Story | Innovations & Improvements
ArcelorMittal Hamburg Turns 50 – Leading Another Ironmaking Renaissance
March 30, 2021
INTRODUCTION
When Willy Korf built Badische Stahlwerke (BSW), his first so-called ‘mini-mill’ in Kehl in 1968, his large competitors tried to squeeze him out by limiting the availability of scrap steel to use in its electric arc furnace (EAF). He knew that if his revolutionary approach to steel production was to survive and succeed, it would need a source of metallic iron to relieve its dependence on scrap supplies. It so happened that Midland-Ross in the USA was introducing a new direct reduction process, known as MIDREX®, about the same time…and the rest is history.
A PLACE IN DR INDUSTRY HISTORY
When Hamburger Stahlwerke (HSW) was built in south Hamburg in 1970, a MIDREX Plant was included in the project. The plant would supply direct reduced iron (DRI) for the HSW EAF melt shop and also to Korf’s BSW mill. The MIDREX Plant was started up in October 1971, and has produced over 18 million tons of DRI in its illustrious 50 years of operation.
The HSW DRI-EAF steelworks was inaugurated in April 1972, and by November 1975, had produced one million tons of wire rods. Today, the steelworks is owned and operated by the ArcelorMittal Group as ArcelorMittal Hamburg and is one of Germany’s largest wire rod producers and a leading company worldwide for producing wire rods by the mini-mill concept.
LN Mittal acquired HSW in 1995 and renamed it ISPAT HSW. Through the years, the company name has changed several times, as Mittal expanded his steel operations, culminating with the merger with Arcelor to form the ArcelorMittal Group. The steel mill, which can produce 250 grades of steel, has undergone several upgrades and modifications to increase its liquid steel and wire rod capacity. Likewise, the MIDREX Plant has been modernized to make it capable of over 600,000 tons/year of DRI (Note: the plant was originally built with a rated capacity of 400,000 t/y).
DRI makes up an average of 45% of the iron charge to the ArcelorMittal Hamburg melt shop. The DRI plant has the lowest annual electricity consumption of all MIDREX Plants and includes a unique system that pneumatically conveys DRI fines and dust from the MIDREX Plant to the melt shop, where they are injected into the EAF.
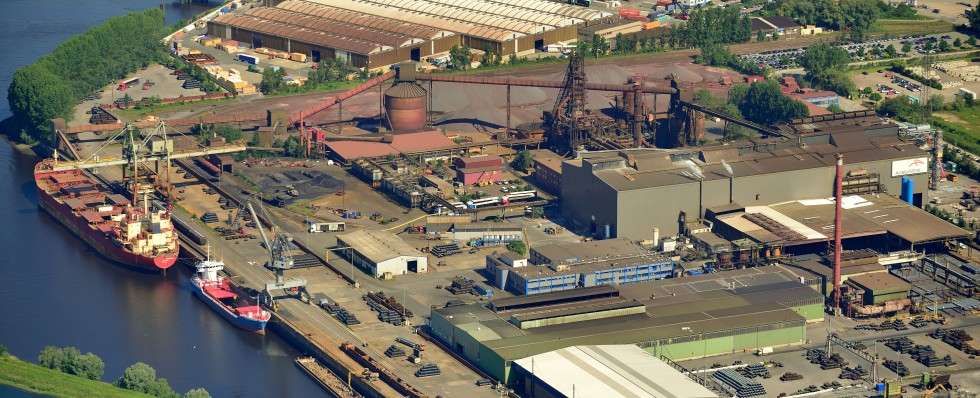
ArcelorMittal Hamburg, located on the bank of the Elbe River
LEADING ROLE IN THE FUTURE OF IRON & STEELMAKING
The ArcelorMittal Group has developed a low-emissions technology strategy to permanently reduce CO2 emissions, which targets not only the use of alternative feedstocks but also the direct avoidance of carbon (Carbon Direct Avoidance, CDA). As one aspect of its strategy, ArcelorMittal has launched a first-of- its-kind project in its Hamburg steelworks to use hydrogen on an industrial scale for the direct reduction of iron ore for use in the steel production process. The Hamburg works already has one of the most energy-efficient production processes of the ArcelorMittal Group due to the production and use of natural gas-based DRI. The aim of the new hydrogen-based process is to enable steel production with the lowest CO2 emissions.
