Advancing Performance of Nu-Iron’s MIDREX® DRI Plant
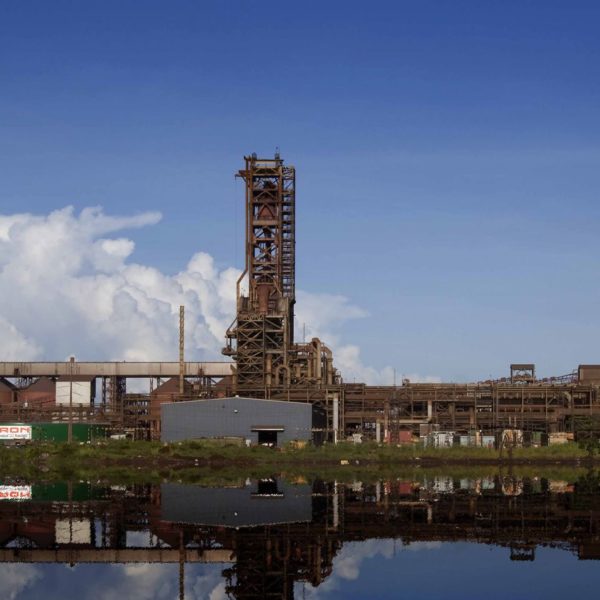
EDITOR’S NOTE: This article has been adapted from a paper given at the 2016 AISTech Conference.
In September 2004, Nucor acquired the physical assets of American Iron Reduction, a 1.2 million ton per year cold DRI (CDRI) plant utilizing MIDREX® Direct Reduction Technology.
Nucor relocated the plant to Point Lisas, Trinidad in 2005, from it’s original location in Louisiana, USA. In the process, it increased the plant’s capacity to 1.6 million metric tons per year. The new plant, Nu-Iron Unlimited, commenced DRI production on December 30, 2006. The company is the largest shipper of CDRI in the world and has produced more than 12 million tons of cold DRI since start-up, which has been successfully shipped to and melted in Nucor Steel mills in the USA.
Looking to push technology and performance even further, Nu-Iron established a Direct Reduction Engineering and Technology (DRET) group in coordination with Midrex Technologies, Inc. Nu-Iron is a wholly owned, full subsidiary of Nucor Steel, the most diversified steelmaker and the largest recycler of steel and steel products in the United States. This article will present and describe the measures thus far employed to enhance the operation, reliability and productivity of the plant including both maintenance practices and equipment development.
BACKGROUND
During the 1990s, rising scrap prices forced USA mini-mills to look for alternate sources of feedstock. An attractive option was domestic natural gas-based direct reduction because of low natural gas prices, from $1.50-2.00 per million Btu at the wellhead. GS Industries, then the parent company of Georgetown Steel Corporation, and Birmingham Steel partnered to develop a new MIDREX® Direct Reduction Plant. The concept was to produce ore-based metallic DRI in Louisiana, which would be shipped to their mini-mills in the Southeast and Midwest USA. Excess product would be sold to others.
The plant was known as American Iron Reduction (AIR) and was located in Convent, Louisiana, on the Mississippi River between New Orleans and Baton Rouge. This location had several advantages including: inexpensive natural gas, rail connections, and river access to receive Brazilian iron ore and ship out DRI. The plant, shown in Figure 1, included a 6.65 meter diameter MIDREX® Shaft Furnace, a 15-bay MIDREX® Reformer and was the first MIDREX® Plant to incorporate a vertical furnace feed conveyor. AIR was started up in January 1998, and passed the performance test within one month of first product. Production rates of up to 180 ton/hour were achieved, with metallization levels as high as 96% and carbon content of 1.8%. Unfortunately, the USA steel market turned down in 1998, reducing demand for DRI and AIR did not operate continuously. By the second half of 2000, rising natural gas prices forced the owners to close the plant permanently. It produced a total of 1.65 million tons of DRI from start-up until its closure in September 2000.
