Iron and Steel Production Considerations for Navigating the EU Low Carbon Roadmap
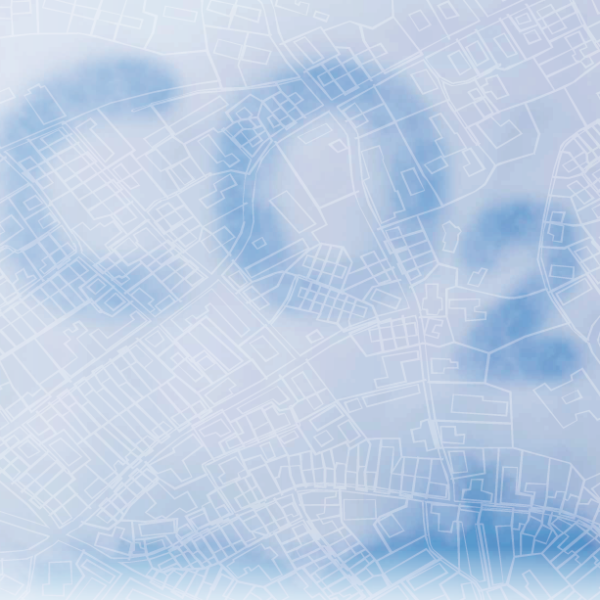
EDITOR’S NOTE:
Adapted from a paper by T. Buergler, J. Prammer and R. Hackl, voestalpine Stahl GmbH, Austria, and B. Kohl, voestalpine AG, Austria, titled Raw materials and technologies for Iron and Steelmaking under the aspects of the EU Low Carbon Roadmap
Over the past 15 years, the transformation of our rapidly growing global society to a low-carbon based production economy has been a hot topic of discussion. The intention is for 80% of the CO2 reduction to come from new concepts and approaches with the remaining 20% coming from process development. The larger fraction of the reduction (80%) can only be achieved by a transfer of global energy/power production away from carbon containing fuels. Since this falls outside the direct influence of the iron and steel industry, we must focus on the process improvements portion of the reduction (20%).
While there is no immediate known and proven path to totally eliminate carbon from the iron and steel production cycle, the use of natural gas, (i.e., bringing more energy into the cycle via hydrogen versus carbon), can act as a bridge technology for the transfer between carbon and non-carbon based energy systems. Use of HBI and DRI produced with natural gas allows flexibility for the EAF steel production route as well as for the integrated BF/BOF steel production.
Thus far efforts to reduce carbon usage and CO2 production since the beginning of the 21st century have reduced the European Union (EU) share of CO2 production to approximately 10% of the world total. Notwithstanding this, each country and every company therein has its own timeline for reducing CO2 intensity, and plant life cycles and the speed at which carbon-lean energy sources are adopted must be considered.
Within the last 50 years, energy consumption by industry has been reduced by 30%, and the main driver behind it has been technology development. Now the thermodynamic limits are close to the consumption levels and it will become more difficult to achieve further significant reduction levels. Therefore, we must look to better use clean energy sources, such as natural gas, to supplement production technologies.
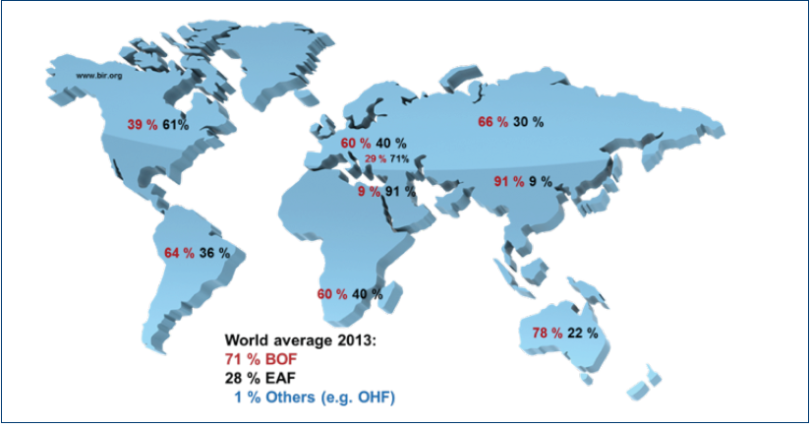
FIGURE 1.
