Producing DRI in Bahrain: United Steel Company (SULB)
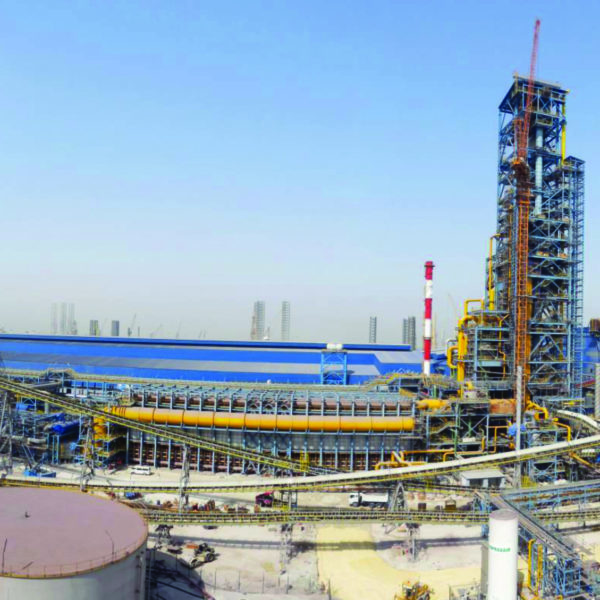
EDITOR’S NOTE:
In 2013, the Kingdom of Bahrain became the most recent country in the Middle East, North Africa (MENA) region to join the growing number of direct reduced iron (DRI) producing nations. Bahrain’s United Steel Company (SULB) signed a contract in March of 2010 with Midrex Technologies, Inc. and its parent company, Kobe Steel, Ltd., for supply of a MIDREX® Direct Reduction Plant having an annual capacity of 1.5 million metric tons with the capability to produce hot DRI (HDRI) and cold DRI (CDRI) simultaneously. SULB’s direct reduction plant was constructed in the Hidd Industrial Area adjacent to an iron ore pellet plant presently owned by Bahrain Steel and supplied by Kobe Steel. The DRI plant is instrumental in SULB’s vision to fill the void of medium and heavy section steelmaking capacity in the MENA region. This article looks at the construction and start-up of the SULB DRI Plant, as well as some of the unique project challenges and how they were solved.
BACKGROUND
In 2009, there was a lack of medium and heavy section steelmaking capacity in the area to support the significant growth that the Gulf Coast Region of MENA was experiencing. The Regional Industrial Investment Vehicle, Foulath, was interested in finding a partner with whom to develop such a business to fill this role. Yamato Kogyo, Ltd. of Japan, which has medium and heavy section experience and know-how, was interested in investing in the MENA region. As a result, the two parties formed a partnership, SULB, to develop a project to build the desired steelmaking facility.
Foulath already had interest in an iron oxide pelletizing plant at Hidd, Bahrain. The site had adequate adjacent land on which to build the proposed steel plant. The Hidd site has excellent access to both land and oceangoing transportation to the entire emerging GCC (Gulf Cooperation Council) market and when coupled with the pelletizing capacity immediately next door, proved to be an excellent location (see Figure 1).
After careful study of the market demand and other available steel capacity in the area, the decision was made to build an electric arc furnace (EAF)-based steel works capable of 900,000 tons per year of liquid steel and a heavy sections rolling mill with an annual capacity of 700,000 tons. SULB selected SMS Concast AG of Switzerland, SMS Meer GmbH of Germany and Samsung Engineering Co., Ltd. of South Korea to provide the EAF melt shop and heavy sections rolling mill.
As is the case with most integrated steel mills in MENA, SULB chose to include a direct reduction plant as the primary source of iron units for the EAF melt shop. A tender for the DRI plant was issued in January 2008, and based on the operational success of other MIDREX® Direct Reduction Plants in the MENA region, contracts were awarded in 2010 to Kobe Steel Ltd. and Midrex Technologies, Inc. for a 1.5 million tons per year DRI plant. The plant would be designed as a MIDREX® Combination Plant capable of simultaneous production of hot and cold DRI (HDRI and CDRI, respectively). During the design phase of the project, SULB elected to include an HDRI transport conveyor. Paramount to this decision was the successful operation and performance of the HDRI transport and handling system at Hadeed (Module E) installed in 2007 by Aumund Fördertechnik GmbH, in cooperation with Midrex and Primetals (formerly Siemens VAI).
