Hot Briquetted Iron: Steel’s Most Versatile Metallic in the Transition to the Hydrogen Economy
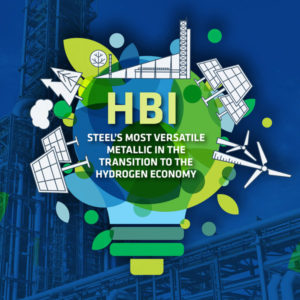
INTRODUCTION
It is difficult to have a conversation in the steel industry today without the word “hydrogen” coming up and how hydrogen will be used to decarbonize the steel industry. Much is being said and written about needing to achieve carbon-neutrality by 2050, as well as the many challenges and obstacles to reaching that goal. But few suggestions are being offered for what can be done in the immediate future to lower CO2 emissions that will have the least impact on the financial sustainability of steelmakers – especially those operating traditional integrated mills ( e oven/blast furnace/basic oxygen furnace) to produce high quality metallic iron for steel production.
Carbon-neutral steelmaking is coming, but it will not happen overnight. It will take time for steel producers to adapt their standard operating procedures to the new reality of hydrogen steelmaking. For BF/BOF steelmaking, gradual decarbonization by using natural-gas based Hot Briquetted Iron (HBI) is the most immediate and effective method for reducing CO2 emissions now available to the steel industry. HBI use will not only reduce CO2 emissions but also increase BF productivity.
This article will talk briefly about longer term plans for decarbonizing the steel industry with hydrogen and the challenges associated with it but will focus on how HBI, already regarded as “steel’s most versatile metallic,” is contributing to efforts to reduce CO2 emissions and could do more moving forward toward the Hydrogen Economy.
THE CARBON CHALLENGE
Carbon has been used for centuries to make steel, and for a good reason – it is the alloying element in producing steel from iron (Fe). Carbon (C) and oxygen (O2) are used to provide the energy and lower the melting point and therefore, the energy required to melt the iron. So, it’s a thermodynamic fact that some form of carbon is going to be required to make steel (see Figure 1). That is one reason why carbon-neutral steelmaking is a more accurate term and a lot more likely to be achieved as hydrogen is increasingly used in basic steelmaking.
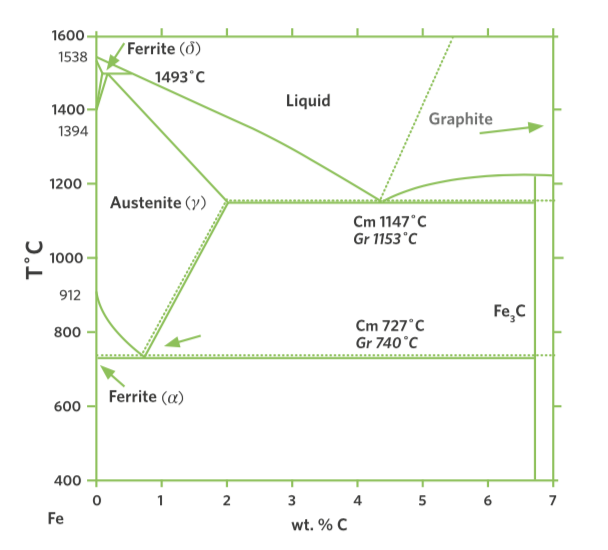
FIGURE 1.
Thermodynamics of Steelmaking
On a macro basis, there are three ways to lower the CO2 emitted during iron and steel production:
- reduce energy consumption so less energy (and carbon) is required per ton of steel
- sequester the CO2 underground, either in storage or for enhanced oil recovery
- use an energy source with less carbon than coal
Option 1 has been a serious focus for many years. Since 1980, the USA steel industry has reduced energy consumption per ton of steel by almost 50%. However, further gains are increasingly difficult, as the processes become more and more efficient.
Option 2 is being developed, and has great promise. However, there are practical limitations, environmental issues, and political entanglements to overcome.
Option 3 may be the most promising and practical solution for significantly reducing carbon emissions in the near-term. Clean-burning natural gas is an attractive alternative energy source and reductant to coal and rate.