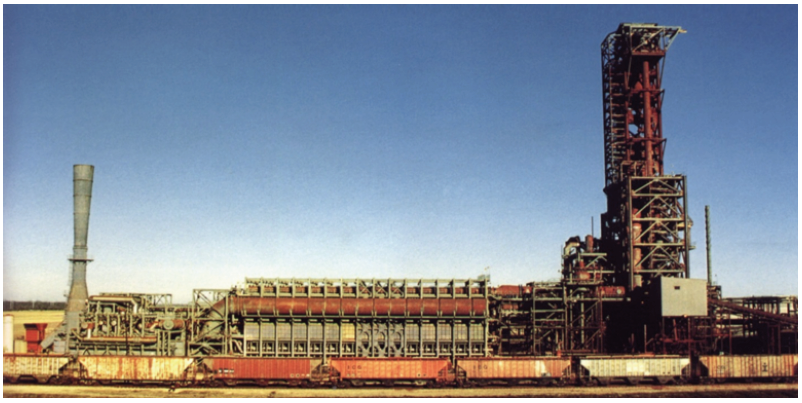
FIGURE 1.
American Iron Reduction - Convent, Louisiana, USA
After performing its due diligence, Nucor determined that it would be feasible to dismantle the AIR Plant and relocate it to Trinidad, which could provide a competitive supply of natural gas and favorable logistics for receiving iron ore and shipping DRI to Nucor’s melt shops in the United States. Such a move was not unprecedented, as relocation of MIDREX® Plants had been done twice before. The former Norddeutsche Ferrowerke GmbH (NFW) plant in Germany was moved to India in 1990, and the British Steel Modules in Scotland were relocated to Mobile, Alabama in 1997. In September 2004, Nucor purchased the idled AIR Plant and began dismantling it. In April 2005, Nucor signed a contract with Midrex Technologies, Inc. for upgrading the plant’s capacity by 400,000 tons per year. A site was identified at the Point Lisas Industrial Estate in Trinidad.
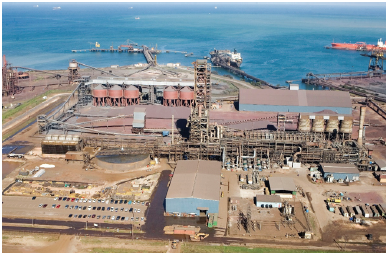
FIGURE 2. Nu-Iron Unlimited – Pt. Lisas, Trinidad & Tobago
Nucor registered the company, Nu-Iron Unlimited, under the laws of Trinidad and Tobago. Several obstacles were overcome by Nucor’s construction and engineering group to safely and efficiently dismantle and transport the plant on 13 ocean barges down the Mississippi River, across the Gulf of Mexico and Caribbean Sea to its final destination at Point Lisas, Trinidad, with the last barge diverting slightly to avoid Hurricane Katrina. Simultaneously, Nucor worked closely with Midrex to expand the plant’s capacity by adding reforming capability and gas compressor capacity, which increased the nameplate rating to 1.6 million tons per year. The completed facility is shown in Figure 2, with the shaft furnace in the center of the photo, the DRI storage bins just to the left and the receiving and shipping docks just to the right of the furnace tower.
Production began on December 30, 2006, and the first cargo was shipped to Mobile, Alabama, on January 21, 2007. With no steelmaking capability at its site in Trinidad, Nu-Iron ships all DRI produced to four ports in the USA: Charleston, South Carolina; Mobile, Alabama; New Orleans, Louisiana and Morehead City, North Carolina. After discharge, the product is transported via barges to receiving mills based in: Berkeley County, South Carolina; Tuscaloosa, Alabama; Decatur, Alabama; Memphis, Tennessee; Hickman, Arkansas and Hertford County, North Carolina.
CREATION OF DRET TEAM- ADVANCING PLANT PERFORMANCE
As a key part of Nucor’s ore-based metallics (OBM) strategy, the Nu-Iron facility is one of the world’s most advanced DRI operations. It is based on flexibility, inclusion and performance. Adhering to the Nucor quality principles, Nu-Iron boasts world class DRI product quality while maintaining a safe and productive work environment. Typical DRI product is greater than 96% metallization (amount of reduced Fe content) with carbon content of 2.8% or higher. The plant also features exemplary safety standards, with a DART of 0.0. DART is a safety metric that stands for “days away, restricted or transferred.” Nu-Iron’s DART is well below the national industry average of 1.67.