The DRI plant follows the MIDREX NG™ flowsheet, which utilizes natural gas to create reducing gas for making DRI in the MIDREX® Shaft Furnace. The design basis summary of the plant is shown in Figure 2.
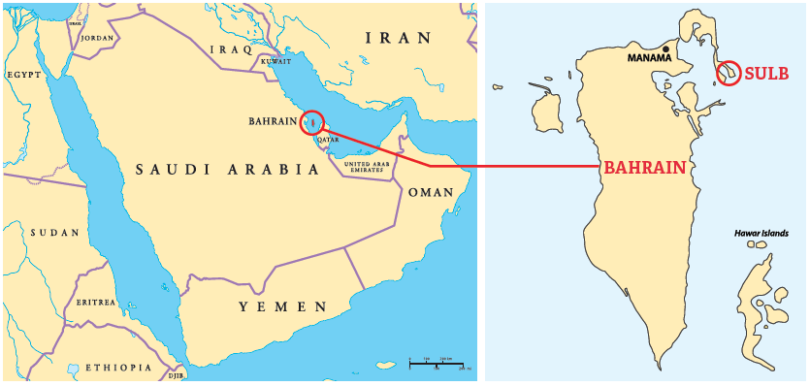
FIGURE 1.
SULB's location in Hidd, Bahrain
CHALLENGES AND START-UP
The SULB reformer was designed to be larger than MIDREX® Reformers at other comparably sized plants in order to better handle the unusually high nitrogen and carbon dioxide content of the incoming natural gas (>11 percent and >6 percent, respectively). Also, the natural gas source in Bahrain contains an average of 600 ppm sulfur, so a separate natural gas treatment process was required. A Merichem LO-CAT® processing unit was selected and included as part of the project scope.
In the MIDREX® Reformer, natural gas is heated and catalytically reformed along with recycled CO2 and H2O from the reduction process to generate a rich reducing gas.
As part of the MIDREX NG™ plant design, the reduction byproducts, CO2 and H2O, along with unreacted H2 and CO are recycled to minimize energy consumption and to produce additional reducing gas. In addition to providing reducing gas, the MIDREX® Reformer also supplies the energy needed for the reduction reactions within the MIDREX® Shaft Furnace.
By design, the MIDREX® Reformer is able to manage CO2 in the recycle gas in order to capitalize on the heating value of the recycle gas and generate more reducing gas. This means less natural gas is needed to produce the desired amount of reducing gas.
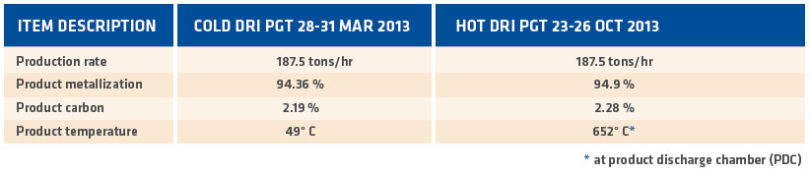
FIGURE 3.
Performance Guarantee Test Results
The recycle of byproduct CO2 from the reduction furnace creates an additional reforming reaction of CH4 + CO2 to produce 2H2 and 2CO, generating extra reducing gas for making DRI. The MIDREX® Reformer enables recycled gas and hot reformed gas to be fed to the shaft furnace without quenching and reheating, thus resulting in a very efficient process. This single component eliminates the need for a separate CO2 removal system and a process gas reheater, as well as the cost to build and operate these units.
Commissioning of the MIDREX® Plant was performed with no significant start-up issues. The performance guarantee test (PGT) was conducted only 30 days after provisional acceptance. The PGT, which was passed on the first attempt in only three days, proved that the DRI plant was ready for production. The PGT results are shown in Figure 3.
The DRI plant began commercial operation on 3 February 2013, producing only CDRI. As there was an immediate regional market for the CDRI, the plant was able to produce product and generate revenue while awaiting completion and commissioning of the melt shop and rolling mill.
HDRI production began in August 2013, following commissioning and completion of the PGT. Once stable operation was achieved, the actual simultaneous production of both CDRI and HDRI closely matched or exceeded both the guarantee values and the actual PGT values, as shown in Figure 4.
