DRI and Its Effects On the Scrap Steel Market in the US
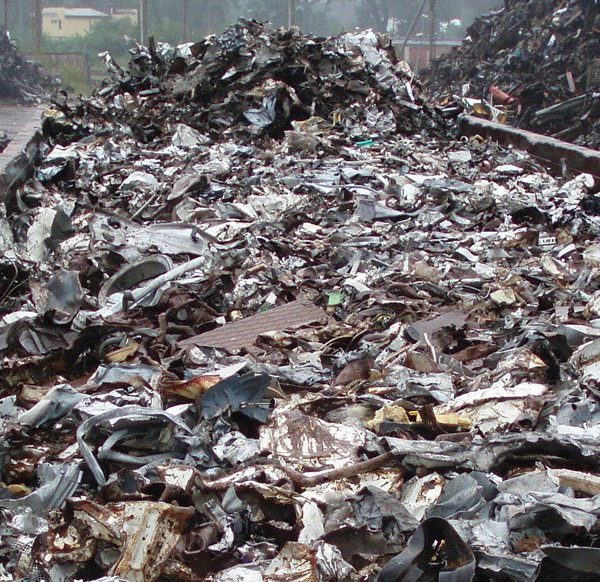
The U.S. to use MORE scrap steel not less
INTRODUCTION
Not that long ago, direct reduced iron (DRI) industry and steel scrap were locked in a struggle reminiscent of the famous Cold War-era shoe-pounding pronouncement by former USSR premier Nikita Khrushchev … “We will bury you!”
A lot has changed in a relatively short time in steel industry years. Today, DRI exerts significant influence on the scrap market but in a way that those metallics industry combatants of yester-years never imagined.
LET’S TALK METALLICS
We use the word “metallic” to mean a material typically containing at least 60% iron (Fe), which is used either in ironmaking or steelmaking. This includes the following shown in the right column.
DRI, in its various forms – cold DRI (CDRI), hot DRI (HDRI) and HBI, and pig iron are collectively known as ore-based metallics (OBMs) because they are derived from naturally-occurring iron ore. OBMs are particularly valuable for electric arc furnace (EAF) steelmaking because they are extremely low in copper and other residual metals and steel made with OBMs contains much less nitrogen and hydrogen. These qualities allow EAF steelmakers to produce steels that are malleable, ductile and formable… you can shape the steel without it tearing or marring.
Any amount of DRI/HBI can be used in an EAF, from 0-100%; yes, there are melt shops that use only DRI because scrap is difficult and expensive to source. Remember, the main goal is to meet the chemical specification of the steel. Therefore, it pays to have the ability to blend DRI/HBI, scrap and even pig iron to accomplish the goal at the lowest cost.
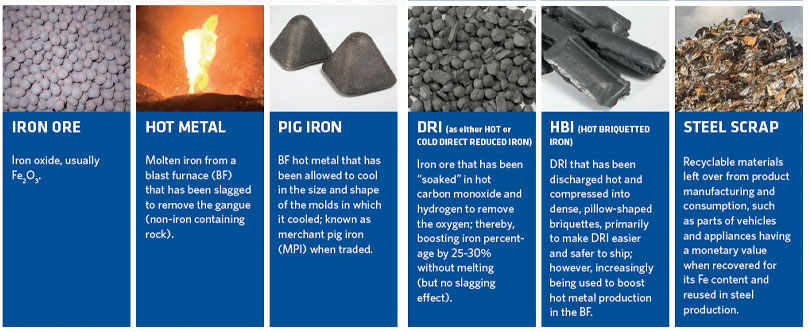
FROM OH TO BOF TO EAF
Once upon a time, in a steel industry nearly forgotten, steel was made primarily in an open hearth (OH) furnace. The OH was big and not very efficient by modern standards. However, its big selling point in its day was the energy savings due to its regenerative stoves.
In the 1960s and 1970s, the OH was replaced by the basic oxygen furnace (BOF), a far more efficient way to make steel. The last OH in the USA closed in 1991. Today, there are only a handful of open hearths still operating in Ukraine, Russia and India… and they will close soon.
The electric arc furnace (EAF) was widely used during World War II to produce alloy steels. However, it was years later, around the time when the BOF overtook the OH, that the low capital cost mini-mill concept was introduced and the EAF came into its own as a steelmaking furnace.