With the latest and most productive DRI technology in use at the Point Lisas site, Nu-Iron sought to push the DRI technology and plant performance even further. To see where they could go, Nu-Iron began benchmarking their operations and comparing themselves to various other MIDREX® DRI facilities. Through their discovery phase, they determined that there was room for improvement.
The company had goals of setting new standards and breaking internal and external records. With a vision set, the next item was to create a team empowered to make changes. As embodied in Nucor basic philosophy, Nu-Iron embraced the idea of “… succeeding by working together.”
To achieve this end, in 2014, Nu-Iron established a Direct Reduction Engineering and Technology (DRET) team. Its primary focus was to keep the plant running at optimum performance, improve product quality and minimize downtime.
The DRET team brought together about a dozen professionals from all the engineering disciplines at the plant site. Members of DRET include process engineering, E&I, mechanical engineering, a refractory specialist, a control systems engineer, senior technicians and specialists. It also includes a mechanical engineer from Midrex Technologies, Inc., who functions as an onsite MIDREX® Technology liaison. The group takes a broad view towards various aspects of plant operation in order to define realistic and achievable goals. Once defined, the group systematically outlines and implements procedures and strategies to attack the challenges. The DRET team sought best operational practices and procedures throughout the industry. Using this inclusive approach, they did not limit themselves and embraced practices from the blast furnace industry, as well as from other MIDREX® DRI plants.
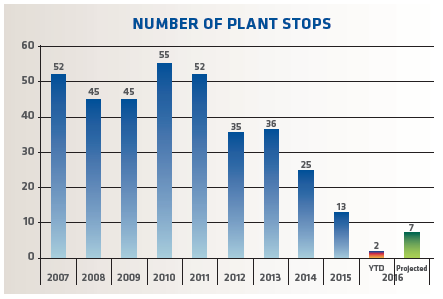
FIGURE 3. Unscheduled number of plant stops
The DRET team is responsible for major shutdown planning, creating and maintaining a 5-year “living document” for plant maintenance and operations, conducting root cause analysis investigations and developing equipment preventive maintenance procedures, as well as implementing the Management of Change process. DRET is a hands-on team, not administrative, which is one of the reasons it is so effective. With the proper vision and team established, Nu-Iron embarked on ways to improve operation through minimizing unscheduled downtime. They adopted available thermography and vibration analysis technologies to enhance their preventive maintenance programs.
Where possible the plant increases automation and focuses on frequent monitoring of key equipment and process streams. Thermography and oil and vibration analysis are used to effectively monitor the health of vital equipment, to reduce wear, predict maintenance needs and limit the number of unscheduled plant stops (Figure 3).

FIGURE 4. Downtime Analysis
A key to maximizing plant performance very simply is to maintain stable operations and minimize plant stops wherever possible. A plant stop can result from any interruption in the operation of the plant and subsequent production. A stop can be the result of an equipment trip from a voltage dip or a component failure, a lost interlock, operator error, even poorly designed control logic. A stop also occurs when plant operations are intentionally halted for planned maintenance.
Two examples of adopting blast furnace best practices include the use of laser analyzers and blast furnace refractory systems. The DRET group pursued the use of laser analyzer technology over mass spectrometers for online gas analysis and control of the DRI making operation. The laser analyzer technology was recognized as a blast furnace best practice and readily adopted by Nu-Iron as a cost effective alternative to mass spectrometry. DRET also successfully incorporated blast furnace refractory practices such as shotcrete and pouring castable refractory in critical areas throughout the refractory system. The effectiveness of the DRET group can be illustrated in the drop of mechanical and process stoppages, as seen in Figure 4.
