MIDREX® Process Meets the Challenges
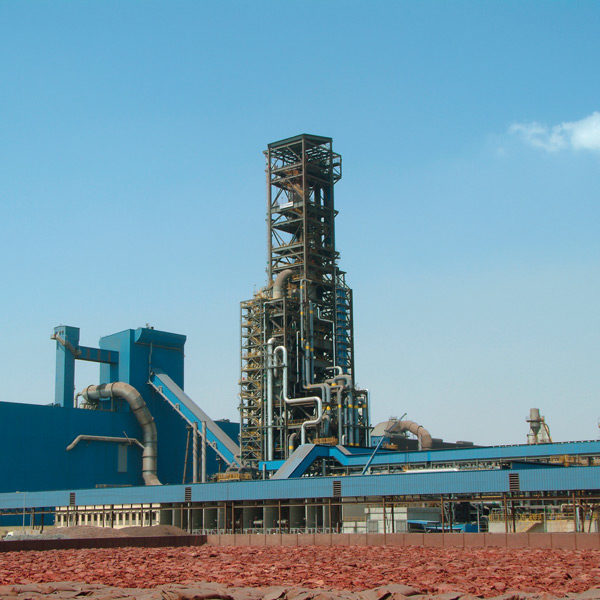
Sometimes we take our history for granted, but that’s not always a negative thing.
When I first started at Midrex in 1996, just out of university, the 6.65-meter shaft furnace was a relatively new and crucial step for us. We talked about a “MEGAMOD” plant design, as if it were a stretch for our capabilities. Apart from the COMSIGUA HBI plant in Venezuela, all of the latest contracted plants were designed to produce DRI only (we didn’t call it CDRI [cold DRI] back then, as we didn’t have a proven option for producing HDRI [hot DRI]). We were treading carefully on our first attempts at feeding oxide to a furnace with a vertical conveyor, we were installing the first of our oxide coating and oxygen injection systems, and we were just starting to talk about developing 3D models of our plants as an input for engineering. And no single direct reduction module had ever produced one million tons of DRI in a year.
The year 2004 ushered in serious diversity with respect to product demands of our customers, including higher capacity HBI plants and combo plants that could produce both CDRI/ HBI or CDRI/HDRI. These capacity and product diversity demands required the integration of centrifugal process gas compressors into the process and the development of hot transport conveyors, a product cooler external to the reduction furnace, and a myriad of additional upgrades and innovations. None of these was a trivial development, and our Engineering team experienced the growing pains of implementing previously unproven technologies. Sometimes, as we move ahead, we don’t fully appreciate the effort that it takes to reach these
achievements.
The fascinating aspect of being in the “middle of the battle” has been to see how our teammates developed solutions for and responded to each of these challenges. I have always been impressed by the sheer talent and determination that the various teams at Midrex demonstrate, particularly in Engineering. We have a diverse team continually growing in its capabilities. Over the past year we have brought fantastic new teammates onboard (who don’t yet fully understand what kind of ride they’re in for). We are fortunate to have experienced team members who serve as the “backbone” and provide necessary mentoring by sharing their lessons learned, some of which have come with a lot of “bumps and bruises.” We have the right people to meet the oncoming challenges, and we will continue to grow as we look for additional outstanding talent that fits our company culture.
So, what kind of challenges do we face in 2022? Producing DRI with “green” hydrogen is at the top of the list. Tightening environmental requirements will require new, improved abatement technologies. Demands for digitalization and automation will press us to provide enhanced offerings in plant control systems. Solutions for using lower-grade ores will bring economic advantages to the DR market. And maybe the biggest challenge will be getting it all done in the midst of increasing demand for DRI bolstered by global initiatives to decarbonize the market.
We have a talented team that has developed technologies which we are ready to offer now: MIDREX FlexTM provides the technology for transitioning a natural gas-based plant to operate with up to 100% hydrogen. And for customers who want to produce DRI with 100% hydrogen from day one, we have the MIDREX H2TM solution available.
Years from now, as we look back on 2022, these challenges and technologies will be proven and a part of our history that we may take for granted as well.