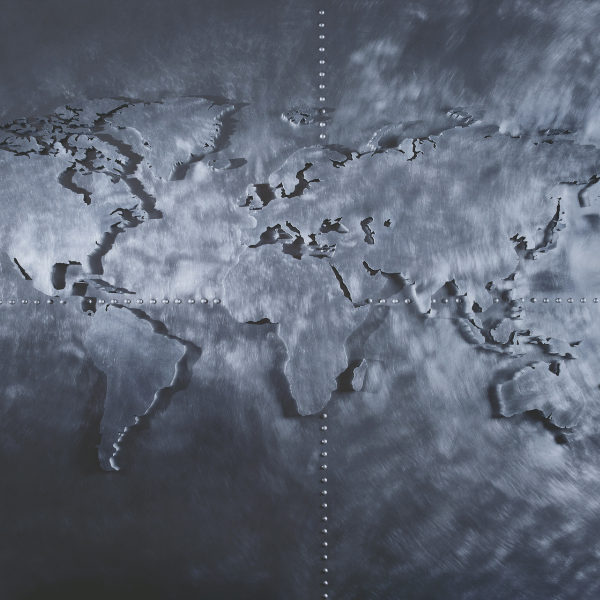
One of the things that separated Midrex from other US industrial companies doing business internationally in the 1970s was the decision to enter into two-way licensing agreements rather than to build, own, and operate plants. This innovative approach involved the sharing of technology, know-how, and field experience among Midrex and the operators of MIDREX® Plants. It allowed Midrex to focus on what it did best – design and supply direct reduction process technology and proprietary equipment – while cooperating with its customers to make improvements based on actual plant operations. The results speak for themselves.
For the first 20 years, Midrex primarily provided technical advice and managed the transfer of technology. In 1990, Professional Services International (PSI) was established as a subsidiary of Midrex to more actively support the growing number of MIDREX® Process Licensees and to provide procurement and logistics services to Kobe Steel, parent company of Midrex. The decision was made in 2004 to integrate PSI into Midrex and Midrex Solutions was formed, which soon was renamed Midrex Global Solutions (MGS). In 2018, the benefits of digitalization were added to the toolbox – thus the MGS 2.0 relaunch.
How well a plant is maintained and serviced is instrumental in determining its performance, reliability, and longevity. Plus, the larger the capital investment, the more important the selection of an aftermarket services provider becomes.
Midrex Global Solutions goes beyond supplying spare parts and materials. As both the provider of process technology and an OEM equipment supplier, Midrex has a comprehensive understanding of customer needs from which to develop practical and sustainable solutions in cooperation with operators of individual MIDREX® Plants.
This issue of Direct From Midrex will introduce MidrexConnect™, a Web-based platform for viewing and analyzing process variables needed to make fast, informed, and accurate operational and maintenance decisions. The second article in this issue will present examples of how two other MGS programs, Plant Services and Proprietary Equipment & Parts, are using the power of digitalization and the process expertise of Midrex to provide reformer management and catalyst optimization solutions for quality and performance assurance.
Midrex has assembled a team of experienced engineers and plant operators with the expertise and experience to quickly diagnose situations and create timely, sustainable solutions which are specific to each customer. MGS is the only plant services provider that can guarantee that its solutions are designed, manufactured, and installed to exact MIDREX® Process specifications and backed by 50 years of dedication to the continued success of its process licensees.