Regional difference of production processes
IRON AND STEEL TECHNOLOGY
Steel is essential to the modern world. Thanks to its strength and its properties of formability, steel is one of the most versatile and adaptable engineering materials available. It is the material of choice for a wide range of applications ranging from the construction of bridges and buildings, to automotive and machine parts, as well as food packaging, power generation and aerospace engineering. The major end use industries include construction (35%), automotive (18%) and mechanical engineering and metal goods (each 14%). Steel’s recyclability also makes it a key material for sustainable development [1].
There are two general methods of crude steel production in use in the 21st century: the basic oxygen furnace route (BOF) and the electric arc furnace route (EAF), as shown in Figure 1. The BOF route converts iron ores to steel via blast furnaces (BF) or smelting reduction (SR) processes and basic oxygen furnaces (BOF). The EAF route converts steel scrap and/or direct reduced iron (DRI) and/or hot briquetted iron (HBI) from direct reduction (DR) processes to steel via electric arc furnaces (EAF).
Iron ores, which are iron oxides with an iron content of 60% or greater, must first be reduced into iron by removing the oxygen bound to the iron either by melting in the BF or with the help of reducing agents, mainly carbon monoxide (CO) and hydrogen (H2) in a DR process. Iron reduction is the most energy intensive step in the steel production process, consuming approximately 90% of the primary energy required to make steel. EU crude steel production is today almost evenly divided between the BF-BOF and the Scrap-EAF routes. In 2013, BF-BOF accounted for 60% of EU27 production and Scrap-EAF the remaining 40%. Although other iron and steel production processes, such as the COREX®/FINEX®-BOF route or the DR/EAF route are used in different parts of the world, they have little to no significance for the EU [2].
The most common primary production route uses the blast furnace (BF) in combination with the basic oxygen furnace (BOF). The best available technology (BAT) benchmark in Europe for emission of the blast furnace route is 1,475 kg CO2 per ton crude steel (CS). Due to continuous optimization, the industry is already approaching the theoretical minimum of 1,371 kg CO2 / tCS. Therefore, further substantial emission reduction is only possible through the implementation of new breakthrough technologies. Key areas of process development are Carbon Capture and Storage (CCS) or Use (CCU) in combination with fossil fuels and hydrogen as innovative reducing agents for the reduction process [1].
REDUCTION OF CO2 INTENSITY
Depending on the separation of iron and oxygen, the iron and steel industry is one of the more energy-intensive industries. It is expected to contribute to the climate targets and to reduce greenhouse gas emissions (GHG) significantly by 2050. For example, the German iron and steel industry consumed 6% (554 PJ) of the total German end-use energy demand and caused 4% (41 Mt CO2) of the total GHG emissions in 2011 [3]. Since the pre-industrial era, the concentration of GHG in the atmosphere has risen steadily from below 300 ppm (1900) to 400 ppm in May 2013 [4], as shown in Figure 2.
In order to maintain a chance to keep global warming below 2.1° C compared with the pre-industrial age, the maximum threshold is considered to be 450 ppm; however, this would be reached in 30 years at current emission reduction levels. Drastic emission reduction is necessary across the world to achieve this target. As suggested by the Intergovernmental Panel on Climate Change (IPCC) for developed countries, the EU targets a reduction in GHG emissions of 80-95% by 2050. This target is in line with the recommendations to decrease global emissions by 50%.
That roadmap for a competitive low-carbon economy by 2050 requires examination of possible cost-efficient paths toward reducing EU domestic greenhouse gas emissions by 80% by 2050 (Figure 3).
According to the commission’s report, European industry would have to cut back its emissions below 1990 levels by 34- 40% by 2030 and by 83-87% by 2050. In this context, the commission and the European Parliament invited industrial sectors to develop their own low-carbon roadmap.