KEEPING COPPER IN CHECK
Up until recently, the steel market was clearly divided. Integrated steelmakers, with their blast furnaces making hot metal would make the low residual steel grades in the basic oxygen furnace (BOF). The EAF-based mini-mills made the higher residual, commodity grades using scrap steel. All that changed in the 1990s with the advent of the thin slab caster. The marriage of the EAF mini-mill and thin slab casting has resulted in the building of a dozen of these mills in the US, having a cumulative annual capacity of 20-25 million tons of high quality flat products.
One of the primary factors was and continues to be protecting the steel from contamination by residual metals, especially copper. Hot metal, like the other OBMs contains virtually no copper or other residual metals (typically below 0.005% Cu, which on the scale where a point of copper is 0.01%, is “zero points”).
For example, let’s make a heat of steel in an EAF with a copper specification of 18 points (0.18% Cu content). For the sake of easy math, let’s make the numbers simple. We have scrap with an average copper of 0.20%, ranging from about 0.18% up to nearly 0.25% and DRI/HBI or pig iron with zero points of copper (< 0.005%).
Because the scrap varies over a range and we cannot afford to miss the steel specification, we must be careful. So, we will aim for 15 points Cu (0.15%) and use 25% OBMs and 75% scrap … and make the specification better than 99.99% of the time.
By using 75% scrap steel for the Fe charge, costs are kept low. A BF-BOF mill cannot do this because BOF scrap usage cannot be adjusted to levels above 20% … so the EAF takes market share away from the BF-BOF.
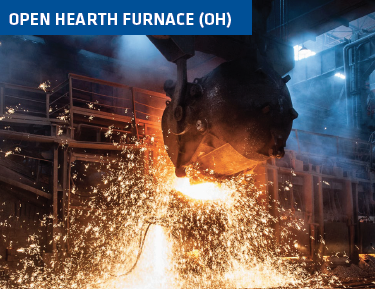
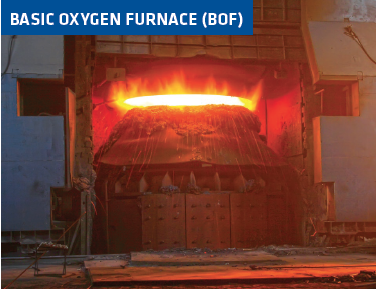
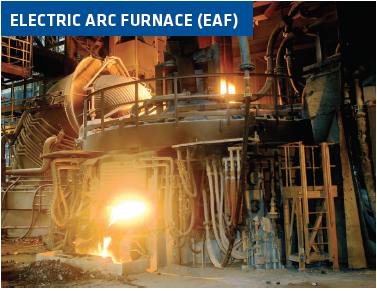
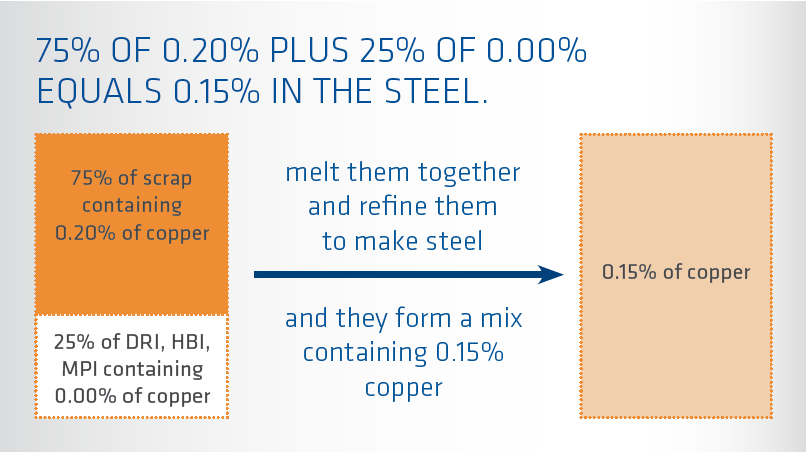
A DOSE OF (SCRAP) REALITY
As the number of EAF flat products mills increases, the need for prime scrap mounts, and no one is going to manufacture additional cars, refrigerators, washing machines just to produce more prime scrap. Therefore, it could be said that were it not for OBMs, most of the EAF-based flat products mills could not have been built. So, even though scrap suppliers must compete with OBMs, at least half of this market would not even exist if not for DRI/HBI and merchant pig iron (MPI).
In other words, the existence of the DRI/HBI and MPI enables the consumption of an additional 5-10 million tons per year of scrap steel in the US alone.