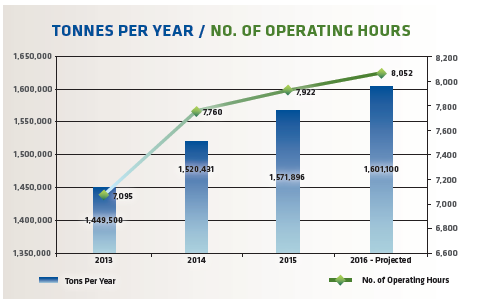
FIGURE 5. DRI tons produced & number of operating hours
Since start-up of the plant, Nu-Iron has focused on product quality while ramping up operation. Figure 5 shows both the increase in tons of CDRI produced, as well as the number of hours the plant operated during the period. Through adoption of new procedures and monitoring, Nu-Iron has made considerable strides over past years and is confident that current 2016 operations will exceed 2015 results.
As previously stated, Nu-Iron produces high quality DRI. The plant produces a premium, highly metallized product (greater than 96% metallization/reduced Fe content) with carbon content of 2.8% or higher. Nu-Iron operations focuses on metallization over carbon in production of this product, meaning they favor the production of a higher metallized product over maximizing carbon content. The product specs exceed the standards of many other operating DRI facilities. In fact, any DRI produced with met lower than 96% is considered remet by Nu-Iron’s internal standards. Note that remet does not have an industry standard definition for met percentage of metallization; however, typically anything under 89% is generally considered remet, and thus Nu-Iron’s remet would be considered as acceptable product by most plants throughout the world.
Remet is material processed through the furnace that does not meet the individual quality requirements of the producing plant. Production of remet can occur during process condition upsets. Remet is also generated when starting up and shutting down plant operations. Typically, remet is reprocessed through the furnace to meet metallization and/or carbon content requirements and is not a loss of material, but it does impact overall plant production and efficiency. Considering that remet is generated for every plant stop, the desire to operate without interruption is intensified.
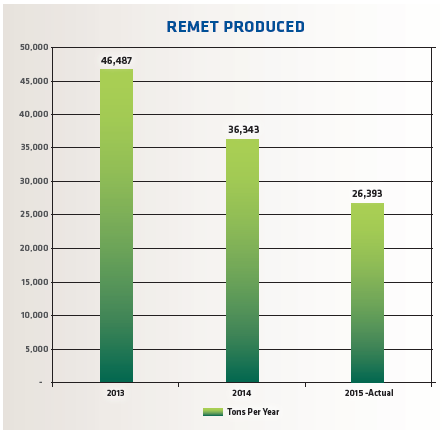
FIGURE 6. DRI produced as remet
To produce such high quality product consistently would typically cause one of two effects. The plant would tradeoff general productivity (ton/hour) for product quality and/or reject more DRI produced as remet. Through DRET implemented initiatives, Nu-Iron has been able to continue to ramp up production while simultaneously lowering the amount of DRI products being produced with metallization under 96% (Figure 6).
ADDITIONAL DRET INITIATIVES
Beyond core DRI plant operation and production of DRI product, the DRET group pursues additional initiatives keeping with core Nucor philosophies. These include the addition of a belt filter press, a newly developed DRI polisher and cold briquetter to improve yield, efficiencies and environmental quality in addition to plant profitability. The belt filter press allows Nu-Iron to reclaim water that would normally be lost in evaporation from sludge ponds. This advancement grew out of necessity as the seasonally high precipitation of Trinidad did not lend itself to typical industry best practices of using sludge ponds to dry out clarifier slurry. The solution currently implemented reclaims water for process use, as well as eliminates the need for settling ponds.
Nu-Iron also developed and constructed a DRI polisher of their own design – a cylindrical tumbler that effectively peens the surface of the DRI pellets resulting in a significant reduction in the amount of dust and fines generated through subsequent handling and improving recognized yield. In addition, the plant is now employing a DRI fines cold briquetting system to reclaim DRI fines and safely ship materials to the USA. These technology implementations minimize yield loss by reclaiming more of the iron content, and also represent environmental advances to plant operation keeping with Nucor’s environmental vision.
SUMMARY
The Nucor culture inspires high performance and results driven operations that embody safety and teamwork. The DRET group embodies core Nucor values and spirit to do better, looking to push technology and performance further while creating a safe and prosperous work environment. The DRET group, by working together various internal team members and including Midrex Technologies, Inc. into the fold has established new goals and set new standards for direct reduction ironmaking. Improved systems and procedures can produce desired availability, product specs and productivity; however, the right culture, the Nucor way, is one that will take us beyond.