All of the energy sources currently used for ironmaking – except natural gas – share an important characteristic: they are comprised almost totally of carbon and generate lots of carbon dioxide as a by-product. Traditional coke-based ironmaking produces from 1.6 to 2.2 tons of CO2 per ton of iron. On the other hand, natural gas, which is primarily methane (CH4), has four hydrogen atoms for each carbon atom and therefore, a higher proportion of carbon-to-hydrogen. Since almost all the carbon and hydrogen used in an iron and steelmaking facility is eventually converted to CO2 and H2O (water), natural gas produces much less CO2 than does coal.
Table I shows the CO2 emission rates for combusting methane versus two types of coal.
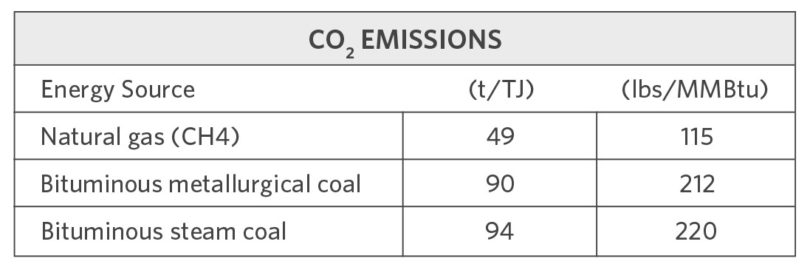
TABLE I.
CO2 Emissions for Iron and Steelmaking Energy Sources
As the table shows, natural gas emits only about one-half the CO2 per unit of energy as does coal. When iron is reduced with coke or charcoal, each atom of oxygen in the iron oxide (iron ore) requires one atom of carbon. In a blast furnace, the carbon from the coke or charcoal is first partially oxidized to carbon monoxide (CO) using gaseous oxygen (O2). The oxygen is provided by blast air (heated air enriched with additional oxygen) then injected into the blast furnace at the tuyeres. The carbon monoxide diffuses into the highly porous ore and collects an additional oxygen atom from the iron oxide, creating metallic iron (Fe) and forming carbon dioxide (CO2).
When methane is used, each molecule of CH4 is first reformed into one carbon monoxide molecule (CO) and two hydrogen molecules (H2). Each of these three molecules will take one oxygen atom from each molecule of CH4, and each of these three molecules will take one oxygen atom from the iron oxide. So, the products of the reduction reaction are two water molecules (H2O) and one carbon dioxide molecule (CO2). In other words, only one-third as much CO2 is generated.
“If it were possible to produce the entire world’s iron with natural gas direct reduction plants, over one billion tons of CO2 could be avoided per year.”
– Robert Hunter, 3-4Q2009 Direct From Midrex
HYDROGEN-BASED DIRECT REDUCTION
Before talking specifically about HBI and how it can contribute to a reduction in CO2 emissions, let’s briefly look at using hydrogen to produce DRI products (cold DRI [CDRI], hot DRI [HDRI], and HBI) and some of the major challenges that this route has before it is viable.
MIDREX® Plants already use ~55% hydrogen in the reducing gas, with some plants using up to 80% H2. The hydrogen is derived from the reforming of natural gas.
Figure 2 and Figure 3 show flowsheets that illustrate the near-term transition to H2 addition in a MIDREX NGTM (natural gas) Plant and the future use of 100% H2. In Figure 2, a desired amount of additional hydrogen is introduced. The key piece of equipment to highlight is the MIDREX Reformer, which performs two major functions: 1) reforming the natural gas and CO2 to H2 and CO, and 2) heating the reducing gas. The reformer is adaptable for the entire transition from 0% H2 up to 100% H2 – it becomes purely a heater when using 100% H2 (see Figure 3).
