Midrex Provides SULB Operational Flexibility…
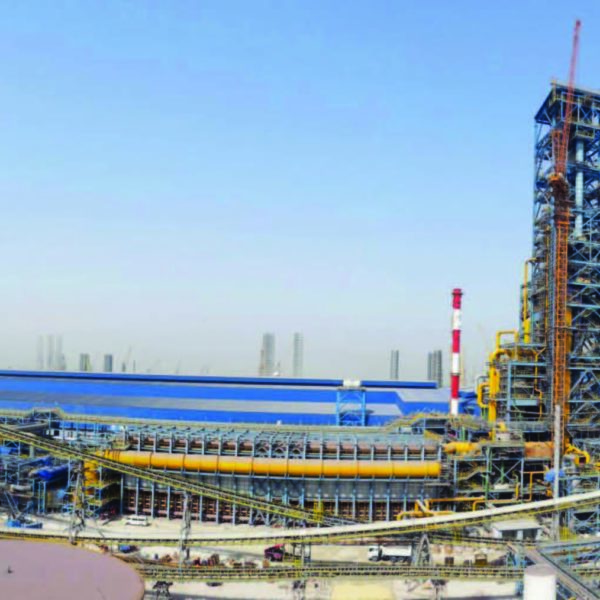
Teams with Kobe Steel to Solve Spikes in Natural Gas H2S Content
When Foulath of Bahrain and Yamato Kogyo Company Ltd. of Japan decided to have Kobe Steel Ltd. supply a 1.5 million ton/year MIDREX® Direct Reduction Plant for their joint venture steel project, Bahrain United Steel Company (SULB), they knew the plant would need a system to handle the hydrogen sulfide (H2S) in the natural gas they would receive. H2S content in the local natural gas at the time of the plant contract in 2010 ranged from about 350 to a maximum of 600 ppmv.
Feed gas to the reformer in the MIDREX® Direct Reduction Process needs to contain 2-5 ppmv of H2S – less than 2 ppmv may cause the catalyst to deposit carbon in the reformer tubes and reduce tube life; more than 5 ppmv may decrease catalyst activity and have a negative effect on reformer capacity. Therefore, due to the inherent natural gas quality in Bahrain, a LO-CAT® (a registered trademark of Merichem Company of Houston, Texas, USA) H2S Treatment System was included in the MIDREX® Plant design.
LO-CAT® is a patented, wet scrubbing, liquid chemical reduction-oxidation system that uses a chelated iron solution to convert H2S to safe, stable elemental sulfur. It does not use any toxic chemicals and does not produce any hazardous waste byproducts. The SULB system was designed to treat natural gas having H2S content of up to 600 ppmv by reducing the H2S to 5 ppmv or less. A diagram of the LO-CAT System is shown in Figure 1.
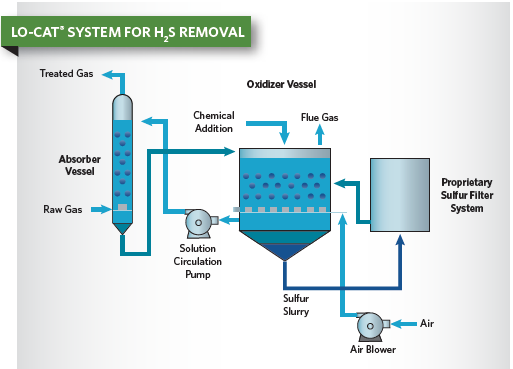
FIGURE 1.
Diagram of the LO-CAT® System for H2S Removal
Shortly after successful completion of the Plant Acceptance Test in February 2013, SULB brought to the attention of Kobe Steel Ltd. (KSL), the turnkey supplier of the MIDREX® Plant, that the H2S level in the natural gas being supplied was averaging 650 ppmv and had spiked as high as 900 ppmv. SULB requested KSL to provide a solution for handling H2S levels of up to 1000 ppmv.