Studies confirm that the EU commission target without a radical transfer of the energy systems is far beyond the reach of the steel sector. From an economic perspective, only 10% emissions reduction per ton of steel is possible between 2010 and 2030 and 15% between 2010 and 2050. Also, there is very high potential for CO2 mitigation from innovative technologies in which steel cannot be replaced by any other material, indicating that European climate targets hardly can be reached even without considering steel production [5].
CO2 trend in the atmosphere [4]
FIGURE 2.
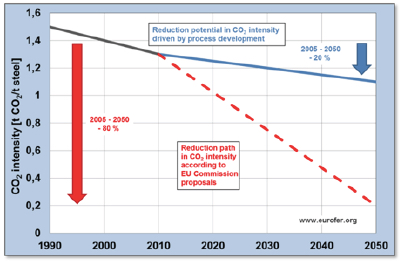
FIGURE 3.
CO2 reduction path in the EU Roadmap [5]
STEEL INDUSTRY TECHNOLOGY TREND
If the steel industry is to continue producing in Europe and retaining its global competitiveness while “de-carbonizing” its operations, substantial research must continue into carbon-lean technologies. Further major reduction in emissions has been the subject of a number of scientific studies and programs in recent years. The ULCOS program, set up in 2004, has made a major contribution to the issue. The initiative, which includes major European steel producers, was supported by the European Commission. It has evaluated the technical CO2 reduction potential of over 80 existing and potential technologies, out of which it identified technologies with a long-term emissions reductions potential of more than 50%. These include the blast furnace with top gas recycling (BF-TGR), bath smelting (HISARNA) and direct reduction. These technologies must be investigated further in R&D programs including pilot and demonstration plants. All breakthrough technologies rely on the development of CCS and/or the transfer from carbon to hydrogen as reducing agent to unfold their full abatement potential (Figure 4).
In future decades of this century, the traditional model of the integrated steelworks (i.e., taking in iron ore as a raw material and reducing it to metallic iron) will come under great challenge (Figure 5). Since the year 2000, the amount of steel made per year has doubled from 800 Mt to 1.6 Bt, but there is something quite important about the last 15 years of steel production compared with everything that came before.
Fifteen years is about the time required for steel products to enter into the scrap cycle [6]. Starting from scrap and using the electric arc furnace (EAF) rather than the blast furnace to make steel could result in a significant change in the carbon footprint of the steel production cycle. However, as long as scrap remains fairly scarce, production economics will tend to favor the BF-BOF route. But what happens when new steel enters the scrap cycle and a transfer from carbon to renewable energy takes place? There could be a shift towards EAF metallurgy for new units and a more or less constant level of BF-BOF units.
![FIGURE 4 Ironmaking Technology with CCS [5]](https://www.midrex.com/wp-content/uploads/FIGURE-4-Ironmaking-Technology-with-CCS-5-e1606331436189.png)
FIGURE 4.
Ironmaking Technology with CCS [5]
COMBINATION OF PROCESS ROUTES
There are two primary limitations related to replacing carbon intensive steel production: plant lifetime and the availability of carbon-lean energy. Iron and steel production units have lifetimes measured in decades. Almost all existing blast furnace plants in the world have the latest technical standards and will remain in production until the middle of the century. Therefore, a technology change can be implemented only when a new investment is planned. The DR/EAF route could be a new approach for an integrated plant in the future.
The availability of renewable or carbon-lean energy on a continuous basis for more than 8,500 hours per year is not entirely within the influence of the metallurgical industry. Today we have technologies available to reduce the CO2 intensity further, but every company and country has its own timeline for this process.
Considering all these trends in iron and steel metallurgy in the next few decades, the question becomes what is now the best available technology for a new production unit? A possible answer can be found in the decision by voestalpine to build an HBI plant in Texas, USA, to produce iron metallics for its BF-BOF steelworks in Europe, as well as to be a source of merchant product to sell to other steelmakers (Figure 6). The 2.0 Mtpy MIDREX® Direct Reduction Plant designed to produce HBI, is the largest of its kind in the world, and is seen as a landmark development. The start-up is planned the first half 2016. US natural gas prices were a key factor in the decision.