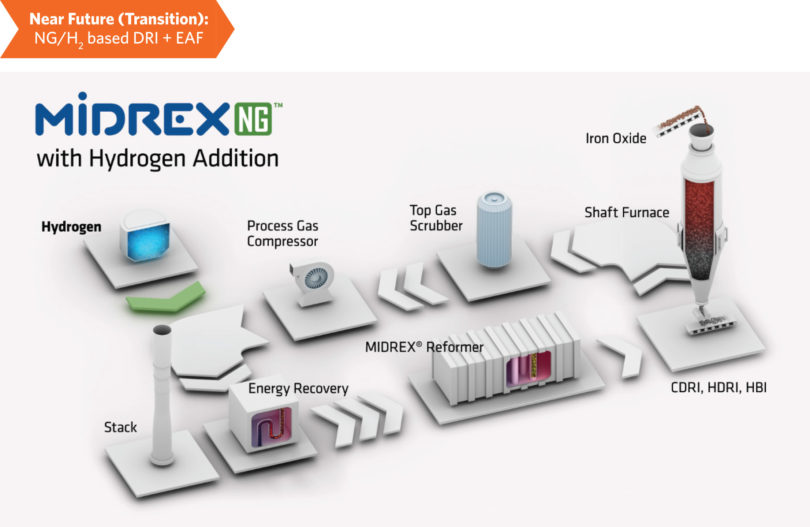
FIGURE 2.
MIDREX NG with Hydrogen Addition
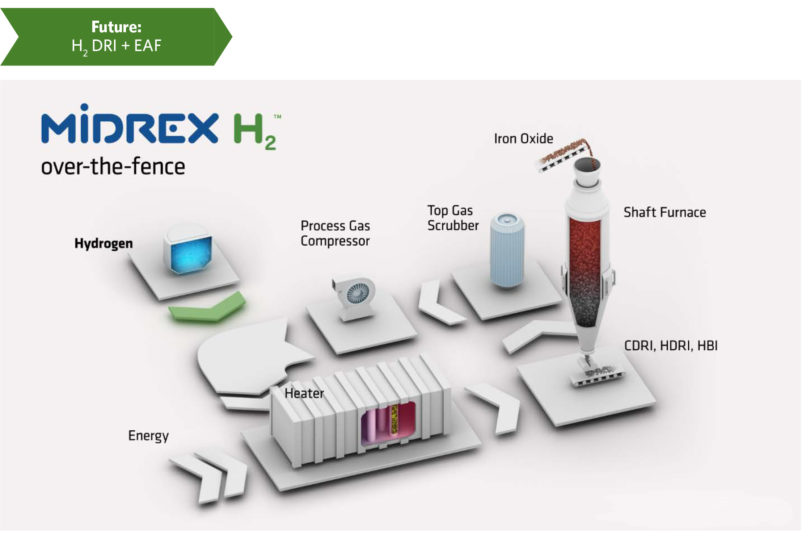
FIGURE 3.
MIDREX H2
The flowsheet in Figure 3 is for a plant designed from the beginning to operate with 100% hydrogen – known as MIDREX H2TM – and shows the Reformer being replaced with a Heater. The flowsheet is basically the same and includes the same equipment, but the design basis for some equipment has changed. Hydrogen has a lower molecular weight than the typical process gas in a MIDREX NG Plant, so the Process Gas Compressors will be modified. The design of the Top Gas Scrubber is modified to handle the additional water being condensed out of the top gas from the furnace due to the higher percentage of hydrogen. Also, the design of the heat recovery is optimized for a given set of operating conditions that will change as the MIDREX Process transitions to 100% H2.
The expected consumption of hydrogen in a MIDREX H2 Plant is 600-650 Nm3/t DRI (54-58 kg/t DRI) for process requirements only. Therefore, a 2.0 million tons/year plant would require an 800 MW electrolyzer – electrolyzer capacity that has yet to be demonstrated commercially (assuming 200 Nm3/h of H2 per 1 MWh).
It’s not that electrolyzer technology is not available; it’s the manufacturing of the equipment that is lagging. Current manufacturing just can’t support this level of production. Also, the cost of electrolysis units is still very high and there is a wide range among suppliers.
When the capital cost of electrolyzers and the current price of electricity are looked at together (Figure 4), it is obvious that significant improvements are required to make hydrogen-based iron and steelmaking the economical choice.
Given these figures, the price of hydrogen would need to be below $0.50/kg to be competitive with a natural-gas based MIDREX Plant (assuming a natural gas price of $4.0/MMBtu).