SULFATREAT MEDIA & SYSTEM
KSL asked Midrex to determine the most effective technology for treating natural gas containing up to 1000 ppmv of H2S and design a system that would complement the LO-CAT System already installed and operating at the SULB site. The solution was SulfaTreat (a product of Mi-Swaco of Chesterfield, Missouri, USA), a non-hazardous granular material that can be used in a variety of configurations to remove H2S from natural gas streams through batch-processing treatment.
During the H2S removal process, gas flows through the consistently sized and shaped Sulfa Treat media, which is packed into a vertical pressure vessel where it chemically reacts with the H2S to form a stable, safe byproduct. The life of the SulfaTreat media depends on the amount of H2S that passes through the bed of the pressure vessel. This economically matches the need for H2S removal with variations in system flow conditions and outlet specifications, regardless of the total volume or other common components of the gas.
In the SulfaTreat system, iron oxide and the H2S in the gas stream combine in an electrochemical reaction to produce primarily iron pyrite (FeS2) and water (H2O). The reaction involves the transport of electrons promoted by the moisture layer on the SulfaTreat media, similar to a corrosion process. Water saturation is necessary for the Sulfa-Treat media to be effective. A lack of moisture will slow down the removal process.
To best accommodate the routine replacement of SulfaTreat media, the system is arranged in a lead-lag bed arrangement; i.e., in series (Figure 2).
When the sulfur removal capacity of the lead bed is exhausted, it is isolated and the lag bed remains in service while the media is replaced in the lead bed. After the media is replaced, both beds can be brought online and the lag bed becomes the lead bed, and the cycle is repeated.
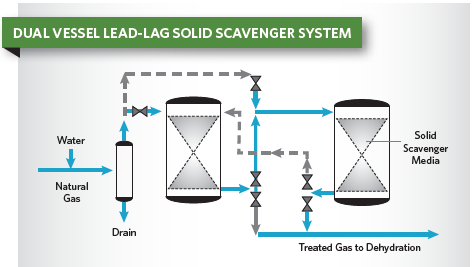
FIGURE 2.
Diagram of the SulfaTreat Lead-Lag System for H2S Removal
DESIGN CASES
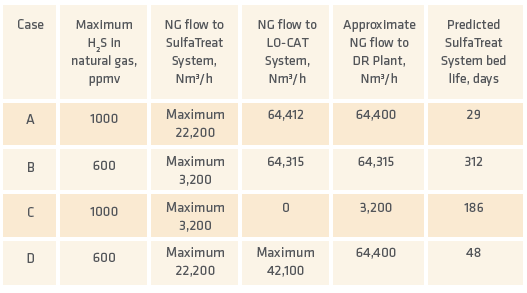
TABLE I. Four design Cases for SulfaTreat System at Sulb
Case A is a series operation. It assumes the approximate natural gas flow to the DR plant to be 64,400 Nm3/h and ensures a maximum of 657 ppmv of H2S is delivered to the existing LO-CAT System, which has previously demonstrated the ability to operate acceptably at this inlet H2S level. This amounts to 1.43 metric tons of sulfur removed per day from the load on LO-CAT. The natural gas pressure conditions at the inlet of LO-CAT are similar to the current operating conditions (approximately 17 barg +/- 0.5 bar).
Case B also is a series operation and assumes a minimum flow rate of natural gas to the SulfaTreat System while the LO-CAT System is in operation.
Case C is neither a series nor a parallel operation case. Similar to Case B, it assumes a minimum flow rate of natural gas to the SulfaTreat System, but the LO-CAT System is offline in Case C. In this case, the natural gas to the DR Plant is used to fire the auxiliary burners only.
Case D is a parallel operation case. It assumes that the LO-CAT System is limited in the flow rate of natural gas that it can receive at its inlet. For this case, a new bypass line around LO-CAT was required.
ASSURING SUSTAINABLE OPERATION
SULB owns and operates a “combination plant,” the latest plant design from Midrex. A combo plant, as it is known, includes a hot discharge MIDREX® Shaft Furnace that is configured for simultaneous discharge of cold DRI (CDRI) and hot DRI (HDRI). The plant is equipped with one of several hot transport systems available from Midrex to retain the sensible heat in the HDRI while it is transported to the melt shop (Figure 3).
