Defining and Redefining DRI – An Evolving, Enduring Relationship with Steelmakers
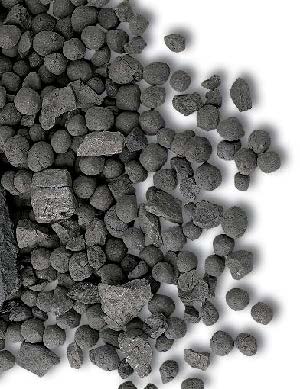
Some form of direct reduction ironmaking has been around for nearly 3000 years, yet today ask a group of steelmakers, “What is direct reduced iron?” and you will receive a variety of answers. Go a step further and ask, “How does DRI relate to scrap,” and likely each one will also have a different response.
Alternative Iron or Scrap Supplement… Just don’t call it a Substitute!
DRI, in the modern era (1946-present), has been closely identified with scrap. Initially, it was an alternative source of metallic iron used in electric arc furnaces (EAFs) to produce commodity-grade steel products in areas where sufficient scrap was not readily available. Beginning in the 1970s, the combination of a DRI plant and an EAF steel mill provided the foundation for national industrialization programs throughout countries in the natural gas rich Middle East & North African (MENA) region.
Meanwhile, leading EAF-based steelmakers in other industrialized countries, most notably the USA, were intent on moving from producing basic grades of steel to competing with traditional integrated producers in the quality and special steel grades. The introduction of technologies, such as continuous cast-ing and its further refinement, thin slab/strip casting, provided the means to make these products.
At this point, even the most progressive EAF operators were saying they could compete with traditional integrated mills in the higher-grade steel grades using premium scrap alone. However, increased demand for premium scrap was putting a severe strain on supplies, which in turn was pushing prices higher. DRI emerged as a means to moderate scrap prices and increase the supply of iron units available to EAF mills.
Meanwhile, the effect of DRI’s chemical characteristics, especially the extremely low residual levels, was be-ing noticed throughout the global steel industry. DRI/EAF mills in gas-rich countries were making exceptional quality billets and USA mills, such as Georgetown Steel Corporation were producing the highest quality wire rods.
Today, EAF operators are blending DRI products and scrap to produce steel grades of all descriptions and specifications in the most economical manner. DRI has become a versatile scrap supplement allowing various scrap to be used by EAF steelmakers while still achieving product spec.
Advent of Merchant Iron
With the increased demand for high quality iron units in the EAF charge, concern for the availability and price of premium scrap mounted. DRI was regarded as a material that could compete with premium scrap and help moderate prices. However, natural gas prices in the USA precluded the production of DRI, so a market was created for merchant iron. The idea was to produce DRI in countries where natural gas associated with petroleum extraction was flared and therefore, priced low. If the country also produced iron ore, the value of making and selling DRI as a merchant product was greatly increased – case in point, Venezuela.
The volume of merchant DRI shipments increased from four thousand metric tons/year (t/y) to almost one million t/y between 1970 and 1984; however, there were several incidents involving shipments of DRI that caught fire and damaged the vessels and their cargoes. This resulted in stricter guidelines by the United Nations maritime body now known as International Maritime Organization (IMO). A form of DRI that was safer to ship over open oceans was needed.
Hot briquetted iron (HBI) was the response by the direct reduction industry.
HBI is significantly denser than traditional DRI, which in some circles is still known as “sponge iron,” making it much more resistant to reoxidation and over-heating. FIOR de Venezuela built and operated the first HBI plant in 1976; however, it was not until Sabah Gas Industries began marketing and shipping HBI from its Malaysian plant in 1984 that the product gained wide recognition. In 2016, almost five million tons of HBI were shipped.
The introduction of HBI, and its acceptance by IMO as a preferred form of DRI for ocean shipping, brought the benefits of DRI to a broader iron and steelmaking audience, including blast furnace (BF) operators. DRI, in pellet and lump form, was not suitable for use in the BF due to its limited strength. HBI has the mass to blend well with other charge materials and increase the metallization of the BF bed so less coke is consumed, thus reducing CO2 emissions and increasing hot metal production.
Throughout the 1990s, HBI was marketed as a replacement or substitute for scrap. It was promoted as a higher quality material than scrap and priced accordingly. The HBI and scrap industries tried to convince buyers to pay more for their products while buyers purchased both products whenever the price was “right.” After several price cycles, HBI promoters and scrap suppliers began to realize their products were commodities; i.e., basic inputs used in the production of finished products, which added more value when used together in the production of steel.
DRI & Scrap – Better Together
Scrap and the different forms of DRI – cold DRI (CDRI), hot DRI (HDRI) and HBI – today are used together in various percentages, depending on the products being made and the operating practice in use. Forward-looking EAF steelmakers, such as Nucor, have invested in their own strategically located DRI plants.
Modern DRI plants are designed to produce multiple product forms “on demand,” providing operators the flexibility to quickly respond to changing market situations. DRI can be transferred to the meltshop while hot to take advantage of the sensible heat. Plants with hot dis-charge furnaces are equipped with briquetting machines to provide a product option when the meltshop is down or steel market conditions are not favorable.
Building an Enduring Relationship
The DRI-scrap relationship is not unlike a human relationship. It starts with passion, each party focused on satisfying its wants, needs and desires. Next comes adjusting to reality, realizing and learning to cope with things that don’t go as expected. After having to adjust to reality, the parties feel vulnerable and are afraid of giving too much. Each wants the other to change and a power struggle ensues. This is the first major test of a relationship.
In the aftermath of the power struggle, the parties separate to reflect and gain perspective. At this point, a re-evaluation of expectations and willingness to contribute takes place. This provides the basis for reconciliation, when each party recognizes and respects that the other will remain an individual while part of the relationship.
The final stage in a committed relationship is complete acceptance. There is an integration of the need of the self and the needs of the relationship. Each party takes responsibility for its own needs, as well as for supporting the other party. A balance between autonomy and union is maintained. When conflicts arise, the parties know how to resolve them relatively quickly. Resentments are few. There are few surprises because they know what to expect. They accept reality for what it is with no denial or fantasy involved. They work together as a team while maintain-ing separate identities. The need of the self and the needs of the relationship are integrated and mutually respected.
Researchers are said to estimate that less than 5% of relationships ever reach acceptance. So far DRI and scrap are proving that former adversaries not only can coexist – they can be more valuable when working together.
(Thanks to the Relationship Institute for the free article, “The Stages of Commit-ted Relationships,” posted online January 14, 2015)