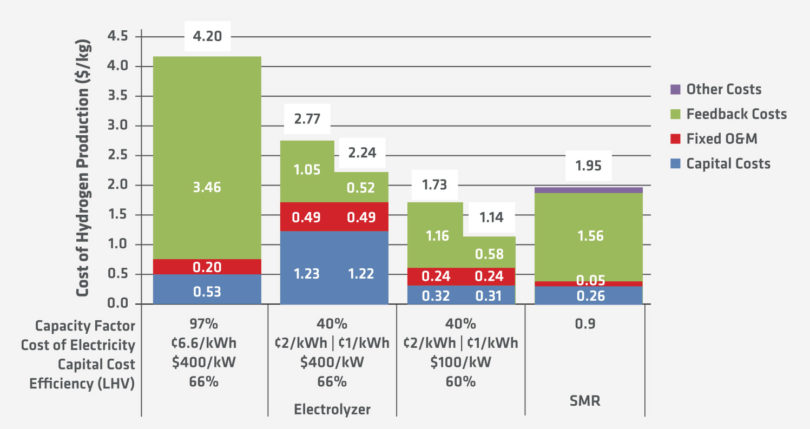
FIGURE 4.
Cost Challenge of H2 Iron & Steelmaking (1)
“Natural gas is hydrogen in disguise.”
– Lourenco Goncalves, CEO, Cleveland-Cliffs, Inc.
A PRACTICAL WAY TO KEEP BFS OPERATING
A report issued in June 2021 by Global Energy Monitor, recommended that three main targets need to be met by the global steel sector to align with the goal for mid-century global energy net-zero carbon emissions:
- Steelmaking capacity needs to be aggressively shifted from the dominant blast furnace-basic oxygen furnace (BF-BOF) steelmaking route to electric arc furnace (EAF) steelmaking.
- All remaining BF-BOFs need to be outfitted with best available technology (BAT) or retired; and
- Novel low-emissions and net-zero steelmaking technologies, including hydrogen-DRI production, need rapid development, scaling up, and deployment.(2)
Replacing the BF/BOF steelmaking route with DRI/EAF would significantly reduce CO2 emissions, but the capital expenditures would be enormous, not to mention the disruption due to construction time, learning curves, and the required shifts in corporate cultures. However, keep in mind that in order for iron and steelmaking to be carbon-neutral, the power source also needs to be carbon-neutral – and that is even a bigger challenge than decarbonizing the steel industry.
The use of HBI in the BF to reduce CO2 emissions should be considered Best Available Method (BAM) if not Best Available Technology (BAT). It has been proven to reduce CO2 emissions 20% or more.
HBI is the densified form of DRI that is ideal for ocean carriage due to its resistance to water pick-up (reduced risk of oxidation) and for use as a metallic charge to the BF and BOF due to its increased mass and density. HBI is made by compressing DRI discharged hot (≥ 650° C) into pillow-shaped briquettes typically 30x50x100 mm in size with a density of ≥ 5 g/cm3. No binder is required in the production of HBI by the MIDREX Process.
HBI has been around for decades but its full impact is just beginning to be realized by the steel industry. Environmental and productivity gains using HBI in the various steel production routes are well-documented. Typically, HBI contains over 90% Fe (with metallization up to 96%) and therefore, these metallics do not require further reducing in the BF; they only need to be melted. In addition to providing a method to reduce CO2 emissions, charging HBI into a BF is a way to increase productivity when a steel mill either needs to make up for a shortage of hot metal demand in relation to the BF/caster capacity or to provide sufficient hot metal during a reline or repair of a BF. In fact, using HBI in the BF charge may be the best chance to keep some integrated steel works in operation for years to come.
HOT BRIQUETTED IRON USE IN THE BF
The parent company of Midrex, Kobe Steel, Ltd. (KSL), has combined the direct reduction technology of Midrex and the KSL engineering business with the blast furnace operation technology and know-how of Kobe Steel’s iron and steel business to demonstrate an enhanced method of BF operation. The KSL technology envisions charging up to 30% HBI produced with a hydrogen-rich gas to significantly lower coke rate and thus, reduce CO2 emissions (Figure 5).