The 1.5 million ton per year combo plant was started up in January 2013 producing CDRI to feed the SULB steel mill. In mid-August 2013, the HDRI transport system to deliver HDRI to the steel shop was commissioned.
The SULB steel works is located in Hidd Industrial Area, adjacent to a two-plant 12 million t/y pelletizing operation owned by Gulf Industrial Investment Company (GIIC). Oxide pellets used in the DRI plant are purchased from the GIIC facility, both plants being supplied turnkey by KSL. Plant 1 was started up in 1984, with a design capacity of 4 million t/y and was upgraded in-house to 5 million t/y in 2007. Plant 2 began commercial operation in early 2010, with a design capacity of 6 million y/y and is capable of producing 7 million t/y.
Natural gas for the SULB works is supplied by Bahrain Petroleum Company (BAPCO). This is associated petroleum gas (APG), or associated gas, which is found with deposits of petroleum, either dissolved in the oil or as a free gas above the oil in the reservoir. APG typically was released as a waste product by the petroleum extraction industry until the advent of direct reduction technology, which transforms it into useful process gas.
As SULB found out, the chemical composition of APG can fluctuate, especially the H2S content, which can have a detrimental effect on the operation of a DRI plant reformer. Now that the Sulfa-Treat system has been installed to complement the LO-CAT System (see Figure 4), SULB has the flexibility to operate in the most cost-effective way regardless of the H2S level coming from BAPCO in the APG.
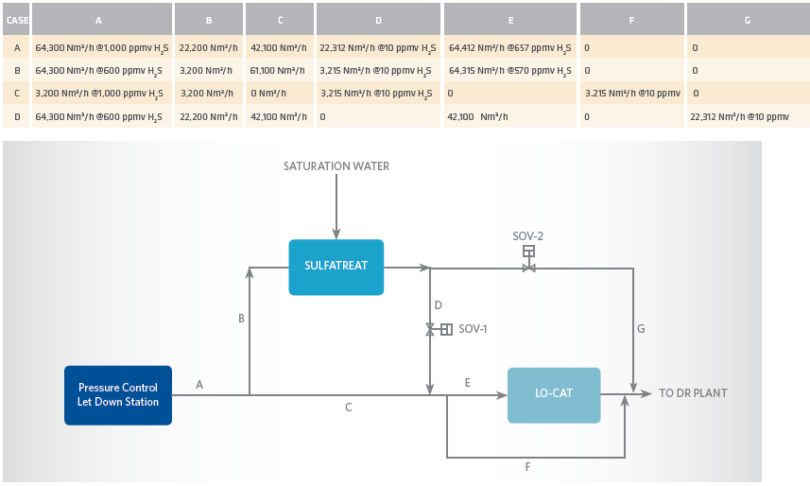
FIGURE 4.
Diagram of Parallel Installation of SulfaTreat and LO-CAT Systems
MIDREX GLOBAL SOLUTIONS
How well a plant is maintained and serviced is instrumental in determining its performance, reliability, and longevity. The larger the capital investment, the more important the selection of an aftermarket services provider becomes.
Midrex Global Solutions (MGS), as its name represents, does more than provide spare parts and materials. It takes a broad, in-depth approach to the needs of Midrex customers and develops comprehensive solutions based on the knowledge, expertise and experience of Midrex and its family of Process Licensees.
MGS is the latest in the natural progression of customer service functions that has evolved as the number of MIDREX® Plants has increased globally. For the first 20 years, Midrex primarily provided technical advice and managed the transfer of technology. In 1990, Professional Services International (PSI) was established as a subsidiary of Midrex to provide procurement and logistics services to KSL, the parent company of Midrex, as well as to supply spare parts to MIDREX® Process Licensees. The decision was made in 2004 to integrate PSI into Midrex, and Midrex Solutions was formed soon thereafter (later renamed Midrex Global Solutions).
Within a MIDREX® Plant, MGS is capable of servicing a wide range of production and maintenance operations. These activities include designing engineered solutions, managing maintenance, repair and operation (MRO) programs, sourcing and procuring spare parts and materials, and providing field services. The successful SulfaTreat project for SULB is an excellent example of the capabilities of MGS.