The potential for HBI to be used in the BF-BOF steelmaking route, rather than just in EAF-based steelmaking, could work to the advantage of European iron and steelmakers under the target of CO2 reduction. The use of HBI to boost BFs with limited hot metal capacities while contributing to a smaller carbon footprint of an integrated steelworks could prove attractive to other steelmakers worldwide (Figure 7). This story is not new. HBI has been used successfully by steelmakers in the USA in BF-BOF steel making for 25 years, so there is no technology risk associated with using it compared with breakthrough technologies like TGR-BF and Smelting Reduction.
![FIGURE 5 Developments in world steel production [6]](https://www.midrex.com/wp-content/uploads/FIGURE-5-Developments-in-world-steel-production-6-e1606331539700.png)
FIGURE 5.
Developments in world steel production [6]
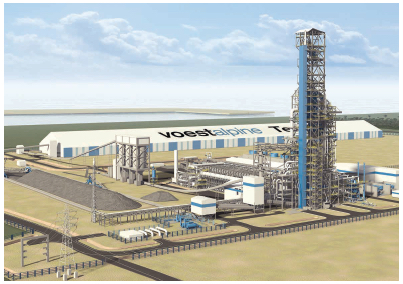
FIGURE 6.
Rendering of HBI plant in Corpus Christi, TX
CONCLUSION
The transformation of our society to a low carbon based production economy is an inevitability which the steel industry must face. The European Union crude steel production is today almost entirely divided between the BF-BOF and the Scrap-EAF routes. Depending on the separation of iron and oxygen, the iron and steel industry, which is one of the most energy-intensive industries, is expected to contribute to achieving climate change targets and to reducing GHG emission significantly by 2050. All breakthrough technologies developed by programs like ULCOS rely on the development of CCS and/or the transfer from carbon to hydrogen as reducing agent to unfold their full abatement potential. The use of clean-burning natural gas can act as a bridge technology for the transfer between the energy systems. Direct reduction and HBI allow broad flexibility for the EAF steel production route, as well as for integrated BF-BOF steel production in the quest to reduce CO2 intensity.
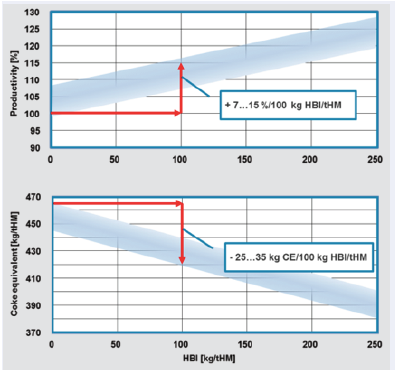
FIGURE 7.
HBI as input material in the BF process
Abbreviations
EU European Union
BF Blast Furnace
BOF Basic Oxygen Furnace
DR Direct Reduction
EAF Electric Arc Furnace
DRI Direct Reduced Iron
HBI Hot Briquetted Iron
GHG Greenhouse Gases
BAT Best Available Technology
CCS Carbon Capture and Storage
CCU Carbon Capture and Use
IPPC Intergovernmental Panel on Climate Change
ULCOS Ultra Low CO2 Steelmaking
References
[1] Lüngen, H.-B.; Ghenda J.-Th. et al.: Steel’s Contribution to a Low-Carbon Europe 2050 Technical and economic analysis of the steel sector’s CO2 abatement potential; ECSC 2014
[2] Bureau of International Recycling: World Steel Recycling in Figures 2009 – 2013, Brussels 2014
[3] Fischedick, M.; Marzinkowski, J. et al.: Techno-economic evaluation of innovative steel production Technologies; Journal of Cleaner Production 84 (2014)
[4] U.S. Department of Commerce, National Oceanic and Atmospheric Administration, Earth System Research Laboratory, Global Monitoring Division
[5] European Parliament: Making the Grade ,Steel Roadmap for a Low-carbon Europe 2050; Parliament Magazine, October 2013
[6] Allwood, J.: New Mindset for Material Efficiency and Reduced Energy Demand; ECSC 2014