ArcelorMittal commissioned Midrex in September 2019, to design a demonstration plant at its Hamburg site to produce steel with hydrogen. The companies will cooperate on several projects, ranging from research and development to the implementation of new technologies. The first project, incorporating the expertise of Midrex and ArcelorMittal, will demonstrate the large-scale production and use of DRI made with almost 100% hydrogen.
“Our Hamburg site offers optimum conditions for this innovative project: an electric arc furnace with DRI system and iron ore pellets stockyard, as well as decades of know-how in this area,” Frank Schulz, CEO of ArcelorMittal Germany, said. “The use of hydrogen as a reducing agent shall now be tested in a new shaft furnace.”
From 2023 onwards, the demonstration plant will produce about 100,000 tons of direct reduced iron per year, initially with “grey” hydrogen sourced from natural gas, and later – once available in sufficient quantities and at economical cost – with “green” hydrogen from renewable energy sources.
“With Midrex technology, we have been producing high quality steel in an efficient and innovative way for 50 years,“ Dr. Uwe Braun, CEO of ArcelorMitall Hamburg, said. “The possibilities of this technology are still not exhausted and we are working together to make steel production fit for a sustainable future through the direct reduction of iron ore with hydrogen. The innovation capacity of DRI technology is enormous, and its potential has not yet been fully developed. We are convinced that we can still achieve a lot with this technology in order to produce excellent steel in a climate-neutral manner”.
Dr. Braun continued to say, “Our site is the most energy-efficient production plant in the ArcelorMittal Group. The existing MIDREX Plant in Hamburg is already the plant with the lowest CO2 emissions for high quality steel production in Europe. With the new hydrogen-based DRI plant, we will raise steel production to a completely new level, as part of our worldwide ambition to be carbon neutral by 2050.”
“We are delighted to work with ArcelorMittal”, Stephen C. Montague, President and CEO of Midrex Technologies, Inc, said. “ArcelorMittal now operates six plants with MIDREX direct reduced iron technology. With number seven, we’re going to lead the way in using renewable energy to make DRI for steel production.
“It’s only fitting that we and ArcelorMittal have teamed up for this first step towards carbon neutral steel production on an industrial scale,” Montague observed. “We are proud that they have chosen to take this momentous step with us.”
For more information about ArcelorMittal’s path to low-carbon steelmaking, visit their website.
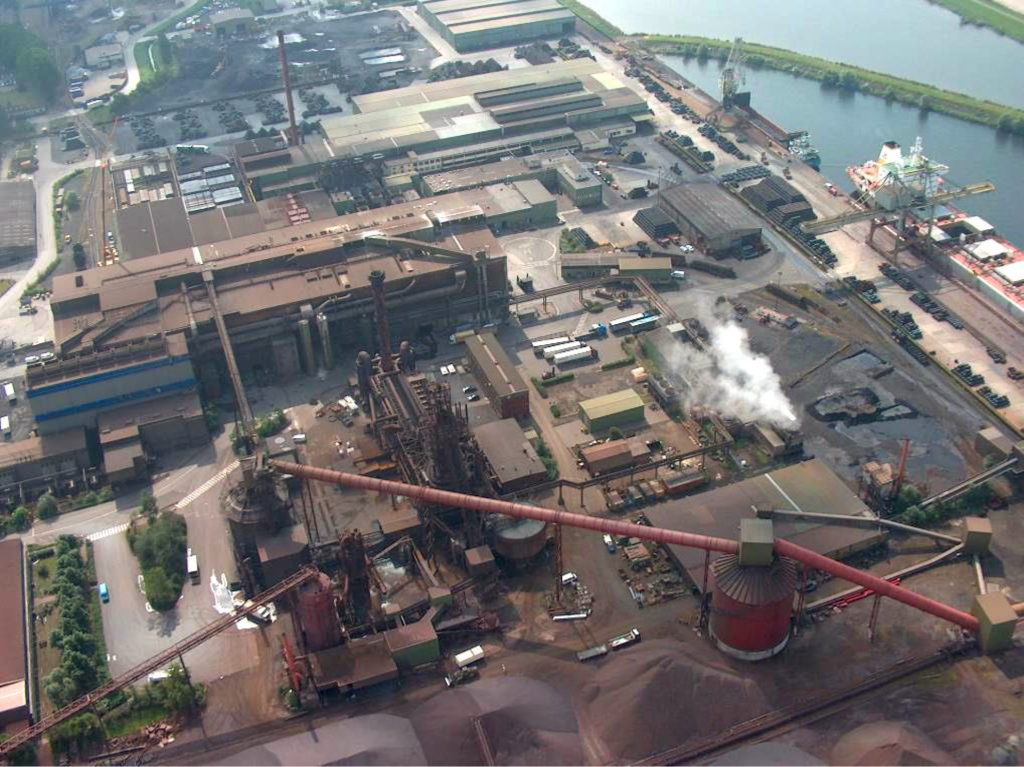
MIDREX CDRI Plant in Hamburg, Germany. Start-up: 1971
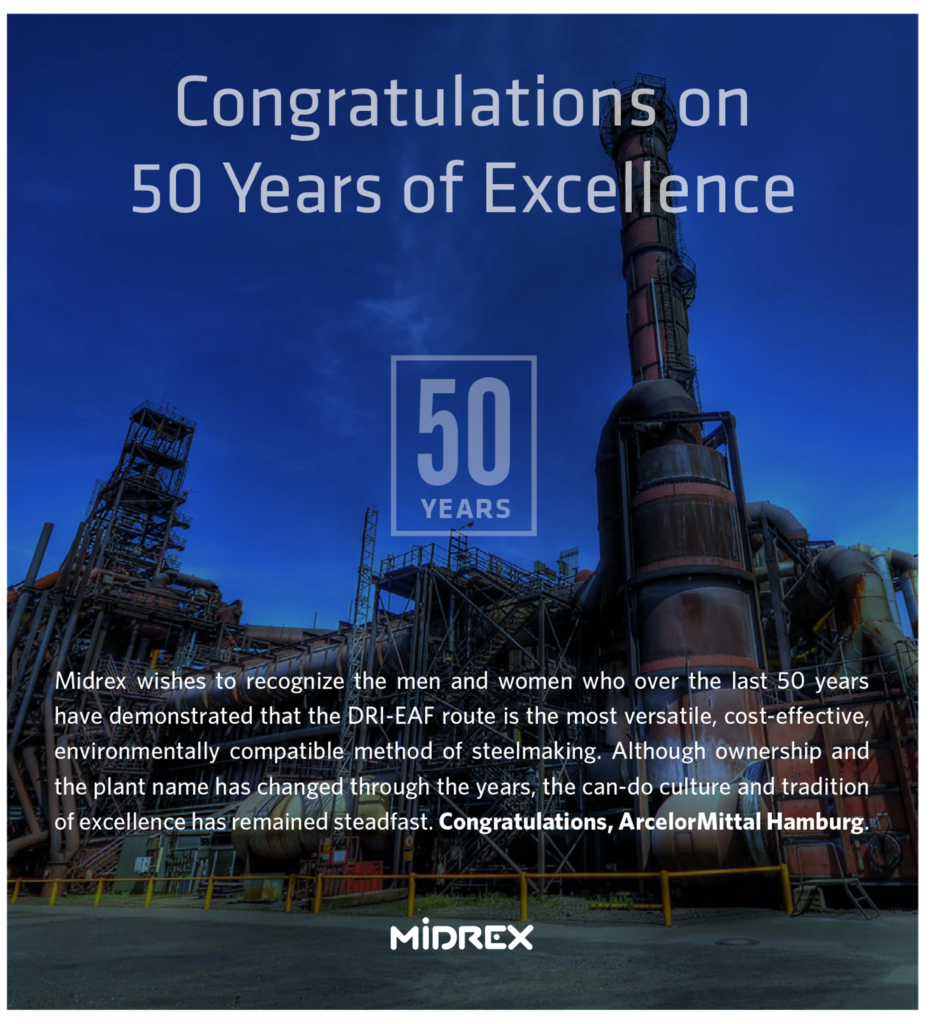