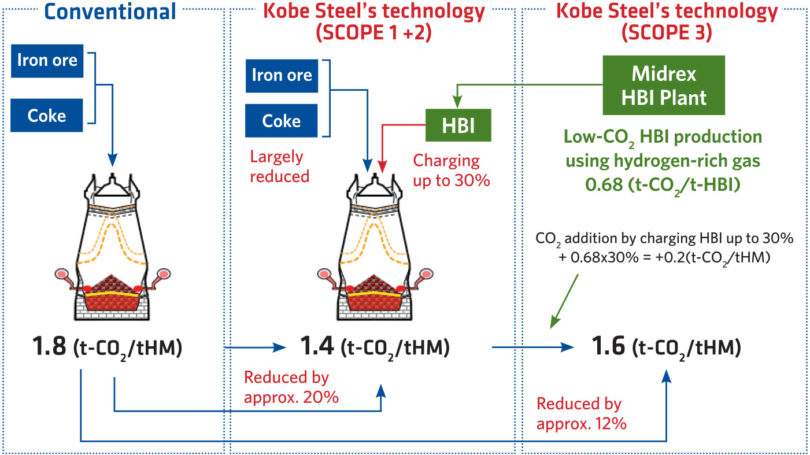
FIGURE 5.
Kobe Steel Technology for BF Operation with HBI Produced with Hydrogen-rich Gas (3)
KSL recently performed a demonstration using 305 kg of HBI per ton of hot metal (THM), which translated into a 20% reduction in the reducing agent rate from 518 kg/THM to 415 kg/ THM (Figure 6).
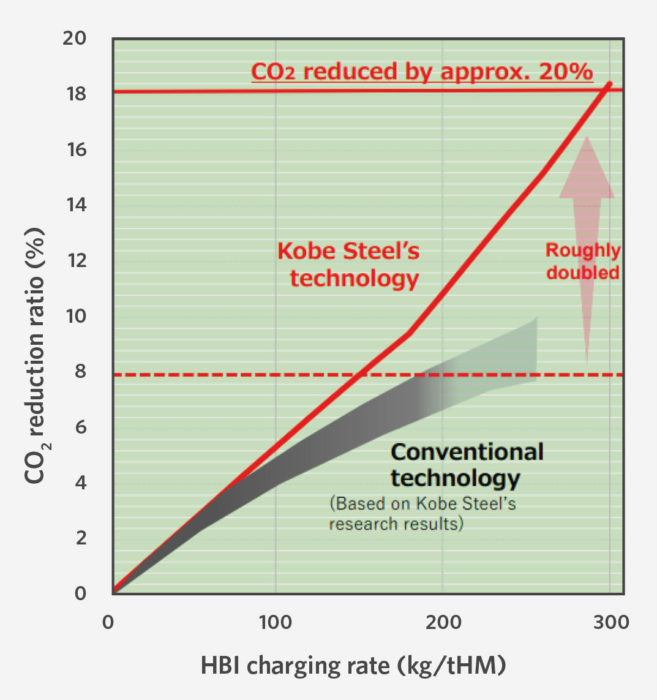
FIGURE 6.
CO2 Reduction in BF Operations (3)
The coke rate was reduced during the demonstration test by 85 kg/THM, to a world’s lowest level of 239 kg/THM (Figure 7). The coke rate was an improvement of more than 20% over the previous test with HBI, which lowered the rate by 34 kg/ THM. With coke priced at $400/t, that is a savings of $32/THM in coke alone.
