People, Growth & Technology

A MIDREX® Plant must successfully complete a series of tests that measure various operating parameters allowing Midrex to complete its performance obligations for our customer.
The results of these tests are indicative of what the plant is capable, but in no means are they limiting on the expectation of what can be achieved during the plant’s lifetime. We call this test the PGT – Performance Guarantee Test. The PGT is a critical milestone for any project and something everyone at Midrex takes very seriously.
PGT also can be used to describe the “test” Midrex is facing as we play our role in decarbonizing our industry – People driving Growth with Technology.
If not for a group of talented, innovative, and determined people more than 50 years ago, there might not be a Midrex today. They saw a value-added future for their know-how and expertise in changing the way iron ore is prepared for steelmaking – direct reduction. No, they didn’t invent direct reduction; they created a better way to make direct reduced iron (DRI) and established a culture of engagement, achievement, and teamwork.
Through the years, Midrex has not only introduced numerous innovations and improvements to its process technology but has been the driving force in establishing DRI as an essential metallic material for sustainable steelmaking. In 1971, when the longest-serving MIDREX® Plant began operating in Hamburg, Germany, DRI production was less than one million metric tons (Mt). DRI production in 2022 was 127.36 Mt, with MIDREX Plants accounting for 73.55 Mt. Today, DRI is essential for production of the highest quality steel grades in the electric arc furnace (EAF) and the use of hydrogen-based DRI in the EAF is generally regarded as the steelmaking route most capable of meeting the carbon dioxide (CO2) emissions standards of the future.
People inside and outside the company have asked, “What is Midrex?” Is it a technology company? Is it an engineering company? Is it an aftermarket solutions company? There is one simple answer…yes. As Stephen Montague, my friend, colleague, and mentor since I started my journey at Midrex, was fond of saying, Midrex is “a small team doing big work, committed to loving and serving others.”
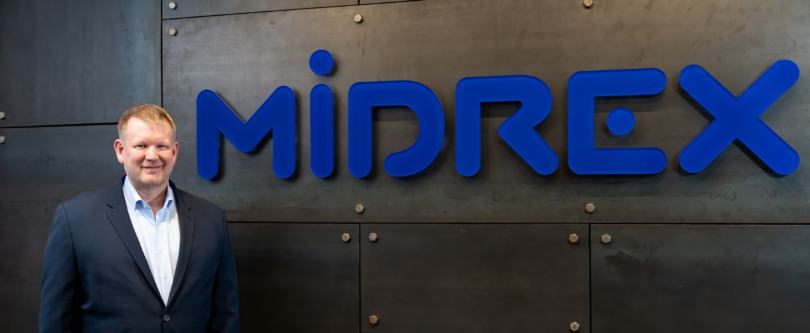
And judging by the results of our first 50 years, we must invest in the people at Midrex, grow Midrex, and continue to advance our technology.
The topic of decarbonization has intensified in the past few years. When I joined Midrex, hydrogen-based DRI plants were a thought for the future. Today, we are designing a 2.1 Mt plant for H2 Green Steel that will use 100% hydrogen as reducing gas and a 2.5 Mt plant for thyssenkrupp Steel paired with a melter that will be capable of producing high quality, low CO2 DRI from blast furnace-grade pellets.
Sustainability – technological and financial – is foremost in the minds of steel executives across the globe, and we are continuously evaluating our capabilities and adding resources to provide sustainability solutions. We are confident in our culture of innovation, improvement, teamwork, and service. And judging by the results of our first 50 years, we must invest in the people at Midrex, grow Midrex, and continue to advance our technology.
Just like for our projects, P-G-T is the measure of our success.
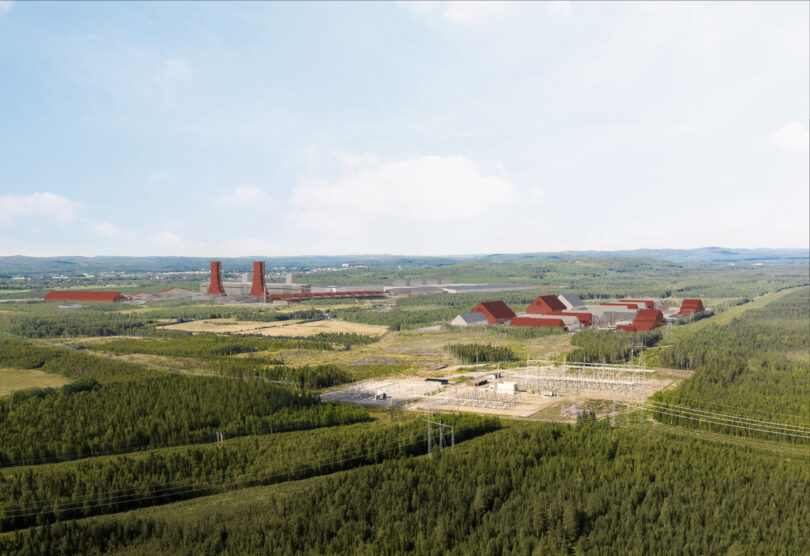
The 2.1 million tons per year MIDREX H2TM Plant will be located in Boden, northern Sweden.