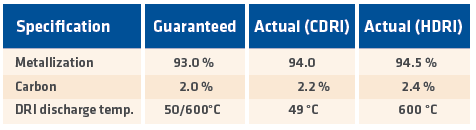
FIGURE 4.
DRI Product Quality While Simultaneously Producing CDRI and HDRI at Design Capacity (187.5tph)
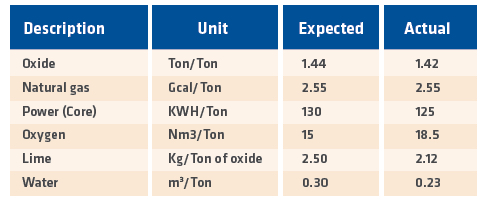
FIGURE 5.
Consumption Figures During Actual Operation
Consumption values had been a concern throughout the process evaluation and design phases of the project; therefore, SULB was very pleased that the actual values when operating were remarkably close to those expected for each constituent. Of particular interest was the improvement in iron oxide and water consumption, as shown in Figure 5.
The SULB DRI plant eclipsed design values within its first full year of normal operations. These improvements over design values have significant cost and environmental advantages especially considering the expected life of the MIDREX® Plant based on others in operation.
In addition to meeting and exceeding production milestones, the ability of the MIDREX® Plant to reliably and simultaneously produce HDRI and CDRI has been an important factor for SULB. This has allowed SULB to supply HDRI required by the melt shop while producing CDRI for both internal use and export. SULB has the option to vary production when and if necessary in response to market or melt shop conditions.
The splits for both production and use are shown in Figure 6.
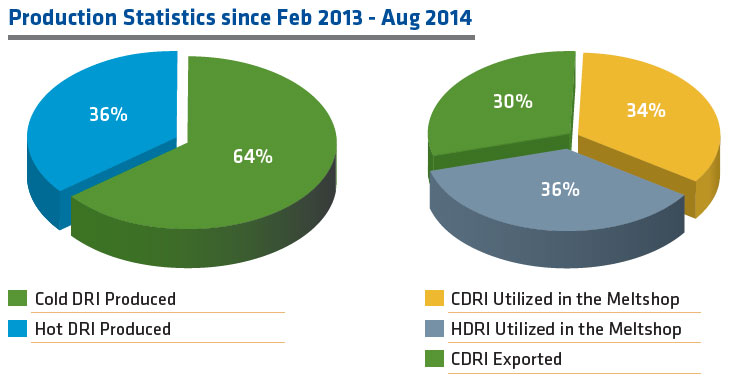
FIGURE 6.
HDRI & CDRI Production and Use
CONCLUSION
SULB’s MIDREX® Direct Reduction Plant was commissioned in 2013, adding Bahrain to the growing list of DRI producing countries in the MENA region. The Kobe Steel/Midrex project team and the client addressed unique challenges including varying natural gas specifications beyond the original project scope to add HDRI transport. Despite the challenges, SULB’s MIDREX® Plant began commercial operation on time and on schedule with no major start-up issues. The new DRI plant, with an annual capacity of 1.5 million metric tons, can produce hot DRI (HDRI) and cold DRI (CDRI) simultaneously. It is a key strategic factor in SULB’s efforts to fill the void of medium and heavy sections steelmaking capacity in the MENA region.
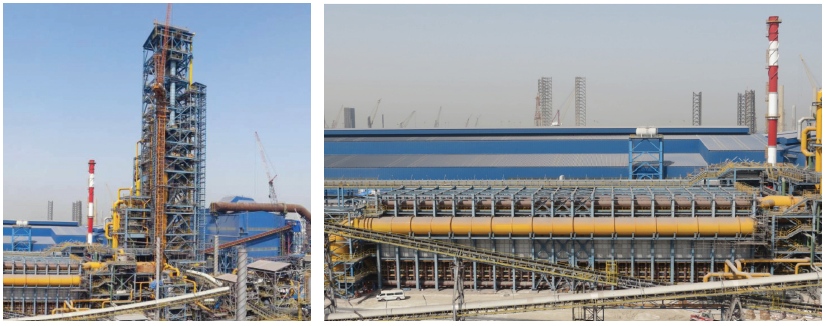