Midrex Technical Support & Services: Redefining “Aftermarket”
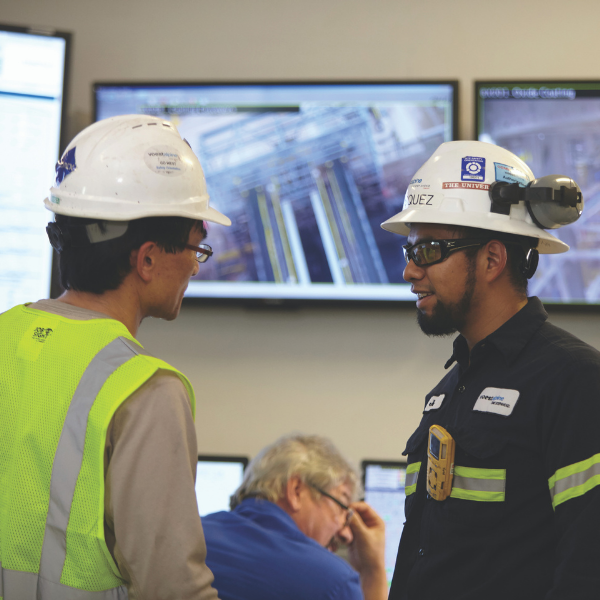
Midrex made a commitment to collaborative technology transfer even before the first full-scale MIDREX® Direct Reduction Plant was built in the early 1970s. Now, almost 50 years later, with more than 90 modules located around the world, we are providing our customers with innovative, essential, and effective technology-based processes and systems and the services and support to ensure they receive the highest return on their investments.
Each plant is unique in its staffing, mission, and operating conditions. Depending on time, location, and circumstances, the service requirements can be very different, even for the same plant. Therefore, an effective service provider must have the skills, ingenuity, and experience to create custom solutions – and the consistent presence and relationships to gain the trust and cooperation of the customers.
We don’t regard customer support and services in the traditional “aftermarket” sense because Midrex is actively involved in all aspect of a plant – design, supply, operation, and maintenance – a seamless transition from plant supply to plant operation services and support. Our all-inclusive approach to support and services is based on:
- Two-way technology transfer
- Collaborative technical support
- Digitally-based advanced solutions
Organizationally, Midrex has two groups devoted to customer support and services: Technical Services and Global Solution. Technical Services is the main point of contact for Midrex with operating plants and provides support under the provisions of the MIDREX Process License in the form of:
- responding to technical inquiries from Process Licensees
- collecting operational/production data for preparing the annual MIDREX Plants Operations Report and to facilitate benchmarking
- organizing the technical program of the annual Midrex Operations Seminar and/or webinars
- identifying plant improvements and improvements needed
- coordinating plant visits
- supervising the preparation of Technical Bulletins and Instructions (TSBs and I&Is)
Global Solutions supplies spare parts and provides engineered solutions and the services to implement them. Engineered solutions include plant audits, debottlenecking studies, process automation upgrades, adapting equipment for local conditions, incorporating new technologies, such as Adjustable Carbon Technology (ACT™). Services range from reformer management to field-based support, such as refractory replacement and mechanical or operations advice, as well as Integrated Plant Solutions (IPS), a custom-tailored suite of services to match specific client needs. Each service offering is tailor-made to match customer needs.
The most recent Midrex service offering is complete DRI-to-EAF optimization through our partnership with AMI Automation This partnership allows all MIDREX DRI-EAF integrated facilities to achieve the lowest cost of liquid steel produced from iron oxide by optimizing the DRI plants and the EAFs as a single unit. Therefore, all decisions are based on the effect on liquid steel produced and not the performance of the individual operations.
Supplying, supporting, and servicing technology for direct reduction-based steelmaking is our business – our only business – and Global Solutions is the only plant services provider that can guarantee the solutions it provides are designed and manufactured to exact Midrex specifications.