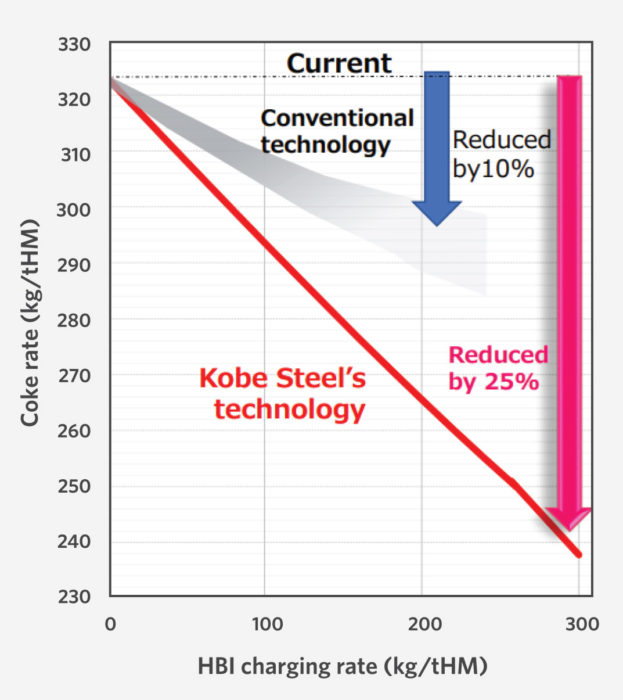
FIGURE 7.
Reduction in Coke Rate Using HBI (3)
An example of how HBI is being used in BFs and the benefits it provides is voestalpine in Linz, Austria, which uses HBI from its own plant in Corpus Christi, Texas, USA, (Figure 8) in its blast furnaces.
The use of different charging rates of HBI in the Linz BFs was examined over the period from 2017-01-01 to 2018-01-31 based on daily average data. When 100 kg HBI/t HM is charged to the BF, the following conclusions can be drawn:
- Reducing agents (CE) can be decreased by 21.9 – 27.5 kg/t HM, whereas the coke rate can be decreased by 10.9 – 18.1 kg/t HM.
- Productivity can be increased up to 7.3 – 10.1% at constant oxygen levels.
- Gas utilization drops by approximately 0.4 – 1.1% because HBI is a pre-reduced material and less oxide is charged to the BF. The decrease in quantity of charged oxide also reduces the quantity of CO and H2 which are transformed into CO2 and H2O.
- The calorific value of top gas rises by 12.3 – 23.5 Wh/Nm3 due to the higher contents of CO and H2.
- A correlation between the top gas temperature, cooling apacity, and permeability and the use of HBI cannot
be seen. - The S-content of hot metal is lower and C-content higher (high quality) with a charge of 100 – 150 kg HBI/t HM compared to when no HBI is charged. The S- and C-content in hot metal does not depend only on the charged HBI quantity, which reduces the sulfur containing reducing agents, but also on other factors, such as the slag rate, the quantity and nature of the high S-content recycling material, and the melting rate. (4)
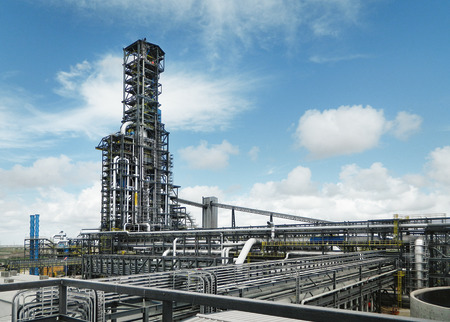
FIGURE 8.
voestalpine Texas HBI Plant
SOURCING HOT BRIQUETTED IRON
If we accept that the most effective, currently available means of lowering the amount of CO2 generated by the steel industry is to use HBI produced by a natural gas-based direct reduction plant in the BF, the important question becomes: “How to source HBI?”
HBI can be sourced two ways by an integrated steel mill: 1) buy HBI from a dedicated merchant HBI plant or from a DRI plant with the capability to produce HBI; or 2) build a natural gas-based DRI plant with HBI capabilities either onsite near steelmaking operations or off-shore where there are sufficient supplies of reasonably priced natural gas.
For most BF producers, merchant HBI plants are the most obvious sources of supply. Merchant HBI allows those who do not wish to own and operate their own plant to purchase material in the open market. To date, BF operators have chosen to obtain HBI in this manner. HBI plants dedicated to merchant supply exist in Venezuela, Libya, Russia, Malaysia, and US (Figure 9). With the exception of Russia, HBI supply has shipments have been limited for several of these suppliers due to political and economic issues. Although DRI plants equipped with briquetting machines have the capability of producing HBI, their first priority is to supply hot DRI (HDRI) to their own steel operations. Therefore, BF operators would be subject to the uncertainty of the spot market.
To have greater control of HBI supply, without having to rely on merchant sources would require building a dedicated facility, as some EAF steelmakers have historically done. In regions where natural gas is not readily available or sufficiently allocated for HBI production, off-shore sourcing may be a practical option. Europe is the first to pursue the off-shore HBI sourcing solution, but it will not be the last. BF producers in India and China, who are faced with limited or high cost natural gas, much like in Europe, have an even greater incentive to search for ways to decrease smog derived from the burning of coal.
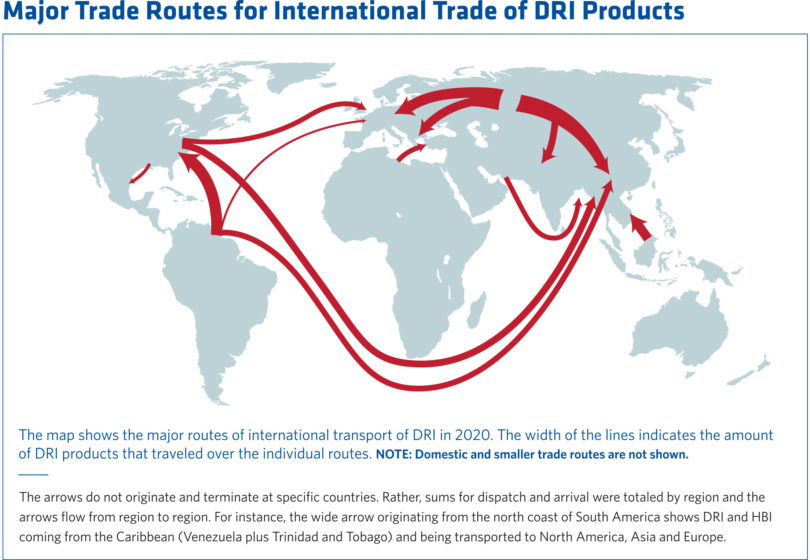
FIGURE 9.
Major Trade Routes for DRI Products 5 (Land, domestic, and smaller routes are not shown)
CONCLUSION
Sustainability is ultimately the key issue for every steelmaker going into the future. DRI products, which until recently have been viewed by integrated steelmakers as an EAF-specific charge material, may actually present a long-term, scalable solution going forward. The use of HBI as a charge material in the blast furnace is now being seen as an effective way to help displace CO2 emissions while increasing hot metal production of the BF.
Investing either directly or through long-term supply contracts in natural gas-based direct reduction plants to make HBI in strategically-located sites around the globe is a reality. The voestalpine Texas plant, the plants at LGOK in Russia, the original MIDREX HBI Plant in Labuan, Sabah, Malaysia, and newest HBI plant owned and operated by Cleveland-Cliffs, Inc., are producing and shipping millions of tons each year.
The BF market shows tremendous potential for merchant HBI sales. However, the amount of HBI available to the merchant market is extremely limited. In order to meet even the most conservative estimate of future demand, additional HBI plants need to be built. Midrex has been the leading supplier of HBI technology since the early 1980s and looks forward to supplying the additional capacity that will be needed with the broadest range of energy and raw materials options in the industry.
References:
- DOEH2@Scale: https://www.energy.gov/sites/prod/files/2018/08/f54/fcto-h2-scale-kickoff-2018-3-ruth.pdf.
- “Pedal to the Metal 2021 – No Time to Delay Decarbonizing the Global Steel Sector,” a report by Global Energy
Monitor, 1254 Utah Street, San Francisco, CA 94110, authors: Caitlin Swalec, Research Analyst for The Global Steel Plant Tracker, and Christine Shearer, Program Director for Coal. - Kobe Steel Ltd.: https://www.kobelco.co.jp/english/releases/1207624_15581.html.
- “Using HBI in Blast Furnaces – Results Achieved by voestalpine Linz,” an article by Anna Griesser and Thomas
Buergler, voestalpine Stahl GmbH, published in 3Q2020 Direct From Midrex. - Midrex Technologies, Inc.: 2020 World Direct Reduction Statistics.